Understanding Component Tombstoning
In the world of electronics manufacturing, “tombstoning” is a phenomenon that can cause significant issues in the production process. Tombstoning, also known as “Manhattan effect” or “Stonehenge effect,” occurs when a surface-mount component (SMC) lifts up from one of its pads during the Reflow Soldering process, resulting in a vertical standing position that resembles a tombstone.
What Causes Tombstoning?
Several factors can contribute to the occurrence of tombstoning in electronic components:
-
Uneven heating: If one side of the component heats up faster than the other, the solder on the hotter side will melt first, causing the component to lift up and stand vertically.
-
Pad design: Inadequate pad design, such as pads that are too small or too far apart, can increase the likelihood of tombstoning.
-
Component size and weight: Smaller and lighter components are more prone to tombstoning due to their lower mass and inertia.
-
Solder Paste inconsistency: Uneven solder paste application or inconsistent paste viscosity can lead to tombstoning.
-
Reflow profile: An improper reflow profile, with too high or too low temperatures, can cause uneven heating and increase the risk of tombstoning.
The Impact of Tombstoning on Electronics Manufacturing
Tombstoning can have a significant impact on the quality and reliability of electronic assemblies:
-
Open circuits: When a component tombstones, it creates an open circuit, preventing the proper flow of electricity and causing the device to malfunction.
-
Reduced mechanical strength: A tombstoned component has a weaker mechanical connection to the board, making it more susceptible to damage from vibration or physical stress.
-
Increased production costs: Tombstoning can lead to higher rework costs, as the affected components must be removed and replaced manually.
-
Lower yield rates: If tombstoning occurs frequently, it can significantly reduce the overall yield rate of the production line, leading to increased costs and delayed shipments.
Preventing Component Tombstoning
To minimize the occurrence of tombstoning in your electronic assemblies, consider the following tips and tricks:
1. Optimize Pad Design
Proper pad design is crucial for preventing tombstoning. Ensure that the pads are appropriately sized and spaced for the specific component being used. Follow these guidelines:
- Use pads that are slightly larger than the component terminations to provide adequate surface area for solder joint formation.
- Maintain a consistent pad size and shape for both ends of the component to promote even heating.
- Ensure that the pad spacing is appropriate for the component size and pitch to prevent bridging or insufficient solder joint formation.
Component Package | Recommended Pad Width | Recommended Pad Length |
---|---|---|
0402 | 0.5 mm – 0.6 mm | 0.5 mm – 0.6 mm |
0603 | 0.7 mm – 0.9 mm | 0.7 mm – 0.9 mm |
0805 | 1.0 mm – 1.2 mm | 1.0 mm – 1.2 mm |
1206 | 1.5 mm – 1.7 mm | 1.5 mm – 1.7 mm |
2. Control Solder Paste Application
Consistent solder paste application is essential for preventing tombstoning. Use a stencil with the appropriate thickness and aperture size to ensure even paste deposition on the pads. Consider these tips:
- Use a stencil thickness that is appropriate for the component pitch and size. A typical stencil thickness ranges from 0.1 mm to 0.15 mm.
- Ensure that the stencil apertures are correctly aligned with the pads on the PCB to prevent paste misalignment.
- Regularly inspect and clean the stencil to maintain consistent paste deposition and prevent clogging.
- Use solder paste with the appropriate viscosity and particle size for the specific application. Consult the paste manufacturer’s recommendations.
3. Optimize Reflow Profile
An optimized reflow profile is crucial for achieving even heating and preventing tombstoning. Follow these guidelines:
- Use a reflow profile that is appropriate for the specific solder paste and component types being used.
- Ensure that the peak temperature is high enough to achieve complete solder melting but not so high that it causes damage to the components or PCB.
- Maintain a consistent ramp rate and time above liquidus (TAL) to promote even heating and solder joint formation.
- Incorporate a proper cooling rate to allow the solder joints to solidify without causing thermal stress.
Reflow Profile Parameter | Recommended Value |
---|---|
Ramp Rate | 1-3°C/second |
Peak Temperature | 235-245°C |
Time Above Liquidus (TAL) | 60-90 seconds |
Cooling Rate | 1-4°C/second |
4. Consider Component Placement Orientation
The orientation of components on the PCB can also influence the likelihood of tombstoning. When possible, follow these guidelines:
- Place components perpendicular to the direction of the board’s travel through the reflow oven. This orientation helps to promote even heating and reduces the risk of tombstoning.
- Avoid placing components too close to the edge of the board, as this can lead to uneven heating and increased tombstoning risk.
- Consider using symmetrical component placement to balance the thermal mass and promote even heating.
5. Implement Process Controls
Implementing appropriate process controls can help to minimize the occurrence of tombstoning and improve overall production quality. Consider these measures:
- Regularly monitor and calibrate the reflow oven to ensure consistent temperature profiles and minimize thermal variations.
- Implement a robust quality control system to identify and address tombstoning issues promptly.
- Provide training to operators to ensure proper handling and placement of components during the assembly process.
