What is a Castellated-Hole-PCB?
A Castellated-Hole-PCB, also known as a castellated printed circuit board, is a type of PCB that features small, half-moon shaped holes along the edges of the board. These castellations allow for easy and secure connections between multiple PCBs or modules, creating a more compact and efficient design. Castellated-Hole-PCBs are commonly used in applications such as wearable devices, IoT modules, and small form factor electronics.
Advantages of Castellated-Hole-PCBs
- Space-saving design
- Easy and secure connections between boards
- Reduced assembly time and costs
- Improved mechanical strength
- Enhanced thermal management
The Castellated-Hole-PCB Production Process
Step 1: PCB Design
The first step in producing a Castellated-Hole-PCB is to design the board using PCB design software, such as Altium Designer, Eagle, or KiCad. When designing the board, consider the following factors:
- Board size and shape
- Component placement
- Trace routing
- Castellated hole size and spacing
Castellated Hole Design Guidelines
Parameter | Recommended Value |
---|---|
Hole Diameter | 0.8 mm – 1.2 mm |
Hole Spacing | 1.27 mm – 2.54 mm |
Copper Plating Thickness | 25 μm – 35 μm |
Solder Mask Opening | 50 μm – 100 μm larger than hole diameter |
Step 2: PCB Fabrication
Once the PCB design is complete, the next step is to fabricate the board. The fabrication process involves the following sub-steps:
- Copper etching
- Drill castellated holes
- Apply solder mask
- Apply silkscreen
- Surface finish (e.g., ENIG, HASL, OSP)
Copper Etching
Copper etching is the process of removing unwanted copper from the PCB substrate, leaving only the designed traces and pads. This is typically done using a photolithographic process and chemical etching.
Drilling Castellated Holes
After copper etching, the castellated holes are drilled along the edges of the board. The holes are typically drilled using a specialized drill bit that creates the half-moon shape.
Applying Solder Mask and Silkscreen
Solder mask is applied to the PCB to protect the copper traces from oxidation and short circuits. Silkscreen is then applied to add component labels and other markings to the board.
Surface Finish
Finally, a surface finish is applied to the exposed copper areas to protect them from oxidation and improve solderability. Common surface finishes include:
- ENIG (Electroless Nickel Immersion Gold)
- HASL (Hot Air Solder Leveling)
- OSP (Organic Solderability Preservative)
Step 3: PCB Assembly
After the PCB is fabricated, the next step is to assemble the components onto the board. This can be done using various methods, such as:
- Manual soldering
- Reflow soldering
- Wave soldering
Manual Soldering
Manual soldering involves hand-placing and soldering each component onto the PCB. This method is suitable for low-volume production or prototyping.
Reflow Soldering
Reflow soldering is an automated process that involves applying solder paste to the PCB pads, placing components using a pick-and-place machine, and then passing the board through a reflow oven to melt the solder and form a permanent connection.
Wave Soldering
Wave soldering is another automated process that involves passing the PCB over a molten solder wave to form connections on the bottom side of the board. This method is typically used for through-hole components.
Step 4: Testing and Inspection
Once the PCB is assembled, it must be thoroughly tested and inspected to ensure proper functionality and quality. This can involve various methods, such as:
- Visual inspection
- Automated optical inspection (AOI)
- In-circuit testing (ICT)
- Functional testing
Visual Inspection
Visual inspection involves manually inspecting the PCB for any visible defects, such as solder bridges, missing components, or damaged traces.
Automated Optical Inspection (AOI)
AOI uses high-resolution cameras and image processing software to automatically detect and classify defects on the PCB.
In-Circuit Testing (ICT)
ICT involves using a bed-of-nails fixture to make electrical contact with the PCB and test for shorts, opens, and component values.
Functional Testing
Functional testing involves testing the PCB in its intended application to ensure proper operation and performance.
Frequently Asked Questions (FAQ)
-
Q: What are the advantages of using Castellated-Hole-PCBs?
