Determining correct trace widths on printed circuit boards ensuring stable operation without exceeding safe current density or heating levels requires careful ampacity and thermal analysis. While engineers historically performed these cumbersome calculations by hand, online utilities now automate analysis for convenient web-based trace width requirements planning aligned with IPC guidelines.
This guide covers key concepts for PCB trace current capacity and temperature rise analysis followed by use of web-based calculators implementing industry standard methods from IPC-2221.
Trace Current Rating Background
Before employing automated calculators, understanding trace analysis fundamentals merits discussion.
Defining Trace Ampacity Limits
Ampacity denotes current carrying capacity before exceeding temperature limits degrading materials or performance. Excess current density in PCB traces causes overheating damage over time.
Factors Influencing Safe Trace Currents
Key considerations influence allowable sustained trace currents:
- Trace material (copper vs aluminum)
- Trace thickness – Ounces of metal determines cross section
- Ambient air temperature – Impacts heating dissipation rate
- ** Electrical insulation** – Laminate thermal conductivity
Varying combinations of these parameters determine maximum permissible currents.
Failure Modes from Overheating Damage
Significantly exceeding ampacity limits causes:
- Intermittent function from dried solders and failing components
- Eventual trace delamination destroying conductive paths
- Combustion destroying electronics (very extreme)
Engineers avoid such failures through analysis guiding layout. Next we cover governing industry standards helping determine suitable PCB trace currents.
Overview of IPC-2221 Trace Current Guidelines
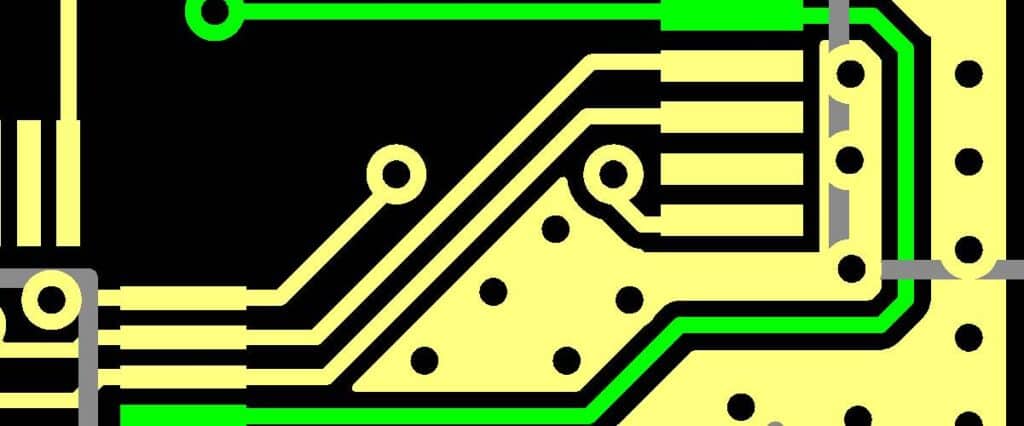
Among IPC specifications focused on ensuring robust electronics manufacture, IPC-2221 “Generic Standard on Printed Board Design” establishes reference trace ampacity and temperature rise limits for common PCB conductor and substrate parameters to guide layout.
IPC-2221 draw critical data from the underlying IPC-2152 “Standard for Determining Current Carrying Capacity in Printed Board Design” defining:
- Test methods assessing sample boards
- Pass criteria avoiding material degradation from heat
- Measurement instrumentation standards
- Reporting procedures
This empirically validated foundation provides basis then for IPC-2221 safe operating trace current design limits across common scenarios.
We will examine key outputs from this industry standard now.
IPC-2221: Trace Current Design Limit Tables
IPC-2221 Section 6.2 prescribes maximum allowable ampacities for signal traces based on:
- Conductor thickness
- Copper weight
- Ambient operating temperature
with numerous material combinations across external and internal layers.
External Layer Table (IPC-2221)
Internal Layer Table (IPC-2221)
Accounting for less heat dissipation internally, inner layer limits drop further:
These values guide trace widths selection for intended currents during layout. However manually interpreting tables proves unwieldy. Online calculators automate analysis instead.
Web-Based IPC-2221 Trace Width Calculator Overview
Rather than separately determining minimum widths needed for target currents based on IPC-2221 lookups, dedicated free web tools perform necessary thermal analysis automatically.
OSH Park’s handy IPC-2221 Trace Width Calculator covers standard external layer scenarios simplifying current capacity planning.
Input Parameters
The calculator prompts critical data points:
- Trace copper thickness / weight
- Ambient operating temperature
- Target current level
with assumptions for common FR-4 dielectric thermal conductivity and resistivity.
Automatic Output
Given inputs, the calculator then derives minimum trace width required keeping temperature rise within IPC-2221 limits, preventing heat damage at intended operating currents.
Helpful fail warning alerts also flag risky configurations:
The handy web utility delivers rapid pass/fail feedback without manually consulting limitation tables.
However, we must also consider temperature rise models for comprehensive thermal analysis…
Calculating Trace Temperature Rise
While the IPC-2221 trace width calculator validates trace cross sections meet target currents, estimating temperature increases quantitatively helps assess thermal margins more precisely.
