Introduction to PCB Circuit Boards
Printed Circuit Boards (PCBs) are the backbone of modern electronic devices. They are used in a wide range of applications, from simple consumer electronics to complex industrial equipment. PCBs are essential components that provide mechanical support and electrical connectivity for electronic components. In this ultimate guide, we will explore everything you need to know about PCB circuit boards.
What is a PCB?
A PCB, or Printed Circuit Board, is a thin board made of fiberglass or other composite material that is used to mechanically support and electrically connect electronic components using conductive pathways, tracks, or signal traces etched from copper sheets laminated onto a non-conductive substrate.
Types of PCBs
There are several types of PCBs, each with their own unique characteristics and applications:
-
Single-sided PCBs: These PCBs have conductive tracks on only one side of the board. They are the simplest and most cost-effective type of PCB.
-
Double-sided PCBs: These PCBs have conductive tracks on both sides of the board. They offer more flexibility in terms of component placement and routing.
-
Multi-layer PCBs: These PCBs have multiple layers of conductive tracks sandwiched between layers of insulating material. They are used in complex electronic devices that require high density and high-speed connectivity.
-
Flexible PCBs: These PCBs are made of flexible materials that allow them to bend and twist. They are used in applications where space is limited or where the PCB needs to conform to a specific shape.
-
Rigid-Flex PCBs: These PCBs combine the benefits of rigid and flexible PCBs. They have rigid sections for mounting components and flexible sections for connecting different parts of the device.
PCB Materials
PCBs are made of a variety of materials, each with their own properties and characteristics. The most common PCB materials include:
-
FR-4: This is the most widely used PCB material. It is made of fiberglass reinforced with epoxy resin. FR-4 has good mechanical and electrical properties and is suitable for most applications.
-
Polyimide: This is a high-performance PCB material that is used in applications that require high temperature resistance and flexibility. Polyimide PCBs are often used in aerospace and military applications.
-
PTFE: This is a low-loss PCB material that is used in high-frequency applications such as radar and wireless communication. PTFE PCBs have excellent dielectric properties and low moisture absorption.
-
Aluminum: This is a metal-backed PCB material that is used in applications that require good thermal conductivity and heat dissipation. Aluminum PCBs are often used in power electronics and LED lighting.
PCB Design and Manufacturing Process
The PCB design and manufacturing process involves several steps, each of which is critical to the quality and reliability of the final product.
PCB Design
The first step in the PCB design process is to create a schematic diagram of the circuit. This diagram shows the electrical connections between the components and helps to ensure that the circuit will function as intended.
Once the schematic is complete, the next step is to create a layout of the PCB. This involves placing the components on the board and routing the conductive tracks between them. The layout must take into account factors such as signal integrity, electromagnetic compatibility, and thermal management.
PCB Manufacturing
The PCB manufacturing process involves several steps, including:
-
Etching: The conductive tracks are etched onto the PCB substrate using a photolithographic process.
-
Drilling: Holes are drilled into the PCB to allow components to be mounted and to provide electrical connectivity between layers.
-
Plating: The holes are plated with a conductive material to provide electrical connectivity between layers.
-
Solder Mask: A protective layer is applied to the PCB to prevent short circuits and to protect the conductive tracks from damage.
-
Silkscreen: Text and symbols are printed onto the PCB to identify components and to provide assembly instructions.
-
Testing: The PCB is tested to ensure that it meets the required specifications and functions as intended.
