Understanding PCB Quality
Printed Circuit Boards (PCBs) are the backbone of modern electronics, and China has become a major player in the global PCB manufacturing industry. However, not all PCBs from China are created equal. It is crucial to distinguish between good and bad quality PCBs to ensure the reliability and longevity of your electronic devices. In this article, we will explore the key factors that determine PCB quality and provide guidance on how to identify high-quality PCBs from China.
What is a PCB?
A PCB is a flat board made of insulating material, such as fiberglass or composite epoxy, with conductive pathways etched onto its surface. These pathways, known as traces, connect various electronic components, such as resistors, capacitors, and integrated circuits, to form a complete electronic circuit. PCBs are used in a wide range of applications, from consumer electronics to industrial equipment and aerospace systems.
Why PCB Quality Matters
The quality of a PCB directly impacts the performance, reliability, and durability of the electronic device it powers. A low-quality PCB can lead to various issues, such as:
- Malfunction or failure of the electronic device
- Shorter product lifespan
- Increased maintenance and repair costs
- Potential safety hazards, such as electrical shorts or fires
On the other hand, a high-quality PCB ensures:
- Optimal performance of the electronic device
- Longer product lifespan
- Reduced maintenance and repair costs
- Enhanced safety and reliability
Factors Affecting PCB Quality
Several factors contribute to the overall quality of a PCB. Understanding these factors is essential when evaluating PCBs from Chinese manufacturers.
1. Material Selection
The choice of materials used in PCB fabrication plays a significant role in determining the board’s quality. High-quality PCBs use superior materials that offer excellent electrical insulation, thermal stability, and mechanical strength. Some key materials to consider include:
- Substrate material: FR-4 is the most common substrate material used in PCBs due to its good electrical insulation properties and cost-effectiveness. Higher-grade materials, such as polyimide or Teflon, are used for more demanding applications.
- Copper foil: The thickness and purity of the copper foil used for the conductive traces impact the PCB’s electrical performance and current-carrying capacity.
- Solder mask: A high-quality solder mask protects the PCB from oxidation, provides electrical insulation, and improves the board’s aesthetic appearance.
2. Manufacturing Process
The manufacturing process employed by the PCB fabricator directly affects the quality of the final product. A well-controlled and optimized manufacturing process ensures consistent quality across multiple production runs. Key aspects of the manufacturing process include:
- Etching: The accuracy and precision of the etching process determine the quality of the conductive traces, ensuring proper electrical connections and minimizing signal loss.
- Drilling: High-quality PCBs feature clean and precise drilled holes, free from burrs or debris, to ensure reliable electrical connections between layers.
- Lamination: Proper lamination ensures strong bonding between the layers of the PCB, preventing delamination and improving the board’s mechanical strength.
- Surface finish: The choice of surface finish, such as HASL, ENIG, or OSP, affects the PCB’s solderability, durability, and shelf life.
3. Quality Control
Stringent quality control measures are essential to ensure that only high-quality PCBs leave the manufacturing facility. A reputable PCB manufacturer will have a comprehensive quality control system in place, which includes:
- Incoming material inspection: Verifying the quality and consistency of raw materials before they enter the production process.
- In-process inspection: Monitoring and controlling critical process parameters during PCB fabrication to identify and correct any deviations.
- Final inspection: Conducting thorough visual, electrical, and functional testing of finished PCBs to ensure they meet the specified requirements.
- Traceability: Maintaining detailed records of materials, processes, and test results for each PCB to enable traceability and facilitate root cause analysis in case of issues.
4. Certifications and Standards
Reputable PCB manufacturers in China adhere to international standards and hold relevant certifications to demonstrate their commitment to quality. Some key certifications and standards to look for include:
- ISO 9001: Quality Management System
- ISO 14001: Environmental Management System
- UL (Underwriters Laboratories) certification
- IPC (Association Connecting Electronics Industries) standards, such as IPC-A-600 for acceptability of printed boards and IPC-6012 for qualification and performance specification for rigid printed boards
How to Identify High-Quality PCBs from China
Now that we understand the factors that contribute to PCB quality, let’s explore some practical ways to identify high-quality PCBs from Chinese manufacturers.
