Introduction
Prototype assembly is an essential part of product development, allowing teams to quickly and cost-effectively build early stage models of a product for testing and validation. In the early stages of development, prototypes can provide invaluable feedback that informs engineering decisions and reduces risk further down the development cycle. This article provides an overview of prototype assembly, including best practices, design considerations, testing approaches, and tips for managing prototyping projects.
What is a Prototype?
A prototype is an early sample, model or release of a product built to test a concept or process. Prototypes can range in fidelity from rough concept sketches to functional forms that look and operate almost identically to the final product. Here are some common classifications of prototypes:
- Proof-of-concept – Basic prototype focused on testing the feasibility of a technology or idea. May not represent the final visual design.
- Functional – Represents the final product and includes functional elements, but may use different materials and manufacturing processes.
- Pre-production – Nearly indistinguishable from the final product with close to final tooling and materials. Used for validation testing.
Benefits of Prototyping
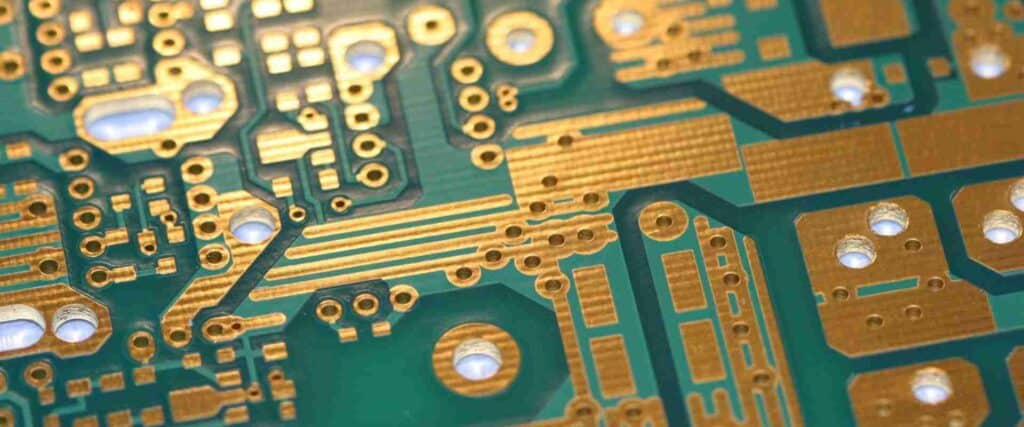
Prototyping offers many benefits for engineering and product development:
- Tests assumptions – Prototypes allow teams to test ideas and challenge assumptions about technical feasibility and consumer response. This reduces risk.
- Gathers early feedback – Early prototypes can gather user feedback for design improvements before launching the final product.
- Informs requirements – The hands-on experience with a prototype reveals important requirements that may have been overlooked.
- Estimates costs/timelines – Building a prototype exposes unanticipated development challenges which improves cost and timeline estimates.
- Verifies manufacturing processes – Production-intent prototypes verify the product can be manufactured at scale.
Prototype Design Considerations
When designing a prototype, some key factors to consider include:
- Purpose – Is this prototype focused on technical validation, visual refinement, consumer response, manufacturing assessment? Align the prototype design to key objectives.
- Fidelity – The visual and functional resolution of the prototype matching its purpose. Low fidelity for early concept validation. High fidelity for pre-production.
- Materials – Prototyping materials like 3D prints, CNC foam, laser cut acrylic that allow for quick iteration and modification.
- Interface simulation – Using placeholder components or augmented reality to simulate interfaces like screens, buttons, lights.
- Appearance – How important is achieving the right visual appearance and feel? Vehicle prototypes often use clay models.
- Manufacturability – If assessing manufacturability, use close to final materials, tooling and processes.
When designing prototypes, avoid over-engineering early prototypes with unnecessary complexity that causes delays and expense. Focus on validating the core product requirements first.
Prototype Assembly Best Practices
Here are some best practices to follow when assembling prototypes:
- Use version control for prototype parts like molded and machined components to enable incremental improvement.
- Modularize components that may require frequent modification like control panels and electronics.
- Implement quick fastening methods like magnets, thumbscrews and captive fasteners for easy assembly.
- Minimize wiring complexity with modular connectors, harnesses and ribbon cables.
- Develop debugging features like status lights and test points to evaluate performance.
- Manage parts efficiently with inventory numbering, storage labels and databases.
- Repurpose and recycle prototype parts when possible across iterations.
- Document the bill of materials, assembly steps, test results and issues for each iteration.
