Introduction to PCB Lamination
PCB lamination is a critical process in the manufacturing of printed circuit boards (PCBs). It involves bonding together multiple layers of PCB material using heat, pressure, and adhesive to create a single, unified board. The lamination process ensures that the PCB layers are properly aligned and securely bonded, providing the necessary electrical insulation and mechanical strength for the final product.
Sequential lamination, also known as sequential build-up (SBU), is a specific technique used in PCB lamination. Unlike traditional lamination methods that bond all layers simultaneously, sequential lamination builds up the PCB layer by layer. This approach offers several advantages, such as improved control over layer alignment, reduced stress on the board, and the ability to incorporate embedded components and high-density interconnects (HDIs).
In this article, we will explore the top trends and techniques in sequential lamination PCB manufacturing. We will discuss the benefits of sequential lamination, the materials and equipment used, and the latest advancements in this field. By understanding these trends and techniques, PCB designers and manufacturers can leverage sequential lamination to create high-quality, reliable, and innovative PCBs for various applications.
Benefits of Sequential Lamination
Improved Layer Alignment
One of the primary benefits of sequential lamination is improved layer alignment. In traditional lamination methods, all layers are bonded simultaneously, which can result in misalignment due to thermal expansion and contraction of the materials. Sequential lamination addresses this issue by building up the PCB layer by layer, allowing for precise alignment and registration of each layer.
Reduced Stress on the Board
Sequential lamination also reduces stress on the PCB during the manufacturing process. By laminating layers individually, the board experiences less thermal and mechanical stress compared to traditional lamination methods. This reduction in stress minimizes the risk of warping, delamination, and other defects that can compromise the integrity of the PCB.
Embedding Components and HDIs
Sequential lamination enables the incorporation of embedded components and HDIs into the PCB. Embedded components, such as resistors, capacitors, and ICs, are placed within the PCB layers during the lamination process. This technique saves space on the board surface, reduces the overall size of the PCB, and improves signal integrity by minimizing the distance between components.
HDIs, which involve fine-pitch vias and micro-vias, can also be achieved using sequential lamination. The layer-by-layer build-up allows for the precise placement of micro-vias, enabling higher interconnect density and improved signal routing.
Flexibility in Material Selection
Sequential lamination offers flexibility in material selection for each layer of the PCB. Different materials can be used for specific layers based on their electrical and mechanical properties. For example, high-frequency materials can be used for signal layers, while standard FR-4 can be used for power and ground layers. This flexibility allows for optimized PCB designs that meet specific application requirements.
Materials and Equipment for Sequential Lamination
PCB Laminates
PCB laminates are the base materials used in the lamination process. They consist of a reinforcement material, such as glass fiber, impregnated with a resin, typically epoxy. The choice of laminate material depends on the desired electrical and mechanical properties of the PCB. Common laminate materials include FR-4, high-Tg FR-4, polyimide, and PTFE.
Prepregs
Prepregs are partially cured sheets of resin-impregnated reinforcement material. They are used as adhesive layers between the PCB laminates during the lamination process. Prepregs come in various thicknesses and resin content to accommodate different PCB designs and requirements.
Lamination Presses
Lamination presses are used to apply heat and pressure to the PCB layers during the lamination process. There are two main types of lamination presses: hydraulic presses and vacuum presses.
Hydraulic presses use hydraulic cylinders to apply pressure to the PCB stack. They are suitable for high-volume production and can handle larger PCB sizes.
Vacuum presses, on the other hand, use a vacuum chamber to remove air from the PCB stack before applying heat and pressure. Vacuum presses provide more uniform pressure distribution and are ideal for laminating high-density PCBs with fine features.
Lamination Process Control Equipment
Lamination process control equipment is used to monitor and control the lamination parameters, such as temperature, pressure, and time. This equipment ensures that the lamination process is consistent and repeatable, resulting in high-quality PCBs.
Some examples of lamination process control equipment include:
- Temperature controllers: Used to regulate the temperature of the lamination press.
- Pressure gauges: Used to monitor and control the pressure applied during lamination.
- Timers: Used to control the duration of the lamination cycle.
- Data loggers: Used to record and store lamination process data for quality control and traceability purposes.