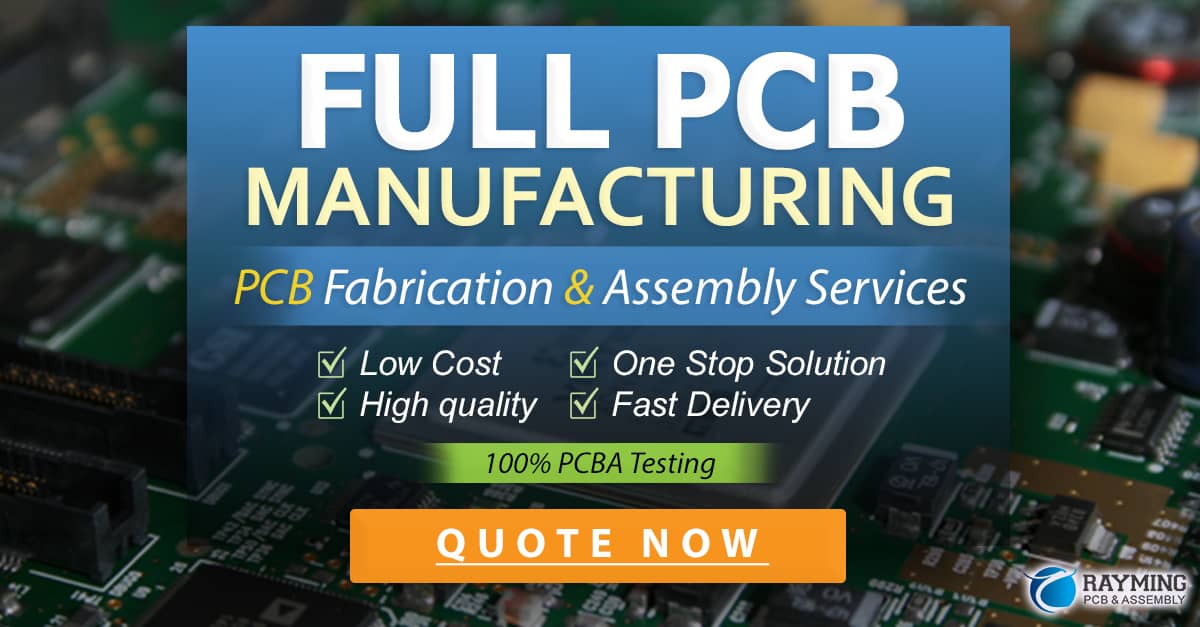
PCB Assembly
Once the PCB has been manufactured, the next step is to assemble the components onto the board. There are two main methods of PCB assembly: through-hole and surface mount.
Through-Hole Assembly
Through-hole assembly involves inserting the leads of the components through holes in the PCB and soldering them in place. This method is simple and reliable but is limited in terms of component density and requires more manual labor.
Surface Mount Assembly
Surface mount assembly involves placing the components directly onto the surface of the PCB and soldering them in place. This method allows for higher component density and can be automated using pick-and-place machines. However, it requires more precise placement and can be more difficult to repair.
PCB Testing and Inspection
After the PCB has been assembled, it must be tested and inspected to ensure that it meets the required specifications and functions as intended. There are several methods of PCB testing and inspection, including:
Visual Inspection
Visual inspection involves examining the PCB for defects such as solder bridges, missing components, and incorrect component placement. This can be done manually or using automated optical inspection (AOI) equipment.
Electrical Testing
Electrical testing involves measuring the electrical characteristics of the PCB, such as resistance, capacitance, and inductance. This can be done using a variety of test equipment, such as multimeters, oscilloscopes, and LCR meters.
Functional Testing
Functional testing involves testing the PCB under actual operating conditions to ensure that it functions as intended. This can be done using specialized test equipment or by integrating the PCB into the final product and testing it as part of the overall system.
PCB Standards and Regulations
PCBs are subject to a variety of standards and regulations to ensure their quality, reliability, and safety. Some of the most important PCB standards and regulations include:
IPC Standards
The IPC (Association Connecting Electronics Industries) is a global trade association that develops standards for the electronics industry. IPC standards cover a wide range of topics related to PCBs, including design, manufacturing, assembly, and testing.
UL Standards
Underwriters Laboratories (UL) is a global safety certification company that develops standards for the safety of electrical and electronic products. UL standards cover topics such as flammability, electrical insulation, and mechanical strength.
RoHS Directive
The Restriction of Hazardous Substances (RoHS) Directive is a European Union regulation that restricts the use of certain hazardous substances in electrical and electronic equipment. PCBs must comply with RoHS requirements to be sold in the EU.
