What are RoHS-Compliant Circuit Boards?
RoHS stands for “Restriction of Hazardous Substances”. It is an EU directive that restricts the use of certain hazardous materials in the manufacture of electronic and electrical equipment. The goal is to reduce the environmental and health risks associated with e-waste.
RoHS-compliant circuit boards are printed circuit boards (PCBs) that meet the requirements of the RoHS directive. This means they do not contain more than the maximum allowed levels of these restricted substances:
Substance | Maximum Limit |
---|---|
Lead (Pb) | 0.1% |
Mercury (Hg) | 0.1% |
Cadmium (Cd) | 0.01% |
Hexavalent Chromium (Cr6+) | 0.1% |
Polybrominated Biphenyls (PBB) | 0.1% |
Polybrominated Diphenyl Ethers (PBDE) | 0.1% |
All homogeneous materials in the PCB must meet these limits. A homogeneous material is one that cannot be mechanically disjointed into different materials. For example, the plastic insulation on a wire is a homogeneous material, but the wire as a whole is not.
Benefits of Using RoHS-Compliant PCBs
There are several important benefits to using RoHS-compliant circuit boards:
-
Environmental protection – By reducing the use of hazardous substances, RoHS helps minimize the environmental impact of e-waste. When old electronics end up in landfills, these toxic materials can leach into the soil and water.
-
Human health and safety – Exposure to substances like lead and mercury is linked to various health problems. RoHS aims to reduce occupational exposure for electronics workers as well as contamination of air, water, and soil that could impact surrounding communities.
-
Easier recycling – RoHS-compliant boards are easier to recycle since they contain fewer hazardous materials that require special handling. This supports a circular economy.
-
Legal compliance – For electronics sold in the EU market, RoHS compliance is mandatory. Using compliant PCBs ensures your products meet these legal requirements. Other countries have similar laws modeled after RoHS.
-
Improved reliability – Some RoHS-compliant PCB finishes, like immersion silver and OSP, can enhance the reliability and longevity of the boards compared to non-RoHS finishes like HASL (hot air solder leveling).
How are RoHS-Compliant PCBs Manufactured?
The manufacturing process for RoHS-compliant PCBs is largely the same as for traditional PCBs. The key difference is in the materials used. Here’s a quick overview of the process:
-
PCB Design – The circuit board is designed using EDA (electronic design automation) software. The design specifies the layout of the board, including the placement of components and routing of traces.
-
Material Selection – RoHS-compliant base materials, like FR-4 laminates, are chosen. These must not contain the restricted substances above the allowed limits.
-
PCB Fabrication – The bare board is fabricated using standard processes like etching, drilling, and plating. However, the chemicals and processes used must be RoHS-compliant. For example, lead-free solder is used instead of leaded solder.
-
Component Assembly – The electronic components are soldered onto the board. Again, lead-free solder is used. RoHS-compliant components are selected to ensure the entire board is compliant.
-
Testing and Inspection – The assembled PCB undergoes various tests to verify its functionality and RoHS compliance. This may include X-ray fluorescence (XRF) testing to check for the presence of restricted substances.
Challenges of RoHS Compliance
While necessary and beneficial, RoHS compliance does present some challenges for PCB manufacturers:
-
Higher melting point of lead-free solder – Lead-free solder typically has a higher melting point than leaded solder. This requires higher processing temperatures, which can stress components and the board itself.
-
Whisker growth – Some lead-free finishes, particularly tin, are prone to the growth of small conductive filaments known as whiskers. These can cause short circuits.
-
Supply chain management – Ensuring RoHS compliance requires careful management of the supply chain to ensure all raw materials and components are compliant. This can be challenging, particularly for complex, multi-part components.
-
Cost – RoHS-compliant materials and processes can be more expensive than traditional ones. However, the cost difference has decreased over time as RoHS has become more widely adopted.
Despite these challenges, the electronics industry has successfully adapted to RoHS requirements. Ongoing research and development continue to improve RoHS-compliant materials and processes.
Choosing the Right RoHS-Compliant PCB
When selecting a RoHS-compliant PCB for your project, there are several key factors to consider:
Base Material
The most common base material for RoHS-compliant PCBs is FR-4, a glass-reinforced epoxy laminate. It offers good mechanical strength, electrical insulation, and heat resistance. However, there are also other RoHS-compliant base materials available for specialized applications:
Material | Characteristics | Typical Applications |
---|---|---|
Polyimide | High heat resistance, flexible | Aerospace, military, high-temperature environments |
Rogers RO4000 Series | Low dielectric constant and loss, stable at high frequencies | High-frequency applications like RF and microwave |
Isola IS410 | Low dissipation factor, high thermal reliability | Automotive, telecommunications |
PCB Finish
The PCB finish is the surface coating applied to the copper traces to prevent oxidation and enhance solderability. Common RoHS-compliant finishes include:
Finish | Pros | Cons |
---|---|---|
Immersion Tin | Good solderability, low cost | Prone to whisker growth |
Immersion Silver | Excellent solderability, flat surface | More expensive than tin, can tarnish over time |
Organic Solderability Preservative (OSP) | Low cost, good for fine-pitch components | Limited shelf life, not suitable for multiple reflow cycles |
Electroless Nickel Immersion Gold (ENIG) | Good shelf life, suitable for gold wire bonding | More expensive, risk of black pad syndrome |
The right finish depends on your specific application, budget, and reliability requirements.
