Introduction to PCB Design Issues
Printed Circuit Board (PCB) design is a complex process that requires careful consideration of various factors to ensure optimal performance, reliability, and manufacturability. Despite the advancements in PCB design software and manufacturing techniques, designers often encounter numerous challenges that can lead to costly mistakes and delays in product development. In this article, we will discuss ten common problems in PCB design and provide insights on how to avoid or mitigate them.
1. Incorrect Component Placement
The Importance of Proper Component Placement
One of the most critical aspects of PCB design is component placement. Incorrect component placement can lead to various issues, such as signal integrity problems, thermal management difficulties, and manufacturing challenges. Proper component placement is essential for ensuring optimal performance and reliability of the PCB.
Common Mistakes in Component Placement
Some common mistakes in component placement include:
- Placing components too close to each other, leading to signal crosstalk and thermal issues.
- Placing components in a way that makes routing difficult or impossible.
- Neglecting to consider the orientation of components, which can affect assembly and manufacturing.
Best Practices for Component Placement
To avoid issues related to component placement, consider the following best practices:
- Group components based on their functionality and signal flow.
- Maintain appropriate spacing between components to minimize signal crosstalk and thermal issues.
- Orient components in a way that facilitates efficient routing and manufacturing.
- Use design rules and constraints to ensure proper component placement.
2. Signal Integrity Issues
Understanding Signal Integrity
Signal integrity refers to the ability of a PCB to maintain the quality and timing of electrical signals as they propagate through the board. Poor signal integrity can lead to various problems, such as signal distortion, crosstalk, and electromagnetic interference (EMI).
Factors Affecting Signal Integrity
Several factors can affect signal integrity in PCB design, including:
- Trace length and width
- Impedance matching
- Termination techniques
- Via placement and design
- Material selection
Techniques for Improving Signal Integrity
To improve signal integrity in PCB design, consider the following techniques:
- Use controlled impedance traces to match the impedance of the source and load.
- Implement proper termination techniques, such as series termination and parallel termination.
- Minimize the number of vias and optimize their placement and design.
- Use appropriate materials, such as low-loss dielectrics and high-quality copper.
- Perform signal integrity simulations to identify and mitigate potential issues.
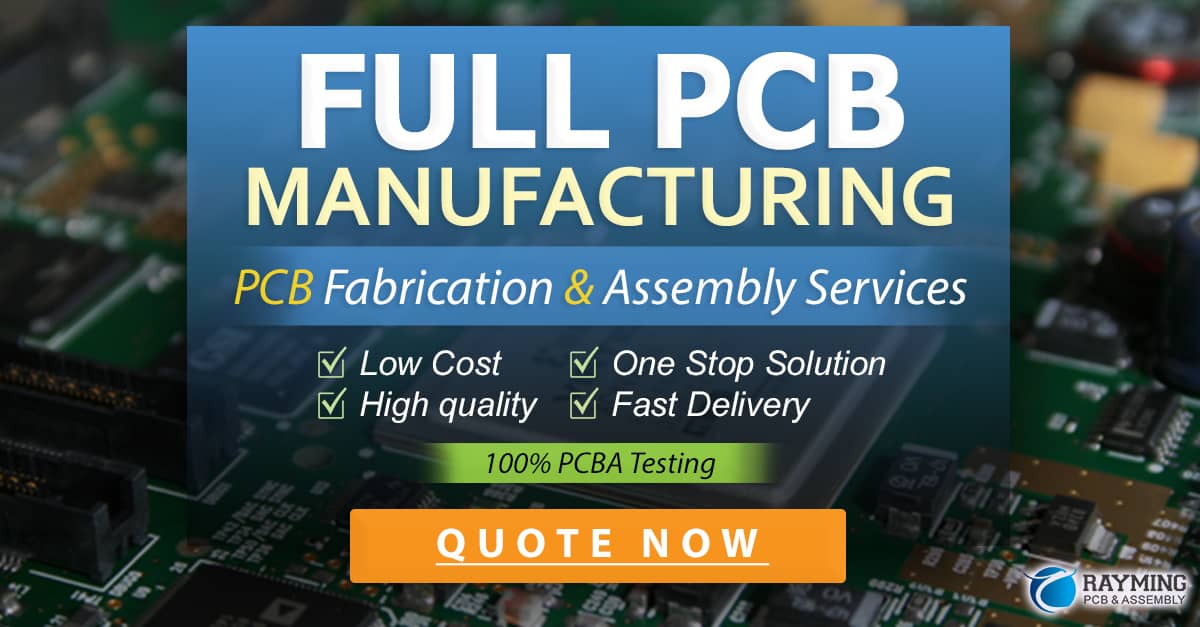
3. Power Distribution Network (PDN) Design
The Role of PDN in PCB Design
The power distribution network (PDN) is responsible for delivering clean and stable power to all components on the PCB. A poorly designed PDN can lead to various issues, such as voltage drops, ground bounces, and electromagnetic interference (EMI).
