What is a Thru-hole Pad?
A thru-hole pad, also known as a plated through hole (PTH), is a type of mounting pad used in printed circuit board (PCB) manufacturing to solder components with wire leads. The pad consists of a hole drilled through the PCB with a copper plating that extends through the hole, electrically connecting the top and bottom surfaces. Components are inserted through these holes and soldered in place on the opposite side.
Thru-hole technology was the dominant method for mounting components on PCBs before the widespread adoption of surface-mount technology (SMT). Despite the shift towards SMT, thru-hole mounting remains important for specific applications, such as high-power devices, connectors, and components subjected to mechanical stress.
Advantages of Thru-hole Mounting
Thru-hole mounting offers several advantages over surface-mount technology:
-
Mechanical strength: Thru-hole components are secured by their leads, which are soldered through the board, providing a stronger mechanical connection than SMT components.
-
Ease of assembly: Manual assembly of thru-hole components is often easier than SMT components, as the leads help to align the component with the pads.
-
High-power handling: Thru-hole components can dissipate more heat than their SMT counterparts due to their leads, which act as heat sinks.
-
Compatibility with older designs: Many legacy designs still rely on thru-hole components, making them essential for maintaining and repairing older equipment.
Thru-hole Pad Classifications
Thru-hole pads can be classified based on various criteria, such as their size, shape, and solder joint quality. Understanding these classifications is crucial for ensuring the reliability and performance of the soldered connection.
Pad Size Classification
Thru-hole pads are classified by their diameter, which is determined by the size of the component lead and the required mechanical strength. Common pad sizes include:
Pad Diameter (mm) | Typical Application |
---|---|
0.6 – 0.8 | Small signal components, resistors, diodes |
0.8 – 1.0 | General-purpose components, capacitors, ICs |
1.0 – 1.5 | Power components, connectors |
1.5 – 2.0 | High-power components, large connectors |
Pad Shape Classification
Thru-hole pads can also be classified based on their shape, which affects the solder joint’s strength and reliability. Common pad shapes include:
- Circular pads: The most common shape, suitable for most applications.
- Oval pads: Provide additional mechanical strength and are often used for connectors or components subjected to mechanical stress.
- Teardrop pads: Offer improved resistance to thermal stress and are commonly used in high-reliability applications, such as aerospace and military electronics.
Solder Joint Quality Classification
The quality of the solder joint is crucial for ensuring the reliability and performance of the electrical connection. Solder joints can be classified based on various criteria, such as:
- Fillet formation: A well-formed fillet should be concave and extend around the component lead and pad.
- Wetting: The solder should wet the pad and lead evenly, without any voids or gaps.
- Hole fill: The solder should fill the hole completely, ensuring a strong mechanical and electrical connection.
The IPC-A-610 standard defines several classes of solder joint quality, each with specific criteria for acceptance:
Class | Description | Typical Application |
---|---|---|
1 | General electronic products, less stringent requirements | Consumer electronics, non-critical applications |
2 | Dedicated service electronic products, moderate requirements | Industrial controls, automotive electronics |
3 | High-performance electronic products, stringent requirements | Aerospace, military, medical devices |
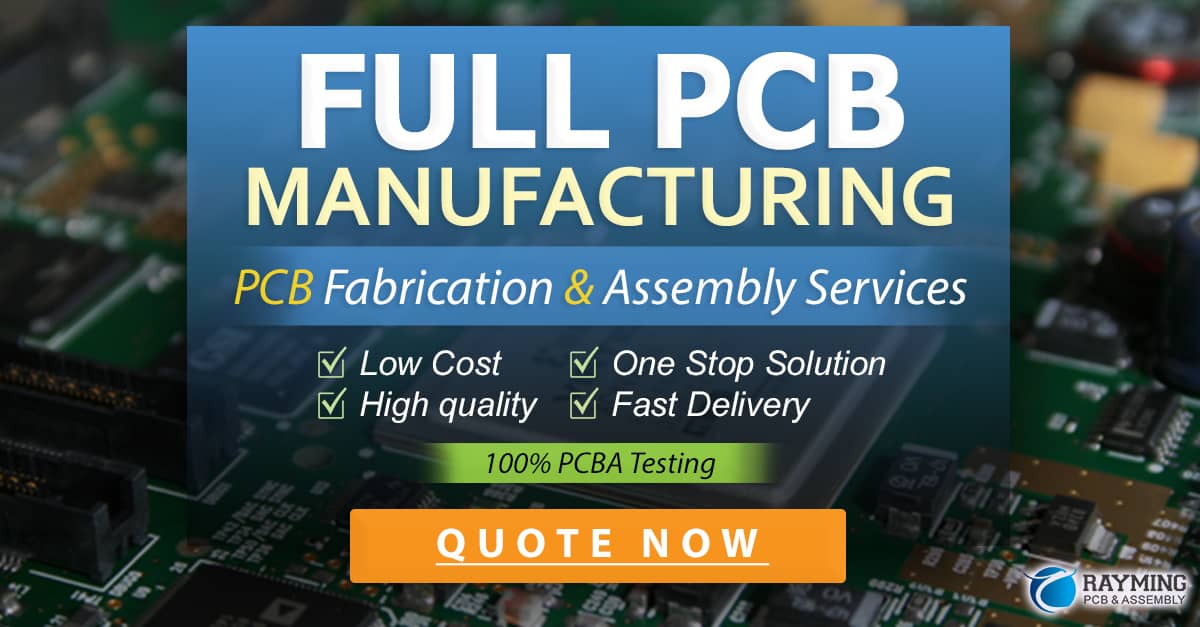
Soldering Techniques for Thru-hole Pads
Several soldering techniques can be used for thru-hole pads, depending on the application and production volume:
- Manual soldering: Suitable for low-volume production, prototyping, and rework. Requires a soldering iron, solder wire, and flux.
