Surface mount technology (SMT) has revolutionized the electronics manufacturing industry. With SMT, components are mounted directly onto the surface of printed circuit boards (PCBs) rather than through holes in the board. This allows for miniaturization and automation of the assembly process. One of the most critical tools in SMT assembly is the stencil used to apply solder paste to the PCB pads. Selecting the right SMT stencil manufacturer is key for producing high-quality boards efficiently. This guide will examine what to look for when choosing an SMT stencil maker.
What is an SMT Stencil?
An SMT stencil is a thin metal sheet, usually made of stainless steel, laser cut with apertures matching the pads of the PCB. During assembly, the stencil is placed over the board and solder paste is applied across it using a squeegee. The solder paste deposits through the openings onto the pads on the PCB. After stencil printing, the components can be placed and will adhere to the board due to the tackiness of the paste. The board then passes through a reflow oven melting the paste to form solder joints.
The stencil apertures must be precisely cut to match the circuit board layout. Any discrepancies will impact paste deposition and ultimately soldering quality. Stencils usually range from 3 mils to 8 mils thick. Laser cutting and electroforming are common methods for patterning stencil apertures.
Stencil Design Considerations
Several factors go into engineering SMT stencils:
- Aperture dimensions – The openings must match PCB pad sizes and positions accurately. This requires precision in stencil manufacturing.
- Aperture walls – The edge walls impact paste release. Rounded walls aid release while straight walls provide cleaner printing.
- Stencil thickness – Thicker stencils give a larger paste volume but lower print resolution. Thinner stencils provide fine features but less paste capacity. 4-6 mils is typical.
- Alloy selection – Stainless steel offers durability for high volume production. Nickel allows easier cleaning of dried paste.
- Stencil tensioning – Applying tension prevents warping and aids particle release.
- Surface coatings – Coatings like titanium nitride improve paste release and extend stencil life.
Matching the stencil design to the application is vital for maximizing print quality, yield, and throughput. This is where working with an experienced SMT stencil provider is beneficial.
Key SMT Stencil Manufacturing Capabilities
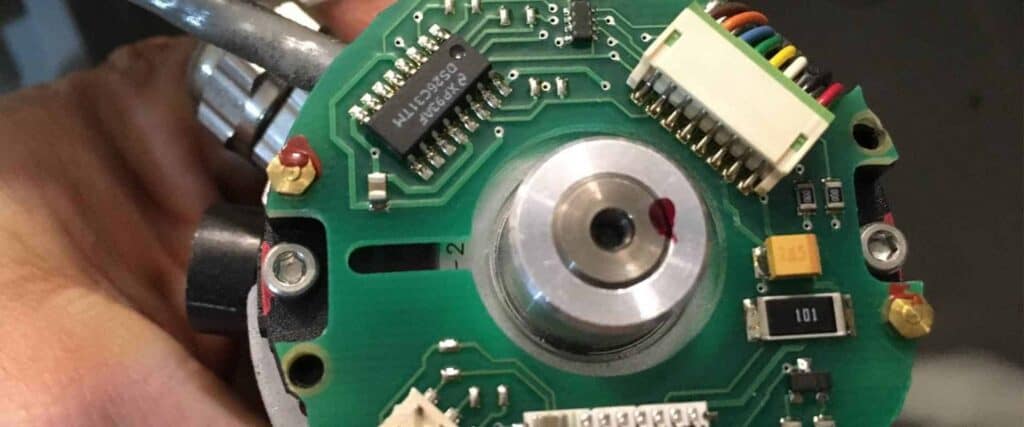
Printed circuit board assembly relies on receiving defect-free stencils designed for the application. Here are key capabilities to look for in an SMT stencil manufacturer:
- Precision laser cutting – This achieves accurate, repeatable aperture geometries in the micron range. Photochemical etching has limits around 125 microns.
- Automated inspection – Automated optical inspection ensures accuracy of aperture positions/dimensions. This inspection should integrate with statistical process control.
- Cleanroom assembly – Stencils require assembly in a clean environment to prevent defects. ISO Class 5 cleanrooms are suitable.
- Surface treatments – Treatments like electropolishing and coatings improve stencil performance and durability.
- Rapid prototyping – Fast fabrication of prototype stencils enables design verification prior to full production.
- Short lead times – Manufacturers with quick turnaround reduce delays during product development and new product introduction.
- Design for manufacturability – Experienced engineers can assess stencil designs for potential manufacturability issues. This prevents problems.
- Responsive customer support – Selecting a vendor that provides feedback on stencil designs and is easy to contact eliminates headaches.
These advanced capabilities allow SMT stencil manufacturers to deliver maximum quality and process control for their customers.
Key Factors in Selecting an SMT Stencil Manufacturer
Choosing the right partner for SMT stencil manufacturing has a major influence on printed circuit board assembly quality and efficiency. Here are key factors to consider in selecting a vendor:
Quality Systems
Look for robust quality systems including ISO 9001 certification, well-defined manufacturing and inspection procedures, quality metrics monitoring, and attention to continuous improvement. This brings consistency.