PCB Applications
PCBs are used in a wide range of applications across many industries. Some of the most common PCB applications include:
Consumer Electronics
PCBs are used in a wide range of consumer electronics, including smartphones, tablets, laptops, and televisions. PCBs in consumer electronics must be designed for high-volume production and must meet strict cost and reliability requirements.
Automotive Electronics
PCBs are used in a variety of automotive electronics, including engine control units, infotainment systems, and advanced driver assistance systems (ADAS). PCBs in automotive applications must be designed to withstand harsh environmental conditions and must meet strict safety and reliability requirements.
Medical Devices
PCBs are used in a variety of medical devices, including diagnostic equipment, monitoring systems, and implantable devices. PCBs in medical applications must meet strict regulatory requirements and must be designed for high reliability and long-term performance.
Industrial Automation
PCBs are used in a variety of industrial automation applications, including robotics, process control, and machine vision. PCBs in industrial applications must be designed for ruggedness and reliability in harsh environments.
Aerospace and Defense
PCBs are used in a variety of aerospace and defense applications, including avionics, radar, and satellite communications. PCBs in aerospace and defense applications must meet strict performance and reliability requirements and must be designed to withstand extreme environmental conditions.
Future Trends in PCB Technology
PCB technology is constantly evolving to meet the demands of new applications and technologies. Some of the key trends in PCB technology include:
Miniaturization
As electronic devices become smaller and more compact, PCBs must also become smaller and more densely populated. This requires advanced manufacturing techniques and materials to achieve the required level of miniaturization.
High-Speed Design
As data rates continue to increase, PCBs must be designed for high-speed signal integrity and low-loss performance. This requires advanced design techniques such as impedance matching, signal routing, and shielding.
3D Printing
3D printing technology is being increasingly used in PCB manufacturing to create complex geometries and to reduce waste. 3D printing can also be used to create embedded components and to integrate electronics into mechanical structures.
Embedded Components
Embedded components are electronic components that are integrated directly into the PCB substrate. This can reduce the size and weight of the PCB and can improve signal integrity and reliability.
Advanced Materials
New materials are being developed for PCBs to improve performance and reliability in challenging environments. These materials include high-temperature ceramics, low-loss dielectrics, and conductive polymers.
Frequently Asked Questions (FAQ)
- What is the difference between a PCB and a circuit board?
A PCB (Printed Circuit Board) is a type of circuit board that has conductive tracks printed or etched onto the surface. A circuit board is a more general term that refers to any board that is used to mechanically support and electrically connect electronic components.
- How long does it take to manufacture a PCB?
The time required to manufacture a PCB depends on several factors, including the complexity of the design, the materials used, and the manufacturing process. Simple PCBs can be manufactured in a few days, while complex PCBs may take several weeks or even months to produce.
- What is the difference between through-hole and surface mount assembly?
Through-hole assembly involves inserting the leads of components through holes in the PCB and soldering them in place. Surface mount assembly involves placing components directly onto the surface of the PCB and soldering them in place. Surface mount assembly allows for higher component density and can be automated using pick-and-place machines.
- What is the purpose of a solder mask on a PCB?
A solder mask is a protective layer that is applied to the surface of a PCB to prevent short circuits and to protect the conductive tracks from damage. The solder mask also provides insulation between adjacent tracks and pads.
- What is the IPC standard for PCBs?
The IPC (Association Connecting Electronics Industries) is a global trade association that develops standards for the electronics industry. IPC standards cover a wide range of topics related to PCBs, including design, manufacturing, assembly, and testing. The most commonly used IPC standard for PCBs is IPC-6012, which specifies the requirements for rigid printed boards.
Conclusion
PCBs are essential components in modern electronic devices, providing mechanical support and electrical connectivity for electronic components. The design and manufacturing of PCBs involves several critical steps, including schematic design, layout, etching, drilling, plating, and testing. PCBs are used in a wide range of applications, from consumer electronics to aerospace and defense, and are subject to various standards and regulations to ensure their quality and reliability. As technology continues to evolve, PCBs will continue to play a critical role in enabling new applications and technologies.
0 Comments