What Is Wave Soldering?
Wave soldering is an automated soldering process that involves passing a PCB over a molten solder wave to create electrical connections between the components and the board. It is primarily used for soldering through-hole components, where the leads of the components are inserted into holes drilled in the PCB.
Advantages of Wave Soldering
Wave soldering offers several advantages over other soldering techniques:
- High-speed process: Wave soldering is a fast and efficient method, making it suitable for high-volume production.
- Consistent results: The automated nature of wave soldering ensures consistent and reliable solder joints across the entire PCB.
- Cost-effective: Wave soldering is cost-effective for large-scale production as it reduces manual labor and minimizes errors.
- Versatility: Wave soldering can accommodate a wide range of component sizes and types, making it suitable for various PCB designs.
Wave Soldering Equipment
To perform wave soldering, several key pieces of equipment are required:
Conveyor System
The conveyor system transports the PCBs through the various stages of the wave soldering process. It typically consists of a conveyor belt or a chain-driven system that moves the boards at a controlled speed.
Fluxer
The fluxer applies a thin layer of flux to the bottom side of the PCB before it enters the solder wave. Flux is a chemical agent that helps remove oxidation from the metal surfaces and promotes better solder wetting.
Preheater
The preheater is used to gradually raise the temperature of the PCB before it reaches the solder wave. Preheating helps activate the flux, removes moisture, and minimizes thermal shock to the components.
Solder Pot
The solder pot contains the molten solder that forms the solder wave. It is typically made of titanium or a ceramic material to withstand the high temperatures and resist erosion.
Solder Wave
The solder wave is the most critical component of the wave soldering process. It is a continuously flowing wave of molten solder that the PCB passes over to create the solder joints. The wave is generated by a pump that circulates the molten solder from the solder pot.
Cooling System
After the PCB passes through the solder wave, it enters the cooling system to solidify the solder joints. The cooling system can be either air-cooled or water-cooled, depending on the specific requirements.
The Wave Soldering Process
The wave soldering process involves several key steps:
Step 1: PCB Preparation
Before the PCB enters the wave soldering machine, it undergoes a preparation process. This includes:
- Component placement: Through-hole components are inserted into the corresponding holes on the PCB.
- Inspection: The PCB is inspected to ensure all components are correctly placed and oriented.
- Masking: Areas of the PCB that should not be soldered, such as connectors or test points, are masked using heat-resistant tapes or coatings.
Step 2: Fluxing
The prepared PCB enters the fluxer, where a thin layer of flux is applied to the bottom side of the board. The flux can be applied using various methods, such as spray fluxing, foam fluxing, or brush fluxing. The type of flux used depends on the specific requirements of the PCB and the soldering process.
Step 3: Preheating
After fluxing, the PCB moves into the preheater section. The preheater gradually raises the temperature of the board to activate the flux and remove moisture. Preheating also helps minimize thermal shock to the components when they come into contact with the molten solder.
The preheating temperature and duration vary depending on the size and thickness of the PCB, as well as the components used. Typical preheating temperatures range from 80°C to 150°C (176°F to 302°F), and the preheating time can be anywhere from 30 seconds to a few minutes.
Step 4: Wave Soldering
The preheated PCB now enters the wave soldering section, where it passes over the molten solder wave. The solder wave is typically created by pumping molten solder through a nozzle or a series of nozzles. The height, shape, and flow rate of the solder wave are carefully controlled to ensure optimal soldering results.
As the PCB moves over the solder wave, the molten solder comes into contact with the exposed metal surfaces of the component leads and the PCB Pads. The solder wets these surfaces, creating a strong mechanical and electrical connection.
The temperature of the molten solder is typically maintained between 240°C and 260°C (464°F to 500°F), depending on the type of solder alloy used. The most common solder alloy for wave soldering is a tin-lead (SnPb) alloy, such as 63/37 (63% tin, 37% lead) or 60/40 (60% tin, 40% lead). However, with the increasing demand for Lead-Free Soldering, lead-free alloys like SAC305 (96.5% tin, 3% silver, 0.5% copper) are also widely used.
Step 5: Cooling
After passing through the solder wave, the PCB enters the cooling section to solidify the solder joints. Cooling can be achieved through various methods, such as air cooling or water cooling.
