Introduction
For hardware startups and engineers, having a reliable prototype PCB (printed circuit board) manufacturer is crucial during the design and testing phase. Choosing the right partner can significantly impact your ability to iterate quickly and bring innovative products to market faster. This guide will walk you through the key factors to consider when selecting a PCB prototyping service.
Capability Range
The first thing to examine is the manufacturer’s capability range in terms of:
Layer Count
Most prototypes require 2-8 layers. Choose a partner that can handle your required layer count for current and future projects. Going with a shop that maxes out at 2 layers could slow you down later.
Minimum Line/Space
This refers to the smallest trace width and spacing between copper traces on the PCB. For intricate, high-speed or high-frequency boards you’ll want at least 4mil line/space.
Solder Mask Type
Liquid Photo Imageable (LPI) solder mask is preferred for its durability and resolution on complex boards. Avoid shops using lower-quality dry film solder mask for prototypes.
Finishing
ENIG (electroless nickel immersion gold) offers excellent solderability and contact integrity for prototypes. Hasl (Hot Air Solder Leveling) is more prone to oxidation problems.
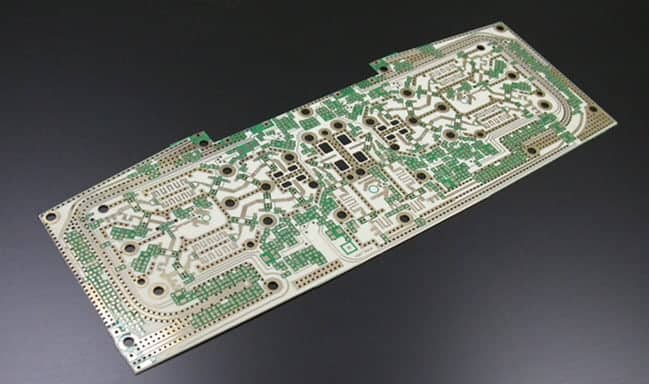
Material Type
Standard FR-4 glass epoxy is fine for most prototypes but if you need high frequency performance choose a PCB shop with advanced materials like high-frequency FR-4, Rogers, Arlon etc.
Panel Size
If size and quantity requirements warrant, look for a manufacturer that can produce panelized boards for more efficiency and lower cost.
Quick Turnaround
Look for manufacturers that can deliver in 5-7 days from order to shipment for fastest design validation. Some shops even offer 24-48 hour rush service.
Quality Processes
Don’t compromise quality to save a few bucks on prototype PCBs. Review the manufacturer’s quality certifications and processes:
- IPC standards – IPC are a set of rigorous PCB manufacturing standards. Look for certification to IPC-A-610 for assembly and IPC-6012 for fabrication at a minimum.
- Validation Testing – Such as netlist testing, AOI (Automated Optical Inspection) and electrical testing. These processes ensure your design files translate accurately to physical boards.
- DFM Checking – DFM (Design for Manufacturability) analysis by engineering staff to catch any issues before production. This optimizes yield.
- Test Coupons – Inclusion of test point coupons on panelized boards to validate line widths, registration and impedance.
Additional Services
The most capable prototype PCB companies offer a range of additional services to simplify your process:
- Assembly – Full SMT (surface mount) assembly, not just bare boards.
- Testing – Assistance with test plan development, fixture design and performing functional testing of assembled boards.
- DFM Analysis – Providing recommendations to optimize the design for manufacturability and performance.
- Engineering Support – Quick feedback and real-time communication for any issues that come up.
- Supply Chain Management – Procurement of components needed for SMT assembly as a single point of contact.
Location
When speed is critical, choosing a prototype PCB manufacturer with facilities in your region can significantly cut down lead times and shipping costs. For example North America, Europe or Asia.
In some cases it may be feasible to visit the manufacturer for an audit or to inspect prototypes before full production ramp up.
Qualifications
Here are key credentials to look for in any PCB prototyping partner:
- ISO-9001 certified quality management processes.
- ITAR registration if your project requires it.
- Excellent customer reviews and client list.