Technical Expertise
Select a vendor with experience in microelectronics assembly and familiarity with SMT stencil design tradeoffs. Their expertise can optimize stencil performance.
Precision Manufacturing
Precision laser cutters, tensioning equipment, cleanrooms, and automated inspection tools ensure accuracy and repeatability. Ask about their capabilities.
Customer Service
The right supplier will have responsive account management, engineering assistance, rapid prototyping, and short lead times. This facilitates collaboration.
Reliability
On-time delivery of stencils according to specifications is critical. Examine suppliers’ track records for consistently meeting commitments.
Cost Effectiveness
Although initial cost is important, consider total value including quality, yield, delivery, and service. The right supplier provides value.
Factor | Description |
---|---|
Quality Systems | Robust procedures and metrics for consistent performance |
Technical Expertise | Knowledge to optimize stencil designs |
Precision Manufacturing | Advanced tools ensure accuracy and repeatability |
Customer Service | Responsiveness and collaboration |
Reliability | Proven record of on-time delivery |
Cost Effectiveness | Total value not just initial cost |
Selecting an SMT stencil provider with strengths across these areas will pay dividends for PCB assembly success.
FAQ
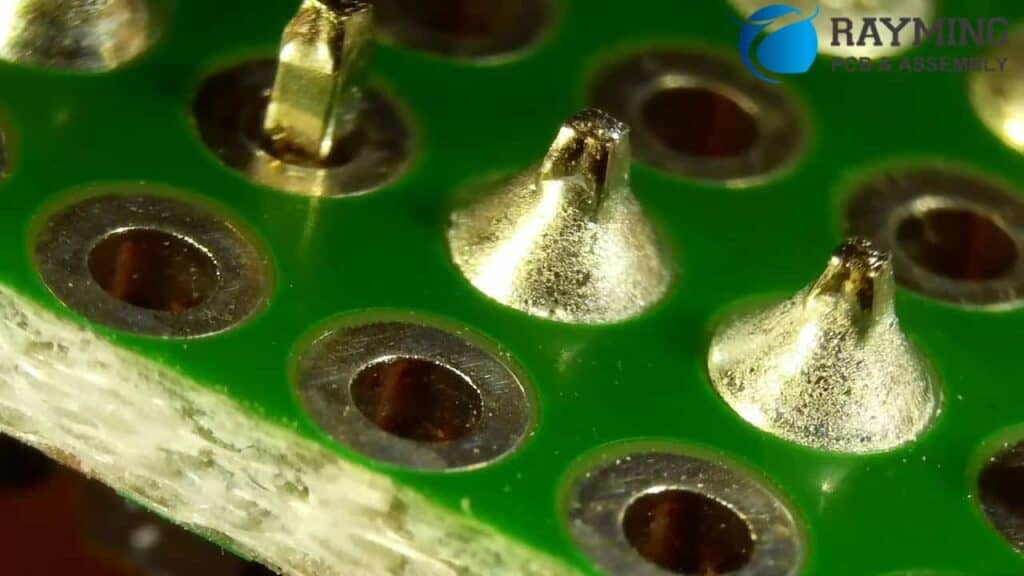
Here are some frequently asked questions about SMT stencils and working with SMT stencil manufacturers:
What are some common SMT stencil defects?
Common stencil defects include:
- Inaccurate aperture dimensions
- Poor aperture wall quality (e.g. burrs or jagged edges)
- Dents, nicks, or scratches
- Pits or voids in the stencil surface
- Bowing or warping
- Smearing or clogging of apertures with particle contamination
- Misregistration of apertures to fiducials
How long do SMT stencils last?
With proper care an SMT stencil can last 1-2 years and over 100 print cycles. Key factors impacting life include:
- Stencil thickness – thicker is longer lasting
- Stencil alloy – nickel better than steel
- Aperture dimensions – larger openings endure longer
- Surface coatings – treatments like titanium nitride extend lifespan
- Cleaning methods – excessive abrasion shortens life
What is the typical lead time for SMT stencils?
For standard designs, most manufacturers can deliver in 5-10 business days. For complex designs or prototype volumes, 10-15 days is common. Expedited 24-48 hour service may be possible but typically costs more.
Should SMT stencils be cleaned after every print?
Light wiping is sufficient after most prints. More thorough cleaning is recommended every 5-20 prints depending on factors like aperture size. Excessive cleaning can damage stencils. Work with your stencil maker on optimal cycle times.
What are recommended SMT stencil handling procedures?
- Use lint-free gloves when handling to prevent skin oils and particulates
- Avoid placing stencils on hard surfaces to prevent scratches
- Store in protective packaging in a clean, climate controlled area
- Apply tensioning during storage and use to prevent warping
- Use stencil wiping pads not abrasive wipes for gentle cleaning
Following these simple procedures will extend the life of SMT stencils and maintain print quality.
In summary, the SMT stencil is a crucial component enabling automated printed circuit board assembly. Partnering with the right stencil manufacturer that provides high precision, quality control, rapid prototyping, and responsive collaboration will ensure you consistently receive defect-free stencils optimized for your process. This in turn will maximize yields, quality, and productivity for your surface mount printed circuit board manufacturing.
0 Comments