What is PCB Panelization?
PCB panelization is the process of grouping multiple printed circuit board (PCB) designs onto a single panel for manufacturing. This panel is then run through the PCB fabrication process as a single unit, and the individual boards are separated (depanelized) at the end.
Panelization allows for more efficient use of materials and faster production times compared to manufacturing each PCB design separately. It’s an essential step in the PCB manufacturing process, especially for high volume production.
Why is PCB Panelization Important?
There are several key reasons why PCB panelization is crucial:
-
Cost Savings – Producing multiple PCBs on a single panel reduces material waste and setup times, lowering the overall cost per board.
-
Faster Production – Panelizing PCBs allows for batch processing, which speeds up fabrication and assembly compared to handling each board individually.
-
Consistency – PCBs manufactured on the same panel under identical conditions have greater consistency in quality and specifications than boards produced separately.
-
Automated Assembly – Panelization is necessary for automated assembly lines and pick-and-place machines which require consistent spacing and orientation of boards.
-
Easier Handling – Panels are easier to transport and handle throughout the manufacturing process compared to individual small PCBs.
-
Testing Efficiency – Panels allow for batch testing of multiple PCBs simultaneously, speeding up quality control.
-
Labeling and Traceability – Panels provide space for labeling, barcodes, and fiducial marks for traceability and automated assembly.
-
Scalability – Effective panelization allows manufacturers to scale up production volumes efficiently to meet demand.
Considerations for PCB Panelization Layout
Designing an efficient panel layout requires careful planning and consideration of several factors:
Board Spacing and Depanelization Method
Adequate spacing must be left between individual PCBs on the panel to allow for clean depanelization (board separation) after fabrication. The spacing required depends on the depanelization method used:
Method | Spacing |
---|---|
V-Scoring | 0.5 – 1.0 mm |
Tab Routing | 1.0 – 2.0 mm |
Pizza Cutter | 2.0 – 3.0 mm |
Milling/Routing | 3.0 – 5.0 mm |
Tooling and Fiducial Marks
Tooling holes and fiducial marks on the panel assist with aligning and securing the panel during fabrication and assembly. Their placement and size should follow the specifications of the manufacturing equipment used.
Orientation and Balancing
Orient the individual PCB designs on the panel to minimize material waste and ensure the panel is balanced. An unbalanced panel can cause issues during fabrication. Rotating boards 90° or 180° can often lead to a more efficient layout.
Panelization Software Tools
Specialized panelization software can automatically generate optimized panel layouts based on your PCB designs and manufacturing specifications. Some popular tools include:
- CAMtastic (Altium)
- GerberPanelizer
- PanelMaker (SolidWorks PCB)
- TriMech Panel Creator
These tools help streamline the panelization process and ensure the resulting panel meets manufacturing requirements.
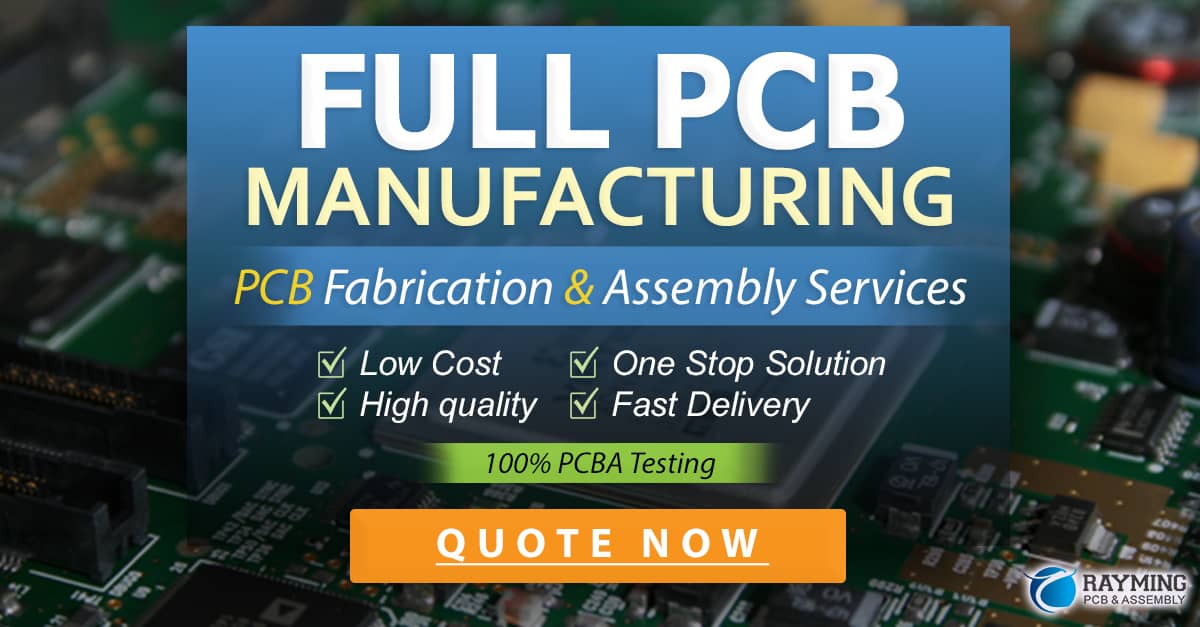
PCB Panelization Techniques
There are several techniques used to panelize PCBs, each with its own advantages and considerations.
