Introduction to RF PCB Design
RF (Radio Frequency) PCB (Printed Circuit Board) design is a specialized area of electronics engineering that focuses on designing and manufacturing PCBs for high-frequency applications. RF PCBs are used in various applications such as wireless communication systems, radar systems, satellite communication, and many other high-frequency electronic devices.
Designing an RF PCB requires a deep understanding of the principles of electromagnetics, transmission line theory, and microwave engineering. RF PCB designers must also have a good grasp of the manufacturing processes and materials used in PCB fabrication.
In this ultimate guide, we will cover everything you need to know about RF PCB design, from the basics of RF theory to advanced design techniques and best practices.
Understanding the Basics of RF Theory
Before diving into RF PCB design, it is essential to understand the basics of RF theory. RF refers to the portion of the electromagnetic spectrum that ranges from 3 kHz to 300 GHz. This range of frequencies is used for various applications, including radio and television broadcasting, cellular communication, and satellite communication.
Electromagnetic Waves
RF signals are transmitted through electromagnetic waves, which are a combination of electric and magnetic fields that propagate through space at the speed of light. The wavelength of an electromagnetic wave is inversely proportional to its frequency, as shown in the following equation:
λ = c/f
Where:
– λ is the wavelength in meters
– c is the speed of light (approximately 3 x 10^8 m/s)
– f is the frequency in hertz (Hz)
Transmission Lines
In RF PCB design, transmission lines are used to carry RF signals from one point to another on the PCB. A transmission line is a two-conductor structure that supports the propagation of electromagnetic waves. The most common types of transmission lines used in RF PCB design are microstrip and stripline.
Microstrip Transmission Lines
Microstrip transmission lines consist of a conductor trace on top of a dielectric substrate, with a ground plane on the bottom. The characteristic impedance of a microstrip transmission line is determined by the width of the conductor trace, the thickness and dielectric constant of the substrate, and the height of the substrate above the ground plane.
The characteristic impedance of a microstrip transmission line can be calculated using the following equation:
Z0 = (87/sqrt(εr + 1.41)) * ln(5.98h/(0.8w + t))
Where:
– Z0 is the characteristic impedance in ohms
– εr is the dielectric constant of the substrate
– h is the thickness of the substrate in meters
– w is the width of the conductor trace in meters
– t is the thickness of the conductor trace in meters
Stripline Transmission Lines
Stripline transmission lines consist of a conductor trace embedded between two ground planes, with a dielectric substrate on either side. Stripline transmission lines have lower radiation losses and better isolation compared to microstrip transmission lines, but they are more difficult to manufacture and have higher capacitance.
The characteristic impedance of a stripline transmission line can be calculated using the following equation:
Z0 = (60/sqrt(εr)) * ln(4h/(0.67π(0.8w + t)))
Where:
– Z0 is the characteristic impedance in ohms
– εr is the dielectric constant of the substrate
– h is the distance between the ground planes in meters
– w is the width of the conductor trace in meters
– t is the thickness of the conductor trace in meters
RF PCB Material Selection
The choice of materials used in RF PCB design is critical to the performance and reliability of the final product. RF PCBs require materials with low dielectric loss, high thermal conductivity, and good mechanical stability.
Substrate Materials
The most common substrate materials used in RF PCB design are:
Material | Dielectric Constant | Loss Tangent | Thermal Conductivity (W/mK) |
---|---|---|---|
FR-4 | 4.5 | 0.02 | 0.3 |
Rogers RO4003C | 3.38 | 0.0027 | 0.71 |
Rogers RO4350B | 3.48 | 0.0037 | 0.69 |
Isola I-Tera MT40 | 3.45 | 0.0031 | 0.62 |
FR-4 is the most common substrate material used in PCB design, but it has relatively high dielectric loss and is not suitable for high-frequency applications. Rogers and Isola materials are specifically designed for RF applications and have lower dielectric loss and higher thermal conductivity compared to FR-4.
Conductor Materials
The most common conductor materials used in RF PCB design are:
Material | Conductivity (S/m) | Skin Depth at 1 GHz (μm) |
---|---|---|
Copper | 5.96 x 10^7 | 2.1 |
Silver | 6.30 x 10^7 | 2.0 |
Gold | 4.10 x 10^7 | 2.5 |
Copper is the most common conductor material used in PCB design due to its high conductivity and low cost. Silver and gold are sometimes used in high-frequency applications due to their lower skin depth and higher conductivity compared to copper.
Soldermask and Silkscreen
Soldermask and silkscreen are also important materials in RF PCB design. Soldermask is a thin layer of polymer that is applied over the copper traces to protect them from oxidation and prevent solder bridging. Silkscreen is used to print text and symbols on the PCB for identification and assembly purposes.