1. Research and Due Diligence
Before engaging with a Chinese PCB manufacturer, conduct thorough research and due diligence to assess their reputation, capabilities, and track record. Some steps to take include:
- Reviewing the manufacturer’s website and marketing materials to understand their focus, expertise, and target markets.
- Searching for online reviews, testimonials, and case studies from previous clients to gauge their satisfaction level and the manufacturer’s ability to deliver quality products.
- Checking the manufacturer’s certifications and compliance with relevant industry standards.
- Requesting references from the manufacturer and contacting them to gather first-hand feedback on their experience working with the manufacturer.
2. Communication and Collaboration
Effective communication and collaboration with your Chinese PCB manufacturer are crucial to ensure that your requirements are clearly understood and met. Consider the following:
- Provide detailed and accurate specifications, drawings, and files to minimize the risk of misinterpretation or errors.
- Engage in regular communication with the manufacturer throughout the production process to stay informed of progress, address any concerns, and make necessary adjustments.
- Establish a clear quality assurance plan with the manufacturer, outlining the inspection and testing requirements at various stages of production.
- Consider visiting the manufacturing facility in person or sending a representative to assess the facility, processes, and quality control measures firsthand.
3. Prototype and Testing
Before committing to a large-scale production run, it is advisable to order a prototype or small batch of PCBs from the manufacturer for evaluation and testing. This allows you to:
- Verify that the manufactured PCBs meet your specifications and quality expectations.
- Conduct functional and reliability testing to ensure the PCBs perform as intended under various operating conditions.
- Identify any potential issues or areas for improvement and work with the manufacturer to address them before proceeding with mass production.
4. Continuous Monitoring and Improvement
Maintaining high PCB quality is an ongoing process that requires continuous monitoring and improvement. Once you have established a working relationship with a Chinese PCB manufacturer, consider the following:
- Implement a supplier performance monitoring system to track key metrics, such as on-time delivery, product quality, and responsiveness to issues.
- Conduct regular audits of the manufacturing facility to ensure that quality control processes are being followed consistently.
- Foster a culture of continuous improvement by encouraging open communication, sharing feedback, and collaborating with the manufacturer to identify and implement process enhancements.
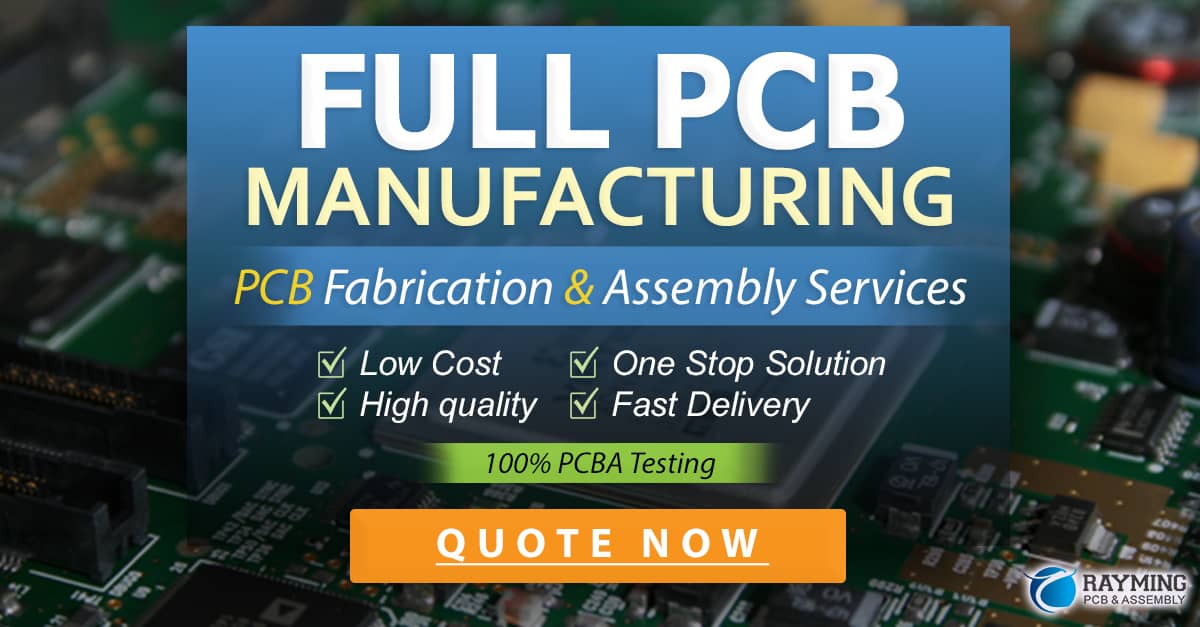
Conclusion
Distinguishing good and bad PCBs from China requires a thorough understanding of the factors that contribute to PCB quality, as well as a proactive approach to supplier selection and management. By focusing on material selection, manufacturing processes, quality control, certifications, and standards, you can identify high-quality PCB manufacturers in China. Conducting due diligence, effective communication, prototype testing, and continuous monitoring will further ensure that you receive PCBs that meet your quality expectations and contribute to the success of your electronic products.
