Surface mount technology (SMT) is a method for assembling printed circuit boards (PCBs) by mounting electronic components directly onto the surface of the PCB. This process has largely replaced the older through-hole technology and has enabled greater miniaturization and density of electronic circuitry.
In SMT PCB assembly, components are placed onto pads or lands on the PCB surface and soldered into place using solder paste and reflow or wave soldering techniques. SMT components are typically much smaller and have leads or terminations designed for surface mounting rather than through-hole mounting.
SMT Component Types
There are several common types of surface mount components:
Passive Components
- Resistors – Used to limit or resist current flow
- Capacitors – Store and release electrical charge
- Inductors – Used to store energy in magnetic fields
Active Components
- Integrated Circuits (ICs) – Combine multiple transistors and other components in a small package
- Transistors – Semiconductor devices used for amplifying or switching electronic signals
Component | Description |
---|---|
Resistors | Limit current flow |
Capacitors | Store electrical charge |
Inductors | Store energy in magnetic fields |
Integrated Circuits (ICs) | Combine multiple electronic components |
Transistors | Amplify or switch electronic signals |
Other Components
- Diodes – Allow current flow in one direction only
- LEDs – Light emitting diodes that produce light
- Crystals, oscillators – Provide a clock signal/timing reference
- Sensors, MEMS – Detect physical properties like motion, pressure, etc
- Connectors – Allow detachable electrical connections
SMT Assembly Process Steps
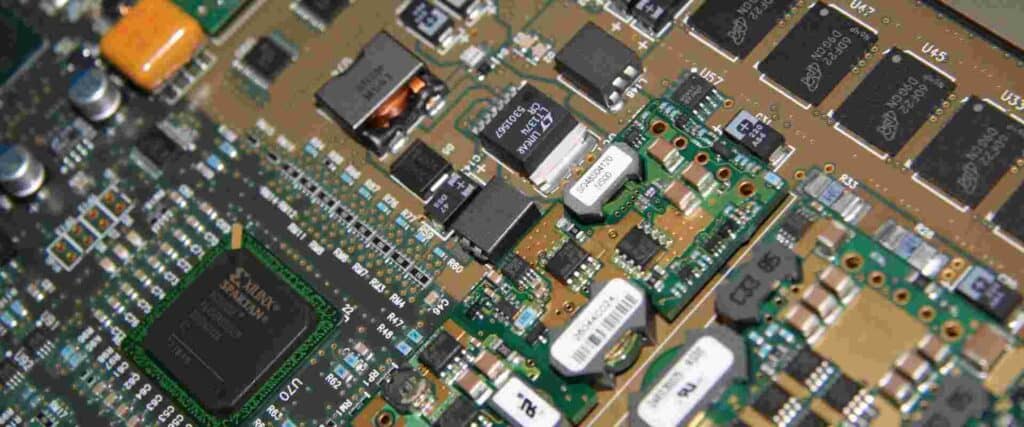
The surface mount assembly process consists of the following key stages:
1. PCB Fabrication
The bare PCB is fabricated with copper traces and pads for mounting the components. The PCB substrate is usually FR-4 fiberglass material.
2. Solder Paste Application
Solder paste containing powdered solder and flux is applied to the PCB pads using stenciling or screen printing. This deposits small amounts of solder paste where components will be placed.
3. SMT Component Placement
SMT components are precisely placed onto the solder paste deposits on the PCB using automated pick and place machines. Feeders supply components to the pick and place heads.
4. Solder Reflow
The populated PCB passes through a reflow oven with heat zones. The solder paste melts, fusing components to pads.
5. Cleaning
Any residual flux is cleaned from the PCB using solutions/cleaners. This removes contamination and increases long term reliability.
6. Inspection and Testing
PCBs are visually inspected and electrically tested to verify proper assembly and functionality without defects. Rework may be done if needed.
7. Conformal Coating
A protective polymer coating may be applied to shield the assembled PCB from moisture, dust, chemicals.