In RF PCB design, it is important to choose soldermask and silkscreen materials that have low dielectric loss and do not interfere with the RF signals. Some common soldermask materials used in RF PCB design are:
- Taiyo PSR-4000 BN
- Hitachi MCL-E-679
- Rogers RO4400
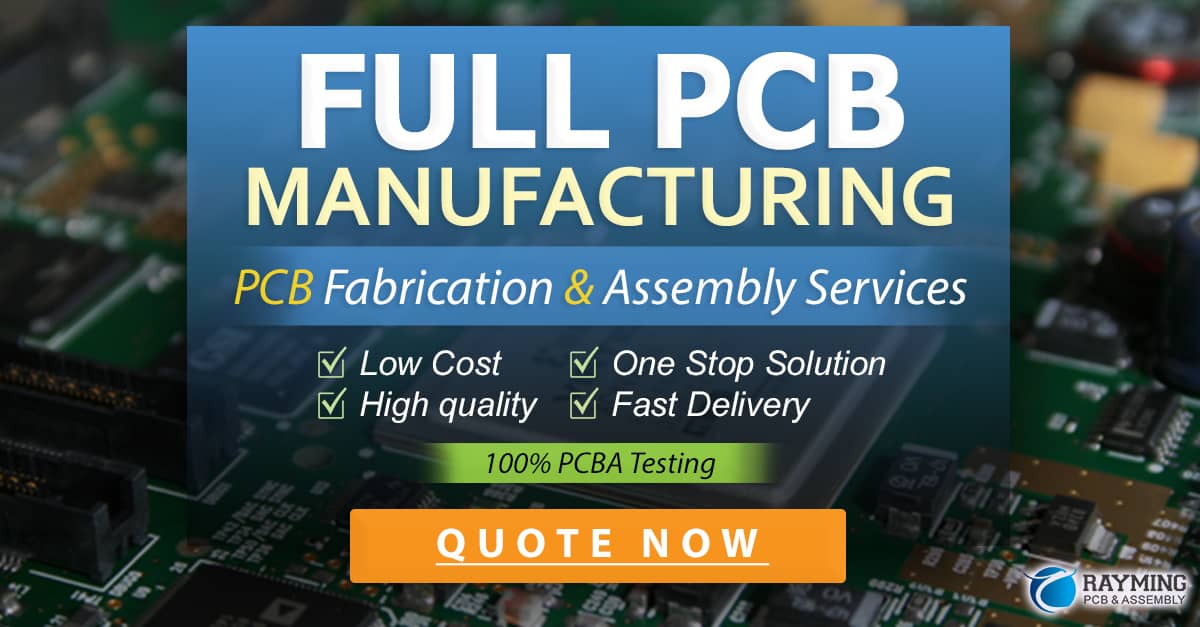
RF PCB Layout and Routing
Proper layout and routing are critical to the performance and reliability of RF PCBs. RF signals are sensitive to impedance mismatches, crosstalk, and radiation losses, which can cause signal distortion and degradation.
Impedance Matching
Impedance matching is the process of designing transmission lines and components to have the same characteristic impedance as the source and load impedances. This minimizes reflections and ensures maximum power transfer from the source to the load.
In RF PCB design, impedance matching is typically achieved by adjusting the width of the conductor traces and the thickness of the dielectric substrate. The goal is to design transmission lines with a characteristic impedance that matches the impedance of the components and connectors used in the system.
Some common impedance values used in RF PCB design are:
- 50 ohms for most RF systems
- 75 ohms for video and cable TV applications
- 100 ohms for differential signaling
Grounding and Shielding
Proper grounding and shielding are essential to minimize electromagnetic interference (EMI) and crosstalk in RF PCBs. Ground planes should be used to provide a low-impedance return path for RF currents and to shield sensitive circuits from external interference.
In multi-layer PCBs, ground planes should be placed adjacent to signal layers to provide maximum shielding and minimize crosstalk. Via fences can also be used to provide additional shielding between signal layers.
Component Placement
Component placement is another important consideration in RF PCB design. Components should be placed as close as possible to their associated transmission lines to minimize parasitic inductance and capacitance. Decoupling capacitors should be placed as close as possible to active devices to provide a low-impedance path for high-frequency noise.
In general, components should be placed in a logical order that minimizes the length of transmission lines and provides a clear signal path from input to output. Care should also be taken to avoid placing components too close to the edge of the PCB, as this can cause unwanted radiation and coupling to adjacent circuits.
Routing Techniques
Proper routing techniques are essential to minimize signal distortion and loss in RF PCBs. Some common routing techniques used in RF PCB design are:
- Microstrip and stripline routing for controlled impedance transmission lines
- Co-planar waveguide (CPW) routing for high-frequency applications
- Grounded coplanar waveguide (GCPW) routing for improved isolation and shielding
- Differential pair routing for balanced signaling and noise reduction
In general, transmission lines should be routed as straight as possible to minimize discontinuities and reflections. Bends and curves should be avoided whenever possible, and when necessary, they should be made with a large radius to minimize impedance mismatches.
