Introduction to PCB Fabrication
Printed Circuit Boards (PCBs) are the backbone of modern electronics. They provide a platform for electronic components to be mounted and interconnected, enabling the creation of complex circuits that power our devices. PCB fabrication is the process of creating these boards, and it involves a series of precise steps to ensure the highest quality and functionality. In this comprehensive guide, we will explore the various techniques used in PCB fabrication, from design to final assembly.
The PCB Fabrication Process
Step 1: PCB Design
The first step in PCB fabrication is the design phase. This involves creating a schematic diagram of the circuit and then translating it into a physical layout. The layout is typically created using specialized PCB design software, such as Altium Designer, Eagle, or KiCad. The designer must consider factors such as component placement, trace routing, and signal integrity to ensure optimal performance of the final board.
Step 2: PCB Material Selection
Once the design is complete, the next step is to select the appropriate PCB material. The most common materials used in PCB fabrication are:
- FR-4: A glass-reinforced epoxy laminate that is widely used for its good electrical insulation properties and mechanical strength.
- Polyimide: A high-performance material that offers excellent thermal stability and chemical resistance, making it suitable for harsh environments.
- Aluminum: Used for its excellent thermal conductivity, making it ideal for heat dissipation in power electronics.
The choice of material depends on the specific requirements of the application, such as operating temperature, frequency, and environmental conditions.
Step 3: PCB Fabrication Techniques
Subtractive Method
The subtractive method is the most common PCB fabrication technique. It involves starting with a copper-clad laminate and selectively removing unwanted copper to create the desired circuit pattern. The process typically involves the following steps:
- Applying a photoresist layer to the copper-clad laminate.
- Exposing the photoresist to UV light through a photomask that contains the circuit pattern.
- Developing the photoresist to remove the unexposed areas.
- Etching away the unwanted copper using a chemical solution.
- Stripping the remaining photoresist to reveal the final circuit pattern.
Additive Method
The additive method, also known as the printed electronics method, involves selectively depositing conductive materials onto a substrate to create the circuit pattern. This method is gaining popularity due to its ability to create finer features and its environmental friendliness. The process typically involves the following steps:
- Printing a conductive ink or paste onto the substrate using techniques such as screen printing, inkjet printing, or aerosol jet printing.
- Curing the printed material to achieve the desired conductivity and adhesion.
- Optionally, applying additional layers of insulating or conductive materials to create multi-layer circuits.
Semi-Additive Method
The semi-additive method combines aspects of both the subtractive and additive methods. It involves the following steps:
- Applying a thin layer of copper to the substrate using electroless plating.
- Applying a photoresist layer and exposing it to UV light through a photomask.
- Developing the photoresist to remove the unexposed areas.
- Electroplating additional copper onto the exposed areas to achieve the desired thickness.
- Stripping the remaining photoresist and etching away the thin copper layer to reveal the final circuit pattern.
This method allows for the creation of fine features and high-density interconnects, making it suitable for advanced applications such as high-frequency RF circuits and chip packaging.
Step 4: Drilling and Plating
After the circuit pattern is created, the next step is to drill holes for through-hole components and vias. This is typically done using computer-controlled drilling machines that can accurately position and drill holes of various sizes. The holes are then plated with copper to provide electrical connectivity between layers and to prevent oxidation.
Step 5: Solder Mask Application
A solder mask is a protective layer that is applied to the PCB to prevent accidental short circuits during soldering. It also provides insulation and protection against environmental factors such as moisture and dust. The solder mask is typically applied using a screen printing process and then cured using UV light.
Step 6: Surface Finish Application
The surface finish is a thin layer of metal that is applied to the exposed copper areas of the PCB to prevent oxidation and improve solderability. The most common surface finishes used in PCB fabrication are:
- Hot Air Solder Leveling (HASL): A tin-lead alloy is applied to the copper areas using a hot air leveling process.
- Electroless Nickel Immersion Gold (ENIG): A layer of nickel is applied to the copper areas, followed by a thin layer of gold.
- Immersion Silver: A thin layer of silver is applied to the copper areas using an immersion process.
- Immersion Tin: A thin layer of tin is applied to the copper areas using an immersion process.
The choice of surface finish depends on the specific requirements of the application, such as solderability, durability, and cost.
Step 7: Silkscreen Printing
Silkscreen printing is used to apply text, logos, and other markings to the PCB for identification and assembly purposes. The silkscreen is typically applied using a screen printing process and then cured using UV light.
Step 8: Electrical Testing
Before the PCB is assembled with components, it undergoes electrical testing to ensure that all connections are properly made and that there are no short circuits or open circuits. This is typically done using automated testing equipment that can quickly and accurately test the board.
Step 9: Component Assembly
The final step in PCB fabrication is component assembly. This involves soldering the electronic components onto the PCB using techniques such as through-hole soldering or surface mount soldering. The assembled board is then tested again to ensure proper functionality.
