Introduction
Prototyping is a critical step in new product development. High-quality prototypes enable companies to test concepts, evaluate designs, and de-risk the path to production. However, building prototypes from scratch can be complex, time-consuming, and prone to quality issues. This is where prototype assembly services can help.
Prototype assembly services provide dedicated expertise and capacity for constructing prototypes accurately and efficiently. By outsourcing prototype builds, product developers can accelerate innovation, reduce costs, and bring better products to market faster.
This guide covers the key benefits of leveraging prototype assembly services, how to select the right partner, and the end-to-end process of engaging with an assembly provider. Follow these best practices to maximize prototype quality and speed.
Benefits of Using Prototype Assembly Services
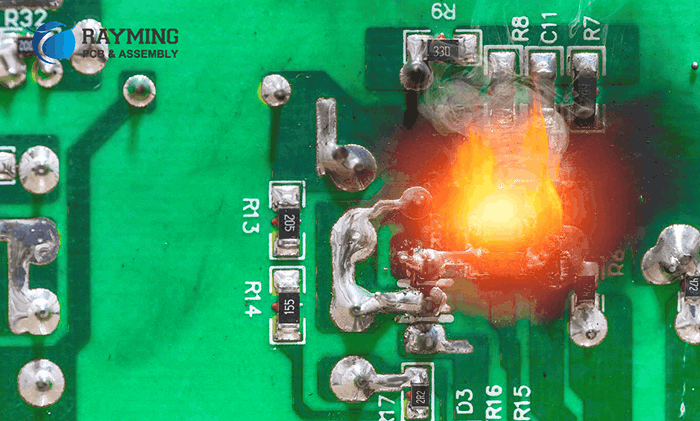
The major advantages of outsourcing prototype assembly include:
Faster Build Speed – Specialized assemblers have proven build processes to construct prototypes rapidly. Parallel assembly operations shrink lead times.
Flexible Scaling – Assembly providers can easily scale capacity up or down to match variable demand. This prevents backlogs from stalling projects.
Cost Efficiency – Dedicated assemblers achieve lower per-unit costs through economy of scale. Buying power on materials is another savings.
Quality Execution – With rigorous quality controls and experienced technicians, assembly providers achieve high precision builds to spec.
Accelerated Learning – Fast turnaround on prototypes creates rapid test-and-learn iterations to refine the design quickly.
Reduced Overhead – No need to purchase tools, equipment and hire specialized labor to perform assembly in-house.
How to Select the Right Prototype Assembly Partner
With the variety of assembly providers available, it is important to choose a partner that best matches your specific prototyping needs:
Range of Capabilities – Seek broad expertise in different build methods like CNC machining, 3D printing, sheet metal fabrication, and more.
Materials Experience – Choose partners with know-how in the specific plastics, metals, composites, and other materials used in your prototypes.
Quality Systems – Look for robust quality control processes, inspection protocols, and international quality certifications.
Related Industry Experience – Prefer assemblers with proven experience in your product segment for relevant insights.
Engineering Collaboration – Pick providers open to design reviews and engineering collaboration to refine the assembly process.
Prototyping Focus – Choose specialty prototype assemblers over general contract manufacturers for greater build speed.
Security – For sensitive designs, ensure robust security practices are in place including NDAs.
Scalability – Look for ability to flexibly scale up/down capacity so lead times stay short.
Evaluating partners against these criteria results in the right strategic relationship for prototyping success.
The Prototype Assembly Process Step-by-Step
Follow this step-by-step process to maximize efficiency and collaboration with your chosen assembly provider:
Step 1 – Design Review
Submit initial CAD models and drawings for design review. The assembler provides feedback on design for manufacturability and selects the optimal build methods.
Step 2 – Engineering Collaboration
Work jointly to modify designs if needed to improve manufacturability based on the assembler’s recommendations.
Step 3 – Prototyping Plan
Finalize project plan detailing schedule, budget, quality oversight, and other terms to provide clear expectations.
Step 4 – Obtain Raw Materials
The assembler sources all required parts, hardware, and materials at the best cost based on volumes required.
Step 5 – Program Generation
For processes like CNC machining, specialized programming is completed based on CAD models.
Step 6 – Manufacturing Prototype
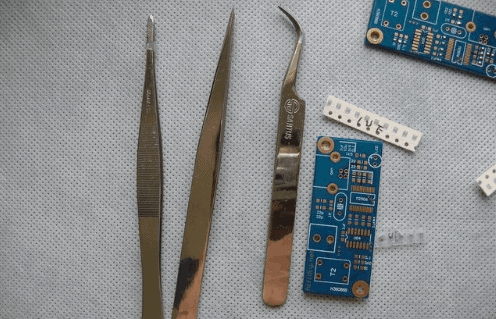
The prototype is constructed by trained technicians following the defined quality management plan.
Step 7 – Inspection Testing
Each assembly is inspected against specifications. Testing and validation checks for full functionality.
Step 8 – Final Prototype Delivery
The finished prototype units are delivered along with documentation of quality data, materials, and work instructions.
Step 9 – Design Review
Evaluate the prototypes collaboratively to improve manufacturability for the next design iteration.
Maintaining regular communication and feedback loops is key to maximizing prototyping efficiency with an assembly partner.
Table: In-House vs Outsourced Prototype Assembly
Factor | In-House Assembly | Outsourced Assembly |
---|---|---|
Speed | Slower process | Faster turnaround |
Expertise | Learning curve required | Leverages specialized expertise |
Quality | Higher risk of defects | Mature quality control |
Overhead | High equipment costs | Low, outsourced model |
Scalability | Limited capacity | Flexible, on-demand |
Cost | High per-unit cost | Low due to economies of scale |
Key Takeaways
Prototype assembly services enable faster, lower-cost, and lower-risk product development compared to in-house build:
- Accelerate innovation through rapid prototyping iterations
- Focus internal efforts on design rather than production
- Leverage specialized expertise for high-quality execution
- Scale on demand avoiding capacity bottlenecks
- Reduce costs through purchasing leverage and labor savings
- Mitigate quality risks with mature assembly practices
By selecting the right strategic partner, outsourced prototype assembly provides a fast track to turning bold ideas into reality.
Frequently Asked Questions
Q: When does it make sense to outsource vs. do prototype assembly in-house?
A: Outsourcing is preferable when project complexity, quality requirements, or capacity constraints exceed internal capabilities. It enables a focus on design over production.
Q: What level of design change is possible during prototyping with an assembly partner?
A: There is flexibility to modify and iterate designs through the build-test-learn cycles as long as the assembler is involved in engineering reviews.
Q: How can we protect sensitive or confidential product designs and data?
A: Require NDAs, limit data sharing only to essentials, and work only with assemblers with strong information security controls. On-site assembly can also limit risks.
Q: Can assembly partners scale up from prototyping to production volumes?
A: Prototype assemblers specialize in low volume work. For scaled production, a full contract manufacturer is recommended instead.
Q: What quality standards should assembly providers adhere to?
A: ISO 9001 certification is a minimum requirement. Additional certifications in ISO 13485, AS9100, or IATF 16949 demonstrate rigorous quality systems for more complex prototypes.
0 Comments