What is a PCB Stiffener?
A PCB stiffener, also known as a PCB stiffening plate or PCB backing plate, is a flat sheet of material that is attached to a flexible or rigid-flex printed circuit board (PCB) to provide support and prevent excessive bending or flexing. PCB stiffeners are essential components in the design and manufacturing of rigid-flex and flex circuits, as they help maintain the structural integrity of the PCB and ensure reliable performance in various applications.
Types of PCB Stiffeners
There are two main types of PCB stiffeners:
- Rigid PCB Stiffeners
- Flexible PCB Stiffeners
Rigid PCB Stiffeners
Rigid PCB stiffeners are typically made from materials such as:
- FR-4 (Flame Retardant 4)
- Aluminum
- Stainless Steel
- Copper
These materials offer excellent rigidity and thermal stability, making them suitable for applications that require a high degree of mechanical strength and durability.
Flexible PCB Stiffeners
Flexible PCB stiffeners are made from materials that offer a combination of flexibility and support, such as:
- Polyimide
- Polyester
- Kapton
These materials allow for some degree of flexing while still providing the necessary support to prevent damage to the PCB.
The Importance of PCB Stiffeners in Rigid-Flex and Flex Circuits
PCB stiffeners play a crucial role in the performance and reliability of rigid-flex and flex circuits. Here are some key reasons why PCB stiffeners are essential:
1. Mechanical Support
Flexible and rigid-flex PCBs are prone to bending and flexing, which can cause damage to the copper traces and components on the board. PCB stiffeners provide the necessary mechanical support to prevent excessive bending and ensure that the PCB maintains its intended shape.
2. Improved Reliability
By reducing the stress on the PCB caused by bending and flexing, PCB stiffeners help improve the overall reliability of the circuit. This is particularly important in applications where the PCB is subjected to frequent movement or vibration, such as in wearable devices or automotive electronics.
3. Enhanced Thermal Management
PCB stiffeners can also help with thermal management by providing a heat-spreading surface that helps dissipate heat away from the components on the board. This is especially important in high-power applications where thermal management is critical to ensure reliable operation.
4. Increased Durability
PCB stiffeners help increase the durability of rigid-flex and flex circuits by protecting the PCB from damage caused by mechanical stress and environmental factors such as moisture and temperature fluctuations.
Designing with PCB Stiffeners
When designing rigid-flex or flex circuits that incorporate PCB stiffeners, there are several factors to consider:
1. Material Selection
The choice of material for the PCB stiffener depends on the specific requirements of the application, such as the desired level of rigidity, thermal conductivity, and environmental resistance. FR-4 and aluminum are common choices for rigid PCB stiffeners, while polyimide and Kapton are often used for flexible PCB stiffeners.
2. Thickness
The thickness of the PCB stiffener should be selected based on the desired level of support and the overall thickness of the PCB stack-up. Typical thicknesses for PCB stiffeners range from 0.2mm to 1.6mm.
3. Placement
The placement of the PCB stiffener on the board is critical to ensure optimal support and functionality. The stiffener should be positioned in areas where the PCB is most likely to experience bending or flexing, such as at connector locations or where the board transitions from rigid to flexible sections.
4. Attachment Method
PCB stiffeners can be attached to the PCB using various methods, such as:
- Adhesive bonding
- Mechanical fastening (screws, rivets)
- Lamination
The choice of attachment method depends on factors such as the material properties of the PCB and stiffener, the desired level of permanence, and the manufacturing process.
