Introduction to PCB Drilled Holes
Printed Circuit Boards (PCBs) are essential components in modern electronics, providing a platform for interconnecting various electronic components. One crucial aspect of PCB manufacturing is the creation of drilled holes, which serve multiple purposes, such as mounting components, establishing electrical connections between layers, and facilitating heat dissipation. In this article, we will explore the different types of PCB drilled holes, their characteristics, and their applications.
Types of PCB Drilled Holes
Through Holes
Through holes are the most common type of drilled holes found in PCBs. As the name suggests, these holes extend through the entire thickness of the PCB, allowing components to be mounted on one side of the board and soldered on the opposite side. Through holes are typically used for mounting traditional through-hole components, such as resistors, capacitors, and connectors.
Characteristics of Through Holes
- Extend through the entire thickness of the PCB
- Used for mounting through-hole components
- Provide mechanical stability and electrical connectivity
- Require more board space compared to surface-mount components
Applications of Through Holes
- Mounting through-hole components
- Providing electrical connections between layers
- Facilitating heat dissipation for high-power components
- Allowing for manual soldering and inspection
Blind Vias
Blind vias are drilled holes that start from one surface of the PCB and terminate at an internal layer, without extending to the opposite surface. These holes are used to establish electrical connections between the surface layer and one or more internal layers, while conserving board space and improving signal integrity.
Characteristics of Blind Vias
- Start from one surface and terminate at an internal layer
- Used for establishing electrical connections between layers
- Conserve board space compared to through holes
- Improve signal integrity by reducing the length of electrical paths
- Require precise drilling and plating processes
Applications of Blind Vias
- High-density PCB designs with limited board space
- Establishing connections between surface layers and internal power or ground planes
- Reducing signal path length for high-speed applications
- Facilitating the use of advanced packaging techniques, such as chip-scale packaging (CSP)
Buried Vias
Buried vias are drilled holes that are entirely embedded within the internal layers of a PCB, without extending to either surface. These holes are used to establish electrical connections between internal layers, providing a means for efficient routing and signal integrity improvements.
Characteristics of Buried Vias
- Entirely embedded within the internal layers of the PCB
- Used for establishing electrical connections between internal layers
- Conserve board space by eliminating the need for surface connections
- Improve signal integrity by reducing the length of electrical paths
- Require precise alignment and lamination processes
Applications of Buried Vias
- High-density PCB designs with complex routing requirements
- Establishing connections between internal power or ground planes
- Reducing signal path length for high-speed applications
- Facilitating the use of advanced PCB technologies, such as HDI (High-Density Interconnect) and 3D packaging
Micro Vias
Micro vias are small-diameter drilled holes, typically less than 0.15 mm (6 mils), used for establishing high-density interconnections in advanced PCB designs. These holes are often laser-drilled and can be either blind or buried, depending on the specific design requirements.
Characteristics of Micro Vias
- Small-diameter holes, typically less than 0.15 mm (6 mils)
- Used for high-density interconnections in advanced PCB designs
- Can be either blind or buried, depending on the design requirements
- Often laser-drilled for precise control and minimal damage to surrounding materials
- Require specialized manufacturing processes and equipment
Applications of Micro Vias
- High-density interconnect (HDI) PCB designs
- Facilitating the use of fine-pitch components, such as BGAs (Ball Grid Arrays) and CSPs (Chip-Scale Packages)
- Enabling 3D packaging and stacked die configurations
- Improving signal integrity and reducing signal path length in high-speed applications
Plated Through Holes (PTHs)
Plated through holes (PTHs) are drilled holes that are coated with a conductive material, typically copper, to establish electrical connections between layers and provide a means for soldering components. PTHs can be either through holes or blind vias, depending on the specific design requirements.
Characteristics of Plated Through Holes
- Coated with a conductive material, typically copper
- Used for establishing electrical connections between layers and soldering components
- Can be either through holes or blind vias
- Provide mechanical stability and thermal conductivity
- Require precise plating processes to ensure uniform coverage and avoid defects
Applications of Plated Through Holes
- Mounting through-hole components
- Establishing electrical connections between layers
- Providing mechanical stability and thermal conductivity for components
- Facilitating the use of traditional soldering techniques
PCB Drilled Hole Manufacturing Processes
The manufacturing of PCB drilled holes involves several processes, each with its own set of challenges and considerations. The following table summarizes the key processes involved in the creation of various types of PCB drilled holes:
Process | Through Holes | Blind Vias | Buried Vias | Micro Vias | PTHs |
---|---|---|---|---|---|
Drilling | Mechanical | Mechanical or Laser | Mechanical or Laser | Laser | Mechanical |
Plating | Electrolytic or Electroless | Electrolytic or Electroless | Electrolytic or Electroless | Electrolytic or Electroless | Electrolytic or Electroless |
Filling | Not Required | Optional | Optional | Optional | Not Required |
Lamination | Not Required | Required for multi-layer | Required for multi-layer | Required for multi-layer | Not Required |
Drilling Processes
PCB drilled holes can be created using either mechanical drilling or laser drilling, depending on the hole size, precision requirements, and the type of hole being created.
