Introduction to SMD Technology
Surface mount technology, commonly known as SMT, is a method of assembling electronic circuits where components are mounted directly onto the surface of printed circuit boards (PCBs). This differs from the older through-hole technology where component leads are inserted through holes in the PCB and soldered on the other side.
SMD components are significantly smaller than their through-hole counterparts. Rather than using connector pins, SMD components have small metal pads or leads on the bottom which are soldered directly to matching pads on the PCB surface. The small size and low profile of SMD components enables much higher component density on PCBs and allows for miniaturization of electronic devices.
Some key advantages of SMD technology:
- Smaller and lighter PCB assemblies
- Higher component density and miniaturization
- Improved electrical performance at high frequencies
- Lower manufacturing costs at high production volumes
- Automated assembly processes
SMD components must be carefully handled and precisely positioned during assembly processes. A variety of specialized equipment is used in SMD manufacturing to place, align, and solder the tiny components onto PCBs efficiently and reliably.
SMD Component Types
There is a wide variety of different SMD component packages, but some of the most common types include:
Resistors and Capacitors
- 0402 – 1mm x 0.5mm rectangular size
- 0603 – 1.6mm x 0.8mm rectangular size
- 0805 – 2mm x 1.25mm rectangular size
- 1206 – 3.2mm x 1.6mm rectangular size
Integrated Circuits (ICs)
- SOIC – Small Outline Integrated Circuit package
- QFP – Quad Flat Package with leads on all four sides
- BGA – Ball Grid Array package with solder ball terminals underneath
Light Emitting Diodes (LEDs)
- 0603 / 0805 sizes
- Often have directional polarity which must be oriented correctly
SMD Printing and Solder Paste Application
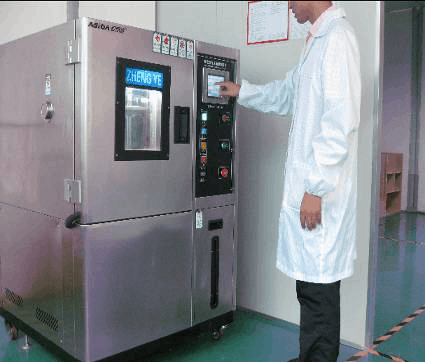
Solder paste is a sticky mixture of solder particles and flux which facilitates SMD soldering. It is printed onto PCB pads in a pattern which matches the solder pads on the components.
Solder Paste Printing Process:
- PCBs are cleaned and prepared with solder mask and surface finish
- Solder stencil is aligned over the PCB
- Solder paste is applied to top of stencil using a squeegee blade
- Solder paste squeegees through apertures onto PCB pads
- Stencil is removed, leaving solder paste deposits in pad pattern
Solder Paste Printing Parameters | Details |
---|---|
Solder Paste | Mixture of solder powder with flux |
Solder Stencil | Laser cut metal sheet with pad apertures |
Stencil Thickness | Typically 100-150 microns for standard components |
Stencil to PCB Alignment | Critical for accurate paste deposits |
Solder Deposit Inspection | Check for missing or excess paste |
Solder paste deposits must have the right amount of paste and be accurately aligned to pads to ensure successful soldering. Machine vision inspection is often used to check paste deposits.
SMD Component Placement
SMD components must be precisely placed onto the solder paste deposits on the PCB pads. High speed Pick and Place machines are used for automated component population.
Pick and Place Process:
- Machines have feeders with tape-and-reel components
- Vision system identifies components and locations
- Vacuum pickup tool grabs components
- Components placed accurately onto solder paste pads
- Cycle time typically 0.1 to 0.5 seconds per component
Pick and Place Parameters | Details |
---|---|
Component Feeders | Tape-and-reel, trays, sticks |
Feeder Setup | Correct components in right feeder slots |
Component Tapes | Orientation, pocket spacing |
Nozzle Selection | Vacuum size for different components |
Placement Accuracy | +/- 50 microns typical requirement |
Placement Speed | Up to >100,000 components per hour |
Component placement accuracy and tip alignment is critical to avoid positional defects such as tombstoning. Fiducial marks and vision alignment improve accuracy.
SMD Soldering Processes
After component placement, the PCB assembly is soldered using a reflow soldering process. The solder paste is heated past its liquidus temperature to establish solder joint connections.
Reflow Oven Soldering
- PCB/components pass through a multi-zone convection oven
- Different heating zones ramp temperature up and down
- Peak temperature melts solder paste to form joint connections
- Typical profile: ramp up to 150°C, above 183°C for 60 sec, peak 230-260°C
- Nitrogen atmosphere prevents oxidation
Reflow Parameters | Details |
---|---|
Heating Zones | Pre-heat, soak, reflow |
Peak Temperature | Above solder melting point |
Time Above Liquidus | For good wetting 60-90 sec |
Cooling Rate | Rapid cooling after reflow peak |
Process Monitoring | Profiles, thermocouples |
Reflow ovens allow efficient high volume soldering. Convection heating and profile control are critical to achieve good solder joint reliability.
Wave Soldering
- Bottom side soldering for SMD mixed with through-hole components
- Bottom of PCB passes over flowing wave or jet of molten solder
- Solder wets onto exposed pads and leads making solder joint connections
- Used where some leaded components are required
- Challenging for many SMD package types due to rapid heating
Wave Solder Parameters | Details |
---|---|
Solder Pot | Molten solder pumped into nozzle |
Preheating | Bottom side PCB heating to 130-160°C |
Wave Shape/Height | Laminar flow preferred |
Conveyor Speed | Travel speed over solder wave |
Fluxing | Removes oxides to enable soldering |
The soldering process must be optimized for the SMD package types and board design to minimize defects such as bridging or tombstoning.
