What is an RF PCB?
An RF PCB, or Radio Frequency Printed Circuit Board, is a specialized type of circuit board designed to work with high-frequency signals. These PCBs are used in various applications, such as wireless communication devices, radar systems, and satellite equipment. RF PCBs require specific design considerations and manufacturing techniques to ensure optimal performance and signal integrity.
Key Features of RF PCBs
- High-frequency operation
- Controlled impedance
- Low dielectric loss materials
- Tight tolerances
- Shielding and grounding techniques
The Importance of Choosing the Right RF PCB Manufacturer
When designing and producing RF PCBs, it is crucial to select a reliable and experienced manufacturer. The right RF PCB fabricator should have the necessary expertise, equipment, and processes in place to ensure the highest quality and performance of your RF PCBs.
Factors to Consider When Choosing an RF PCB Manufacturer
- Experience and expertise in RF PCB fabrication
- Quality control processes and certifications
- Range of materials and capabilities
- Lead times and pricing
- Customer support and communication
Top RF PCB Manufacturers & Fabricators
1. Advanced Circuits
Advanced Circuits is a leading RF PCB manufacturer based in the United States. They offer a wide range of RF PCB fabrication services, including controlled impedance, high-frequency laminates, and advanced shielding techniques. Advanced Circuits is known for their quick-turn capabilities and excellent customer support.
Advanced Circuits’ RF PCB Capabilities
Capability | Description |
---|---|
Materials | Rogers, Isola, Taconic, and more |
Frequencies | Up to 77 GHz |
Layers | Up to 24 layers |
Tolerances | ±5% on controlled impedance |
Shielding | Via fencing, copper pour, and custom shielding |
2. Sierra Circuits
Sierra Circuits is another top RF PCB manufacturer, offering state-of-the-art fabrication services for high-frequency applications. They specialize in complex, multi-layer RF PCBs and provide a range of materials and finishes to meet the specific needs of their clients.
Sierra Circuits’ RF PCB Capabilities
Capability | Description |
---|---|
Materials | Rogers, Isola, Taconic, and more |
Frequencies | Up to 110 GHz |
Layers | Up to 40 layers |
Tolerances | ±5% on controlled impedance |
Shielding | Via fencing, copper pour, and custom shielding |
3. San Francisco Circuits
San Francisco Circuits is a trusted RF PCB fabricator with over 40 years of experience in the industry. They offer a comprehensive range of RF PCB services, including design assistance, material selection, and advanced manufacturing techniques. San Francisco Circuits is known for their high-quality products and exceptional customer service.
San Francisco Circuits’ RF PCB Capabilities
Capability | Description |
---|---|
Materials | Rogers, Isola, Taconic, and more |
Frequencies | Up to 90 GHz |
Layers | Up to 28 layers |
Tolerances | ±7% on controlled impedance |
Shielding | Via fencing, copper pour, and custom shielding |
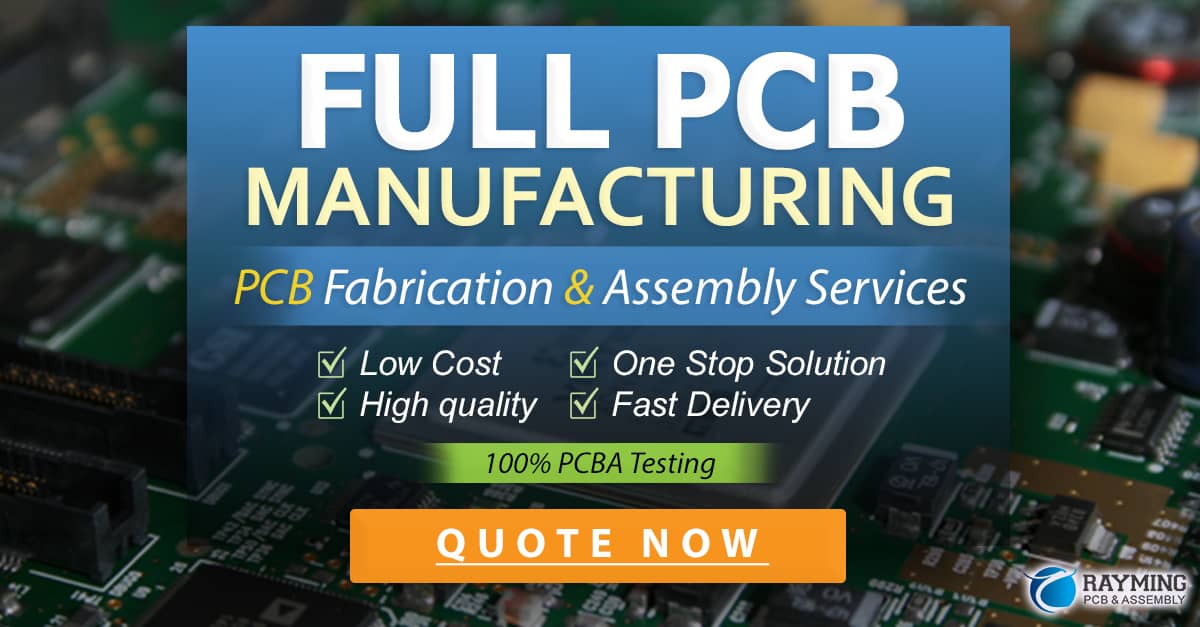
RF PCB Design Considerations
When designing RF PCBs, there are several key factors to consider to ensure optimal performance and signal integrity. These include:
1. Material Selection
Choosing the right dielectric material is critical for RF PCBs. The material should have low dielectric loss, stable dielectric constant, and good thermal properties. Common RF PCB materials include:
- Rogers RO4000 series
- Isola IS680
- Taconic TLY
2. Controlled Impedance
Maintaining consistent impedance throughout the RF PCB is essential for minimizing signal reflections and ensuring proper signal propagation. The most common controlled impedance structures are:
- Microstrip
- Stripline
- Coplanar waveguide
3. Grounding and Shielding
Proper grounding and shielding techniques are crucial for reducing electromagnetic interference (EMI) and improving signal integrity in RF PCBs. Some common techniques include:
- Ground planes
- Via fencing
- Copper pour
- Metal enclosures
4. Layout and Routing
The layout and routing of RF PCBs should be optimized to minimize signal loss, crosstalk, and radiation. Important considerations include:
- Trace width and spacing
- Mitred bends
- Via placement
- Component placement
RF PCB Manufacturing Process
The manufacturing process for RF PCBs is similar to that of standard PCBs, but with added emphasis on precision and quality control. The main steps in the RF PCB manufacturing process are:
