What is a Rigid-Flex PCB?
A Rigid-Flex PCB is a printed circuit board that combines both rigid and flexible substrates, allowing for a more compact and reliable design compared to using separate rigid and flexible PCBs connected by wires or connectors. The rigid portions of the board provide structural support and house most of the components, while the flexible portions allow for bending and folding, enabling 3D configurations and reducing the overall size of the device.
Advantages of Rigid-Flex PCBs
- Space savings and reduced weight
- Improved reliability and durability
- Reduced assembly time and costs
- Enhanced signal integrity
- Increased design flexibility
Rigid-Flex PCB Manufacturing Process Overview
The Rigid-Flex PCB manufacturing process involves several key steps:
- Design and Layout
- Material Selection
- Fabrication
- Lamination
- Drilling and Plating
- Etching
- Solder Mask Application
- Surface Finish
- Cutting and Routing
- Quality Control and Inspection
1. Design and Layout
The first step in the Rigid-Flex PCB manufacturing process is to create a detailed design and layout using specialized CAD software. The design must consider factors such as:
- Component placement
- Layer stackup
- Bend radius and location of flexible regions
- Impedance control
- Signal integrity
- Thermal management
2. Material Selection
Choosing the right materials for a Rigid-Flex PCB is crucial for ensuring its performance and reliability. The most common materials used are:
Material | Description | Advantages |
---|---|---|
FR-4 | Glass-reinforced epoxy laminate | Rigid, cost-effective, and widely available |
Polyimide | High-performance polymer | Flexible, high-temperature resistance, and excellent electrical properties |
Coverlay | Polyimide-based cover layer | Provides protection and insulation for flexible regions |
Adhesives | Epoxy or acrylic-based | Bonds the rigid and flexible layers together |
3. Fabrication
The fabrication process involves creating the individual layers of the Rigid-Flex PCB. This typically includes:
- Printing the circuit patterns onto the copper-clad laminates using photolithography
- Etching away the unwanted copper to create the desired traces and pads
- Laminating the flexible layers with adhesives and coverlays
- Preparing the rigid layers for lamination
4. Lamination
During the lamination process, the rigid and flexible layers are combined using heat and pressure. The adhesives bond the layers together, creating a single, unified structure. The lamination process must be carefully controlled to ensure proper alignment and avoid damaging the flexible regions.
5. Drilling and Plating
After lamination, holes are drilled through the Rigid-Flex PCB to accommodate through-hole components and vias. These holes are then plated with copper to create electrical connections between layers. Specialized drilling techniques, such as controlled-depth drilling, may be used to avoid damaging the flexible layers.
6. Etching
The next step is to etch away the unwanted copper from the outer layers of the Rigid-Flex PCB. This is typically done using a chemical etching process, which selectively removes the copper while leaving the desired traces and pads intact.
7. Solder Mask Application
A solder mask is applied to the Rigid-Flex PCB to protect the copper traces and prevent short circuits during soldering. The solder mask is typically a green or black polymer coating that is selectively applied using photolithography.
8. Surface Finish
A surface finish is applied to the exposed copper areas of the Rigid-Flex PCB to improve solderability and protect against oxidation. Common surface finishes include:
- Hot Air Solder Leveling (HASL)
- Immersion Silver
- Electroless Nickel Immersion Gold (ENIG)
- Immersion Tin
9. Cutting and Routing
The final step in the Rigid-Flex PCB manufacturing process is to cut and route the board to its final shape and size. This is typically done using a CNC router or laser cutter. The cutting and routing process must be carefully controlled to avoid damaging the flexible regions and ensure a clean, precise finish.
10. Quality Control and Inspection
Throughout the Rigid-Flex PCB manufacturing process, strict quality control measures are implemented to ensure the highest level of reliability and performance. This includes:
- Visual inspection
- Automated Optical Inspection (AOI)
- Electrical testing
- Microsectioning
- Thermal cycling
- Bend testing
By adhering to these quality control standards, manufacturers can ensure that their Rigid-Flex PCBs meet the required specifications and perform reliably in the field.
