What is Reflow soldering?
Reflow soldering is a technique that involves applying solder paste to the pads on a PCB, placing the surface mount components onto the solder paste, and then heating the entire assembly in a reflow oven. The heat melts the solder paste, which then forms a permanent connection between the component leads and the PCB pads as it cools and solidifies.
Advantages of Reflow Soldering
- High efficiency: Reflow soldering allows for the simultaneous soldering of multiple components, making it a fast and efficient process for mass production.
- Consistency: The automated nature of reflow soldering ensures consistent and reliable solder joints, reducing the risk of human error.
- Miniaturization: Reflow soldering enables the use of smaller components and finer pitch leads, facilitating the miniaturization of electronic devices.
- Reduced thermal stress: The controlled heating and cooling process in reflow soldering minimizes thermal stress on components compared to manual Soldering Methods.
The Reflow Soldering Process
The reflow soldering process consists of several key stages:
1. Solder Paste Application
Solder paste, a mixture of tiny solder particles suspended in a flux medium, is applied to the PCB pads using a stencil printing process. The stencil, a thin metal sheet with apertures corresponding to the pad locations, is placed over the PCB. Solder paste is then spread across the stencil, filling the apertures and depositing the paste onto the pads.
2. Component Placement
Surface mount components are placed onto the solder paste-coated pads using a pick-and-place machine. These machines use computer-controlled nozzles to accurately position the components based on the PCB design file. The components are held in place by the tackiness of the solder paste.
3. Reflow Oven Heating
The populated PCB is then passed through a reflow oven, which has multiple temperature zones. The oven heats the assembly according to a precise temperature profile, which typically includes the following stages:
Stage | Description | Temperature Range |
---|---|---|
Preheat | Gradual heating to activate the flux and remove solvents | 150°C – 180°C |
Soak | Temperature stabilization to ensure even heat distribution | 150°C – 180°C |
Reflow | Rapid heating to melt the solder particles and form solder joints | 220°C – 250°C |
Cooling | Gradual cooling to allow the solder joints to solidify | Room temperature |
4. Inspection and Testing
After the reflow soldering process, the PCB undergoes visual inspection and electrical testing to ensure the quality of the solder joints and the functionality of the assembled board. Automated optical inspection (AOI) systems and in-circuit testing (ICT) are commonly used methods for this purpose.
Reflow Soldering Equipment
Several key pieces of equipment are used in the reflow soldering process:
1. Stencil Printer
A stencil printer is used to apply solder paste to the PCB pads. It consists of a frame to hold the stencil, a squeegee to spread the solder paste, and a system for aligning the PCB with the stencil.
2. Pick-and-Place Machine
Pick-and-place machines are used to automatically place surface mount components onto the solder paste-coated pads. They use computer-controlled nozzles and vision systems to accurately position the components based on the PCB design file.
3. Reflow Oven
A reflow oven is used to heat the PCB Assembly and melt the solder paste to form permanent solder joints. Reflow ovens come in various configurations, including convection, infrared, and vapor phase, each with its own advantages and limitations.
Oven Type | Heating Method | Advantages | Limitations |
---|---|---|---|
Convection | Hot air circulation | Even heating, good for large PCBs | Slower than other methods |
Infrared | Infrared radiation | Fast heating, energy-efficient | Shadowing effects, potential hot spots |
Vapor Phase | Condensation of vapor | Uniform heating, minimal thermal stress | Higher cost, limited PCB size |
4. Inspection Systems
Automated optical inspection (AOI) systems use cameras and image processing software to detect solder joint defects and component placement errors. In-circuit testing (ICT) systems use probes to verify the electrical continuity and functionality of the assembled PCB.
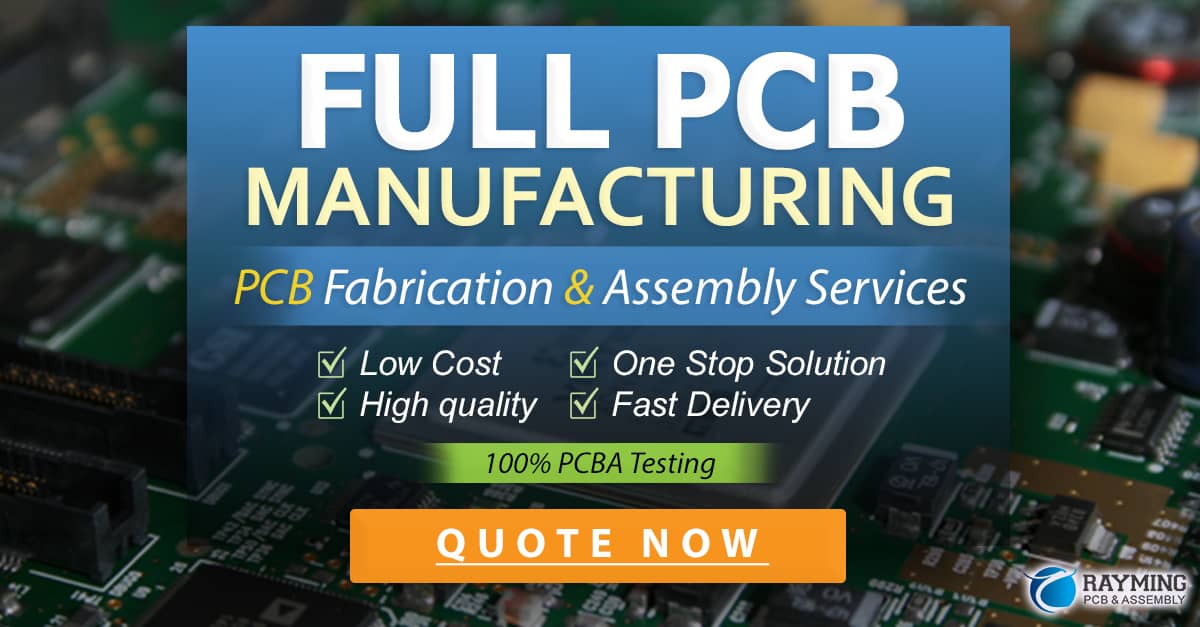
Frequently Asked Questions (FAQ)
-
What is the difference between reflow soldering and wave soldering?
Reflow soldering is used for surface mount components and involves applying solder paste, placing components, and heating the assembly in a reflow oven. Wave soldering, on the other hand, is used for through-hole components and involves passing the PCB over a molten solder wave. -
Can reflow soldering be used for through-hole components?
While reflow soldering is primarily used for surface mount components, it can be used for certain through-hole components with appropriate preparation, such as using solder paste in the holes or using Pin-in-Paste technology. -
What is the purpose of flux in solder paste?
The flux in solder paste serves to remove oxides from the metal surfaces, promote solder wetting, and protect the solder joint from oxidation during the reflow process. -
How does the reflow temperature profile affect the solder joint quality?
The reflow temperature profile must be carefully controlled to ensure proper solder melting, wetting, and solidification. Insufficient heating can result in poor solder joints, while excessive heating can cause component damage or solder defects. -
What are some common defects in reflow soldered PCBs?
Common defects in reflow soldered PCBs include bridging (solder shorts between adjacent pads), tombstoning (components standing on end due to uneven solder melting), insufficient solder, and solder balls (small spheres of solder that can cause short circuits).
In conclusion, reflow soldering is a critical process in the manufacturing of electronic devices, enabling the efficient and reliable assembly of surface mount components on PCBs. By understanding the fundamentals of reflow soldering, the process involved, and the equipment used, engineers and technicians can optimize the process to achieve high-quality solder joints and ensure the reliability of the final product.
0 Comments