What is Solder Bridging?
Solder bridging, also known as solder shorts or solder jumpers, is a common defect that occurs during the printed circuit board (PCB) assembly process. It happens when excess solder inadvertently connects two or more adjacent pads, pins, or traces that are not meant to be connected, causing short circuits and potential malfunctions in the electronic device.
Solder bridging can be a significant issue in PCB manufacturing, leading to reduced yields, increased rework costs, and potential reliability problems. Understanding the causes of solder bridging and implementing appropriate preventive measures are crucial for achieving high-quality PCB assembly.
Causes of Solder Bridging
There are several factors that can contribute to the occurrence of solder bridging during PCB assembly. Some of the main causes include:
1. Excessive Solder Paste Deposition
One of the primary causes of solder bridging is the application of too much solder paste during the stencil printing process. When an excessive amount of solder paste is deposited on the pads, it can flow and spread beyond the intended area during the reflow soldering process, leading to bridging between adjacent pads or pins.
2. Improper Stencil Design
The stencil plays a crucial role in determining the amount and placement of solder paste on the PCB. If the stencil apertures are too large or not properly aligned with the pads, it can result in excessive or misaligned solder paste deposition. This, in turn, increases the risk of solder bridging during the reflow process.
3. Insufficient Solder Mask Clearance
Solder mask is a protective layer applied to the PCB to prevent solder from adhering to unintended areas. If there is insufficient clearance between the solder mask and the pads or traces, solder can flow beyond the desired regions and create bridges.
4. Component Placement Inaccuracies
Accurate component placement is essential for preventing solder bridging. If components are misaligned or not properly seated on the pads, it can lead to solder flowing between the pins or pads, resulting in bridging.
5. Inadequate Reflow Profile
The reflow soldering process involves subjecting the PCB to a controlled temperature profile to melt the solder paste and form reliable solder joints. If the reflow profile is not optimized, it can cause solder to flow excessively or not properly wet the surfaces, increasing the likelihood of bridging.
6. Contamination
Contaminants such as dust, dirt, or oils on the PCB surface or components can interfere with the solder wetting process and contribute to solder bridging. Proper cleaning and handling procedures are essential to minimize contamination risks.
Prevention and Mitigation Strategies
To minimize the occurrence of solder bridging and improve PCB assembly quality, several preventive measures can be implemented:
1. Stencil Design Optimization
Ensure that the stencil design is optimized for the specific PCB layout and component requirements. This includes selecting appropriate aperture sizes, shapes, and locations to achieve the desired solder paste deposition. Regularly inspect and maintain the stencil to ensure its integrity and cleanliness.
2. Solder Paste Printing Process Control
Implement strict process controls during solder paste printing to maintain consistent and accurate solder paste deposition. This includes monitoring and adjusting parameters such as print speed, pressure, and separation distance. Regular calibration and maintenance of the printing equipment are also critical.
3. Solder Mask Design and Application
Pay close attention to the solder mask design and application process. Ensure adequate clearance between the solder mask and the pads or traces to prevent solder from flowing into unintended areas. Use high-quality solder mask materials and follow proper application procedures.
4. Component Placement Accuracy
Invest in high-precision component placement equipment and implement robust process controls to ensure accurate and consistent component placement. Regular calibration and maintenance of the placement machines are essential. Conduct visual inspections and use automated optical inspection (AOI) systems to detect placement errors early in the process.
5. Reflow Profile Optimization
Develop and optimize the reflow profile for each specific PCB assembly. Consider factors such as the solder paste type, component thermal requirements, and board characteristics. Regularly monitor and adjust the reflow profile to ensure optimal solder melting and wetting while minimizing the risk of bridging.
6. Cleanliness and Contamination Control
Implement strict cleanliness and contamination control measures throughout the PCB assembly process. This includes maintaining a clean and dust-free manufacturing environment, using clean gloves and tools, and following proper handling procedures. Regular cleaning and inspection of the PCBs and components can help identify and address contamination issues.