- Use automated optical inspection (AOI) systems to detect tombstoned components and other assembly defects.
Frequently Asked Questions (FAQ)
- What is the difference between tombstoning and drawbridging?
Tombstoning and drawbridging are both defects that can occur during the reflow soldering process. Tombstoning refers to a component lifting up from one of its pads and standing vertically, while drawbridging occurs when a component lifts up from both pads, forming a bridge-like shape. Both defects result in open circuits and can cause device malfunction.
- Can tombstoning occur with through-hole components?
Tombstoning is primarily associated with surface-mount components (SMCs) due to their smaller size and lighter weight. Through-hole components are generally less susceptible to tombstoning because they have longer leads that are inserted into the PCB, providing a stronger mechanical connection. However, through-hole components can still experience other types of soldering defects, such as insufficient hole fill or poor wetting.
- How does the choice of solder paste affect tombstoning?
The choice of solder paste can have a significant impact on the occurrence of tombstoning. Solder pastes with higher viscosity and larger particle sizes tend to be less prone to tombstoning because they provide better support for the component during the reflow process. Additionally, some solder pastes are specifically formulated to reduce tombstoning risk by incorporating additives that promote even melting and wetting.
- Can tombstoning be repaired, or do the affected components need to be replaced?
In most cases, tombstoned components need to be removed and replaced manually. Attempting to reflow the component back into place is generally not recommended, as it can cause damage to the pads or the component itself. Rework technicians should use appropriate tools, such as tweezers or a vacuum pen, to carefully remove the tombstoned component and replace it with a new one.
- Are certain types of components more prone to tombstoning than others?
Yes, certain types of components are more susceptible to tombstoning due to their size, weight, and termination style. Small, lightweight components, such as 0201 and 0402 chip resistors and capacitors, are more prone to tombstoning because they have less mass and inertia to resist the lifting force during reflow. Components with asymmetrical terminations, such as diodes and some LEDs, are also more likely to tombstone due to uneven heating and solder melting.
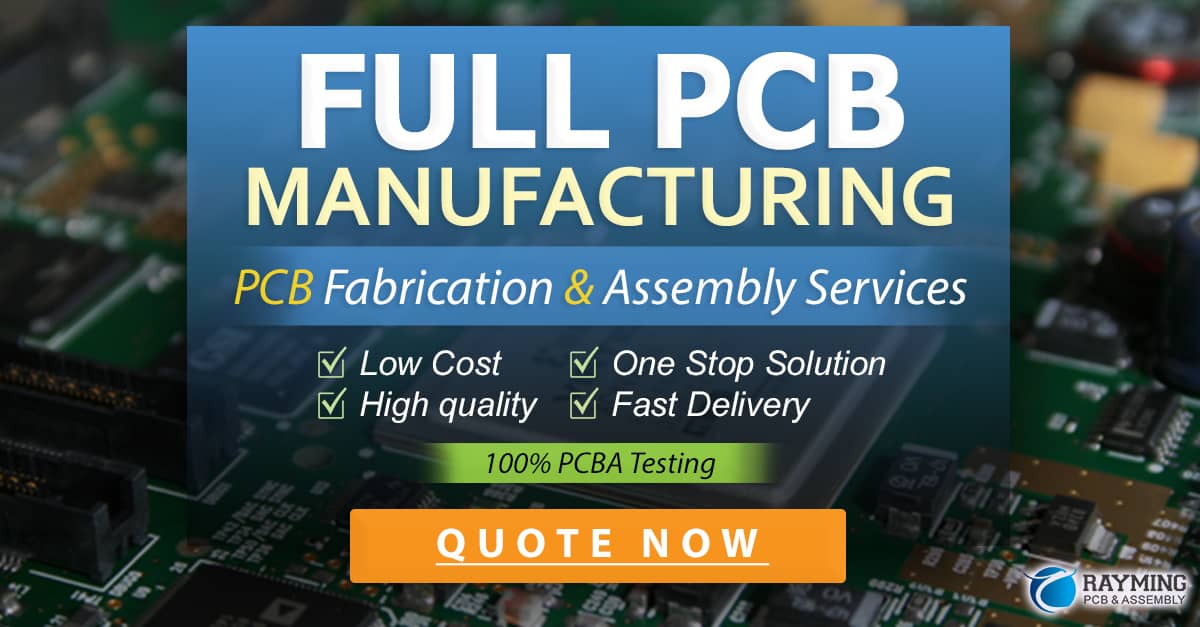
Conclusion
Tombstoning is a common defect in electronics manufacturing that can cause open circuits, reduced mechanical strength, and increased production costs. By understanding the causes of tombstoning and implementing appropriate prevention measures, manufacturers can significantly reduce the occurrence of this issue and improve the overall quality and reliability of their electronic assemblies.
Key strategies for preventing tombstoning include optimizing pad design, controlling solder paste application, implementing appropriate reflow profiles, considering component placement orientation, and implementing process controls. By following these tips and tricks, manufacturers can minimize the risk of tombstoning and ensure the successful production of high-quality electronic devices.
0 Comments