SMD Rework and Repair
Defective solder joints, positional errors, or wrong components may need reworking on assembled SMD boards. This is challenging due to high density and small components.
Common SMD Rework Methods:
- Hand Soldering – requires soldering iron tip optimization and operator skill
- Hot Air – directed heat & airflow for component removal and pad cleaning
- Laser – precision heating to reflow/remove solder joints
- Thermo-tweezers – tweezer tips heat chip quickly for rework
Rework Considerations | Details |
---|---|
Identifying Defects | Optical inspection, x-ray, in-circuit test |
Heating Method | Minimize thermal damage |
Cleanup | Flux residue removal |
Rework Documentation | Recording rework actions taken |
Rework can avoid scrapping costly SMD assemblies, but risks further damaging the board if not done properly.
Quality Control and Inspection
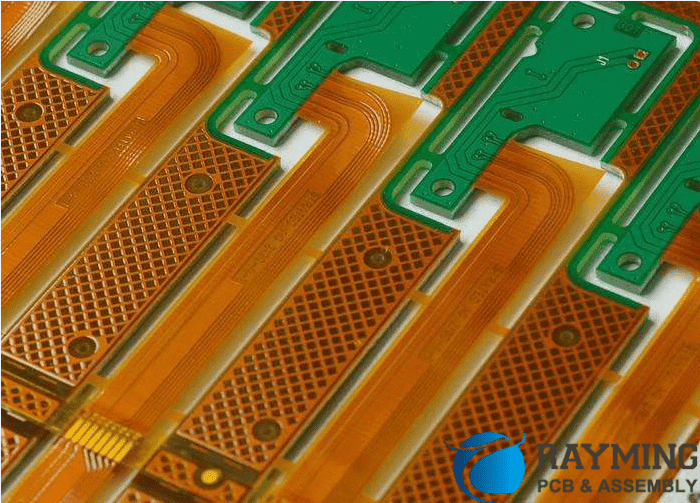
Thorough inspection and testing at multiple stages ensures assembly quality for the small and hidden solder joints.
- Paste Inspection – verify print alignment and deposit volumes
- Post-placement – check component alignment/orientation
- AOI – Automated Optical Inspection checks solder joints
- X-Ray – sees hidden joints and internal structure
- ICT – In-circuit Testing for electrical faults
- AOI/AXI – Automated X-ray Inspection
- Cross-sectioning – solder joint evaluation and process feedback
Inspection Criteria | Common Checks |
---|---|
Solder Paste | Alignment, print volume, slump |
Component Placement | Polarity, position, skewed |
Solder Joints | Flooding, bridges, voids |
Electrical Testing | Opens, shorts, value testing |
Effective process controls and inspection methods are essential to avoid defects and escapes in SMD assembly.
SMD Assembly Challenges
While SMD assembly offers many advantages, some process challenges must be addressed:
- Fine components – handling/placement more difficult at 01005 or 0.4mm BGA pitch
- Mixing SMD and through-hole – soldering process integration
- Dense PCBs – thermal management and rework access
- Tall components – tombstoning risk, placement access
- Fine-pitch ICs – solder bridging potential
- Bottom Terminations – BGAs require x-ray inspection
- RF/high frequency – electrical performance sensitivity
- Rework – low margin for error
Careful process design, optimization, controls, and inspection can overcome these challenges to leverage the full benefits of surface mount technology.
SMD Assembly Equipment
Specialized hardware is essential for efficient and high-quality SMD production:
- Solder Paste Printer – precise solder paste deposition
- Pick and Place Machine – high speed accurate component placement
- Reflow Oven – convection heating for soldering
- Wave Solder – for soldering bottom side SMDs
- AOI System – automated optical inspection of solder joints
- AXI System – automated x-ray inspection
- Rework Station – heat and tools for component removal
- Oven – baking of PCBs and moisture sensitive components
SMD assembly requires significant equipment investments, but enables automated mass production.
Summary of SMD Assembly Benefits
When designed and executed well, the transition to surface mount device assembly provides many advantages:
- Dramatically smaller and lighter products
- High density component packing and miniaturization
- Improved electrical performance
- Lower assembled costs at high volumes
- Automated manufacturing with faster process times
- Flexible and efficient manufacturing
Continuing advances in SMD packaging and assembly technologies will enable electronics innovation and miniaturization. Careful process engineering is key to benefit from SMDs.
FAQ
What are the primary benefits of SMD assembly versus through-hole?
The main advantages of SMD assembly are the small size and low weight of components, higher component density and PCB miniaturization, improved electrical performance at high frequencies, lower manufacturing costs at high volumes, and suitability for automated assembly processes.
What causes tombstoning defects in SMD assembly?
Tombstoning happens when one pad lifts off the board during reflow while the other side stays anchored down. This causes the component to stand upright like a tombstone. It can be caused by uneven solder paste deposition, misaligned parts, non-optimized reflow profile, or board/component warpage.
How does solder paste printing work?
Solder paste printing involves using a stencil placed over the PCB and a squeegee blade to force solder paste through the stencil apertures and onto the pads on the board. The stencil is then removed leaving precise deposits of solder paste ready for component placement.
What processes are used for reworking SMD assemblies?
Common SMD rework methods include hand soldering with fine tip irons, hot air tools to target heating at components, laser assisted heating, and thermal tweezers that can heat individual components. The goal is to apply thermal energy only where needed for reworking.
Why is x-ray inspection important for SMD assemblies?
X-ray inspection can see hidden solder joints like those under BGA packages and inside multi-layer PCBs. It finds defects such as poor wetting, voids, excessive voiding, and bridging that cannot be found with optical inspection alone.
0 Comments