Common PDN Design Challenges
Some common challenges in PDN design include:
- Designing a low-impedance power delivery system
- Minimizing voltage drops across the board
- Reducing ground bounce and power supply noise
- Ensuring adequate decoupling and bypassing
Best Practices for PDN Design
To overcome PDN design challenges, consider the following best practices:
- Use wide and short traces for power and ground planes to minimize impedance.
- Place decoupling capacitors close to power pins to minimize voltage drops and power supply noise.
- Implement a solid ground plane to provide a low-impedance return path for signals.
- Use appropriate bypassing techniques, such as distributed capacitance and pi-filters.
- Perform PDN simulations to identify and mitigate potential issues.
4. Thermal Management
The Importance of Thermal Management in PCB Design
Thermal management is crucial for ensuring the reliability and longevity of electronic components on a PCB. Overheating can lead to component failure, reduced performance, and even safety hazards.
Factors Affecting Thermal Management
Several factors can affect thermal management in PCB design, including:
- Power dissipation of components
- Ambient temperature
- PCB material properties
- Component placement and spacing
- Airflow and cooling mechanisms
Techniques for Improving Thermal Management
To improve thermal management in PCB design, consider the following techniques:
- Place high-power components away from heat-sensitive components.
- Use thermal vias to conduct heat away from components.
- Incorporate heatsinks and cooling fans for high-power components.
- Select PCB materials with appropriate thermal conductivity and Coefficient of Thermal Expansion (CTE).
- Perform thermal simulations to identify and mitigate potential hot spots.
5. Electromagnetic Compatibility (EMC)
Understanding EMC in PCB Design
Electromagnetic compatibility (EMC) refers to the ability of a PCB to function properly in its electromagnetic environment without causing or being susceptible to electromagnetic interference (EMI).
Sources of EMI in PCB Design
Some common sources of EMI in PCB design include:
- High-speed digital signals
- Power supply noise
- Antenna effects from traces and cables
- Electrostatic discharge (ESD)
Techniques for Improving EMC
To improve EMC in PCB design, consider the following techniques:
- Use proper grounding and shielding techniques to minimize EMI.
- Route high-speed signals away from sensitive analog circuits.
- Implement appropriate filtering and suppression techniques, such as ferrite beads and EMI filters.
- Minimize the loop area of current-carrying traces to reduce magnetic field coupling.
- Perform EMC simulations and testing to identify and mitigate potential issues.
6. Manufacturing Considerations
Designing for Manufacturability (DFM)
Designing for manufacturability (DFM) is the practice of designing PCBs in a way that facilitates efficient and reliable manufacturing processes. Neglecting DFM principles can lead to manufacturing issues, such as poor yield, increased costs, and delays in production.
Common DFM Challenges
Some common DFM challenges in PCB design include:
- Ensuring appropriate component spacing and orientation
- Providing adequate clearances for solder masks and silkscreens
- Designing for automated assembly processes
- Considering the limitations of manufacturing equipment and processes
Best Practices for DFM
To incorporate DFM principles in PCB design, consider the following best practices:
- Follow the manufacturer’s design guidelines and constraints.
- Use standard component sizes and packages whenever possible.
- Provide adequate spacing between components and traces for easy assembly and soldering.
- Include Fiducial Markers and testability features to facilitate automated assembly and testing.
- Communicate with the manufacturer early in the design process to identify and address potential issues.
7. Layout Optimization
The Benefits of Layout Optimization
Layout optimization is the process of refining the PCB layout to improve performance, reliability, and manufacturability. An optimized layout can lead to reduced costs, improved signal integrity, and better thermal management.
Areas for Layout Optimization
Some key areas for layout optimization include:
- Component placement and orientation
- Trace routing and spacing
- Via placement and design
- Power and ground plane design
- Thermal management
Techniques for Layout Optimization
To optimize the PCB layout, consider the following techniques:
- Use autorouting tools with appropriate constraints and design rules.
- Perform manual routing for critical signals and high-speed traces.
- Minimize the number of vias and layer transitions.
- Use solid power and ground planes to reduce impedance and improve signal integrity.