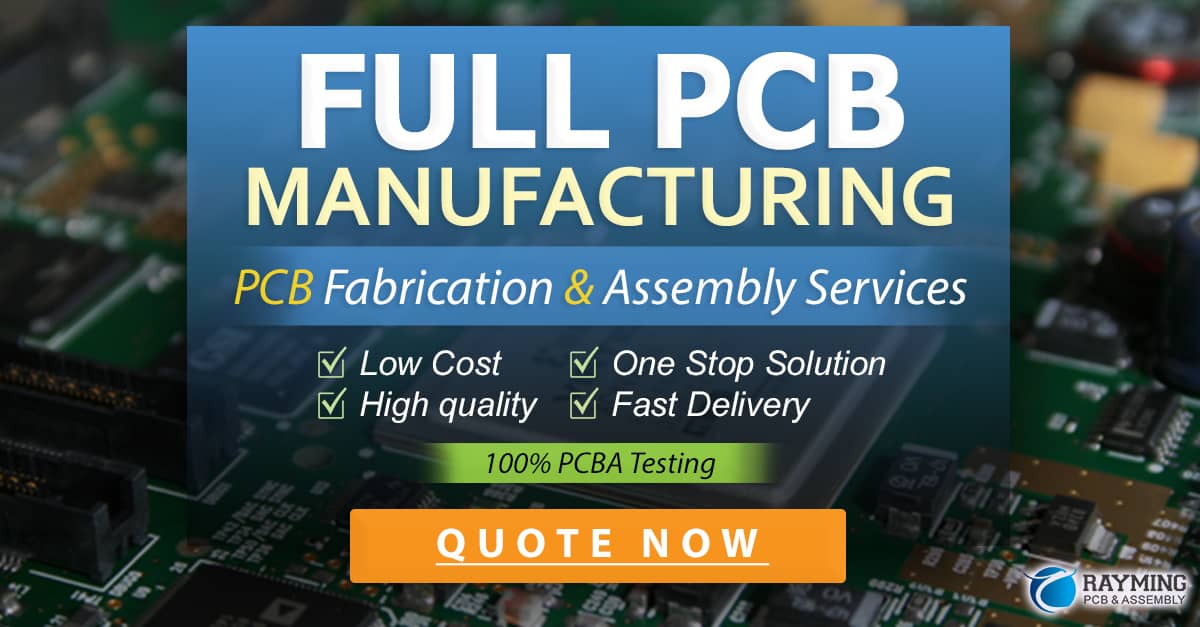
Inspection and Rework
Despite implementing preventive measures, solder bridging can still occur in some cases. Effective inspection and rework processes are crucial for identifying and correcting solder bridging defects.
1. Visual Inspection
Trained operators should visually inspect the PCB assembly for any signs of solder bridging. This can be done using magnification tools or microscopes to examine critical areas such as fine-pitch components or densely populated regions.
2. Automated Optical Inspection (AOI)
AOI systems use high-resolution cameras and advanced image processing algorithms to detect solder bridging and other assembly defects automatically. AOI can quickly scan the entire PCB and identify potential bridging issues, enabling early detection and correction.
3. X-Ray Inspection
For PCBs with hidden or obscured solder joints, such as ball grid array (BGA) packages or chip scale packages (CSPs), X-ray inspection can be used to detect solder bridging. X-ray systems provide a non-destructive means of examining the internal structure of solder joints and identifying bridging defects.
4. Rework and Repair
When solder bridging is detected, rework and repair processes are necessary to correct the defect. This may involve using specialized tools such as soldering irons, desoldering wicks, or hot air rework stations to remove the excess solder and re-soldering the affected components. Proper training and skill are essential for effective rework to avoid further damage to the PCB or components.
Best Practices for Solder Bridging Prevention
To minimize the risk of solder bridging and achieve high-quality PCB assembly, consider the following best practices:
-
Design for Manufacturability (DFM): Collaborate with PCB designers to ensure that the PCB layout is optimized for manufacturability. Consider factors such as pad size, spacing, and solder mask design to reduce the likelihood of solder bridging.
