Introduction to Solder Paste Printing
Solder paste printing is a crucial step in the surface mount technology (SMT) assembly process. It involves depositing solder paste onto the pads of a printed circuit board (PCB) using a stencil. The quality of the solder paste print directly affects the reliability and functionality of the final assembled product. In this article, we will discuss some valuable tips for achieving high-quality solder paste prints.
Choosing the Right Solder Paste
Solder Paste Composition
Solder paste is a mixture of tiny solder particles suspended in a flux medium. The composition of the solder paste plays a significant role in its printing performance. When selecting a solder paste, consider the following factors:
- Alloy type (e.g., tin-lead, lead-free)
- Particle size distribution
- Flux type (e.g., no-clean, water-soluble, rosin-based)
- Viscosity
- Slump resistance
Solder Paste Storage and Handling
Proper storage and handling of solder paste are essential to maintain its quality and consistency. Follow these guidelines:
- Store solder paste in a refrigerator at the manufacturer-recommended temperature (usually between 2-10°C).
- Allow the solder paste to reach room temperature before opening the container to prevent condensation.
- Gently mix the solder paste before use to ensure homogeneity.
- Avoid exposing the solder paste to excessive heat or humidity.
Stencil Design Considerations
Aperture Size and Shape
The stencil aperture size and shape directly impact the volume and geometry of the solder paste deposit. Consider these factors when designing the stencil:
- Pad size and pitch
- Component package type (e.g., QFP, BGA, chip components)
- Solder paste volume requirements
- Aperture wall tapering to facilitate paste release
Stencil Thickness
The stencil thickness determines the height of the solder paste deposit. A thicker stencil results in a higher volume of solder paste. Choose the appropriate stencil thickness based on the following considerations:
- Component lead/ball pitch
- Solder joint size requirements
- Solder paste type and particle size
- PCB surface finish
Typical stencil thicknesses range from 0.100 mm to 0.150 mm (4-6 mils) for standard SMT assemblies.
Stencil Material
Stainless steel is the most common material used for solder paste stencils. It offers durability, stability, and good paste release properties. Other materials, such as nickel-plated stainless steel or laser-cut polyimide, may be used for specific applications or fine-pitch designs.
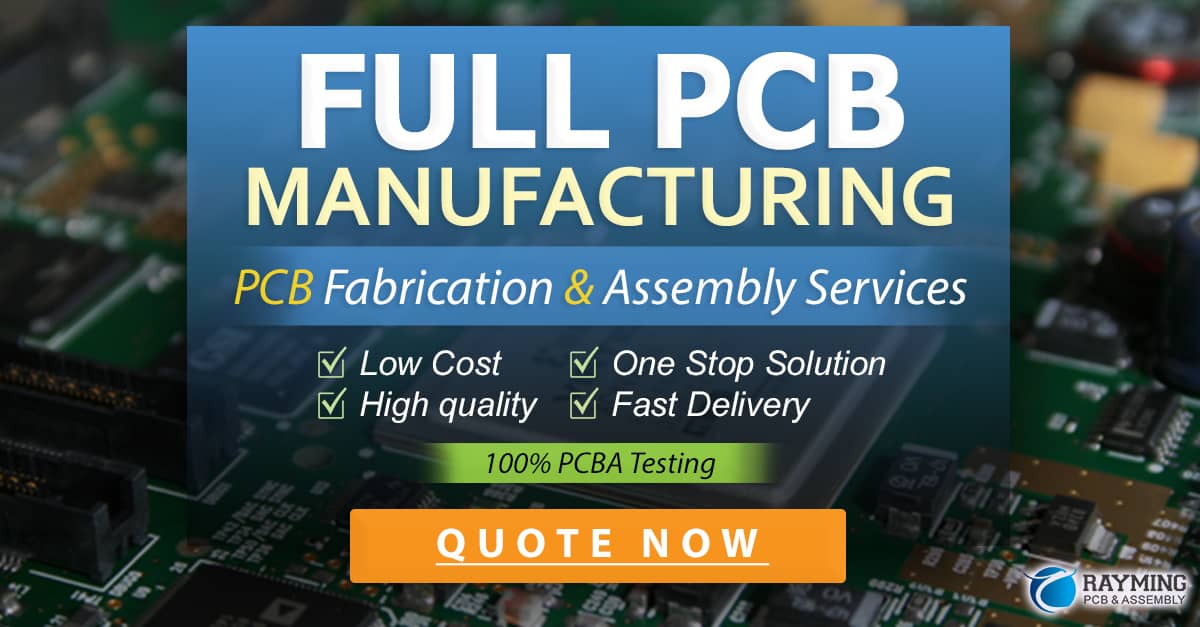
Printer Setup and Calibration
Squeegee Pressure and Speed
The squeegee pressure and speed settings affect the solder paste print quality. Optimal settings depend on the solder paste type, stencil design, and PCB surface characteristics. Follow these guidelines:
- Start with the manufacturer-recommended squeegee pressure and speed settings.
- Adjust the pressure to achieve a consistent paste deposit without smearing or stencil damage.
- Set the speed to allow sufficient time for the solder paste to fill the apertures and release from the stencil.
- Conduct print tests and inspect the results to fine-tune the settings.
Printer Alignment and Leveling
Proper alignment and leveling of the printer are critical for achieving accurate and consistent solder paste prints. Perform the following checks:
- Align the PCB and stencil using fiducial marks or camera-based vision systems.
- Ensure the PCB support pins are properly adjusted to prevent board warping or flexing.
- Level the stencil and PCB to maintain uniform print pressure across the entire surface.
- Verify the squeegee blade parallelism to the stencil surface.
