Introduction
A stencil is an essential tool for assembling printed circuit boards (PCBs) using the surface mount technology (SMT). The stencil is used to apply solder paste onto the PCB pads during the solder printing process before the surface mount components are placed. Using the right stencil is crucial for achieving an accurate and high-quality solder print, which directly impacts the reliability and performance of the assembled PCB. This article provides a comprehensive guide on stencils for PCB assembly covering the types, design considerations, materials, critical factors, and troubleshooting.
Types of Stencils
There are several types of stencils used for PCB solder printing:
Metal Stencils
Metal stencils are the most common type used in PCB assembly. They are made from stainless steel, nickel alloys or brass. Laser cutting is used to cut the stencil apertures to match the PCB pad layout. The benefits of metal stencils include durability, dimensional stability at high temperatures, and ability to produce fine features.
Plastic Stencils
Plastic stencils like polyimide are a lower cost alternative to metal stencils. They can be used for lower volume PCB assembly but have limitations in terms of fine feature definition and high temperature tolerance.
Disposable Stencils
These are single-use stencils made from aluminum foil, paper or plastic films. They are very inexpensive but offer lower quality and consistency compared to metal stencils. Disposable stencils cannot be cleaned or reused.
Reusable Stencils
Reusable stencils are made from flexible materials like silicone, rubber or polyurethane. They conform to the PCB surface and can be cleaned and reused. However, they have limitations in terms of feature size, registration accuracy and material compatibility.
Stencil Design Considerations
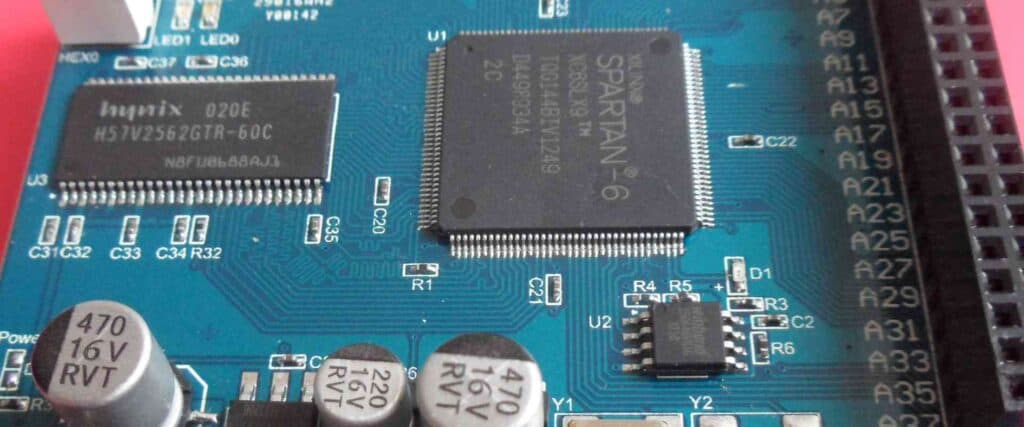
The stencil design has a significant impact on the solder paste printing quality and must match the PCB land pattern design. Here are some key considerations:
Stencil Thickness
Typical stencil thickness ranges from 100 to 150 microns. Thicker stencils improve paste release while thinner stencils improve fine pitch printing capability. Stencil thickness must be optimized based on the PCB design.
Stencil Aperture Design
The stencil aperture openings must match the copper pads on the PCB but are typically designed with a slightly smaller size to account for paste spreading. The area ratio between the stencil aperture and the PCB pad is a critical factor.
Step down Apertures
Step down apertures involve using different thickness in different aperture areas. This helps control the paste volume for adjacent pads with vastly different sizes.
Bridging
Small bridges may be designed between apertures to aid paste release. The bridge width needs to be optimized – too large can lead to bridges while too small can prevent paste release.
Stencil Materials
Stencil material properties directly influence the printing process and quality. Here are some options:
Stainless Steel
Most common metal stencil material due to its durability and dimensional stability at high temperatures. It also allows easy cleaning. However, steel is prone to abrasion during cleaning.
Nickel Alloys
Nickel alloys provide better abrasion resistance compared to steel for longer stencil life. However, nickel can be more difficult to clean.
Brass
Brass stencils are less expensive but suffer from shorter lifespan and poor abrasion resistance.
Plastics
Plastic stencils like polyimide are suitable for lower temperature applications. They are flexible but have limitations in chemical resistance.