-
Process Control and Monitoring: Implement robust process controls and monitoring systems throughout the PCB assembly process. This includes regular calibration and maintenance of equipment, statistical process control (SPC) techniques, and real-time monitoring of key parameters.
-
Training and Skill Development: Provide comprehensive training to operators and technicians involved in PCB assembly. Ensure they have the necessary skills and knowledge to identify and prevent solder bridging issues.
-
Continuous Improvement: Foster a culture of continuous improvement within the PCB assembly process. Regularly review and analyze solder bridging defect data, identify root causes, and implement corrective actions to prevent recurrence.
-
Supplier Quality Management: Work closely with suppliers to ensure the quality and consistency of materials used in PCB assembly, such as solder paste, stencils, and components. Establish quality agreements and conduct regular audits to maintain supplier performance.
Frequently Asked Questions (FAQ)
- What is the difference between solder bridging and solder balling?
-
Solder bridging occurs when excess solder connects two or more adjacent pads or pins that should not be connected, causing short circuits. Solder balling, on the other hand, refers to the formation of small, spherical solder balls that can detach from the solder joint and cause intermittent or open connections.
-
Can solder bridging be detected through visual inspection alone?
-
While visual inspection can detect some instances of solder bridging, it may not be sufficient for identifying all bridging defects, especially in densely populated or fine-pitch areas. Automated optical inspection (AOI) and X-ray inspection are often used to supplement visual inspection and improve detection accuracy.
-
How can solder bridging be prevented in fine-pitch components?
-
Preventing solder bridging in fine-pitch components requires careful control of the solder paste printing process, accurate component placement, and optimized reflow profiles. Using a stencil with appropriate aperture sizes and shapes, ensuring precise alignment, and maintaining consistent solder paste volume are critical factors.
-
What are the consequences of solder bridging in PCB assembly?
-
Solder bridging can lead to short circuits, causing the electronic device to malfunction or fail entirely. It can also result in reduced manufacturing yields, increased rework costs, and potential reliability issues in the field. Solder bridging can compromise the overall quality and performance of the PCB assembly.
-
How can the effectiveness of solder bridging prevention measures be assessed?
- The effectiveness of solder bridging prevention measures can be assessed through various means, such as:
- Monitoring and analyzing solder bridging defect rates over time
- Conducting regular process audits and inspections
- Implementing statistical process control (SPC) techniques to identify trends and variations
- Gathering feedback from operators and technicians on the effectiveness of implemented measures
- Conducting thorough failure analysis and root cause investigations for any solder bridging incidents
By regularly reviewing and evaluating the effectiveness of prevention measures, continuous improvement efforts can be targeted to further reduce the occurrence of solder bridging in PCB assembly.
Conclusion
Solder bridging is a common and potentially severe defect in PCB assembly that can lead to short circuits, malfunctions, and reduced product quality. Understanding the causes of solder bridging, such as excessive solder paste deposition, improper stencil design, insufficient solder mask clearance, component placement inaccuracies, inadequate reflow profiles, and contamination, is crucial for implementing effective prevention strategies.
To minimize the occurrence of solder bridging, PCB manufacturers should focus on optimizing stencil design, controlling solder paste printing processes, ensuring proper solder mask application, achieving accurate component placement, optimizing reflow profiles, and maintaining cleanliness and contamination control. Regular inspection using visual, AOI, and X-ray techniques, along with skilled rework and repair processes, are essential for identifying and correcting solder bridging defects.
By adopting best practices such as Design for Manufacturability (DFM), process control and monitoring, training and skill development, continuous improvement, and supplier quality management, PCB assembly companies can significantly reduce the risk of solder bridging and improve overall product quality and reliability.
As the electronics industry continues to evolve with miniaturization and increasing complexity, addressing solder bridging challenges remains a critical aspect of PCB assembly. By staying updated with the latest technologies, processes, and best practices, manufacturers can effectively prevent and mitigate solder bridging issues, ensuring the production of high-quality and reliable electronic products.
0 Comments