Mechanical Drilling
Mechanical drilling is the most common method for creating through holes and larger blind or buried vias. This process involves using high-speed drill bits to remove material from the PCB substrate. The drill bits are typically made of carbide or diamond-coated materials to ensure durability and precision.
Laser Drilling
Laser drilling is used for creating smaller, high-precision holes, such as micro vias. This process uses focused laser energy to vaporize the PCB substrate material, creating clean and accurate holes without the need for physical contact. Laser drilling is particularly advantageous for creating blind and buried vias, as it allows for precise control over the hole depth and minimizes damage to surrounding materials.
Plating Processes
After drilling, the holes are plated with a conductive material, typically copper, to establish electrical connections and provide a surface for soldering components. There are two main plating processes used in PCB manufacturing:
Electrolytic Plating
Electrolytic plating involves immersing the PCB in an electrolytic solution containing copper ions. An electric current is applied, causing the copper ions to be deposited onto the surface of the holes and any exposed conductive areas. This process is faster and more efficient than electroless plating but requires a conductive surface to initiate the plating process.
Electroless Plating
Electroless plating is a chemical process that deposits a thin layer of copper onto the surface of the holes and any exposed non-conductive areas. This process is slower than electrolytic plating but provides a more uniform coverage and does not require a conductive surface to initiate the plating process. Electroless plating is often used as a pre-treatment step before electrolytic plating to ensure complete coverage of the hole walls.
Filling Processes
In some cases, drilled holes may be filled with a non-conductive material, such as epoxy or resin, to improve the structural integrity of the PCB or to create a smooth surface for subsequent layers. Hole filling is particularly common in high-density PCB designs with blind or buried vias, where the filled holes provide a stable foundation for the lamination of additional layers.
Lamination Processes
For Multi-Layer PCBs with blind or buried vias, the lamination process is critical for creating a cohesive and reliable structure. During lamination, the individual PCB Layers are aligned and bonded together under high pressure and temperature, with the drilled holes serving as interconnects between the layers. Precise alignment and control over the lamination process parameters are essential to ensure the integrity of the interconnections and prevent defects, such as delamination or misregistration.
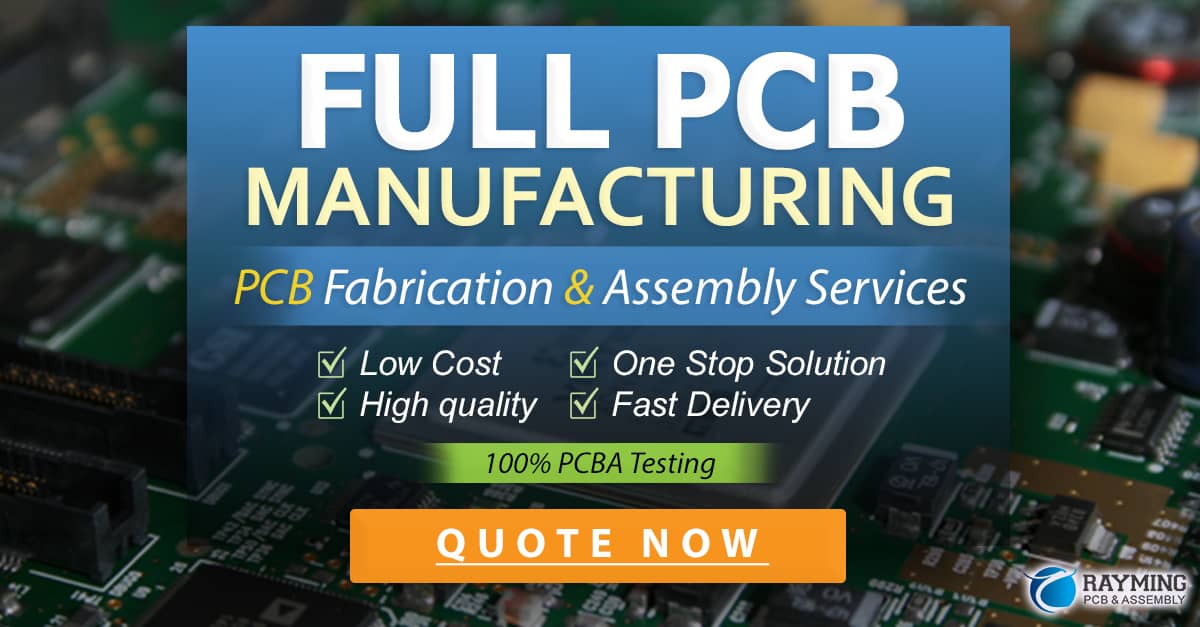
Challenges and Considerations in PCB Drilled Hole Manufacturing
The manufacturing of PCB drilled holes presents several challenges and considerations that must be addressed to ensure the quality, reliability, and functionality of the final product. Some of the key challenges and considerations include:
Hole Size and Aspect Ratio
The size and aspect ratio of the drilled holes can significantly impact the manufacturing process and the overall performance of the PCB. Smaller hole sizes and higher aspect ratios (hole depth to diameter ratio) require more precise drilling and plating processes, as well as tighter control over the materials and equipment used.