Challenges in Rigid-Flex PCB Manufacturing
While Rigid-Flex PCBs offer numerous advantages, their manufacturing process presents several challenges that must be addressed:
-
Design Complexity: Designing a Rigid-Flex PCB requires specialized knowledge and experience to ensure proper functionality and reliability. Designers must consider factors such as bend radius, layer stackup, and material selection to optimize the board’s performance.
-
Material Compatibility: The materials used in Rigid-Flex PCBs must be carefully selected to ensure compatibility and minimize stress during bending. Incompatible materials can lead to delamination, cracking, or other failures.
-
Lamination Process: The lamination process for Rigid-Flex PCBs is more complex than for traditional rigid PCBs. The flexible layers must be properly aligned and bonded to the rigid layers without causing damage or distortion.
-
Drilling and Plating: Drilling and plating through the flexible layers of a Rigid-Flex PCB requires specialized techniques to avoid damaging the delicate materials. Controlled-depth drilling and careful plating process control are essential.
-
Handling and Assembly: Rigid-Flex PCBs are more susceptible to damage during handling and assembly due to the presence of flexible regions. Special care must be taken to avoid excessive bending or stress on the board during these processes.
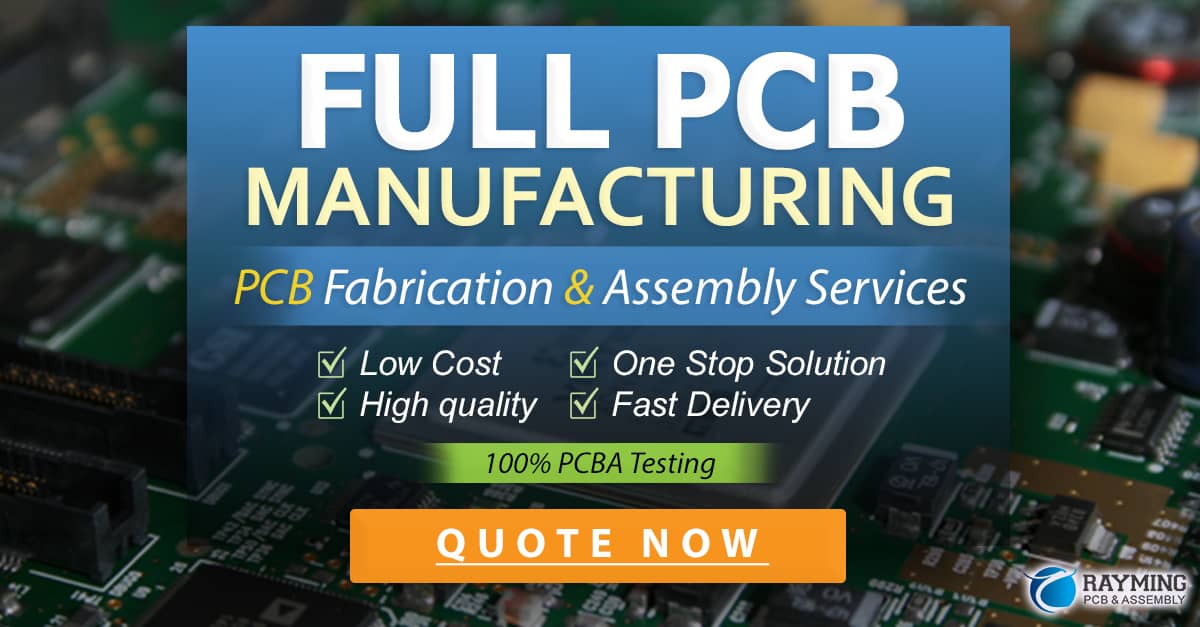
Best Practices for Rigid-Flex PCB Design and Manufacturing
To ensure the success of a Rigid-Flex PCB project, designers and manufacturers should follow these best practices:
-
Collaborate Early: Involve the manufacturer early in the design process to ensure that the Rigid-Flex PCB can be efficiently and reliably produced. The manufacturer can provide valuable input on material selection, layer stackup, and design for manufacturability.
