Introduction to Rigid-flex PCBs
Rigid-flex PCBs are a unique type of printed circuit board that combines the benefits of both rigid and flexible circuits. These boards consist of multiple layers of flexible and rigid substrates that are laminated together to form a single, integrated circuit. The flexible portions of the board allow for bending and folding, while the rigid areas provide structural support and stability.
Rigid-flex PCBs offer several advantages over traditional rigid boards, including:
- Improved reliability and durability
- Reduced size and weight
- Enhanced electrical performance
- Increased design flexibility
Applications of Rigid-flex PCBs
Rigid-flex PCBs are used in a wide range of industries and applications, including:
- Aerospace and defense
- Medical devices
- Consumer electronics
- Automotive systems
- Industrial automation
The ability to bend and fold the flexible portions of the board makes rigid-flex PCBs ideal for applications where space is limited or where the board needs to conform to a specific shape or contour.
Rigid-flex PCB Manufacturing Process
The manufacturing process for rigid-flex PCBs is more complex than that of traditional rigid boards. It involves several key steps, including:
- Design and layout
- Material selection
- Fabrication
- Lamination
- Drilling and routing
- Plating and etching
- Solder mask application
- Surface finish application
- Electrical testing
- Singulation and packaging
Design and Layout
The design and layout of a rigid-flex PCB is critical to its performance and reliability. Designers must carefully consider the placement of components, the routing of traces, and the location of the flexible and rigid portions of the board. They must also take into account the mechanical stresses that the board will be subjected to during use.
Material Selection
The materials used in rigid-flex PCBs must be carefully selected to ensure the board’s performance and reliability. The flexible portions of the board typically use polyimide or other flexible substrates, while the rigid portions use standard PCB materials such as FR-4.
Fabrication
The fabrication of rigid-flex PCBs involves creating the individual layers of the board, including the flexible and rigid substrates, copper traces, and other features. This is typically done using a combination of photolithography and etching processes.
Lamination
Once the individual layers of the board have been fabricated, they are laminated together using heat and pressure. This process bonds the layers together and creates a single, integrated circuit.
Drilling and Routing
After lamination, the board is drilled and routed to create the necessary holes and cutouts for components and connectors. This is typically done using CNC machines or laser drilling equipment.
Plating and Etching
The drilled and routed board is then plated with copper to create the electrical connections between layers. This is followed by an etching process to remove the unwanted copper and create the final circuit pattern.
Solder Mask Application
A solder mask is applied to the board to protect the copper traces and prevent short circuits. The solder mask is typically a green or other colored polymer that is applied using a screen printing process.
Surface Finish Application
A surface finish, such as gold or silver, is applied to the exposed copper areas of the board to prevent oxidation and improve solderability. The surface finish also provides a protective layer that enhances the durability of the board.
Electrical Testing
After the board has been fabricated and assembled, it undergoes extensive electrical testing to ensure that it meets the required specifications and performance standards. This includes testing for continuity, insulation resistance, and other key parameters.
Singulation and Packaging
Finally, the board is singulated (cut into individual pieces) and packaged for shipment to the customer. The packaging must be designed to protect the board from damage during shipping and handling.
Choosing a Rigid-flex PCB Manufacturer
When choosing a rigid-flex PCB manufacturer, there are several key factors to consider, including:
- Experience and expertise
- Quality and reliability
- Capacity and lead times
- Cost and pricing
- Customer service and support
Experience and Expertise
It is important to choose a manufacturer with significant experience and expertise in rigid-flex PCB fabrication. Look for a company that has been in business for several years and has a proven track record of success.
Quality and Reliability
Quality and reliability are critical in rigid-flex PCBs, particularly in high-reliability applications such as aerospace and defense. Look for a manufacturer that has robust quality control processes in place and can provide detailed documentation and traceability.
Capacity and Lead Times
Consider the manufacturer’s production capacity and lead times to ensure that they can meet your needs. Look for a company that has sufficient capacity to handle your order volume and can deliver your boards on time.
Cost and Pricing
Cost is always a consideration when choosing a PCB manufacturer. Look for a company that offers competitive pricing without compromising on quality or reliability.
Customer Service and Support
Finally, consider the level of customer service and support provided by the manufacturer. Look for a company that is responsive to your needs and can provide technical support and assistance throughout the design and manufacturing process.