Critical Factors in PCB Stencil Printing
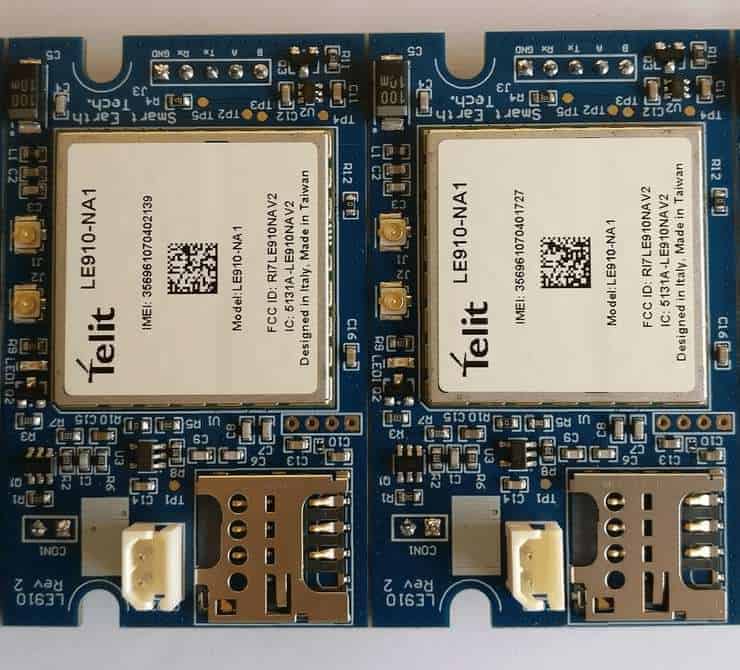
Achieving good print quality requires optimizing multiple stencil and process parameters:
Stencil Thickness
As mentioned earlier, stencil thickness directly impacts paste release and print definition.
Stencil Tension
Applying proper tension while mounting the stencil on the printer ensures good gasketing and registration. Excess tension can damage the stencil.
Print Gap
The gap between the PCB surface and the bottom side of the stencil must be precisely controlled, typically around 0.10-0.15mm. Too low can cause smearing while too high can lead to insufficient paste transfer.
Print Speed
Faster print speeds can lead to smearing while slower speeds reduce throughput. Speed must be balanced with quality.
Separation Speed
The speed at which the stencil separates from the PCB after print affects paste transfer efficiency and bridging. Slower separation is better.
Underside Cleaning
Keeping the stencil underside clean is vital for consistent print quality. Both wet and dry cleaning methods are used. Cleaning frequency is important.
Solder Paste Condition
Fresh paste with optimal tackiness results in good release off the stencil apertures. The paste should also be rolled properly to remove bubbles which can impact release.
Stencil Underprinting Inspection
Given the importance of the stencil printing step, automated optical inspection of the PCB after stencil underprinting is highly recommended. This helps detect any defects early to prevent further assembly with defective prints. Both 2D and 3D AOI systems are available for this purpose.
Stencil Maintenance and Cleaning
Like any other production tool, stencils require regular cleaning and maintenance for sustained performance. Here are some guidelines:
- Perform dry wiping of the stencil underside at regular intervals during printing to remove any picked up paste.
- Clean the stencil thoroughly at the end of each production shift to remove all residual paste.
- Use an automatic stencil cleaning machine for optimal and repeatable cleaning results.
- Avoid aggressive manual wiping which can damage stencil features.
- Periodically inspect stencils and replace once they are worn out beyond recovery.
Troubleshooting Stencil Printing Issues
Here are some common stencil printing defects and potential causes:
Problem: Insufficient paste volume on pads
Causes: Stencil aperture too small, high snap-off distance, too little print pressure
Problem: Smearing or slumping
Causes: Low snap-off distance, high print speed, coarse paste
Problem: Skipping
Causes: Poor paste release, low stencil tension, dried paste, damaged aperture
Problem: Bridging
Causes: Too narrow bridge, slow separation speed, high print pressure
Problem: Poor registration
Causes: Incorrect stencil tensioning, warped stencil, printer issues
Problem: Blocked apertures
Causes: Dried paste, damaged aperture, poor cleaning
Conclusion
The stencil is a vital consumable in the PCB assembly process. Using the optimal stencil design and materials along with controlling the print parameters and regular stencil maintenance is key to achieving high yield and reliable PCB assemblies. As PCBs become smaller and more complex, the quality expectation from stencil printing increases further. The guidelines provided in this article will help manufacturers setup a robust stencil printing process.
Frequently Asked Questions
Q1. How are stencils manufactured?
Stencils are typically manufactured by laser cutting or chemical etching of sheet metal or plastic films based on the stencil design file. Stainless steel is the most common metal used for laser cut stencils due to its high precision capability.
Q2. How often should stencils be cleaned?
A good rule of thumb is to clean stencils after every 20-30 print cycles. More frequent cleaning may be required for fine pitch designs. Proper cleaning intervals help minimize printing defects due to paste residue buildup on stencils.
Q3. What is the typical lifespan of a stencil?
With proper care and maintenance, steel and nickel stencils can last over 50,000 print cycles. Thinner and softer materials like plastics deteriorate faster. Stencil life also depends on the PCB complexity and cleaning process.
Q4. Can stencil design compensate for PCB warp?
Yes, stencil design strategies like multi-level screens and stepped apertures can help reduce paste height variations across warped PCBs. Warped PCBs should be avoided as they lead to non-uniform print quality.
Q5. How does stencil tension impact printing?
Insufficient tension can allow the stencil to lift off locally causing defects. Excessive tension can damage the stencil. 5-25 N/cm frame tension is typically recommended for optimal gasketing without distorting the stencil.
0 Comments