SMT Assembly Equipment
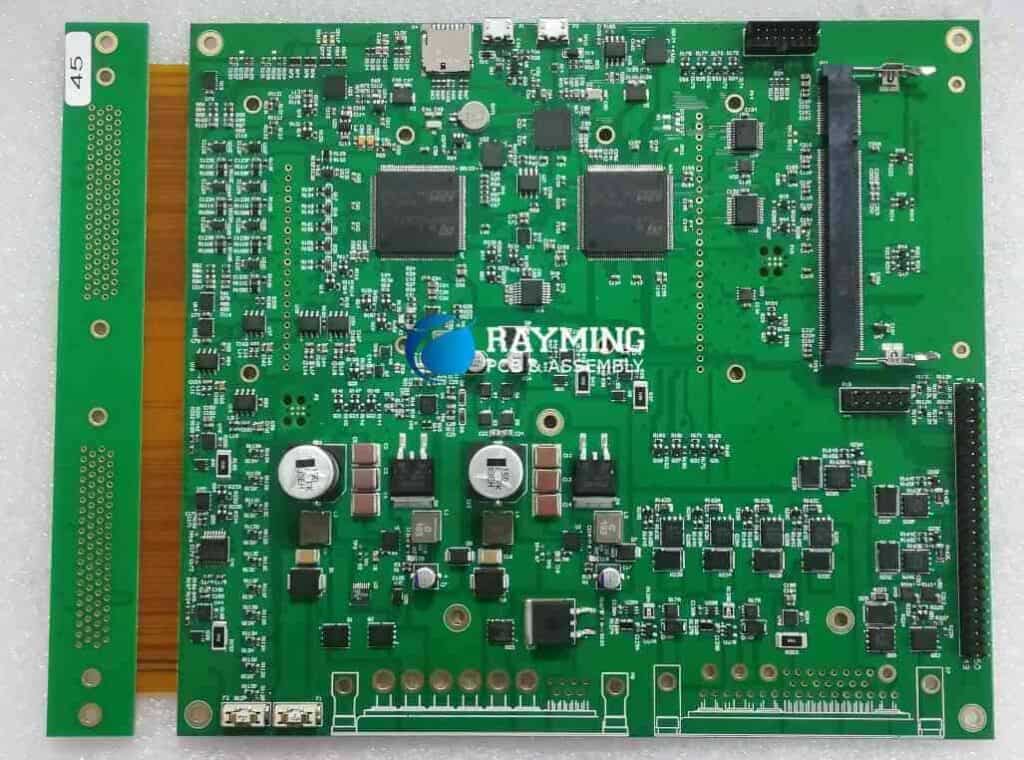
Specialized equipment is used throughout the SMT assembly process:
- Solder Paste Printer – Deposits solder paste on PCB pads
- Pick and Place Machine – Automates component placement onto PCB
- Reflow Oven – Heats solder paste deposits to attach components
- AOI (Automated Optical Inspection) – Imaging system to visualize PCB assembly and identify defects
- In-Circuit Tester – Tests electrical connectivity and function after assembly
- Conformal Coating Machine – Dispenses and cures coating on assembled PCB
Advantages of SMT
Surface mount technology provides a number of benefits over through-hole PCB assembly:
- Smaller size – SMT components take up less space allowing greater PCB miniaturization
- Lower weight – Less material is needed for SMT components and PCBs
- Increased reliability – SMT process automation reduces human errors
- Higher density – More components can be placed closer together on a PCB
- Improved performance – Smaller lead lengths provide better electrical performance
Challenges of SMT
However, SMT also introduces some challenges:
- More expensive – SMT equipment and small components are costlier
- Repair difficulties – SMT components are harder to remove and replace
- Higher process temperatures – Reflow soldering requires heat management
- Tombstoning – Components can stand up during soldering if paste deposits are off-center
- More process steps – SMT is more complex with pad printing, pick and place, reflow, etc.
Frequently Asked Questions
What are the key benefits of SMT?
The main benefits of surface mount technology are increased miniaturization and density of circuitry, lower weight, improved performance, and higher reliability and repeatability when using automated assembly equipment.
How does SMT compare to through-hole PCB assembly?
SMT allows much smaller components and lead lengths, enabling greater miniaturization. It also utilizes automation for assembly, unlike manual through-hole assembly. However, SMT can require more expensive startup costs for equipment.
What types of components are used in SMT?
Common SMT component types include passive components like resistors, capacitors and inductors as well as active components like ICs and transistors. Other SMT components include diodes, LEDs, connectors, sensors and crystals/oscillators.
What is the function of solder paste in SMT assembly?
Solder paste contains powdered solder alloy and flux. It is printed onto PCB pads through stencils before component placement. During reflow soldering, the paste melts to electrically and mechanically connect the components.
How are components placed onto PCBs in SMT assembly?
Automated pick and place machines use suction heads to precisely pick components from feeders and position them onto solder paste deposits on the PCB surface. This enables very rapid and accurate component placement.
0 Comments