What are Solder Bridges?
Solder bridges, also known as solder shorts, are unintended connections between two or more conductors on a printed circuit board (PCB) caused by excess solder. These bridges can cause short circuits, leading to malfunctions or complete failure of the electronic device. As PCB designs become more complex and components get smaller, the occurrence of solder bridges during the assembly process has become a significant challenge for manufacturers.
Types of Solder Bridges
There are two main types of solder bridges:
-
Component-to-component bridges: These occur when excess solder connects the leads of adjacent components, creating an unintended electrical connection.
-
Trace-to-trace bridges: These happen when excess solder connects two or more traces (conductive paths) on the PCB, resulting in a short circuit.
Causes of Solder Bridges
Several factors can contribute to the formation of solder bridges during the PCB assembly process:
1. Inadequate Solder Paste Application
One of the most common causes of solder bridges is the improper application of solder paste. If too much solder paste is applied, or if the paste is not evenly distributed, it can lead to excess solder flow and the formation of bridges.
2. Incorrect Stencil Design
Stencils are used to apply solder paste to the PCB pads. If the stencil apertures are too large or if the stencil is not properly aligned with the pads, it can result in excess solder paste deposition and subsequent bridging.
3. Component Placement Issues
Misaligned or improperly seated components can cause their leads to come into contact with adjacent pads or traces, increasing the risk of solder bridges.
4. Reflow Profile Inaccuracies
The reflow soldering process involves heating the PCB assembly to melt the solder paste and form a strong bond between the components and the board. If the reflow profile (temperature and duration) is not optimized, it can lead to excess solder flow and bridging.
5. PCB Design Factors
Certain PCB design factors can increase the likelihood of solder bridges:
- Insufficient pad-to-pad spacing: When the space between pads is too small, it becomes easier for excess solder to bridge the gap.
- High component density: As more components are placed in a smaller area, the risk of solder bridges increases.
- Fine-pitch components: Components with closely spaced leads, such as QFPs and BGAs, are more prone to solder bridging.
Impact of Solder Bridges on PCB Assembly
Solder bridges can have a significant impact on the quality, reliability, and cost of PCB assembly:
1. Functional Failures
Solder bridges create unintended electrical connections, which can cause short circuits, leading to malfunctions or complete failure of the electronic device.
2. Rework and Repair Costs
When solder bridges are detected, they must be repaired, which involves additional labor and materials. Rework can be time-consuming and costly, especially for complex PCB designs.
3. Decreased Yield
The presence of solder bridges reduces the overall yield of the PCB assembly process, as affected boards must be repaired or scrapped.
4. Delayed Time-to-Market
Rework and repairs due to solder bridges can delay the completion of the assembly process, resulting in longer lead times and delayed product releases.
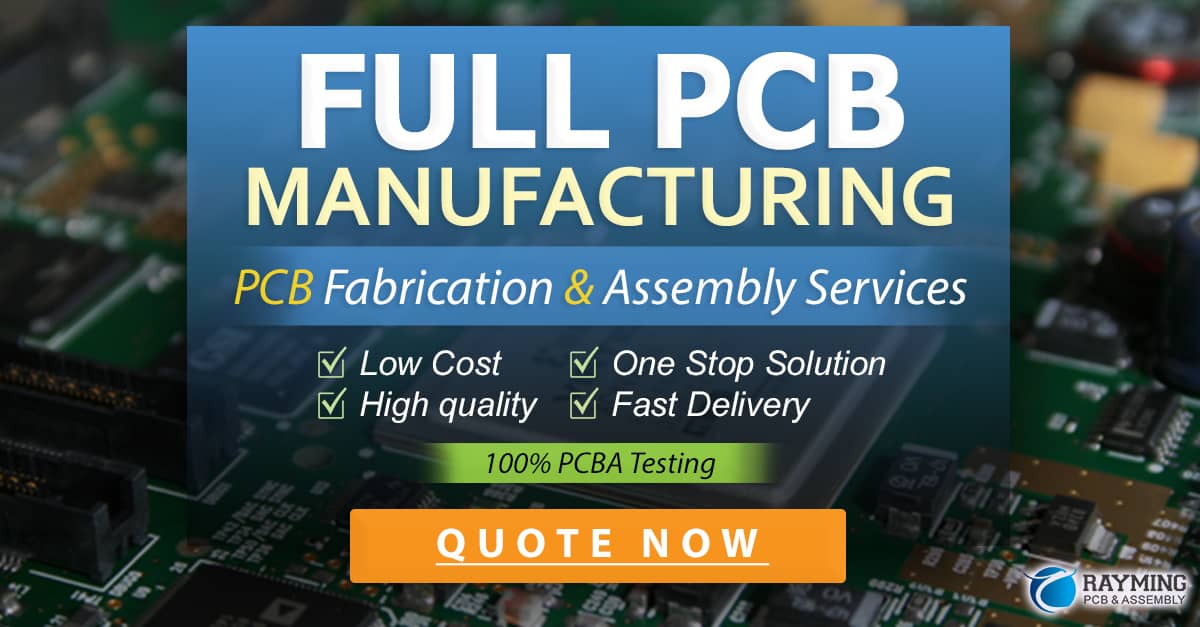
Preventing Solder Bridges in PCB Assembly
To minimize the occurrence of solder bridges, manufacturers can implement several best practices and strategies:
1. Optimize Solder Paste Application
Proper control of solder paste application is crucial for preventing solder bridges. This can be achieved through:
- Stencil design optimization: Ensure that stencil apertures are appropriately sized and positioned to deposit the correct amount of solder paste on each pad.
