Introduction to PCB Via Treatment
In the world of printed circuit board (PCB) manufacturing, vias play a crucial role in interconnecting different layers of a multilayer PCB. Vias are essentially small holes drilled through the PCB substrate that allow electrical connections between different layers. However, these vias need to be properly treated to ensure reliable electrical connections, prevent contamination, and enhance the overall performance of the PCB.
In this article, we will explore three common methods of treating vias in PCB manufacturing: via tenting, via filling, and via plugging. We will discuss the advantages and disadvantages of each method and provide insights into when to use each technique based on the specific requirements of your PCB design.
What is a Via in PCB?
Before diving into the different via treatment methods, let’s first understand what a via is in the context of PCB manufacturing.
A via, short for “vertical interconnect access,” is a small hole drilled through the layers of a PCB to create an electrical connection between different layers. Vias are typically plated with a conductive material, such as copper, to ensure a reliable electrical connection.
There are several types of vias used in PCB design:
- Through-hole via: A via that goes through all layers of the PCB.
- Blind via: A via that connects an outer layer to an inner layer, but does not go through the entire board.
- Buried via: A via that connects two or more inner layers, but does not reach the outer layers.
Vias are essential for creating complex, multilayer PCB designs where signals need to be routed between different layers. However, untreated vias can lead to various issues, such as:
- Contamination: Exposed vias can accumulate dirt, dust, and moisture, leading to corrosion and reduced reliability.
- Solder wicking: During the soldering process, molten solder can be drawn into the via, causing a solder shortage on the component pad.
- Impedance mismatch: Untreated vias can cause impedance mismatch, leading to signal integrity issues, especially in high-frequency applications.
To mitigate these issues, PCB manufacturers employ various via treatment methods, which we will explore in the following sections.
Via Tenting
What is Via Tenting?
Via tenting is a method of covering the via holes with a layer of solder mask on one or both sides of the PCB. This process seals the via and prevents contamination while providing a flat surface for component placement and soldering.
Advantages of Via Tenting
-
Cost-effective: Via tenting is a relatively inexpensive process compared to other via treatment methods, as it does not require additional materials or processing steps.
-
Improved surface flatness: By covering the vias with solder mask, via tenting creates a flatter surface, making it easier to place and solder components.
-
Enhanced solder joint reliability: Tenting prevents solder from being drawn into the via during the soldering process, ensuring a reliable solder joint on the component pad.
-
Reduced contamination: Sealing the vias with solder mask prevents the accumulation of dirt, dust, and moisture, thereby reducing the risk of corrosion and improving the overall reliability of the PCB.
Disadvantages of Via Tenting
-
Limited thermal conductivity: The solder mask used for via tenting has lower thermal conductivity compared to metal fillers, which can limit the heat dissipation capabilities of the PCB.
-
Not suitable for high-frequency applications: Via tenting does not provide the same level of impedance control as other via treatment methods, making it less suitable for high-frequency applications where signal integrity is critical.
When to Use Via Tenting
Via tenting is an excellent choice for PCB designs with the following characteristics:
- Low to medium-density PCBs
- Cost-sensitive applications
- Designs that do not require high thermal conductivity
- Applications where signal integrity is not a critical concern
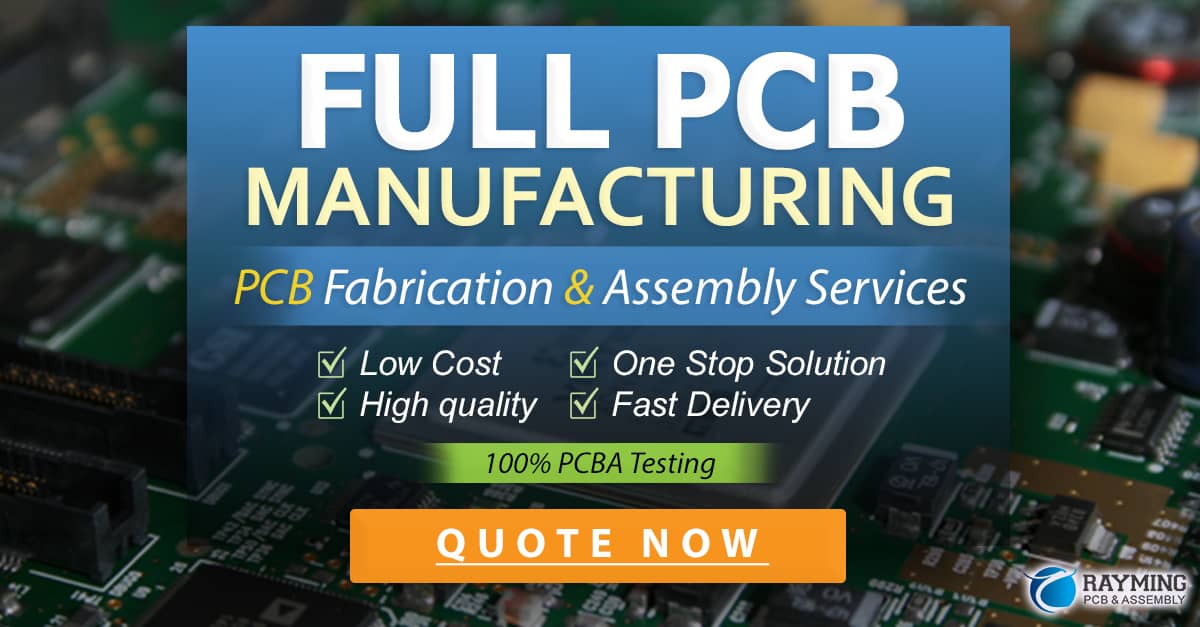
Via Filling
What is Via Filling?