- Decades of experience specifically with prototype PCB work. Generic PCB shops often don’t have the specialized expertise needed.
- Trade organization membership such as the IPC.
Summary
Choosing the right prototype PCB manufacturer requires weighing a variety of factors based on your specific needs. Prioritize quality processes, capability range, value-added services, location, qualifications and customer reputation. Take the time to thoroughly evaluate multiple partners before selecting one. This investment of effort will pay dividends by enabling faster design iteration and better performance.
Frequently Asked Questions
Q: What are the main advantages of using a specialized prototype PCB manufacturer vs. a generic PCB shop?
A: Prototype specialists offer:
- Faster lead times enabled by optimized quick-turn processes.
- More experience with lower volume, highly complex boards needed for R&D.
- Higher quality standards ideal for prototyping vs. high volume production.
- Value-added and customized services aimed at prototype work.
- Engineers and staff specifically focused on low-volume prototyping jobs.
Q: What are some key indicators of quality for a PCB prototype manufacturer?
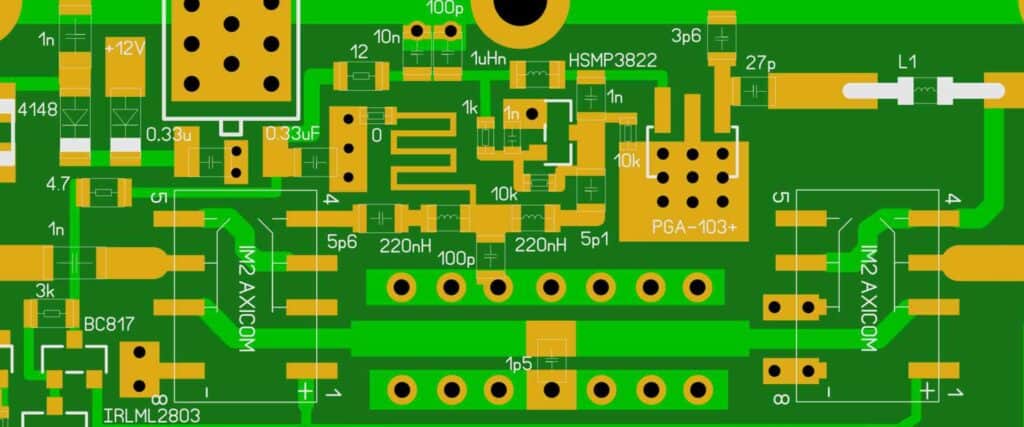
A: Quality indicators include:
- IPC certifications for fabrication and assembly.
- Comprehensive validation testing of boards.
- DFM analysis before manufacturing begins.
- Test coupons included on panelized boards.
- Strict process controls and SPC data collection.
- Technology use such as AOI for inspection.
- Excellent customer reviews/references.
Q: What questions should I ask potential prototype PCB manufacturers?
A: Key questions include:
- What is your PCB technology capability range? (layers, line space, materials etc.)
- What are your typical lead times for prototype orders?
- What DFM analysis and testing is done to ensure quality?
- Do you offer assembly and other services beyond just bare boards?
- Do you have design engineers on staff that can provide feedback?
- Are you ITAR registered if required?
- Can you share customer references/reviews?
Q: Should I order multiple prototype iterations in parallel or sequence them incrementally?
A: It generally works better to incrementally sequence prototype runs when possible. This lets you incorporate learnings from each iteration into the next vs. running all iterations in parallel. However, if time-to-market is critical, parallel prototype builds may be warranted despite the higher cost.
Q: What are some best practices to get the most value from working with a prototype PCB manufacturer?
A: Best practices include:
- Engage the manufacturer’s engineers for DFM analysis and review before finalizing your design files.
- Discuss your prototyping plan and roadmap with the manufacturer.
- Clearly communicate your testing expectations and requirements.
- Review test results and inspect prototypes carefully when received.
- Provide thorough, timely feedback on each prototype run.
- Have your manufacturer help procure needed components for assembly builds.
- Share your schedule needs accurately and openly so the shop can support you.
0 Comments