- Wave soldering: An automated process that involves passing the PCB over a molten solder wave, suitable for high-volume production.
- Selective soldering: An automated process that targets specific areas of the PCB, ideal for mixed-technology boards with both SMT and thru-hole components.
Regardless of the soldering technique used, it is essential to follow best practices to ensure the quality and reliability of the solder joint:
- Use the correct solder alloy and flux for the application.
- Ensure proper hole sizing and pad design to facilitate solder flow and fillet formation.
- Control the soldering temperature and duration to prevent thermal damage to the components and PCB.
- Clean the soldered assembly to remove flux residue and prevent corrosion.
Inspecting and Testing Thru-hole Solder Joints
Inspecting and testing thru-hole solder joints is essential for ensuring the quality and reliability of the electrical connection. Several methods can be used, depending on the application and production volume:
- Visual inspection: A simple and cost-effective method that involves examining the solder joint for defects such as voids, gaps, or incomplete fillet formation.
- X-ray inspection: A non-destructive method that allows for the detection of internal defects, such as voids or insufficient hole fill.
- Automated optical inspection (AOI): A high-speed, automated method that uses cameras and image processing algorithms to detect surface defects.
- Electrical testing: Involves measuring the electrical continuity and resistance of the solder joint to ensure proper electrical performance.
Regular inspection and testing can help identify process issues and prevent defective products from reaching the end-user.
Frequently Asked Questions (FAQ)
1. What is the difference between thru-hole and surface-mount technology?
Thru-hole technology involves mounting components with wire leads through holes in the PCB, while surface-mount technology involves mounting components directly on the surface of the PCB. Thru-hole mounting provides stronger mechanical connections but requires more space and is less suitable for high-density designs compared to SMT.
2. Can thru-hole and surface-mount components be used on the same PCB?
Yes, mixed-technology PCBs that incorporate both thru-hole and surface-mount components are common in many applications. However, the manufacturing process for mixed-technology boards is more complex and may require specialized equipment, such as selective soldering machines.
3. What is the most common solder alloy used for thru-hole soldering?
The most common solder alloy for thru-hole soldering is Sn63Pb37, which contains 63% tin and 37% lead. However, due to environmental and health concerns, lead-free solder alloys, such as Sn96.5Ag3.0Cu0.5 (SAC305), are increasingly being used in many applications.
4. How can I prevent thermal damage to components during thru-hole soldering?
To prevent thermal damage, it is important to control the soldering temperature and duration. Use a soldering iron with adjustable temperature control and set it to the lowest temperature that still allows for proper solder flow. Additionally, use heat sinks or thermal shunts to protect sensitive components during soldering.
5. What are some common defects in thru-hole solder joints?
Common defects in thru-hole solder joints include insufficient hole fill, voids, gaps, and incomplete fillet formation. These defects can be caused by various factors, such as improper hole sizing, incorrect solder alloy or flux, or poor soldering technique. Regular inspection and testing can help identify and correct these issues.
In conclusion, understanding the classification of soldered thru-hole pads is essential for ensuring the quality, reliability, and performance of electrical connections in PCBs. By considering factors such as pad size, shape, and solder joint quality, and by following best practices for soldering, inspection, and testing, manufacturers can produce high-quality thru-hole assemblies that meet the demands of various applications.
0 Comments