- Solder paste inspection (SPI): Implement SPI systems to monitor the quality and consistency of solder paste deposition before the reflow process.
- Regular stencil cleaning: Clean stencils regularly to prevent the buildup of solder paste residue, which can cause uneven deposition.
2. Improve Component Placement Accuracy
Accurate component placement is essential for reducing the risk of solder bridges. Manufacturers can:
- Use high-precision pick-and-place machines: Invest in advanced placement equipment that offers high accuracy and repeatability.
- Implement vision systems: Use camera-based vision systems to verify component alignment and positioning before soldering.
- Conduct regular machine maintenance: Ensure that pick-and-place machines are properly calibrated and maintained to maintain placement accuracy.
3. Optimize Reflow Profile
A well-designed reflow profile is critical for minimizing solder bridging. Manufacturers should:
- Conduct reflow profile optimization: Develop and fine-tune reflow profiles based on the specific requirements of the PCB design and components.
- Monitor reflow process parameters: Continuously monitor and control temperature, conveyor speed, and other reflow process variables to ensure consistency.
- Use nitrogen atmosphere: Consider using nitrogen in the reflow oven to reduce oxidation and improve solder joint quality.
4. Enhance PCB Design for Manufacturability (DFM)
Incorporating DFM principles into the PCB design process can help reduce the risk of solder bridges:
- Increase pad-to-pad spacing: Where possible, design PCBs with sufficient spacing between pads to minimize the chance of solder bridging.
- Optimize component selection: Choose components with appropriate lead spacing and packaging to facilitate reliable soldering.
- Use solder masks: Apply solder masks to the PCB to prevent solder from flowing outside the intended areas.
5. Implement Automated Optical Inspection (AOI)
AOI systems can quickly and accurately detect solder bridges after the soldering process. By identifying defects early, manufacturers can initiate timely repairs and prevent defective boards from progressing further in the assembly process.
Solder Bridge Repair Techniques
When solder bridges are detected, they must be repaired to ensure the proper functioning of the electronic device. There are several techniques for repairing solder bridges:
1. Manual Soldering Iron
For small-scale repairs, a manual soldering iron can be used to remove excess solder and break the bridge. This method requires skill and precision to avoid damaging the components or the PCB.
2. Solder Wick
Solder wick, also known as desoldering braid, is a copper braid that can be used to absorb excess solder. The wick is placed over the solder bridge and heated with a soldering iron, allowing the solder to flow into the braid.
3. Specialized Desoldering Tools
Various specialized desoldering tools, such as desoldering tweezers and vacuum desoldering irons, can be used to remove excess solder and repair bridges. These tools offer more control and precision compared to manual methods.
FAQ
1. What is the difference between a solder bridge and a solder short?
A solder bridge and a solder short refer to the same issue – an unintended connection between two or more conductors caused by excess solder. The terms are often used interchangeably.
2. Can solder bridges be detected during the PCB assembly process?
Yes, solder bridges can be detected using automated optical inspection (AOI) systems after the soldering process. AOI systems use cameras and image processing algorithms to identify defects, including solder bridges.
3. How can solder bridges be prevented in high-density PCB designs?
To prevent solder bridges in high-density PCB designs, manufacturers can:
- Optimize solder paste application using appropriate stencil designs and solder paste inspection.
- Ensure accurate component placement with high-precision pick-and-place machines and vision systems.
- Incorporate DFM principles, such as increasing pad-to-pad spacing and selecting components with suitable lead spacing.
4. Can solder bridges cause permanent damage to the PCB or components?
In some cases, solder bridges can cause permanent damage to the PCB or components if they are not detected and repaired promptly. Short circuits caused by solder bridges can lead to overheating, which may damage the PCB substrate, traces, or components.
5. Are there any automated methods for repairing solder bridges?
While there are specialized desoldering tools that can assist in solder bridge repair, the process often requires manual intervention. Automated solder bridge repair systems are not widely used in the industry due to the complexity and variability of the repair process.
Conclusion
Solder bridges have become a significant challenge in PCB assembly as designs become more complex and components get smaller. These unintended connections can cause short circuits, leading to malfunctions, reduced yield, and increased rework costs. To minimize the occurrence of solder bridges, manufacturers must implement best practices in solder paste application, component placement, reflow profile optimization, and PCB design for manufacturability. When solder bridges are detected, prompt repair using appropriate techniques is essential to ensure the proper functioning of the electronic device. By understanding the causes, impact, and prevention strategies for solder bridges, PCB assembly professionals can work towards improving the quality and reliability of their products.
0 Comments