Via filling is a process where the via holes are filled with a conductive material, typically a specially formulated via fill ink or copper. This process creates a solid, planar surface and provides a conductive path through the via.
Advantages of Via Filling
-
Improved thermal conductivity: Filled vias have better thermal conductivity compared to tented vias, allowing for more efficient heat dissipation from the PCB.
-
Enhanced signal integrity: Via filling helps maintain a consistent impedance profile through the via, reducing signal reflections and improving overall signal integrity.
-
Increased mechanical strength: Filled vias provide additional mechanical support to the PCB, reducing the risk of via breakage during handling or thermal cycling.
-
Better surface flatness: Via filling creates a completely flat surface, which is essential for high-density PCB designs with fine-pitch components.
Disadvantages of Via Filling
-
Higher cost: Via filling is a more expensive process compared to via tenting, as it requires additional materials and processing steps.
-
Longer processing time: Filling vias takes more time than tenting, which can increase the overall manufacturing lead time.
-
Potential for voids: If not properly controlled, the via filling process can result in voids within the filled via, which can compromise the electrical and thermal performance of the PCB.
When to Use Via Filling
Via filling is recommended for PCB designs with the following requirements:
- High-density PCBs with fine-pitch components
- Applications that require excellent thermal management
- High-frequency designs that demand strict impedance control
- PCBs subjected to mechanical stress or thermal cycling
Via Plugging
What is Via Plugging?
Via plugging is a process where the via holes are filled with a non-conductive material, such as epoxy or resin. This process seals the via and creates a smooth, planar surface without providing electrical conductivity through the via.
Advantages of Via Plugging
-
Improved surface flatness: Like via filling, via plugging creates a flat surface that is ideal for high-density PCB designs with fine-pitch components.
-
Reduced signal interference: By using a non-conductive material, via plugging prevents signal coupling between adjacent vias, reducing the potential for signal interference.
-
Enhanced mechanical strength: Plugged vias provide additional mechanical support to the PCB, improving its overall robustness.
Disadvantages of Via Plugging
-
No electrical conductivity: Since the plugging material is non-conductive, plugged vias do not provide electrical connectivity between layers, limiting their use in certain PCB designs.
-
Higher cost: Via plugging is generally more expensive than via tenting due to the additional materials and processing steps involved.
-
Limited thermal conductivity: Non-conductive plugging materials have lower thermal conductivity compared to metal fillers, which can limit the heat dissipation capabilities of the PCB.
When to Use Via Plugging
Via plugging is suitable for PCB designs with the following characteristics:
- High-density PCBs that require a flat surface for component placement
- Applications where signal interference between vias is a concern
- PCBs that demand high mechanical strength but do not require electrical conductivity through the vias
Comparison Table
Via Treatment Method | Electrical Conductivity | Thermal Conductivity | Surface Flatness | Cost |
---|---|---|---|---|
Via Tenting | Yes | Low | Moderate | Low |
Via Filling | Yes | High | High | High |
Via Plugging | No | Low | High | Moderate to High |
FAQ
-
Q: What is the most cost-effective via treatment method?
A: Via tenting is generally the most cost-effective via treatment method, as it does not require additional materials or processing steps compared to via filling and via plugging. -
Q: Which via treatment method is best for high-frequency applications?
A: Via filling is the preferred via treatment method for high-frequency applications, as it provides the best impedance control and signal integrity. -
Q: Can via plugging be used for applications that require electrical conductivity through the vias?
A: No, via plugging is not suitable for applications that require electrical conductivity through the vias, as the plugging material is non-conductive. In such cases, via filling should be used instead. -
Q: How does via filling improve thermal management in a PCB?
A: Via filling improves thermal management by providing a conductive path through the via, which allows for better heat dissipation from the PCB. The filled vias act as thermal vias, transferring heat from hot components to other layers or heatsinks. -
Q: Is it possible to use different via treatment methods in the same PCB?
A: Yes, it is possible to use different via treatment methods in the same PCB, depending on the specific requirements of different areas of the board. For example, you could use via filling for high-frequency sections and via tenting for lower-frequency sections to optimize cost and performance.
Conclusion
In PCB manufacturing, via treatment is a critical process that ensures reliable electrical connections, prevents contamination, and enhances the overall performance of the PCB. The three main via treatment methods – via tenting, via filling, and via plugging – each have their own advantages and disadvantages, making them suitable for different applications.
When selecting a via treatment method for your PCB design, consider factors such as cost, thermal management, signal integrity, and mechanical strength. By understanding the characteristics and limitations of each method, you can make an informed decision that balances your design requirements and budget constraints.
Ultimately, the right via treatment method will depend on the specific needs of your PCB application. By working closely with your PCB manufacturer and providing clear design specifications, you can ensure that your PCBs are manufactured to the highest standards, with properly treated vias that deliver reliable performance and long-term durability.
0 Comments