What is an SMT Stencil?
An SMT stencil is a template used to apply solder paste onto the pads of a PCB during the SMT assembly process. The stencil has openings that match the size and location of the pads on the PCB, allowing for precise solder paste deposition. The thickness of the stencil determines the amount of solder paste applied, which is critical for forming reliable solder joints.
Why Are SMT Stencils Essential?
SMT stencils are essential for several reasons:
-
Precise solder paste application: Stencils ensure that the correct amount of solder paste is applied to each pad, resulting in consistent and reliable solder joints.
-
Improved efficiency: Using a stencil is much faster and more efficient than applying solder paste manually, especially for high-volume production.
-
Reduced defects: Stencils minimize the risk of solder bridging, insufficient solder, or other defects that can occur with manual solder paste application.
-
Compatibility with fine-pitch components: As electronic components become smaller and more complex, stencils enable the accurate application of solder paste on fine-pitch pads.
Types of SMT Stencils
There are several types of SMT stencils available, each with its own advantages and disadvantages.
Laser-Cut Stencils
Laser-cut stencils are created using a high-precision laser to cut the apertures into the stencil material. This process allows for extremely accurate and consistent aperture sizes and shapes. Laser-cut stencils are ideal for high-volume production and applications requiring tight tolerances.
Advantages:
– High precision and accuracy
– Consistent aperture sizes and shapes
– Suitable for fine-pitch components
– Durable and long-lasting
Disadvantages:
– Higher cost compared to other stencil types
– Longer lead times for production
Electroformed Stencils
Electroformed stencils are made by electroplating nickel onto a photoresist-patterned substrate. This process creates a thin, yet durable stencil with smooth aperture walls. Electroformed stencils are well-suited for applications requiring very fine features or intricate designs.
Advantages:
– Excellent for fine-pitch components and intricate designs
– Smooth aperture walls for improved solder paste release
– Thin and lightweight
Disadvantages:
– Higher cost compared to laser-cut stencils
– Limited thickness options
– Longer lead times for production
Chemical-Etched Stencils
Chemical-etched stencils are produced by chemically etching the apertures into the stencil material. This process is less precise than laser cutting or electroforming but offers a more affordable option for less demanding applications.
Advantages:
– Lower cost compared to laser-cut and electroformed stencils
– Faster production times
– Suitable for less demanding applications
Disadvantages:
– Lower precision and accuracy compared to other stencil types
– Not ideal for fine-pitch components or intricate designs
– Aperture walls may not be as smooth, affecting solder paste release
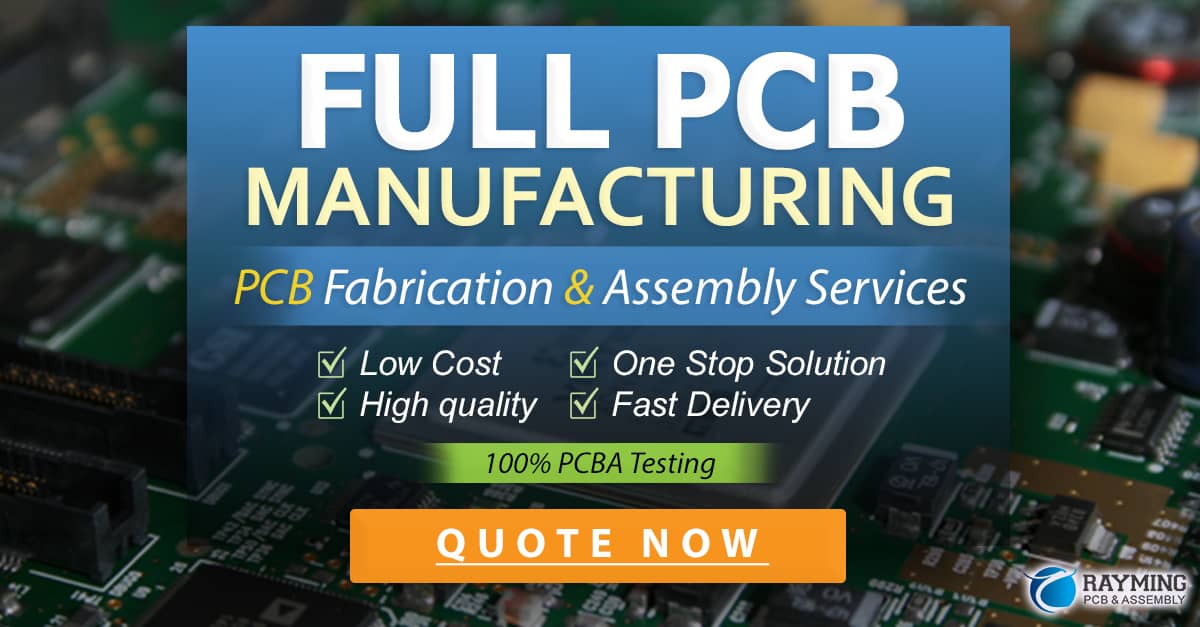
Choosing the Right SMT Stencil
When selecting an SMT stencil for your manufacturing needs, consider the following factors:
-
PCB design: Evaluate the complexity of your PCB design, including the size and pitch of the components, to determine the required stencil type and thickness.