-
Use Appropriate Materials: Select materials that are compatible and suitable for the specific application. Consider factors such as flexibility, temperature resistance, and electrical properties when choosing substrates, adhesives, and finishes.
-
Optimize Bend Radius: Design the flexible regions with an appropriate bend radius to minimize stress and prevent damage. The bend radius should be at least 6-10 times the thickness of the flexible material.
-
Plan for Strain Relief: Incorporate strain relief features, such as stiffeners or support structures, to minimize stress on the flexible regions during bending and assembly.
-
Implement Strict Quality Control: Establish and maintain strict quality control measures throughout the manufacturing process to ensure the highest level of reliability and performance. This includes regular inspections, testing, and documentation.
Frequently Asked Questions (FAQ)
-
What is the typical turnaround time for a Rigid-Flex PCB project?
The turnaround time for a Rigid-Flex PCB project depends on various factors, such as the complexity of the design, the materials used, and the manufacturing process. On average, a Rigid-Flex PCB project can take 3-5 weeks from design to delivery, but this can vary depending on the specific requirements of the project. -
How do I choose the right manufacturer for my Rigid-Flex PCB project?
When selecting a manufacturer for your Rigid-Flex PCB project, consider factors such as their experience with Rigid-Flex PCBs, their manufacturing capabilities, their quality control processes, and their customer support. Look for a manufacturer that has a proven track record of successfully delivering Rigid-Flex PCB projects similar to yours. -
What is the minimum bend radius for a Rigid-Flex PCB?
The minimum bend radius for a Rigid-Flex PCB depends on the thickness and material properties of the flexible layers. As a general rule, the bend radius should be at least 6-10 times the thickness of the flexible material to minimize stress and prevent damage. However, the specific minimum bend radius for your project should be determined in consultation with your manufacturer. -
Can Rigid-Flex PCBs be reworked or repaired?
Reworking or repairing a Rigid-Flex PCB can be challenging due to the presence of flexible regions and the complex lamination process. In some cases, minor repairs may be possible, but extensive rework or repair is often not recommended. It is generally best to prevent the need for rework or repair through careful design, manufacturing, and handling processes. -
How do I test and validate my Rigid-Flex PCB design?
Testing and validating your Rigid-Flex PCB design involves several steps, including: - Design rule checks (DRC) to ensure that the design meets the manufacturer’s specifications
- Signal integrity simulations to verify the performance of critical signals
- Thermal analysis to ensure that the board can dissipate heat effectively
- Mechanical simulations to assess the stress and strain on the flexible regions during bending
- Prototype testing to validate the functionality and reliability of the final product
By working closely with your manufacturer and following best practices for design and testing, you can ensure that your Rigid-Flex PCB performs reliably and meets your application’s requirements.
Conclusion
Rigid-Flex PCBs offer numerous advantages over traditional rigid PCBs, including space savings, improved reliability, and increased design flexibility. However, the manufacturing process for Rigid-Flex PCBs is more complex and challenging than for rigid PCBs, requiring specialized knowledge, materials, and processes.
To ensure the success of a Rigid-Flex PCB project, designers and manufacturers must collaborate closely, follow best practices for design and manufacturing, and implement strict quality control measures throughout the process. By understanding the key steps and challenges involved in Rigid-Flex PCB manufacturing, designers can create more effective and reliable products that meet the demands of today’s increasingly complex electronic devices.
As the demand for smaller, more reliable, and more flexible electronic devices continues to grow, Rigid-Flex PCBs will play an increasingly important role in the electronics industry. By staying up-to-date with the latest developments in Rigid-Flex PCB technology and working with experienced manufacturers, designers can unlock the full potential of this innovative technology and create products that push the boundaries of what is possible.
0 Comments