Introduction to PCB Fabrication
Printed Circuit Board (PCB) fabrication is a crucial process in the electronics industry, enabling the creation of complex circuits on a compact and durable substrate. PCB fabrication involves a series of steps that transform a design into a functional board, ready for component assembly. In this article, we will explore the world of turnkey prototype PCB fabrication and assembly, focusing on the key aspects of the process and the benefits it offers to designers and manufacturers alike.
What is a Printed Circuit Board (PCB)?
A Printed Circuit Board, or PCB, is a flat insulating substrate made of fiberglass, composite epoxy, or other laminate material that supports electrical connections using conductive pathways, tracks, or signal traces etched from copper sheets laminated onto the non-conductive substrate. PCBs are used in virtually all electronic devices, from simple single-layer boards to complex multi-layer boards featuring intricate designs.
The Importance of PCB Fabrication
PCB fabrication is essential for creating reliable and efficient electronic devices. By etching conductive pathways onto a non-conductive substrate, designers can create compact and organized circuits that are easy to mass-produce. PCBs offer several advantages over traditional point-to-point wiring, including:
- Increased reliability
- Reduced electronic noise
- Improved heat dissipation
- Compact design
- Lower manufacturing costs
The PCB Fabrication Process
The PCB fabrication process involves several steps that must be carried out with precision to ensure the quality and functionality of the final product. Below, we will explore each step in detail.
Step 1: Design and Layout
The first step in PCB fabrication is the design and layout of the circuit. This is typically done using specialized software, such as Altium Designer, Eagle, or KiCad. The designer creates a schematic diagram of the circuit, which outlines the electrical connections between components. The schematic is then used to create a layout file, which maps out the physical placement of components and the routing of conductive tracks on the PCB.
Step 2: Film Generation
Once the layout is complete, the next step is to generate a set of films that will be used to transfer the circuit pattern onto the PCB substrate. The films are typically made of a transparent plastic material and feature the circuit pattern in a high-contrast format, such as black ink on a clear background. The number of films required depends on the complexity of the circuit and the number of layers in the PCB.
Step 3: PCB Substrate Preparation
The PCB substrate is prepared by cutting it to the desired size and shape. The substrate is then cleaned to remove any dirt, grease, or other contaminants that could affect the adhesion of the copper layers.
Step 4: Copper Lamination
Thin sheets of copper are laminated onto the PCB substrate using heat and pressure. The copper sheets are typically pre-coated with a photo-sensitive resist material that will be used in the next step.
Step 5: Photoresist Exposure
The films generated in Step 2 are aligned with the copper-laminated PCB substrate, and the assembly is exposed to UV light. The areas of the resist material that are exposed to UV light become soluble, while the unexposed areas remain insoluble.
Step 6: Resist Development
The exposed PCB substrate is then placed in a chemical developer solution, which removes the soluble resist material, exposing the copper underneath. The unexposed resist material remains intact, protecting the copper that will form the conductive tracks.
Step 7: Etching
The developed PCB substrate is placed in an etching solution, typically containing ferric chloride or ammonium persulfate. The etching solution removes the exposed copper, leaving only the copper protected by the insoluble resist material. This step creates the conductive tracks that form the actual circuit.
Step 8: Resist Stripping
After etching, the remaining insoluble resist material is stripped away using a chemical solution, revealing the copper tracks.
Step 9: Drilling
Holes are drilled through the PCB substrate to accommodate through-hole components and to create vias that connect different layers in multi-layer boards. The drilling process is typically done using high-speed, computer-controlled drill machines.
Step 10: Plating and Coating
To protect the copper tracks from oxidation and to improve the solderability of the PCB, a thin layer of protective material is applied. This can be done using various methods, such as solder mask application, silkscreen printing, or Organic Solderability Preservative (OSP) coating.
Step 11: Surface Finish
The final step in PCB fabrication is the application of a surface finish, which further enhances the solderability and protects the exposed copper from oxidation. Common surface finishes include Hot Air Solder Leveling (HASL), Electroless Nickel Immersion Gold (ENIG), and Immersion Silver.
PCB Assembly
Once the PCB fabrication process is complete, the next step is to assemble the components onto the board. PCB assembly can be done manually or using automated equipment, depending on the complexity of the circuit and the volume of production.