RF PCB Manufacturing and Assembly
RF PCBs require specialized manufacturing and assembly techniques to ensure high quality and reliability. Some key considerations in RF PCB manufacturing and assembly are:
PCB Fabrication
RF PCBs typically require tighter tolerances and higher quality materials compared to standard PCBs. Some common requirements for RF PCB fabrication are:
- Tight tolerances on trace width and spacing (typically +/- 0.05mm or better)
- Controlled dielectric thickness and consistency
- Low-loss and high-frequency laminate materials
- Smooth copper surfaces to minimize skin effect losses
- Precise hole drilling and plating to minimize parasitic inductance
PCB Assembly
RF PCB assembly requires specialized equipment and techniques to ensure proper placement and soldering of components. Some common requirements for RF PCB assembly are:
- High-precision pick-and-place machines with vision systems for accurate component placement
- Reflow soldering with precise temperature control to avoid damaging sensitive components
- Automated optical inspection (AOI) to detect soldering defects and component misalignment
- X-ray inspection to verify proper solder joint formation and detect hidden defects
Testing and Verification
RF PCBs require thorough testing and verification to ensure proper functionality and performance. Some common tests performed on RF PCBs are:
- Time-domain reflectometry (TDR) to measure impedance and detect discontinuities
- Vector network analyzer (VNA) measurements to characterize S-parameters and insertion loss
- Spectrum analyzer measurements to detect spurious emissions and harmonics
- Electromagnetic compatibility (EMC) testing to ensure compliance with regulatory standards
Best Practices for RF PCB Design
To ensure successful RF PCB design, it is important to follow some best practices and guidelines. Here are some key best practices for RF PCB design:
-
Start with a clear specification and requirements document that defines the performance goals, operating frequency, power levels, and interface requirements for the system.
-
Use simulation tools to model and optimize the RF circuit before beginning PCB layout. This can help identify potential issues and allow for design refinements before committing to hardware.
-
Choose high-quality, low-loss materials for the PCB substrate, conductors, and components. Avoid using FR-4 for high-frequency applications.
-
Use controlled impedance design techniques to ensure proper matching and minimize reflections. This may require using specialized tools and calculators to determine the optimal trace widths and spacings.
-
Minimize the length of transmission lines and component leads to reduce parasitic inductance and capacitance. Place components as close as possible to their associated traces.
-
Use ground planes and via fences to provide shielding and minimize crosstalk between signal layers. Avoid placing signal traces over gaps or slots in the ground plane.
-
Use differential signaling whenever possible to reduce noise and improve signal integrity. Route differential pairs with tightly-coupled traces and maintain consistent spacing and symmetry.
-
Avoid sharp bends and discontinuities in transmission lines. Use smooth curves and chamfered corners to minimize impedance mismatches and reflections.
-
Use high-quality connectors and cables with proper impedance matching and shielding. Avoid using connectors with excessive insertion loss or VSWR.
-
Perform thorough testing and verification of the RF PCB to ensure proper functionality and performance. Use specialized equipment such as VNAs, spectrum analyzers, and TDR to characterize the system and identify any issues.
FAQ
What is the difference between microstrip and stripline transmission lines?
Microstrip transmission lines have a single conductor trace on top of a dielectric substrate, with a ground plane on the bottom. Stripline transmission lines have a conductor trace embedded between two ground planes, with dielectric substrates on either side. Microstrip lines are easier to fabricate but have higher radiation losses and less isolation compared to striplines.
What is the skin effect and how does it impact RF PCB design?
The skin effect is the tendency of high-frequency currents to flow primarily on the surface of a conductor, rather than uniformly throughout the cross-section. This leads to increased resistance and loss at high frequencies. To minimize skin effect losses, RF PCBs typically use thicker copper traces and smoother copper surfaces compared to standard PCBs.
What is a via fence and why is it used in RF PCB design?
A via fence is a row of closely-spaced vias that are used to provide shielding and isolation between different sections of an RF PCB. Via fences can be used to prevent crosstalk between signal layers, to isolate sensitive circuits from external interference, or to provide a low-impedance return path for RF currents.
What is the purpose of a decoupling capacitor in RF PCB design?
Decoupling capacitors are used to provide a low-impedance path for high-frequency noise and to prevent it from coupling into sensitive circuits. Decoupling capacitors are typically placed as close as possible to active devices such as amplifiers and mixers, and are chosen to have a self-resonant frequency higher than the operating frequency of the circuit.
What are some common RF connectors used in PCB design?
Some common RF connectors used in PCB design are:
- SMA (SubMiniature version A) connectors for frequencies up to 18 GHz
- SMB (SubMiniature version B) connectors for frequencies up to 4 GHz
- MMCX (Micro-Miniature Coaxial) connectors for frequencies up to 6 GHz
- U.FL (Ultra-small Surface Mount Coaxial) connectors for frequencies up to 6 GHz
The choice of connector depends on the frequency, power level, and physical size constraints of the system.
Conclusion
RF PCB design is a complex and specialized field that requires a deep understanding of electromagnetic theory, transmission line principles, and PCB manufacturing techniques. Successful RF PCB design requires careful selection of materials, precise control of impedances and dimensions, and thorough testing and verification.
By following best practices and guidelines for RF PCB design, engineers can create high-performance, reliable systems for a wide range of applications. As the demand for wireless connectivity and high-speed communication continues to grow, the importance of RF PCB design will only continue to increase in the years ahead.
0 Comments