Understanding Circuit Boards and Their Importance
Before diving into the signs that suggest the need for a circuit board test, let’s briefly understand what circuit boards are and their significance in electronic devices.
What Are Circuit Boards?
A circuit board, also known as a printed circuit board (PCB), is a flat board made of insulating material, such as fiberglass or plastic, with conductive pathways etched or printed onto its surface. These pathways, called traces, connect various electronic components like resistors, capacitors, and integrated circuits (ICs) to form a complete electronic circuit.
The Role of Circuit Boards in Electronic Devices
Circuit boards play a crucial role in electronic devices by providing a platform for interconnecting electronic components and enabling the flow of electrical signals between them. They offer several advantages over traditional point-to-point wiring, including:
- Compact design: PCBs allow for the dense packaging of electronic components, resulting in smaller and more portable devices.
- Increased reliability: The use of PCBs reduces the risk of loose connections and short circuits, leading to more reliable electronic devices.
- Simplified manufacturing: PCBs streamline the assembly process, making it easier to mass-produce electronic devices.
- Cost-effectiveness: The standardized design and manufacturing processes of PCBs make them cost-effective for large-scale production.
Signs That Indicate the Need for a Circuit Board Test
Now that we understand the importance of circuit boards let’s explore the top signs that suggest it is time for a #CircuitBoardTest.
1. Intermittent Failures or Glitches
One of the most common signs that a circuit board may require testing is the occurrence of intermittent failures or glitches in the electronic device. These issues can manifest in various ways, such as:
- Random reboots or shutdowns
- Flickering displays or inconsistent performance
- Unexpected behavior or malfunctions
Intermittent failures can be challenging to diagnose because they may not occur consistently and can be triggered by specific conditions, such as temperature fluctuations or vibrations. A thorough circuit board test can help identify the root cause of these issues and determine whether the PCB needs repair or replacement.
2. Physical Damage or Corrosion
Another clear sign that a circuit board requires testing is the presence of physical damage or corrosion. Some common examples include:
- Cracks or breaks in the PCB substrate
- Bent or broken component leads
- Burned or charred areas on the board
- Corroded or tarnished contacts or traces
Physical damage can occur due to various reasons, such as accidental drops, impacts, or exposure to extreme temperatures. Corrosion, on the other hand, can result from exposure to moisture, chemicals, or other harsh environmental conditions. In either case, a damaged or corroded circuit board may not function properly and requires testing to assess the extent of the damage and determine the appropriate course of action.
3. Aging or Outdated Components
As electronic devices age, the components on their circuit boards may become outdated or reach the end of their lifespan. This is particularly true for devices that are subjected to frequent use or operate in demanding conditions. Some signs that suggest aging or outdated components include:
- Decreased performance or slower response times
- Increased power consumption or heat generation
- Frequent component failures or replacements
Performing a circuit board test can help identify components that are nearing the end of their life or no longer meet the device’s performance requirements. This information can be used to plan for component replacements or upgrades, ensuring the device continues to operate reliably.
4. Changes in Operating Environment
Electronic devices are designed to operate within specific environmental conditions, such as temperature, humidity, and altitude ranges. When a device is exposed to conditions outside its intended operating range, it can put additional stress on the circuit board and its components. Some signs that suggest a change in the operating environment include:
- Unusual behavior or performance issues in specific locations or conditions
- Increased failure rates or reduced lifespan of components
- Visible signs of oxidation, corrosion, or other environmental damage
If a device has been exposed to a new or challenging operating environment, it is essential to perform a circuit board test to assess the impact on the PCB and its components. This can help identify potential issues before they lead to more severe failures and ensure the device can withstand the new environmental conditions.
5. Planned Maintenance or Upgrades
Even if an electronic device appears to be functioning correctly, it is still essential to perform regular circuit board tests as part of planned maintenance or upgrade cycles. This proactive approach can help identify potential issues before they cause failures and ensure the device continues to operate at peak performance. Some reasons to perform planned circuit board tests include:
- Routine maintenance schedules based on the device’s usage or operating conditions
- Upgrades or modifications to the device’s functionality or performance
- Compliance with industry standards or regulatory requirements
By incorporating circuit board tests into planned maintenance or upgrade cycles, organizations can minimize the risk of unexpected failures, extend the lifespan of their electronic devices, and ensure they continue to meet the evolving needs of their users.
Circuit Board Testing Methods
There are several methods available for testing circuit boards, each with its own advantages and limitations. Some common circuit board testing methods include:
Visual Inspection
Visual inspection is the most basic form of circuit board testing and involves examining the PCB and its components for visible signs of damage, corrosion, or defects. This method can be performed manually or using automated optical inspection (AOI) systems. While visual inspection can identify obvious issues, it may not detect more subtle problems or functional defects.
Automated Optical Inspection (AOI)
AOI systems use high-resolution cameras and advanced image processing algorithms to inspect circuit boards for defects or anomalies. These systems can quickly scan the entire surface of a PCB and compare it to a reference design, identifying issues such as missing components, incorrect placement, or solder defects. AOI is particularly useful for high-volume production environments where manual inspection would be too time-consuming.
In-Circuit Testing (ICT)
ICT involves using specialized test fixtures and probes to test the functionality of individual components on a circuit board. The test fixtures make contact with specific test points on the PCB, allowing the tester to apply signals and measure responses from each component. ICT can identify issues such as short circuits, open circuits, or component failures, but it requires the development of custom test fixtures for each PCB design.
Flying Probe Testing
Flying probe testing is an alternative to ICT that uses movable test probes instead of a fixed test fixture. The probes can be programmed to move across the surface of the PCB and make contact with specific test points, allowing for more flexible and adaptable testing. Flying probe testing is particularly useful for low-volume production or prototype testing, where the development of custom test fixtures would be impractical.