A: Castellated-Hole-PCBs offer several advantages, including space-saving design, easy and secure connections between boards, reduced assembly time and costs, improved mechanical strength, and enhanced thermal management. -
Q: What is the recommended hole diameter for castellated holes?
A: The recommended hole diameter for castellated holes is between 0.8 mm and 1.2 mm. -
Q: What surface finishes are commonly used for Castellated-Hole-PCBs?
A: Common surface finishes for Castellated-Hole-PCBs include ENIG (Electroless Nickel Immersion Gold), HASL (Hot Air Solder Leveling), and OSP (Organic Solderability Preservative). -
Q: What testing methods are used to ensure the quality of Castellated-Hole-PCBs?
A: Testing methods for Castellated-Hole-PCBs include visual inspection, automated optical inspection (AOI), in-circuit testing (ICT), and functional testing. -
Q: What are the main steps involved in producing a Castellated-Hole-PCB?
A: The main steps in producing a Castellated-Hole-PCB are PCB design, PCB fabrication, PCB assembly, and testing and inspection.
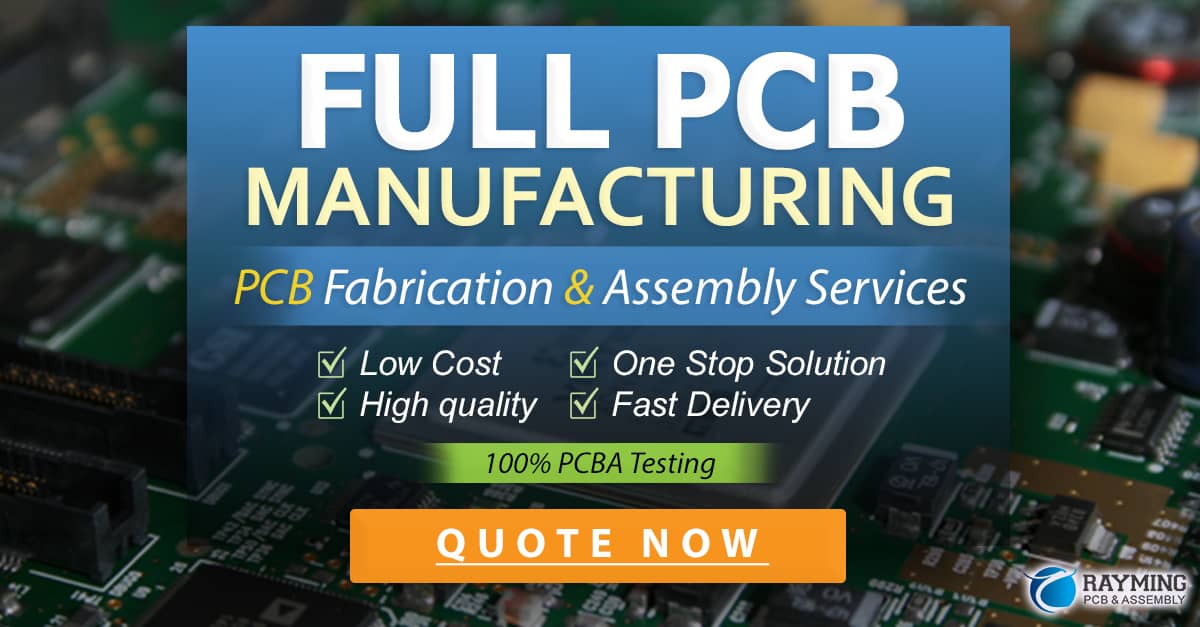
Conclusion
Castellated-Hole-PCBs offer a compact and efficient solution for connecting multiple PCBs or modules in space-constrained applications. By following the proper design guidelines, fabrication processes, assembly methods, and testing procedures, manufacturers can produce high-quality Castellated-Hole-PCBs that meet the needs of their customers. As technology continues to advance and the demand for smaller, more integrated electronics grows, Castellated-Hole-PCBs will likely play an increasingly important role in the electronics industry.
0 Comments