- Material selection and preparation
- Copper etching and patterning
- Lamination and drilling
- Plating and finishing
- Electrical testing and inspection
Quality Control in RF PCB Manufacturing
To ensure the highest quality and performance of RF PCBs, manufacturers employ strict quality control measures throughout the fabrication process. These may include:
- Automated optical inspection (AOI)
- Electrical testing
- Impedance testing
- Cross-sectional analysis
- Visual inspection
Applications of RF PCBs
RF PCBs are used in a wide range of applications, including:
- Wireless communication devices (e.g., smartphones, Wi-Fi routers)
- Radar systems
- Satellite communication equipment
- Medical devices (e.g., MRI machines)
- Automotive systems (e.g., collision avoidance radar)
- Military and aerospace applications
Future Trends in RF PCB Technology
As the demand for high-frequency and high-speed communication systems continues to grow, RF PCB technology is constantly evolving. Some of the future trends in RF PCB technology include:
- Higher frequencies (e.g., mmWave, terahertz)
- Advanced materials (e.g., low-loss dielectrics, graphene)
- 3D printing and additive manufacturing
- Integrating RF components directly into the PCB (e.g., antennas, filters)
- Increased use of simulation and modeling tools for RF PCB design
Frequently Asked Questions (FAQ)
1. What is the difference between an RF PCB and a standard PCB?
RF PCBs are designed to handle high-frequency signals, typically above 100 MHz. They require specialized materials, design techniques, and manufacturing processes to ensure optimal performance and signal integrity. Standard PCBs, on the other hand, are designed for lower-frequency applications and do not require the same level of precision and specialization.
2. How do I choose the right material for my RF PCB?
The choice of material for an RF PCB depends on several factors, including the operating frequency, dielectric constant, loss tangent, and thermal properties. Common RF PCB materials include Rogers RO4000 series, Isola IS680, and Taconic TLY. It is essential to consult with your RF PCB manufacturer to select the most suitable material for your specific application.
3. What is controlled impedance, and why is it important in RF PCBs?
Controlled impedance refers to the consistent maintenance of a specific impedance value throughout the RF PCB. This is important for minimizing signal reflections and ensuring proper signal propagation. Controlled impedance structures, such as microstrip and stripline, are used to achieve this consistency.
4. How can I minimize electromagnetic interference (EMI) in my RF PCB design?
To minimize EMI in RF PCBs, designers can employ various techniques, such as proper grounding and shielding, via fencing, copper pour, and metal enclosures. Additionally, optimizing the PCB layout and routing, using ground planes, and carefully placing components can help reduce EMI.
5. What certifications should I look for when choosing an RF PCB manufacturer?
When selecting an RF PCB manufacturer, look for certifications such as ISO 9001 (quality management), IPC (industry standards for PCB design and fabrication), and UL (safety and performance standards). These certifications demonstrate the manufacturer’s commitment to quality, reliability, and adherence to industry best practices.
Conclusion
RF PCBs are essential components in a wide range of high-frequency applications, from wireless communication devices to radar systems and medical equipment. Designing and manufacturing RF PCBs requires specialized expertise, materials, and processes to ensure optimal performance and signal integrity.
When choosing an RF PCB manufacturer, it is crucial to consider factors such as experience, capabilities, quality control, and customer support. Top RF PCB Fabricators, such as Advanced Circuits, Sierra Circuits, and San Francisco Circuits, offer state-of-the-art services and a comprehensive range of materials and capabilities to meet the specific needs of their clients.
As the demand for high-frequency and high-speed communication systems continues to grow, RF PCB technology will continue to evolve, with advancements in materials, manufacturing processes, and design techniques. By staying informed about these trends and working closely with experienced RF PCB manufacturers, designers can ensure the success of their high-frequency projects.
0 Comments