Functional Testing
Functional testing involves testing the complete electronic device or system to ensure it performs as intended. This type of testing typically requires the device to be fully assembled and powered on, and it may involve simulating real-world operating conditions or user interactions. Functional testing can identify issues that may not be apparent during component-level testing, such as software bugs or system-level compatibility problems.
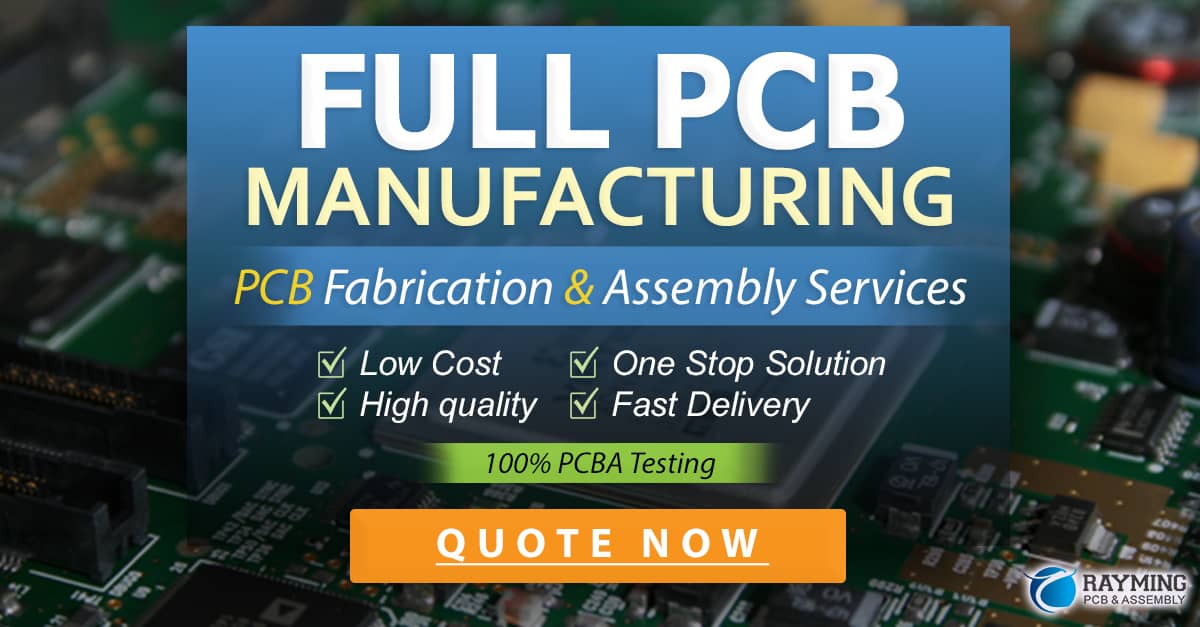
Frequently Asked Questions (FAQ)
1. How often should I perform circuit board tests?
The frequency of circuit board tests depends on several factors, such as the device’s usage, operating environment, and criticality. As a general guideline, consider performing tests:
– During the initial prototype or design validation phase
– Before mass production or deployment
– Periodically during the device’s lifespan, based on its usage and operating conditions
– After any significant changes or upgrades to the device or its components
2. Can I perform circuit board tests in-house, or do I need to outsource them?
The decision to perform circuit board tests in-house or outsource them depends on your organization’s resources, expertise, and testing requirements. In-house testing can provide more control and faster turnaround times but requires an investment in equipment, personnel, and training. Outsourcing to a specialized testing service can be more cost-effective for low-volume or infrequent testing needs and can provide access to a wider range of testing methods and expertise.
3. What are the consequences of not performing regular circuit board tests?
Failing to perform regular circuit board tests can lead to several negative consequences, including:
– Increased risk of unexpected failures or malfunctions
– Reduced device lifespan or reliability
– Increased maintenance or repair costs
– Potential safety hazards or liability issues
– Loss of customer trust or satisfaction
4. How much does circuit board testing cost?
The cost of circuit board testing varies depending on factors such as the complexity of the PCB, the testing methods used, and the volume of boards being tested. Some testing methods, like visual inspection or flying probe testing, may be less expensive than others, like ICT or functional testing. To get an accurate cost estimate, consult with a testing service provider or equipment vendor and provide them with details about your specific testing needs.
5. What should I do if a circuit board test reveals a problem?
If a circuit board test reveals a problem, the next steps will depend on the nature and severity of the issue. Some common actions include:
– Analyzing the test results to identify the root cause of the problem
– Repairing or replacing damaged or defective components
– Modifying the PCB design or manufacturing process to prevent future issues
– Retesting the circuit board to verify that the problem has been resolved
– Documenting the issue and updating relevant procedures or training materials
In some cases, it may be necessary to halt production or recall affected devices to prevent further failures or safety hazards.
Conclusion
Circuit board testing is an essential aspect of ensuring the reliability, performance, and longevity of electronic devices. By recognizing the top signs that indicate the need for a #CircuitBoardTest, organizations can proactively identify and address potential issues before they lead to more severe failures or consequences.
From intermittent glitches and physical damage to aging components and changing operating environments, various factors can compromise the integrity of a circuit board. By employing a range of testing methods, from visual inspection to functional testing, organizations can thoroughly assess the health of their PCBs and make informed decisions about maintenance, repairs, or upgrades.
Ultimately, investing in regular circuit board testing can help organizations minimize downtime, reduce maintenance costs, and ensure their electronic devices continue to meet the needs of their users. By prioritizing circuit board testing as part of their overall maintenance and quality assurance strategies, organizations can enhance the reliability and longevity of their electronic devices and maintain a competitive edge in today’s rapidly evolving technological landscape.
0 Comments