Tab Routing
Tab routing involves connecting the individual PCBs with small tabs which are milled away after fabrication to separate the boards. This method provides good board stability during manufacturing but requires extra milling time for depanelization.
V-Scoring
V-scoring uses a V-shaped groove cut partially through the panel between the PCBs. After fabrication, the boards can be easily snapped apart along these grooves. V-scoring allows for closer spacing of boards compared to tab routing but may not be suitable for thicker PCBs or boards with components near the edges.
Pizza Cutter
The pizza cutter method uses a circular blade to cut through the panel between the PCBs, similar to a pizza cutter. This technique is faster than tab routing but requires more spacing between boards and may leave rougher edges.
Milling/Routing
Milling or routing involves fully cutting through the panel to separate the individual PCBs. This method provides clean edges but requires significant spacing between boards and additional milling time.
The choice of panelization technique depends on factors such as the PCB thickness, component locations, required board spacing, and available manufacturing equipment.
Challenges and Solutions in PCB Panelization
Panelization comes with its own set of challenges that must be addressed for successful manufacturing.
Thin or Flex PCBs
Thin or flexible PCBs can be more difficult to panelize securely. Using methods like tab routing with thicker tabs or adding support rails to the panel can help stabilize these types of boards during manufacturing.
Breakaway Panels
For designs that require very close spacing between PCBs, a breakaway panel may be used. This involves placing the individual PCBs on a temporary frame that holds them securely during fabrication and is then removed and discarded after depanelization. This allows for tighter spacing but increases material waste.
Depanelization Stress
The depanelization process can put stress on the PCBs, especially near the edges. To minimize this stress, use appropriate spacing and depanelization methods for your board thickness and material. Avoid placing sensitive components or connectors too close to the depanelization areas.
Mixed-Thickness Panels
If a panel contains PCBs of different thicknesses, it can lead to uneven surfaces and difficulties during fabrication. One solution is to use a “step-milling” process, where the thicker PCBs are milled down to match the thickness of the thinner ones in certain areas. Alternatively, separate panels can be used for each thickness.
FAQ
1. What is the minimum spacing required between PCBs on a panel?
The minimum spacing depends on the depanelization method used. V-scoring requires the least space at 0.5-1.0 mm, while milling/routing may need up to 5 mm between boards.
2. Can PCBs of different thicknesses be panelized together?
It’s generally not recommended to panelize PCBs of different thicknesses on the same panel, as it can lead to fabrication issues. Step-milling or using separate panels for each thickness are potential solutions.
3. What are fiducial marks, and why are they important?
Fiducial marks are reference points on the panel that help align and orient the panel during fabrication and assembly. They ensure proper positioning of the PCBs and components.
4. How does panelization affect the cost of PCB manufacturing?
Panelization can significantly reduce the cost per PCB by minimizing material waste, setup times, and allowing for batch processing. However, the cost savings depend on factors such as the panel layout efficiency and the manufacturing volume.
5. What software tools are available for creating PCB panel layouts?
There are several dedicated panelization software tools available, such as CAMtastic (Altium), GerberPanelizer, PanelMaker (SolidWorks PCB), and TriMech Panel Creator. These tools can automatically generate optimized panel layouts based on your PCB designs and manufacturing specifications.
Conclusion
PCB panelization is a crucial step in the PCB manufacturing process, offering significant benefits such as cost savings, faster production times, and improved consistency. However, designing an efficient panel layout requires careful consideration of factors such as board spacing, depanelization methods, tooling and fiducial marks, and panel balancing.
Various panelization techniques, such as tab routing, V-scoring, and milling, can be used depending on the specific requirements of the PCBs being produced. Challenges like thin or flexible PCBs, breakaway panels, depanelization stress, and mixed-thickness panels must also be addressed for successful manufacturing.
By understanding the importance of PCB panelization and following best practices for panel design and manufacturing, you can optimize your PCB production process for efficiency, reliability, and cost-effectiveness.
0 Comments