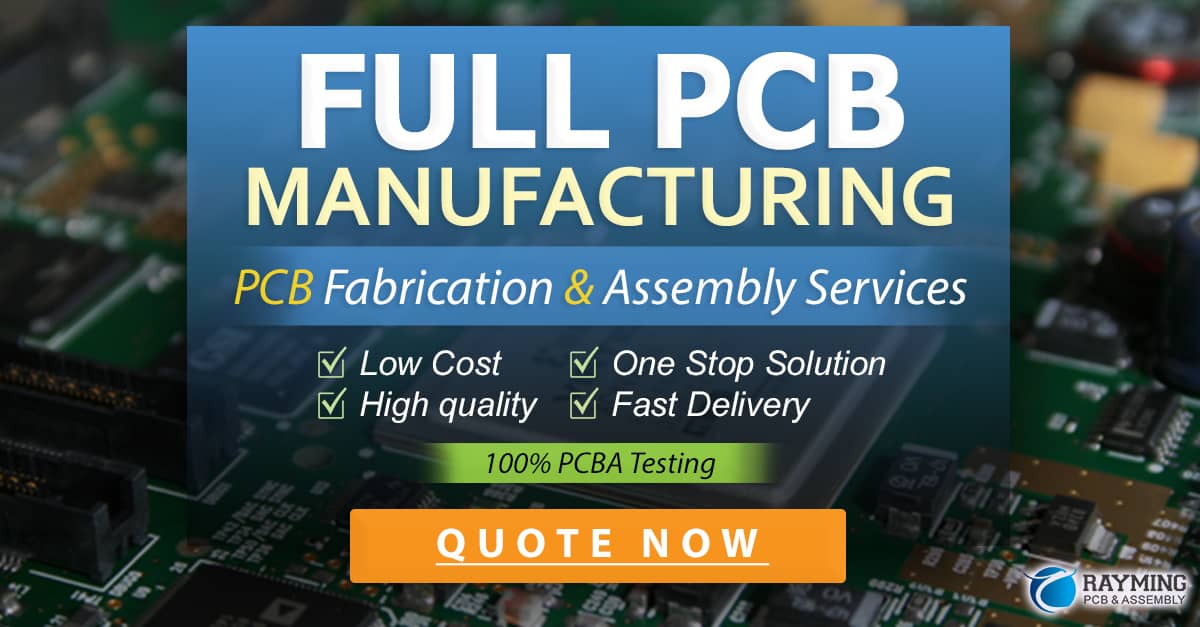
Top Rigid-flex PCB Manufacturers
There are many rigid-flex PCB manufacturers and fabricators around the world, each with their own strengths and capabilities. Here are some of the top manufacturers in the industry:
Manufacturer | Location | Capabilities |
---|---|---|
Flex PCB | USA | Rigid-flex, flex, and rigid PCBs |
Printed Circuits | USA | Rigid-flex, flex, and rigid PCBs |
Cicor Group | Switzerland | Rigid-flex, flex, and rigid PCBs |
Eltek | Israel | Rigid-flex, flex, and rigid PCBs |
Flexible Circuit Technologies | USA | Rigid-flex and flex PCBs |
Flexcom | Taiwan | Rigid-flex, flex, and rigid PCBs |
MFLEX | USA | Rigid-flex and flex PCBs |
Nippon Mektron | Japan | Rigid-flex, flex, and rigid PCBs |
TTM Technologies | USA | Rigid-flex, flex, and rigid PCBs |
Unimicron | Taiwan | Rigid-flex, flex, and rigid PCBs |
These manufacturers offer a range of capabilities and services, from design and prototyping to full-scale production and assembly. They serve customers in a variety of industries, including aerospace, defense, medical, automotive, and consumer electronics.
Rigid-flex PCB Design Considerations
Designing a rigid-flex PCB requires careful consideration of several key factors, including:
- Bend radius and flexibility
- Layer stack-up and materials
- Copper weights and trace widths
- Via placement and design
- Component placement and orientation
- Mechanical stress and strain
Bend Radius and Flexibility
The bend radius and flexibility of the flexible portions of the board must be carefully considered to ensure that the board can withstand the mechanical stresses of bending and folding without damage. The minimum bend radius is typically determined by the thickness and material of the flexible substrate.
Layer Stack-up and Materials
The layer stack-up and materials used in the board must be carefully selected to ensure the board’s electrical and mechanical performance. The flexible portions of the board typically use polyimide or other flexible substrates, while the rigid portions use standard PCB materials such as FR-4.
Copper Weights and Trace Widths
The copper weights and trace widths used in the board must be carefully selected to ensure the board’s electrical performance and manufacturability. Thicker copper weights and wider trace widths can improve the board’s current carrying capacity and reduce resistance, but may also increase the board’s thickness and reduce its flexibility.