-
Solder paste properties: Consider the viscosity and particle size of the solder paste you will be using, as this can affect the stencil aperture design and thickness.
-
Production volume: Higher production volumes may justify investing in a more precise and durable stencil, such as a laser-cut or electroformed stencil.
-
Budget: Assess your budget constraints and weigh the cost of the stencil against the potential benefits in terms of efficiency, accuracy, and defect reduction.
Stencil Thickness
Stencil thickness is a critical factor in determining the amount of solder paste deposited on the PCB pads. The optimal stencil thickness depends on several factors, including the size and pitch of the components, the solder paste properties, and the desired solder joint profile.
Typical stencil thicknesses range from 0.1 mm to 0.2 mm (4-8 mils), with thinner stencils used for smaller components and finer pitches. Thicker stencils are used for larger components or when a higher solder paste volume is required.
Component Pitch | Recommended Stencil Thickness |
---|---|
> 0.65 mm | 0.15 – 0.2 mm (6-8 mils) |
0.5 – 0.65 mm | 0.125 – 0.15 mm (5-6 mils) |
0.4 – 0.5 mm | 0.1 – 0.125 mm (4-5 mils) |
< 0.4 mm | 0.08 – 0.1 mm (3-4 mils) |
Stencil Aperture Design
The design of the stencil apertures is crucial for ensuring the proper solder paste deposition and release. Aperture dimensions should be optimized based on the PCB pad size, solder paste properties, and desired solder joint profile.
Some common aperture design guidelines include:
- Aperture width: 1:1 ratio with the PCB pad width
- Aperture length: 1:1 ratio with the PCB pad length, or slightly shorter to prevent bridging
- Aperture shape: Rectangular for most applications, but circular or oblong shapes may be used for specific requirements
In addition to aperture dimensions, other design factors to consider include:
- Aperture wall angle: A slight taper (5-15 degrees) can improve solder paste release
- Aperture corner radius: Rounded corners can help prevent solder paste from sticking to the aperture walls
- Fiducial marks: Including fiducial marks on the stencil can aid in alignment during the assembly process
Stencil Maintenance and Cleaning
Proper maintenance and cleaning of your SMT stencil are essential for ensuring consistent solder paste deposition and extending the stencil’s life. Regular cleaning helps prevent solder paste buildup, clogging of apertures, and contamination of the PCB.
Some best practices for stencil maintenance and cleaning include:
-
Underside cleaning: Clean the underside of the stencil after every print cycle using a lint-free wipe and a suitable solvent.
-
Periodic deep cleaning: Perform a thorough cleaning of the stencil at regular intervals, using a stencil cleaning solution and a soft brush to remove any stubborn residue.
-
Storage: Store the stencil in a protective container when not in use to prevent damage and contamination.
-
Inspection: Regularly inspect the stencil for signs of wear, damage, or clogged apertures, and replace or repair the stencil as needed.
Frequently Asked Questions (FAQ)
1. How often should I replace my SMT stencil?
The lifespan of an SMT stencil depends on various factors, such as the stencil material, usage frequency, and maintenance practices. Generally, a well-maintained stencil can last for several thousand print cycles. However, it’s essential to regularly inspect the stencil for signs of wear, damage, or clogged apertures and replace it as needed to maintain print quality.
2. Can I use the same SMT stencil for different PCB designs?
While it is possible to use the same stencil for different PCB designs with similar pad sizes and layouts, it’s generally recommended to use a dedicated stencil for each design. This ensures optimal solder paste deposition and reduces the risk of defects caused by incompatible aperture sizes or layouts.
3. How do I store my SMT stencil when not in use?
To prevent damage and contamination, store your SMT stencil in a protective container when not in use. The container should be clean, dry, and free from dust or debris. Avoid storing the stencil in areas with high humidity or extreme temperatures, as this can cause warping or corrosion.
4. What is the best way to clean an SMT stencil?
The best way to clean an SMT stencil is to use a combination of regular underside cleaning and periodic deep cleaning. For underside cleaning, use a lint-free wipe and a suitable solvent to remove solder paste residue after every print cycle. For deep cleaning, use a stencil cleaning solution and a soft brush to remove stubborn residue, followed by a thorough rinse with deionized water and drying with a lint-free cloth.
5. Can I reuse solder paste that has been removed from the stencil during cleaning?
No, it is not recommended to reuse solder paste that has been removed from the stencil during cleaning. The solder paste may have been contaminated during the printing process or exposed to air for an extended period, which can affect its properties and performance. Always use fresh solder paste for each print cycle to ensure the best results.
Conclusion
SMT stencils are a critical component in the surface mount technology assembly process, ensuring precise and consistent solder paste application. By understanding the types of stencils available, their advantages and disadvantages, and the factors to consider when choosing a stencil, you can optimize your SMT assembly process for efficiency, accuracy, and reliability.
Proper stencil maintenance and cleaning are also essential for prolonging the life of your stencil and maintaining high-quality solder paste deposition. By following best practices for stencil care and regularly inspecting your stencil for signs of wear or damage, you can minimize defects and ensure the long-term success of your SMT assembly process.
0 Comments