Manual PCB Assembly
Manual PCB assembly involves hand-placing components onto the board and soldering them in place using a soldering iron. This method is typically used for low-volume production or prototypes, as it is time-consuming and requires skilled technicians.
Automated PCB Assembly
Automated PCB assembly uses machines to place components onto the board and solder them in place. There are two primary methods of automated PCB assembly:
-
Surface Mount Technology (SMT): SMT involves placing surface-mounted components onto pads on the surface of the PCB. The components are then soldered in place using a reflow oven, which melts the solder paste and creates a permanent connection.
-
Through-Hole Technology (THT): THT involves inserting the leads of through-hole components into holes drilled in the PCB. The leads are then soldered in place on the opposite side of the board.
Automated PCB assembly offers several advantages over manual assembly, including:
- Increased speed and efficiency
- Improved accuracy and consistency
- Reduced labor costs
- Higher production volumes
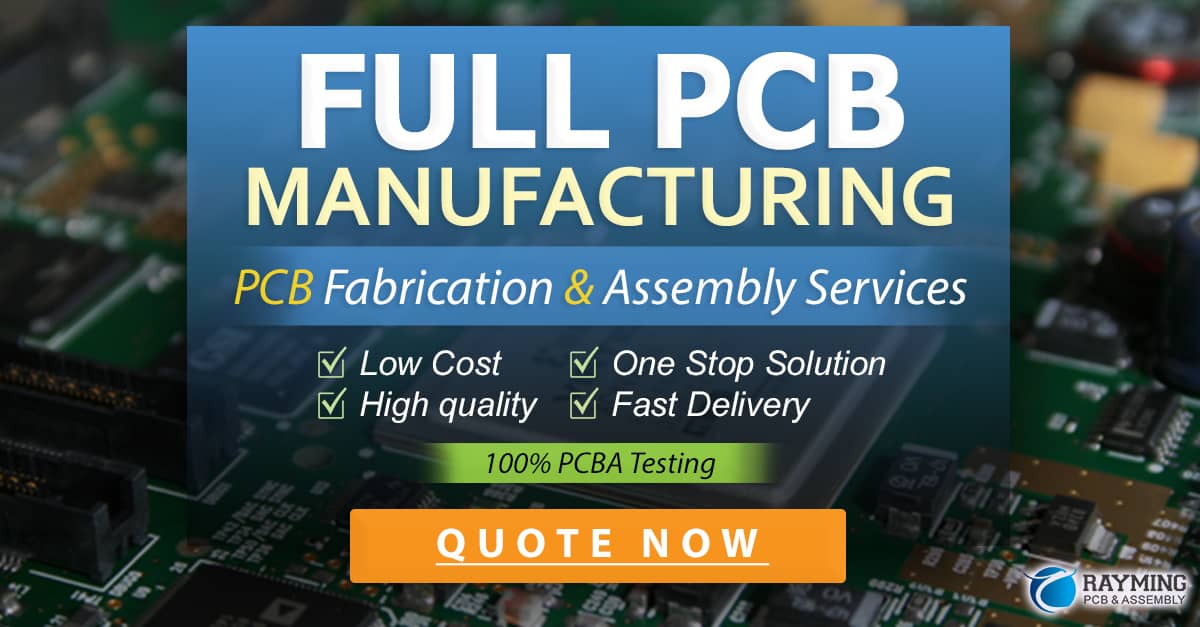
Turnkey Prototype PCB Fabrication and Assembly
Turnkey prototype PCB fabrication and assembly is a comprehensive service that combines both the fabrication and assembly processes, providing a complete solution for designers and manufacturers. By outsourcing the entire process to a single provider, companies can save time and resources, while ensuring a high-quality final product.
Benefits of Turnkey Prototype PCB Fabrication and Assembly
-
Time-saving: By outsourcing the entire process to a single provider, companies can reduce the time required to bring a product to market.
-
Cost-effective: Turnkey services often offer competitive pricing, as the provider can optimize the fabrication and assembly processes for efficiency and cost-effectiveness.
-
Expertise: Turnkey providers have the knowledge and experience necessary to handle complex PCB designs and assembly requirements.