- Perform layout simulations to identify and mitigate potential issues.
8. Stackup Design
The Importance of Stackup Design
The PCB Stackup refers to the arrangement of copper layers, dielectric materials, and planes in a Multilayer PCB. Proper stackup design is crucial for ensuring signal integrity, power integrity, and manufacturability.
Factors Affecting Stackup Design
Several factors can affect stackup design, including:
- The number of layers required
- The thickness and properties of dielectric materials
- The impedance requirements of signals
- The power distribution network design
- The manufacturing capabilities and constraints
Best Practices for Stackup Design
To create an effective PCB stackup, consider the following best practices:
- Use an even number of layers to balance copper distribution and minimize warpage.
- Place signal layers close to power and ground planes to reduce loop inductance.
- Use appropriate dielectric materials based on the frequency and impedance requirements of signals.
- Maintain symmetry in the stackup to minimize warpage and improve manufacturability.
- Collaborate with the manufacturer to ensure the stackup is feasible and cost-effective.
9. Design for Testing (DFT)
The Benefits of DFT
Design for testing (DFT) is the practice of incorporating testability features into the PCB design to facilitate efficient and reliable testing processes. Implementing DFT principles can lead to reduced testing costs, improved product quality, and faster time-to-market.
Common DFT Techniques
Some common DFT techniques in PCB design include:
- Including test points and probe pads for easy access to signals
- Providing boundary scan architecture for automated testing
- Incorporating built-in self-test (BIST) features
- Designing for automated optical inspection (AOI) and X-ray inspection
Best Practices for DFT
To incorporate DFT principles in PCB design, consider the following best practices:
- Identify critical signals and components that require testing.
- Provide adequate test points and probe pads for easy access to signals.
- Use standard test interfaces, such as JTAG and I2C, for automated testing.
- Design the PCB layout to facilitate automated optical inspection (AOI) and X-ray inspection.
- Collaborate with the testing team to ensure the design meets their requirements and constraints.
10. Documentation and Version Control
The Importance of Documentation and Version Control
Proper documentation and version control are essential for ensuring the accuracy, consistency, and traceability of PCB design files. Neglecting these aspects can lead to confusion, errors, and delays in the design and manufacturing processes.
Elements of PCB Documentation
PCB documentation should include the following elements:
- Schematic diagrams
- Bill of materials (BOM)
- PCB layout files
- Assembly drawings
- Fabrication drawings
Best Practices for Documentation and Version Control
To maintain accurate and up-to-date PCB documentation and version control, consider the following best practices:
- Use a consistent naming convention for all design files.
- Maintain a centralized repository for storing and sharing design files.
- Use version control software, such as Git or SVN, to track changes and revisions.
- Include clear and concise documentation for each design file.
- Establish a formal review and approval process for design changes and revisions.
Frequently Asked Questions (FAQ)
- What are the most common signal integrity issues in PCB design?
-
Some of the most common signal integrity issues in PCB design include crosstalk, reflections, and ground bounce. These issues can be mitigated by proper trace routing, impedance matching, and termination techniques.
-
How can I improve thermal management in my PCB design?
-
To improve thermal management in PCB design, consider placing high-power components away from heat-sensitive components, using thermal vias to conduct heat away from components, incorporating heatsinks and cooling fans, and selecting appropriate PCB materials.
-
What are some best practices for designing a reliable power distribution network?
-
Some best practices for designing a reliable power distribution network include using wide and short traces for power and ground planes, placing decoupling capacitors close to power pins, implementing a solid ground plane, and using appropriate bypassing techniques.
-
How can I ensure my PCB design is manufacturable?
-
To ensure your PCB design is manufacturable, follow the manufacturer’s design guidelines and constraints, use standard component sizes and packages, provide adequate spacing between components and traces, and include fiducial markers and testability features.
-
What are the benefits of incorporating design for testing (DFT) principles in PCB design?
- Incorporating DFT principles in PCB design can lead to reduced testing costs, improved product quality, and faster time-to-market. Some common DFT techniques include including test points and probe pads, providing boundary scan architecture, and designing for automated optical inspection (AOI) and X-ray inspection.
Conclusion
PCB design is a complex process that requires careful consideration of various factors to ensure optimal performance, reliability, and manufacturability. By understanding and addressing the ten common problems discussed in this article, designers can create high-quality PCBs that meet the requirements of their applications. Implementing best practices in component placement, signal integrity, power distribution, thermal management, EMC, manufacturing, layout optimization, stackup design, DFT, and documentation and version control can help designers avoid costly mistakes and delays in product development.
0 Comments