Material Selection
The choice of PCB substrate material can affect the drilling and plating processes, as well as the mechanical and thermal properties of the final product. Common PCB substrate materials include FR-4, polyimide, and high-frequency laminates, each with its own set of characteristics and processing requirements.
Plating Uniformity and Adhesion
Ensuring uniform plating coverage and strong adhesion of the conductive material to the hole walls is essential for reliable electrical connections and long-term durability. Factors such as surface cleanliness, plating bath chemistry, and current density must be carefully controlled to achieve optimal results.
Thermal Management
The thermal management of PCBs with drilled holes is a critical consideration, particularly for high-power applications. The holes themselves can serve as thermal vias, providing a path for heat dissipation from components to the PCB substrate or external heat sinks. Proper design and placement of thermal vias can help to minimize thermal stress and improve the overall reliability of the PCB.
Signal Integrity
In high-speed PCB designs, the size, placement, and configuration of drilled holes can have a significant impact on signal integrity. Factors such as hole-to-hole spacing, via stubs, and impedance matching must be carefully considered to minimize signal reflections, crosstalk, and other undesirable effects.
Cost and Manufacturability
The complexity and precision required for the manufacturing of PCB drilled holes can have a direct impact on the overall cost and manufacturability of the PCB. Designers must balance the functional and performance requirements of the PCB with the practical constraints of the manufacturing process, taking into account factors such as hole size, aspect ratio, and the number of layers involved.
Frequently Asked Questions (FAQ)
-
What is the difference between through holes and blind vias?
Through holes extend through the entire thickness of the PCB, while blind vias start from one surface and terminate at an internal layer without reaching the opposite surface. -
What are the advantages of using micro vias in PCB design?
Micro vias offer several advantages, including high-density interconnections, improved signal integrity, reduced signal path length, and compatibility with advanced packaging techniques, such as chip-scale packaging (CSP). -
What is the purpose of plating in PCB drilled holes?
Plating is used to coat the walls of the drilled holes with a conductive material, typically copper, to establish electrical connections between layers and provide a surface for soldering components. -
What are the main challenges in manufacturing PCB drilled holes?
The main challenges in manufacturing PCB drilled holes include achieving precise hole sizes and aspect ratios, ensuring uniform plating coverage and adhesion, managing thermal dissipation, maintaining signal integrity, and balancing cost and manufacturability constraints. -
How do buried vias differ from blind vias?
Buried vias are entirely embedded within the internal layers of a PCB, without extending to either surface, while blind vias start from one surface and terminate at an internal layer. Buried vias are used for establishing connections between internal layers, while blind vias connect surface layers to internal layers.
Conclusion
PCB drilled holes are a critical aspect of PCB manufacturing, serving various purposes, such as component mounting, electrical interconnection, and thermal management. Understanding the different types of PCB drilled holes, their characteristics, and their applications is essential for designing and manufacturing reliable, high-performance electronic devices.
Through holes, blind vias, buried vias, micro vias, and plated through holes each offer unique advantages and are used in specific design scenarios to achieve the desired functionality and performance. The manufacturing processes involved in creating these holes, including drilling, plating, filling, and lamination, require precise control and consideration of various challenges, such as hole size, aspect ratio, material selection, and signal integrity.
As PCB technology continues to advance, with increasing demands for miniaturization, high-speed performance, and reliability, the importance of optimizing PCB drilled holes will only continue to grow. By staying informed about the latest developments and best practices in PCB drilled hole manufacturing, designers and manufacturers can ensure the success of their electronic products in today’s competitive market.
0 Comments