Dedicated calculators facilitate temperature rise analysis for PCB conductors:
Temperature Estimation Factors
Key variables include:
- Ambient board temperature
- Trace metal material
- Trace weight and width dimensions
- Trace length in inches
- Actual current relative to max current percentage
Together these parameters estimate heating.
Temperature Rise Calculator Tool Overview
PCB Toolkit provides a handy web calculator utility accepting necessary dimensions, current levels and board temp inputs to compute estimated trace heating.
The calculator implements IPC-2221 thermal models to predict real-time temperatures on signal traces and planes during load helping engineers quantify heating headroom and margins.
Let’s apply these tools exploring example scenarios…
Practical Trace Thermal Analysis Examples
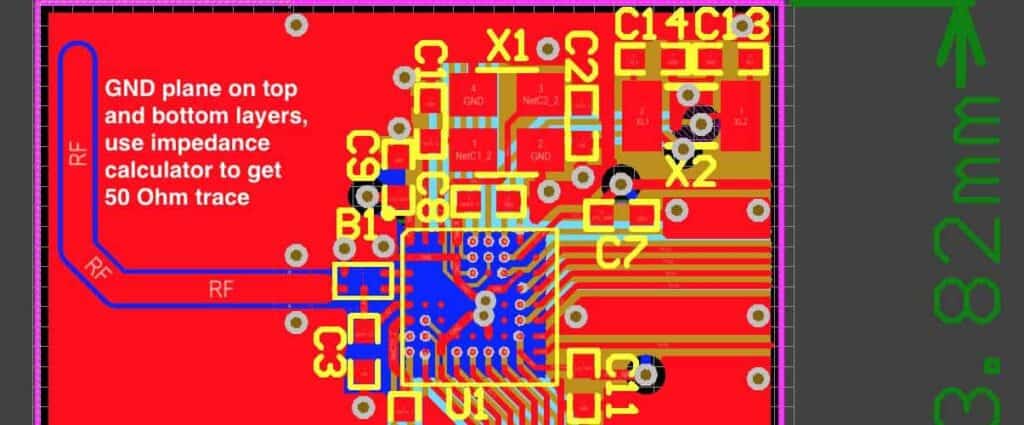
Consider layout requires routing a substantial 8 Amp rail across a 12 inch elongated board section in 1 ounce copper. Standard FR-4 laminate will mount in 70°C ambient temperature environments with mainly convection cooling.
We will check suitability using online calculators:
Step 1 – Determine Minimum Trace Width
First visit OSH Park’s IPC-2221 Trace Width Calculator.
Enter parameters:
- External layer
- 1 oz copper
- 70°C ambient temp
- 8 A target current
The calculator outputs 9.8 mm minimum trace width to support 8A loads given conditions:
This passes initial margin check.
Step 2 – Estimate Temperature Rise
Next, run though PCB Toolkit’s Trace Current/Temperature Calculator to model estimated heating with safer 9.8 mm trace width over 12 inches:
- Enter trace dimensions = 9.8 mm wide
- Set length = 12 inches
- Specify 8A current (relative to IPC-2221 rating = 67%)
- Enter 70°C ambient
- Select default FR-4 thermal conductivity
The calculator forecasts approx 24°C temperature rise for this use case:
The added heating remains within acceptable margins for FR-4 designs avoiding detrimental effects on nearby components.
Quantified heating budgets empower smarter PCB thermal design tradeoffs.
Conclusion
Web-based IPC-2221 trace width and temperature rise calculators automate determining suitable PCB conductor dimensions to safely carry target currents without electrical or thermal failure points. Eliminating manual table lookups and error prone math, the online utilities provide fast pass/fail guidance and reasonably accurate heating estimates per industry trusted standards. Built on rigorous testing, IPC guidelines extend from material science into practical signal layout applications through convenient interactive calculators benefitting working designers daily.
Frequently Asked Questions
Q: Can PCB traces carry more current if briefly pulsed vs continuous loads?
A: Yes, brief transient spikes incur less cumulative heating and may sustain 2-3x higher peak currents without burning conductors. But average power over time still governs to prevent damaging trace materials.
Q: When should I derate target trace currents below IPC-2221 limits?
A: Adding 20-30% safety margin onto IPC-2221 provides headroom accommodating manufacturing variability in trace widths and plating distributions affecting cross sections. More aggressive designs may push closer to tables.
Q: What accuracy can I expect from the temperature calculator results?
A: Heating estimates rely on base lamination thermal conductivity assumptions. Calculator values provide reasonable approximations but neglect impacts of adjacent copper pouring and traces which may increase heating further through parallel thermal resistance.
Q: Can the IPC guidelines apply for external cabling wiring capacity?
A: No, IPC-2221 strictly covers PCB conductor ampacity and heating. External wiring falls under electrical wiring codes like NEC NFPA-70 marking different insulation types and temperature grades. Consult wire/harness specs separately.
Q: Where can I find IPC’s standard test procedures validating the trace ratings?
A: IPC-2152 “Standard for Determining Current Carrying Capacity in Printed Board Design” prescribes detailed test and measurement methodology used validating IPC-2221 allowable current limits under controlled conditions. Contact IPC to obtain documentation.
0 Comments