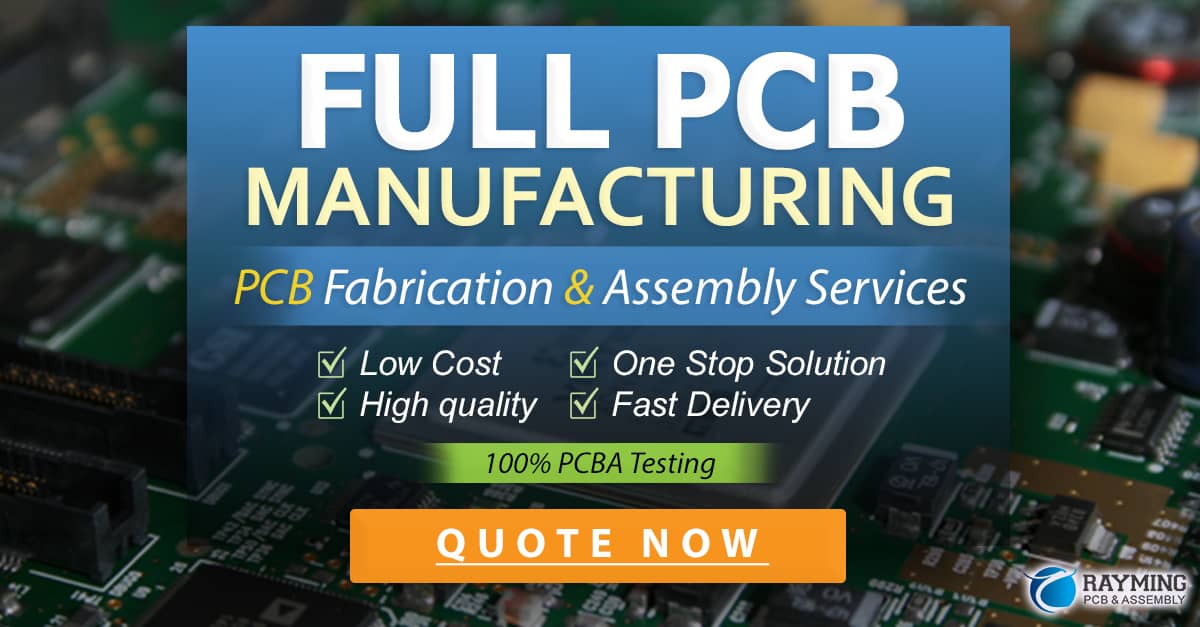
Manufacturing Considerations for PCB Stiffeners
When manufacturing rigid-flex or flex circuits with PCB stiffeners, there are several key considerations:
1. Adhesive Selection
The adhesive used to bond the PCB stiffener to the PCB must be compatible with the materials of both the stiffener and the PCB. The adhesive should also have the necessary mechanical and thermal properties to withstand the intended operating conditions.
2. Lamination Process
If the PCB stiffener is to be laminated to the PCB, the lamination process must be carefully controlled to ensure proper bonding and avoid damage to the PCB or stiffener. Factors such as temperature, pressure, and duration must be optimized for the specific materials being used.
3. Dimensional Stability
The manufacturing process must ensure that the PCB stiffener maintains its intended dimensions and shape, as any deviations can affect the performance and reliability of the final assembly.
4. Compatibility with PCB Manufacturing Steps
The integration of the PCB stiffener into the overall manufacturing process must be carefully planned to ensure compatibility with other steps such as drilling, plating, and component assembly.
Applications of PCB Stiffeners in Rigid-Flex and Flex Circuits
PCB stiffeners are used in a wide range of applications that require the benefits of flexible or rigid-flex PCBs, such as:
- Wearable devices
- Medical equipment
- Automotive electronics
- Aerospace and defense systems
- Industrial control systems
- Consumer electronics
In each of these applications, PCB stiffeners help ensure reliable performance, increased durability, and optimal mechanical and thermal characteristics.
Frequently Asked Questions (FAQ)
- Q: What is the difference between a rigid and flexible PCB stiffener?
A: Rigid PCB stiffeners are made from materials that offer high rigidity and thermal stability, such as FR-4, aluminum, or stainless steel. Flexible PCB stiffeners, on the other hand, are made from materials that provide a combination of flexibility and support, such as polyimide or Kapton.
- Q: How do I choose the right thickness for my PCB stiffener?
A: The thickness of the PCB stiffener should be selected based on the desired level of support and the overall thickness of the PCB stack-up. Typical thicknesses range from 0.2mm to 1.6mm, and the choice depends on factors such as the application requirements and the materials being used.
- Q: Can PCB stiffeners help with thermal management?
A: Yes, PCB stiffeners can help with thermal management by providing a heat-spreading surface that helps dissipate heat away from components on the board. This is particularly important in high-power applications where thermal management is critical for reliable operation.
- Q: What are some common attachment methods for PCB stiffeners?
A: PCB stiffeners can be attached to the PCB using methods such as adhesive bonding, mechanical fastening (screws or rivets), or lamination. The choice of attachment method depends on factors such as the material properties of the PCB and stiffener, the desired level of permanence, and the manufacturing process.
- Q: Are PCB stiffeners suitable for all types of flexible and rigid-flex PCBs?
A: PCB stiffeners are suitable for most types of flexible and rigid-flex PCBs, as they provide the necessary mechanical support, improved reliability, and enhanced durability. However, the specific design and materials used for the stiffener may vary depending on the application requirements and the properties of the PCB itself.
Conclusion
PCB stiffeners are essential components in the design and manufacturing of rigid-flex and flex circuits, providing the necessary mechanical support, improved reliability, enhanced thermal management, and increased durability. When designing with PCB stiffeners, it is important to consider factors such as material selection, thickness, placement, and attachment method to ensure optimal performance and functionality.
By understanding the role of PCB stiffeners and the key considerations for their design and manufacturing, engineers and manufacturers can create reliable and high-performance rigid-flex and flex circuits for a wide range of applications, from wearable devices and medical equipment to automotive electronics and aerospace systems.
0 Comments