-
Quality control: Turnkey providers typically have strict quality control measures in place to ensure the final product meets the required specifications.
-
Scalability: Turnkey services can accommodate a wide range of production volumes, from low-volume prototypes to high-volume production runs.
Choosing a Turnkey Prototype PCB Fabrication and Assembly Provider
When selecting a turnkey prototype PCB fabrication and assembly provider, consider the following factors:
-
Experience: Choose a provider with a proven track record of delivering high-quality PCBs and assemblies.
-
Capabilities: Ensure the provider has the necessary equipment and expertise to handle your specific PCB design and assembly requirements.
-
Turnaround time: Consider the provider’s lead times and ensure they can meet your project deadlines.
-
Quality control: Inquire about the provider’s quality control measures and certifications, such as ISO 9001 or IPC class standards.
-
Customer support: Choose a provider that offers responsive and knowledgeable customer support to help you through the fabrication and assembly process.
Future Trends in PCB Fabrication and Assembly
As the electronics industry continues to evolve, PCB fabrication and assembly processes are adapting to meet new challenges and demands. Some of the key trends shaping the future of PCB fabrication and assembly include:
-
Miniaturization: The trend towards smaller, more compact electronic devices is driving the development of advanced PCB fabrication techniques, such as High-Density Interconnect (HDI) and embedded components.
-
Flexible and stretchable PCBs: The growing demand for wearable electronics and flexible devices is leading to the development of flexible and stretchable PCBs that can conform to various shapes and withstand repeated bending and stretching.
-
3D printing: Additive manufacturing techniques, such as 3D printing, are being explored as an alternative to traditional PCB fabrication methods. 3D printing offers the potential for rapid prototyping and the creation of complex, three-dimensional circuit structures.
-
Automation and AI: Advances in automation and artificial intelligence are enabling more efficient and intelligent PCB assembly processes. Machine learning algorithms can optimize component placement and routing, while robotics can improve the speed and accuracy of assembly tasks.
-
Sustainable materials and processes: As environmental concerns continue to grow, there is an increasing focus on developing sustainable PCB fabrication and assembly processes. This includes the use of eco-friendly materials, such as biodegradable PCB substrates, and the adoption of green manufacturing practices that reduce waste and energy consumption.
Conclusion
Turnkey prototype PCB fabrication and assembly is a comprehensive solution that streamlines the process of creating functional electronic devices. By combining the fabrication and assembly processes under one roof, turnkey providers can offer designers and manufacturers a cost-effective, time-saving, and high-quality solution for their PCB needs.
As the electronics industry continues to evolve, PCB fabrication and assembly processes will adapt to meet new challenges and demands. By staying informed about the latest trends and technologies, designers and manufacturers can ensure they are well-positioned to take advantage of the opportunities presented by the future of PCB fabrication and assembly.
Frequently Asked Questions (FAQ)
-
What is the difference between PCB fabrication and assembly?
PCB fabrication is the process of creating the printed circuit board itself, including the etching of conductive tracks and the application of protective coatings. PCB assembly is the process of placing and soldering components onto the fabricated board. -
What are the advantages of using a turnkey prototype PCB fabrication and assembly service?
Turnkey services offer several advantages, including time-saving, cost-effectiveness, expertise, quality control, and scalability. By outsourcing the entire process to a single provider, companies can streamline their PCB fabrication and assembly needs. -
What factors should I consider when choosing a turnkey prototype PCB fabrication and assembly provider?
When selecting a provider, consider their experience, capabilities, turnaround time, quality control measures, and customer support. Choose a provider that can meet your specific PCB design and assembly requirements while delivering a high-quality final product. -
What are some of the future trends in PCB fabrication and assembly?
Some of the key trends shaping the future of PCB fabrication and assembly include miniaturization, flexible and stretchable PCBs, 3D printing, automation and AI, and sustainable materials and processes. -
How can I ensure the quality of my PCBs when using a turnkey prototype PCB fabrication and assembly service?
To ensure the quality of your PCBs, choose a provider with strict quality control measures and certifications, such as ISO 9001 or IPC class standards. Additionally, provide clear and detailed design specifications, and maintain open communication with your provider throughout the fabrication and assembly process.
0 Comments