Frequently Asked Questions (FAQ)
1. What are the most common PCB substrate materials used in China?
The most common PCB substrate material used in China is FR-4, which offers a good balance of electrical insulation, mechanical strength, and cost-effectiveness. Other materials, such as aluminum-backed, high-frequency, and flexible substrates, are also available for specific applications.
2. How can I verify a Chinese PCB manufacturer’s certifications and compliance with industry standards?
You can verify a Chinese PCB manufacturer’s certifications and compliance by requesting copies of their certificates and audit reports. Additionally, you can check with the relevant certification bodies or industry associations to confirm the validity of the manufacturer’s claims.
3. What should I include in my PCB specifications to ensure clear communication with the Chinese manufacturer?
Your PCB specifications should include detailed information on the board’s dimensions, layer count, material requirements, copper weight, surface finish, hole sizes, tolerances, and any special requirements or features. Providing clear and accurate CAD files, Gerber files, and bill of materials (BOM) will further ensure that the manufacturer understands your requirements.
4. How can I test the quality of PCBs received from a Chinese manufacturer?
You can test the quality of PCBs received from a Chinese manufacturer by conducting visual inspections, electrical tests (such as continuity and insulation resistance), and functional tests. Depending on your product’s specific requirements, you may also need to perform environmental tests, such as thermal cycling, humidity exposure, or vibration testing.
5. What should I do if I receive low-quality PCBs from a Chinese manufacturer?
If you receive low-quality PCBs from a Chinese manufacturer, document the issues thoroughly, including photographs and test results. Communicate the problems to the manufacturer and request an investigation into the root cause. Work with the manufacturer to develop a corrective action plan and establish a timeline for implementing the necessary improvements. If the manufacturer is unwilling or unable to address the quality issues satisfactorily, consider exploring alternative suppliers.
Factor | Good Quality PCB | Bad Quality PCB |
---|---|---|
Material Selection | Uses high-quality, industry-standard materials (e.g., FR-4, high-purity copper) | Uses low-quality, substandard materials |
Manufacturing Process | Employs precise and well-controlled processes (etching, drilling, lamination) | Inconsistent or poor process control, resulting in defects |
Quality Control | Implements thorough incoming, in-process, and final inspection; maintains traceability | Lacks adequate quality control measures or documentation |
Certifications and Standards | Holds relevant certifications (ISO 9001, UL) and complies with industry standards (IPC) | Lacks certifications or fails to meet industry standards |
By understanding these key factors and following the guidelines outlined in this article, you can effectively distinguish between good and bad PCBs from China, ensuring the quality and reliability of your electronic products.
0 Comments