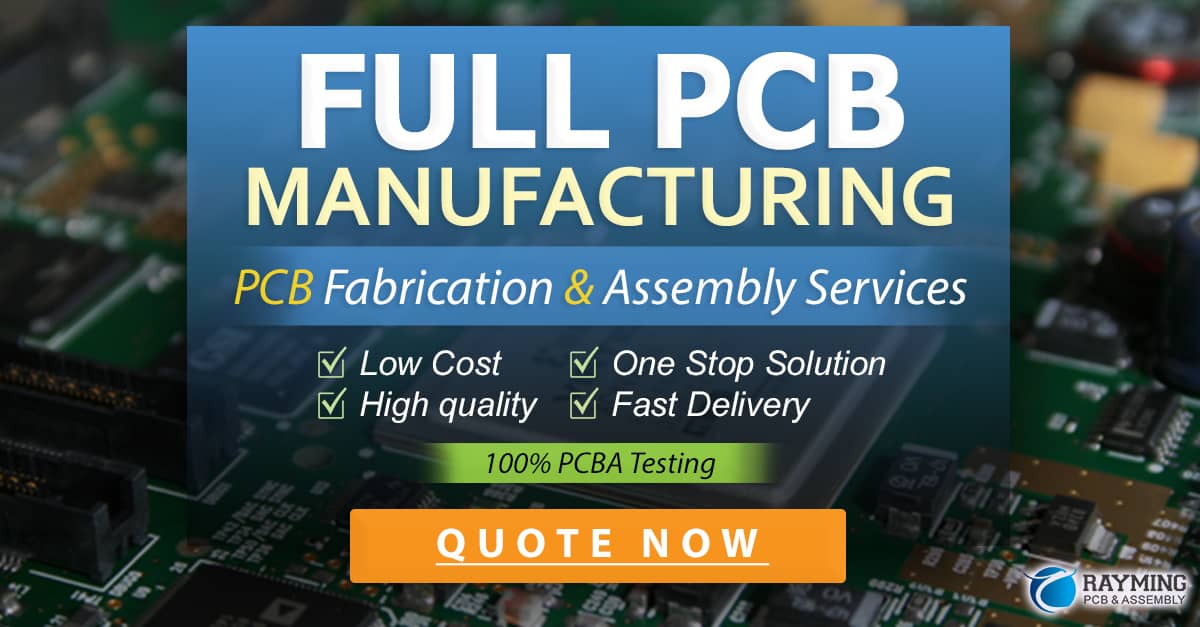
Latest Advancements in Sequential Lamination
Laser Direct Imaging (LDI)
Laser direct imaging (LDI) is a technology that uses lasers to directly image the PCB layers without the need for traditional photomasks. LDI enables high-resolution patterning and registration, making it ideal for sequential lamination PCBs with fine features and HDIs.
3D Printing for Prototyping
3D printing technology is being used to create rapid prototypes of PCBs before committing to full-scale production. 3D-printed PCBs can be used to validate design concepts, test functionality, and identify potential issues early in the development process. This approach reduces development time and costs, allowing for faster time-to-market.
Automated Optical Inspection (AOI)
Automated optical inspection (AOI) systems are used to inspect PCBs for defects and anomalies during the manufacturing process. AOI systems use cameras and image processing algorithms to detect issues such as shorts, opens, and misalignments. The integration of AOI into the sequential lamination process ensures that defects are caught early, reducing the risk of costly rework or scrap.
Advanced Materials
Researchers are continuously developing advanced materials for PCB lamination to meet the demands of emerging technologies. Some examples include:
- Low-loss materials: These materials have low dielectric constant and loss tangent, making them suitable for high-frequency applications such as 5G and millimeter-wave communications.
- Thermally conductive materials: These materials have high thermal conductivity, allowing for efficient heat dissipation in high-power applications.
- Flexible materials: Flexible PCB materials enable the creation of bendable and stretchable circuits for wearable electronics and IoT devices.
Frequently Asked Questions (FAQ)
1. What is the difference between sequential lamination and traditional lamination?
Traditional lamination bonds all PCB layers simultaneously, while sequential lamination builds up the PCB layer by layer. Sequential lamination offers improved layer alignment, reduced stress on the board, and the ability to incorporate embedded components and HDIs.
2. What are the advantages of using sequential lamination for PCB manufacturing?
The advantages of sequential lamination include improved layer alignment, reduced stress on the board, the ability to embed components and HDIs, and flexibility in material selection for each layer.
3. What materials are used in sequential lamination PCBs?
The materials used in sequential lamination PCBs include PCB laminates (e.g., FR-4, polyimide, PTFE), prepregs, and advanced materials such as low-loss, thermally conductive, and flexible materials.
4. What equipment is used in the sequential lamination process?
The equipment used in the sequential lamination process includes lamination presses (hydraulic and vacuum), lamination process control equipment (temperature controllers, pressure gauges, timers, data loggers), laser direct imaging systems, and automated optical inspection systems.
5. What are some of the latest advancements in sequential lamination technology?
Some of the latest advancements in sequential lamination technology include laser direct imaging for high-resolution patterning, 3D printing for rapid prototyping, automated optical inspection for defect detection, and the development of advanced materials for specific applications.
Conclusion
Sequential lamination PCB technology offers numerous benefits and opportunities for the electronics industry. By building up PCBs layer by layer, sequential lamination enables improved layer alignment, reduced stress on the board, and the incorporation of embedded components and HDIs. The flexibility in material selection and the latest advancements in imaging, inspection, and materials further enhance the capabilities of sequential lamination PCBs.
As the demand for high-performance, miniaturized, and reliable electronics continues to grow, sequential lamination will play a crucial role in meeting these requirements. PCB designers and manufacturers who stay up-to-date with the latest trends and techniques in sequential lamination will be well-positioned to create innovative and competitive products in the market.
By understanding the benefits, materials, equipment, and advancements in sequential lamination, the electronics industry can leverage this technology to push the boundaries of PCB design and manufacturing. As research and development in this field continue, we can expect to see even more exciting developments in sequential lamination PCB technology in the future.
0 Comments