Supplier Selection
Choosing a reputable PCB supplier is critical to ensuring RoHS compliance. When evaluating potential suppliers, consider:
-
RoHS Certification – Does the supplier have a RoHS compliance certificate? This should be issued by a third-party testing agency.
-
Testing Capabilities – What testing equipment and procedures does the supplier use to verify RoHS compliance? XRF testing is the gold standard.
-
Supply Chain Management – How does the supplier ensure their raw materials and components are RoHS-compliant?
-
Experience and Reputation – Look for a supplier with a proven track record of producing high-quality, RoHS-compliant PCBs.
Working with a knowledgeable and reliable supplier can help navigate the complexities of RoHS compliance and ensure your PCBs meet all necessary requirements.
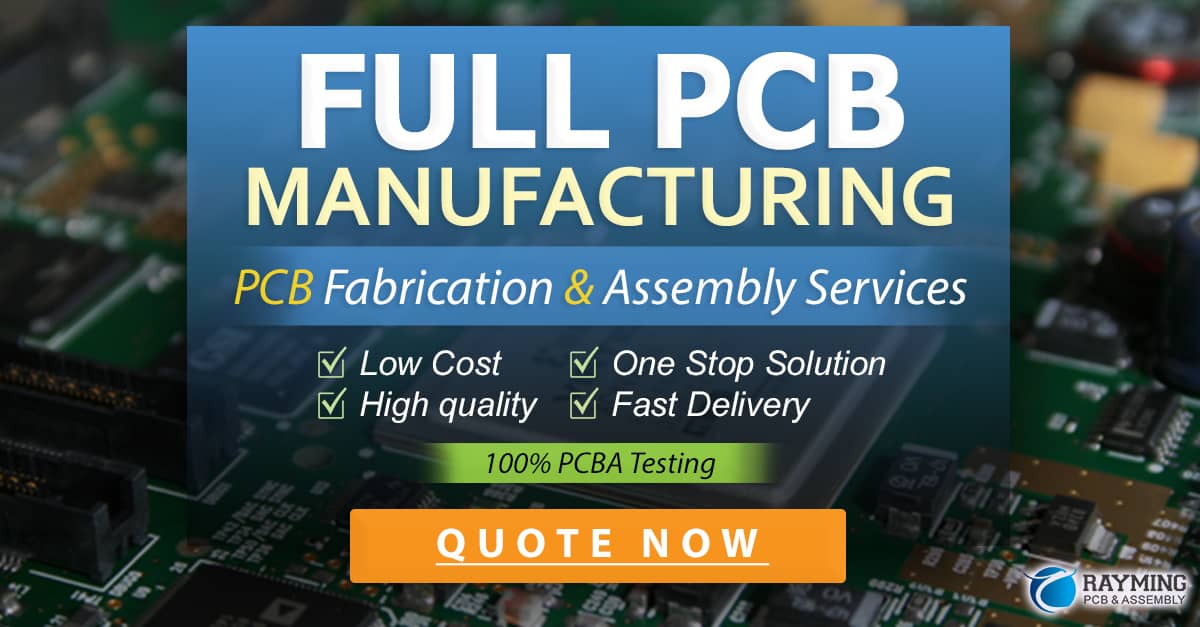
Frequently Asked Questions (FAQ)
1. What happens if I use a non-RoHS-compliant PCB in my product?
If your product is intended for sale in the EU or other markets that have RoHS-type regulations, using a non-compliant PCB could prevent your product from being legally sold in those markets. It could also result in fines or other penalties.
2. Are all electronic components RoHS-compliant?
No, not all electronic components are RoHS-compliant. While RoHS compliance is now widespread, some components, particularly older or specialized parts, may still contain restricted substances. It’s important to verify the RoHS compliance of all components used in your PCB.
3. Can I tell if a PCB is RoHS-compliant just by looking at it?
No, RoHS compliance cannot be determined visually. The restricted substances can be present in small amounts that aren’t visible to the naked eye. XRF testing or other analytical methods are needed to verify compliance.
4. Do RoHS-compliant PCBs cost more than non-compliant ones?
In general, RoHS-compliant PCBs may cost slightly more than non-compliant ones due to the use of specialized materials and processes. However, the cost difference has decreased significantly as RoHS has become the industry standard.
5. Where can I find more information about RoHS and its requirements?
The official EU RoHS directive is a good place to start. The IPC (Association Connecting Electronics Industries) also has a wealth of resources on RoHS and other environmental regulations impacting the electronics industry. Your PCB supplier should also be able to provide guidance on RoHS compliance.
0 Comments