Air cooling involves using fans or blowers to direct cool air onto the PCB, gradually lowering its temperature. Water cooling, on the other hand, uses a water-cooled conveyor or a spray of cool water to rapidly bring down the temperature of the board.
The cooling process is crucial to ensure the formation of strong and reliable solder joints. Rapid cooling helps prevent the growth of large, brittle intermetallic compounds (IMCs) that can weaken the solder joint.
Step 6: Inspection and Cleaning
Once the PCB has cooled down, it undergoes a final inspection to verify the quality of the solder joints. This can be done visually or using automated optical inspection (AOI) systems. AOI systems use cameras and image processing algorithms to detect any soldering defects, such as bridging, insufficient solder, or lifted components.
After inspection, the PCB may require cleaning to remove any residual flux or contaminants. Cleaning methods include using solvents, aqueous solutions, or de-ionized water, depending on the type of flux used and the cleanliness requirements of the application.
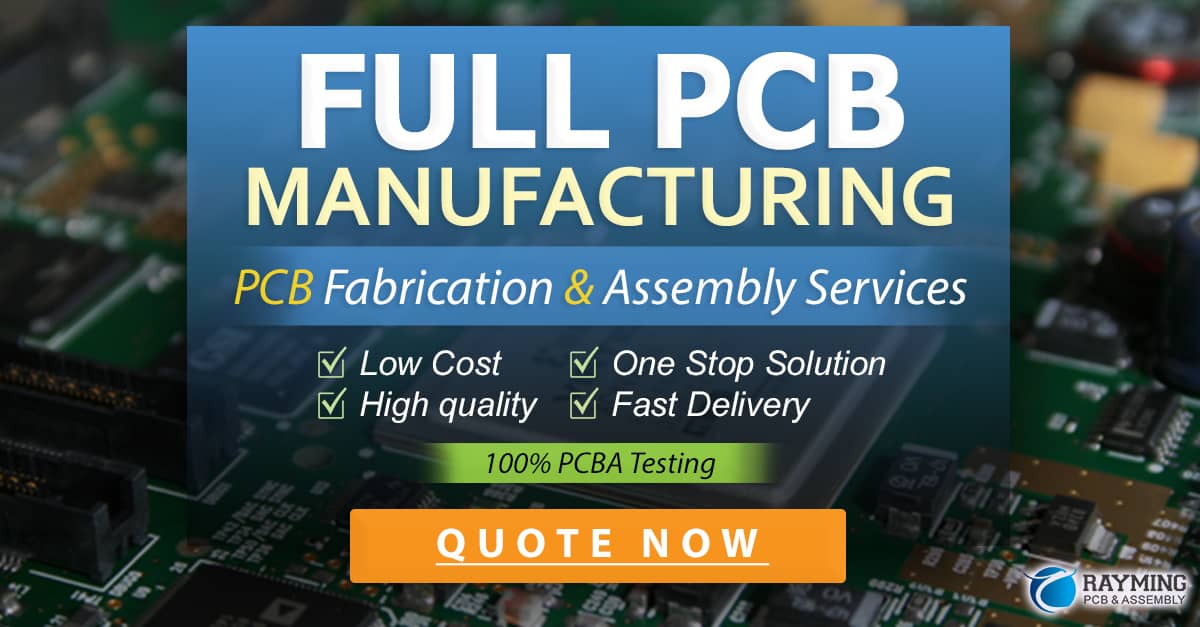
Controlling Wave Soldering Parameters
To achieve optimal soldering results, several key parameters need to be controlled during the wave soldering process:
-
Conveyor speed: The speed at which the PCB moves through the solder wave affects the dwell time (the time the board is in contact with the molten solder). Longer dwell times can lead to overheating and damage to the components, while shorter dwell times may result in insufficient solder wetting.
-
Solder temperature: The temperature of the molten solder must be carefully maintained within the specified range for the solder alloy used. Higher temperatures can cause excessive oxidation and damage to the components, while lower temperatures may lead to poor solder wetting and weak joints.
-
Wave height and shape: The height and shape of the solder wave influence the contact area between the molten solder and the PCB. A well-controlled wave ensures that all the component leads and pads are properly wetted by the solder.
-
Flux type and application: The choice of flux and its application method can affect the soldering quality. The flux must be compatible with the solder alloy and the PCB materials, and it should be applied in the right amount to promote good solder wetting without leaving excessive residues.