Via Placement and Design
The placement and design of vias in the board must be carefully considered to ensure the board’s electrical and mechanical performance. Vias that pass through the flexible portions of the board must be designed to withstand the mechanical stresses of bending and folding without damage.
Component Placement and Orientation
The placement and orientation of components on the board must be carefully considered to ensure the board’s electrical and mechanical performance. Components should be placed in areas of the board that are subject to minimal mechanical stress and strain, and should be oriented to minimize the risk of damage during bending and folding.
Mechanical Stress and Strain
The mechanical stress and strain on the board must be carefully considered to ensure the board’s reliability and durability. The board must be designed to withstand the mechanical stresses of bending, folding, and twisting without damage or failure.
Rigid-flex PCB Testing and Inspection
Rigid-flex PCBs must undergo extensive testing and inspection to ensure their quality, reliability, and performance. Some of the key tests and inspections include:
- Visual inspection
- Continuity testing
- Insulation resistance testing
- Impedance testing
- Flexing and bending tests
- Thermal cycling tests
- Microsectioning analysis
Visual Inspection
Visual inspection is typically the first step in the testing and inspection process. The board is examined under magnification to identify any obvious defects or irregularities, such as scratches, dents, or discoloration.
Continuity Testing
Continuity testing is used to verify that all the electrical connections on the board are intact and functioning properly. This is typically done using a multimeter or other continuity tester.
Insulation Resistance Testing
Insulation resistance testing is used to verify that there are no short circuits or other electrical faults on the board. This is typically done using a high-voltage tester that applies a voltage across the board and measures the resistance between different points.
Impedance Testing
Impedance testing is used to verify that the impedance of the traces on the board meets the required specifications. This is important for high-speed signals and other applications where impedance matching is critical.
Flexing and Bending Tests
Flexing and bending tests are used to verify that the board can withstand the mechanical stresses of bending and folding without damage or failure. The board is subjected to repeated bending and folding cycles to simulate real-world use conditions.
Thermal Cycling Tests
Thermal cycling tests are used to verify that the board can withstand the thermal stresses of temperature changes without damage or failure. The board is subjected to repeated heating and cooling cycles to simulate real-world use conditions.
Microsectioning Analysis
Microsectioning analysis is used to examine the internal structure of the board and verify that it meets the required specifications. A cross-section of the board is cut and polished, and then examined under a microscope to check for defects or irregularities.
Frequently Asked Questions (FAQ)
- What is a rigid-flex PCB?
-
A rigid-flex PCB is a type of printed circuit board that combines rigid and flexible substrates to create a single, integrated circuit. The flexible portions of the board allow for bending and folding, while the rigid portions provide structural support and stability.
-
What are the advantages of using a rigid-flex PCB?
-
Rigid-flex PCBs offer several advantages over traditional rigid boards, including improved reliability and durability, reduced size and weight, enhanced electrical performance, and increased design flexibility.
-
What industries use rigid-flex PCBs?
-
Rigid-flex PCBs are used in a wide range of industries, including aerospace and defense, medical devices, consumer electronics, automotive systems, and industrial automation.
-
How are rigid-flex PCBs manufactured?
-
The manufacturing process for rigid-flex PCBs involves several key steps, including design and layout, material selection, fabrication, lamination, drilling and routing, plating and etching, solder mask application, surface finish application, electrical testing, and singulation and packaging.
-
What should I consider when choosing a rigid-flex PCB manufacturer?
- When choosing a rigid-flex PCB manufacturer, consider factors such as experience and expertise, quality and reliability, capacity and lead times, cost and pricing, and customer service and support.
Conclusion
Rigid-flex PCBs offer a unique combination of flexibility and stability that makes them ideal for a wide range of applications. By combining the benefits of both rigid and flexible circuits, rigid-flex PCBs can provide improved reliability, reduced size and weight, enhanced electrical performance, and increased design flexibility.
When designing and manufacturing rigid-flex PCBs, careful consideration must be given to factors such as bend radius and flexibility, layer stack-up and materials, copper weights and trace widths, via placement and design, component placement and orientation, and mechanical stress and strain.
Choosing the right rigid-flex PCB manufacturer is critical to ensuring the quality, reliability, and performance of your boards. Look for a manufacturer with significant experience and expertise, robust quality control processes, sufficient production capacity, competitive pricing, and excellent customer service and support.
By understanding the key considerations and best practices for rigid-flex PCB design and manufacturing, you can ensure that your boards meet the highest standards of quality, reliability, and performance.
0 Comments