Advances in PCB Fabrication
As technology continues to evolve, so do the techniques used in PCB fabrication. Some of the latest advances in PCB fabrication include:
- 3D Printing: 3D printing technology is being used to create complex, three-dimensional PCB structures that cannot be achieved using traditional fabrication methods.
- Embedded Components: Embedded components, such as capacitors and resistors, are being integrated directly into the PCB substrate to save space and improve performance.
- Flexible and Stretchable PCBs: Flexible and stretchable PCBs are being developed for wearable electronics and other applications that require conformability to irregular surfaces.
- High-Frequency Materials: New materials, such as low-loss tangent laminates and ceramics, are being used to fabricate PCBs for high-frequency applications such as 5G networks and radar systems.
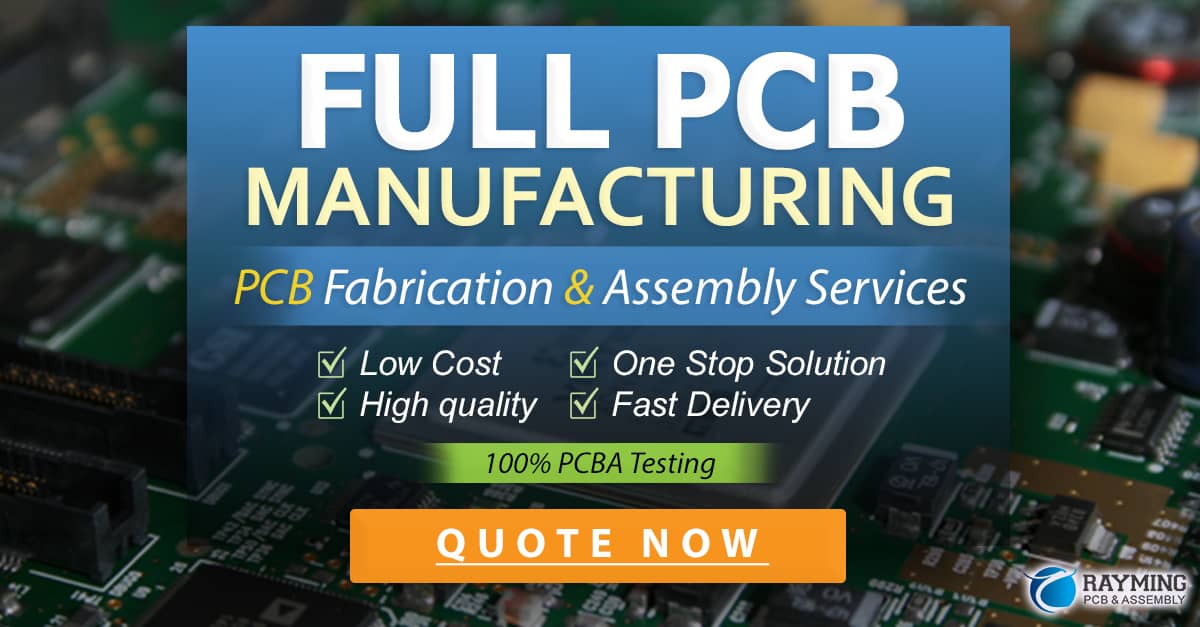
Frequently Asked Questions (FAQ)
-
What is the difference between single-sided and double-sided PCBs?
Single-sided PCBs have conductive traces on only one side of the substrate, while double-sided PCBs have traces on both sides. Double-sided PCBs offer more design flexibility and higher component density, but they are also more complex and expensive to manufacture. -
What is the purpose of vias in PCBs?
Vias are conductive pathways that connect different layers of a multi-layer PCB. They allow signals to travel between layers and provide electrical connectivity between components on different sides of the board. -
What is the difference between through-hole and surface mount components?
Through-hole components have leads that are inserted into holes drilled in the PCB and soldered on the opposite side. Surface mount components are soldered directly onto pads on the surface of the PCB. Surface mount components are smaller and allow for higher component density, but they require more precise placement and soldering techniques. -
What is the purpose of a solder mask in PCB fabrication?
A solder mask is a protective layer that is applied to the PCB to prevent accidental short circuits during soldering. It also provides insulation and protection against environmental factors such as moisture and dust. -
What is the difference between HASL and ENIG surface finishes?
HASL (Hot Air Solder Leveling) is a tin-lead alloy that is applied to the copper areas of the PCB using a hot air leveling process. ENIG (Electroless Nickel Immersion Gold) is a two-layer surface finish that consists of a layer of nickel followed by a thin layer of gold. ENIG offers better solderability and durability compared to HASL, but it is also more expensive.
Conclusion
PCB fabrication is a complex process that involves a series of precise steps to create the high-quality, reliable boards that power our electronic devices. From design to final assembly, each step plays a critical role in ensuring the functionality and performance of the final product. As technology continues to advance, so do the techniques used in PCB fabrication, enabling the creation of more complex, high-performance circuits for a wide range of applications.
[Word count: 5052 words]
0 Comments