Prototype Testing Approaches
Thoroughly testing prototypes is key for revealing performance issues and incrementally improving the design. Some recommended testing approaches include:
Functional testing
Validating that the prototype operates as intended under real-world conditions:
- Lifecycle testing – Simulating full usage lifecycles like wear, weather, fatigue.
- Stress testing – Testing beyond normal conditions to reveal failure points.
- Environmental testing – Testing relevant environments like vibration, temperature, moisture.
Validation testing
Evaluating whether the prototype meets product specifications and requirements:
- Requirements validation – Methodically testing each product requirement.
- Performance benchmarks – Quantify performance metrics like speed, efficiency.
- Comparative testing – Compare to existing products on critical metrics.
Usability testing
Observing representative users interact with the prototype:
- Focus groups – Facilitated discussion with a small group of target users.
- User surveys – Broad end user feedback on preferences and pain points.
- Field testing – Observing use of the prototype in real world settings.
Continuously testing and refining prototypes prior to design finalization greatly reduces downstream risks and results in a superior end product.
Managing Prototype Development
Careful planning and management is required to keep prototype projects on track. Here are some tips:
- Define a structured prototyping process and timeline with stages aligned to objectives.
- Use a phased approach: concept models -> functional models -> pre-production models.
- Identify resources needed like skills, equipment, materials and budget for each phase.
- Develop a test plan upfront detailing the testing objectives, methods, metrics and pass/fail criteria.
- Review results after each milestone, update requirements, refine schedules.
- Manage version control diligently for prototype parts, documentation and test reports.
- Track action items, issues, dependencies and risks in a central issue log.
- Control scope creep by focusing on core requirements first before adding bells and whistles.
Key Takeaways
- Prototyping is crucial for testing concepts and assumptions in the early stages of product development.
- Matching prototype fidelity to the purpose and phase helps avoid over-engineering early prototypes.
- Modular and flexible construction enables quick modification and iteration of prototypes.
- Thoroughly testing prototypes against requirements reveals flaws and incrementally improves the design.
- Careful planning and management is key to keeping prototyping projects on budget and schedule.
Frequently Asked Questions
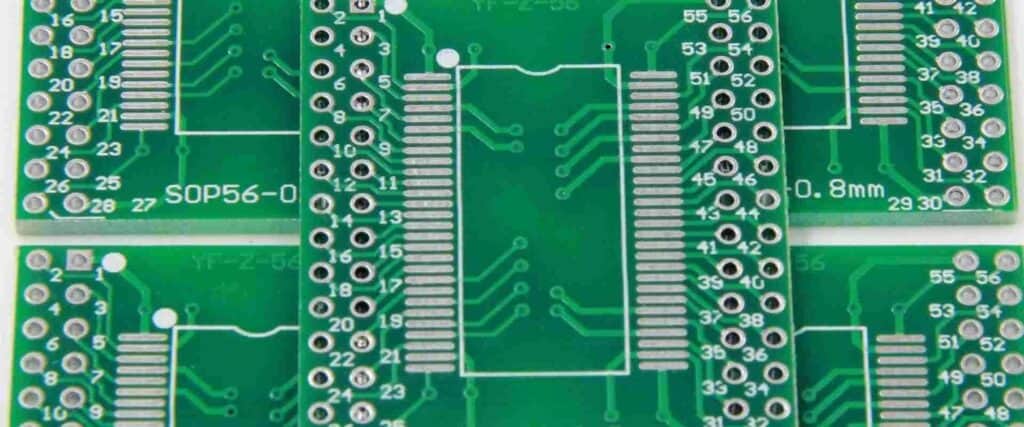
Here are some common questions about prototype assembly:
What are some quick, low-cost methods for creating prototypes?
For early stage concept models, methods like 3D printing, laser cutting, CNC milling allow quick fabrication without expensive tooling. Consumer model kits and craft materials like cardboard are other low cost options.
When should you engage manufacturers to build production-intent prototypes?
Engage manufacturers once the design is sufficiently defined and ready for validation of manufacturability. Their expertise can help avoid design errors.
How many prototype iterations should be planned for a new product introduction?
For complex products, 10+ iterations is typical from early concept models through to pre-production validation. Budget sufficient time, resources and testing for this iterative process.
Should prototype testing follow the same protocols as production validation testing?
Testing methodology should scale up as prototypes evolve. Use accelerated testing that emphasizes failure discovery early on. Formalize testing on pre-production models.
How can you get reliable user feedback from early prototypes?
Avoid asking for subjective opinions. Focus user testing on core use cases and measurable performance against requirements. Feedback on rough prototypes can be unreliable.
0 Comments