-
Preheating temperature and time: The preheating temperature and duration must be optimized based on the PCB design and the components used. Proper preheating ensures that the flux is activated, and the components are not subjected to thermal shock when they come into contact with the molten solder.
Troubleshooting Wave Soldering Defects
Despite careful control of the wave soldering parameters, defects can still occur. Some common wave soldering defects and their causes include:
-
Bridging: Solder bridges form between adjacent pads or leads, causing short circuits. Causes include excessive solder wave height, high solder temperature, or inadequate spacing between components.
-
Insufficient solder: Also known as “dry joints,” insufficient solder leads to weak or incomplete solder joints. Causes include low solder temperature, inadequate flux, or contaminated surfaces.
-
Solder balls: Small spheres of solder that adhere to the PCB surface, potentially causing short circuits. Causes include excessive solder wave height, high solder temperature, or turbulence in the solder wave.
-
Lifted components: Components may lift or shift during the soldering process due to the force of the solder wave. Causes include inadequate component placement, insufficient preheating, or incompatible flux.
To troubleshoot and prevent these defects, it is essential to:
- Optimize the wave soldering parameters based on the PCB design and the components used.
- Ensure proper PCB preparation, including component placement, masking, and cleaning.
- Use compatible flux and solder alloys and apply them in the right amounts.
- Regularly maintain and calibrate the wave soldering equipment to ensure consistent performance.
FAQs
-
Q: Can wave soldering be used for surface mount components?
A: Wave soldering is primarily used for through-hole components. However, some surface mount components can be wave soldered using special techniques like glue dots or adhesive pallets to hold them in place during the soldering process. -
Q: What is the difference between lead-based and lead-free solder alloys in wave soldering?
A: Lead-based solder alloys, such as 63/37 or 60/40 tin-lead (SnPb), have been widely used in wave soldering due to their lower melting point and excellent wetting properties. However, with the increasing environmental and health concerns, lead-free solder alloys like SAC305 (96.5% tin, 3% silver, 0.5% copper) have become more prevalent. Lead-free alloys have higher melting points and may require adjustments to the wave soldering parameters to achieve optimal results. -
Q: How does selective wave soldering differ from conventional wave soldering?
A: Selective wave soldering is a variant of wave soldering that targets specific areas of the PCB, rather than the entire board. It uses a localized solder wave or a nozzle to apply solder only to the desired components or pads. Selective wave soldering is useful for PCBs with a mix of through-hole and surface mount components, or for boards with components that are sensitive to the high temperatures of the conventional wave soldering process. -
Q: What is the role of nitrogen in wave soldering?
A: Nitrogen is sometimes used in wave soldering to create an inert atmosphere around the solder wave. By displacing oxygen, nitrogen helps reduce oxidation of the molten solder and the PCB surfaces, leading to better solder wetting and fewer defects. Nitrogen also helps maintain the stability of the solder wave and reduces solder ball formation. -
Q: How can I optimize the wave soldering process for my specific PCB design?
A: To optimize the wave soldering process for your PCB design, consider the following: - Choose the appropriate solder alloy and flux for your PCB materials and components.
- Design your PCB with adequate spacing between components and pads to minimize bridging and shadowing effects.
- Optimize the conveyor speed, solder temperature, and wave height based on your PCB size, thickness, and component types.
- Conduct test runs and analyze the results to fine-tune the process parameters for your specific design.
- Regularly maintain and calibrate your wave soldering equipment to ensure consistent performance.
Conclusion
Wave soldering is a highly efficient and reliable method for soldering through-hole components onto printed circuit boards. By understanding the fundamentals of wave soldering, the equipment involved, and the step-by-step process, you can optimize your PCB manufacturing process and achieve consistent, high-quality solder joints.
Controlling the key parameters, such as conveyor speed, solder temperature, wave height, and flux application, is crucial for achieving optimal soldering results. Regular maintenance, calibration, and troubleshooting of the wave soldering equipment can help prevent common defects and ensure the long-term reliability of your soldered PCBs.
As the electronics industry continues to evolve, wave soldering remains a vital process for the production of high-quality, reliable electronic assemblies. By staying up-to-date with the latest developments in wave soldering technology and best practices, you can ensure that your PCB manufacturing process remains efficient, cost-effective, and competitive in today’s market.
0 Comments