Stencil Cleaning
Regular stencil cleaning is necessary to prevent solder paste buildup and contamination. Implement a stencil cleaning routine based on the following factors:
- Solder paste type and flux residue
- Print volume and frequency
- Environmental conditions (e.g., temperature, humidity)
Use appropriate cleaning agents and methods, such as manual wiping, spray-in-air systems, or ultrasonic cleaning, to ensure thorough and efficient stencil cleaning.
Print Process Control
Print Parameter Optimization
Optimize the print parameters to achieve the desired solder paste deposit quality. Key parameters include:
- Print pressure
- Print speed
- Separation speed
- Print gap
- Snap-off distance
Conduct print trials and analyze the results using solder paste inspection (SPI) systems or visual examination. Adjust the parameters iteratively until the desired print quality is achieved.
Print Volume Monitoring
Regularly monitor the solder paste print volume to ensure consistency and identify any deviations from the target values. Use SPI systems or offline measurement techniques to assess the print volume. Establish statistical process control (SPC) limits and take corrective actions when necessary.
Environmental Control
Maintain a stable and controlled environment in the printing area to minimize the impact of temperature and humidity variations on solder paste performance. Implement the following measures:
- Control the room temperature and humidity within the recommended ranges (typically 20-25°C and 35-60% RH).
- Avoid direct airflow or drafts near the printer.
- Use ESD-safe equipment and practices to prevent electrostatic discharge damage.
Troubleshooting Common Print Defects
Insufficient or Excessive Solder Paste
Insufficient or excessive solder paste can lead to open circuits, bridging, or tombstoning defects. Address these issues by:
- Adjusting the stencil aperture size or shape
- Optimizing the print pressure and speed
- Checking the solder paste for proper viscosity and consistency
- Verifying the stencil alignment and cleanliness
Solder Paste Smearing or Spreading
Solder paste smearing or spreading can cause bridging or short circuits. Resolve these problems by:
- Reducing the print pressure or speed
- Increasing the snap-off distance
- Ensuring proper stencil cleaning
- Checking the squeegee blade condition and parallelism
Poor Paste Release or Stencil Clogging
Poor paste release or stencil clogging can result in incomplete or inconsistent prints. Address these issues by:
- Optimizing the stencil aperture design and wall tapering
- Adjusting the print parameters (e.g., separation speed, print gap)
- Using a compatible solder paste and flux chemistry
- Implementing regular stencil cleaning and maintenance
Best Practices for Solder Paste Printing
Operator Training and Skill Development
Provide comprehensive training to operators involved in solder paste printing. Cover topics such as:
- Printer setup and calibration
- Stencil handling and maintenance
- Solder paste storage and handling
- Print process control and monitoring
- Defect identification and troubleshooting
Encourage continuous skill development through periodic training sessions and certifications.
Standardized Procedures and Documentation
Establish standardized procedures for solder paste printing to ensure consistency and repeatability. Create detailed documentation, including:
- Standard operating procedures (SOPs)
- Process control plans
- Maintenance and calibration schedules
- Troubleshooting guides
Regularly review and update the documentation to reflect changes in processes or equipment.
Continuous Improvement and Process Optimization
Foster a culture of continuous improvement in solder paste printing. Encourage operators and engineers to:
- Monitor process performance and identify areas for improvement
- Conduct controlled experiments to optimize print parameters
- Implement statistical process control (SPC) techniques
- Share best practices and lessons learned across the organization
Frequently Asked Questions (FAQ)
1. What is the recommended storage temperature for solder paste?
The recommended storage temperature for solder paste is typically between 2-10°C (35-50°F). Always refer to the manufacturer’s guidelines for specific storage requirements.
2. How often should I clean the solder paste stencil?
The frequency of stencil cleaning depends on factors such as the solder paste type, print volume, and environmental conditions. As a general guideline, clean the stencil every 4-8 hours of continuous printing or whenever print quality degrades.
3. What is the optimal solder paste print pressure?
The optimal solder paste print pressure varies depending on the solder paste type, stencil design, and PCB surface characteristics. Start with the manufacturer’s recommended settings and fine-tune the pressure through print trials and analysis. Typical print pressure ranges from 0.2 to 0.5 kg/cm² (3-7 psi).
4. How do I prevent solder paste bridging?
To prevent solder paste bridging, consider the following measures:
– Optimize the stencil aperture design and spacing
– Adjust the print pressure and speed
– Ensure proper stencil alignment and cleanliness
– Use a solder paste with appropriate viscosity and slump resistance
5. What is the shelf life of solder paste?
The shelf life of solder paste varies depending on the manufacturer and the specific formulation. Most solder pastes have a shelf life of 6-12 months when stored at the recommended temperature. Always check the manufacturer’s guidelines and the expiration date on the container.
Conclusion
Solder paste printing is a critical process in SMT assembly that requires careful control and optimization. By following the tips and best practices outlined in this article, you can achieve high-quality solder paste prints and improve the reliability of your assembled products. Remember to select the appropriate solder paste, design the stencil properly, set up and calibrate the printer, control the print process, and continuously monitor and improve your printing operations.
Solder Paste Printing Tips | Benefits |
---|---|
Choose the right solder paste | Ensures compatibility with the process and materials |
Optimize stencil design | Achieves desired solder paste volume and geometry |
Set up and calibrate the printer | Maintains consistent and accurate prints |
Control print parameters | Produces reliable and repeatable results |
Implement regular stencil cleaning | Prevents solder paste buildup and contamination |
Monitor print volume and quality | Identifies deviations and enables corrective actions |
Provide operator training | Enhances skills and reduces human errors |
Establish standardized procedures | Ensures consistency and repeatability |
Foster continuous improvement | Optimizes the process and improves overall performance |
By implementing these solder paste printing tips and best practices, you can enhance the quality and reliability of your SMT assemblies, reduce defects, and increase production efficiency.
0 Comments