Developing new electronic products requires assembling prototypes to validate designs before moving to mass production. While large manufacturers have automated SMT assembly lines, smaller innovators need more flexible options. Prototype and low volume SMT assembly allows building small batches to test product concepts without huge upfront capital costs. This guide covers key considerations for utilizing SMT assembly services for prototypes or initial production runs.
Capabilities to Look For
When selecting an SMT assembly provider, you’ll want to evaluate their capabilities to meet your specific needs:
Low Volume Production
Look for companies focused on supporting prototype builds and small scale production, which is very different than high volume manufacturing.
Quick Turnaround
Getting prototypes produced rapidly allows more design iterations. Seek assembly services offering 1-2 week or faster turnaround.
Flexible Order Quantities
Order only what you need. Suppliers should support building 5, 10 or other small quantities rather than forcing minimum order sizes.
Component Procurement
Your assembly partner should be able to procure common components, avoiding delays finding parts yourself.
Design for Manufacturability
Reputable assemblers will audit your design and identify any issues proactively before build.
Hand Soldering
Some components may require manual soldering which should be offered.
Programming
If your product involves programmable devices like microcontrollers, look for programming and loading services.
Post Assembly Testing
Testing functionality after build avoids defective units. Electrical, optical and other testing should be available.
Certifications
Look for ISO 9001 or other standards certifying quality management processes.
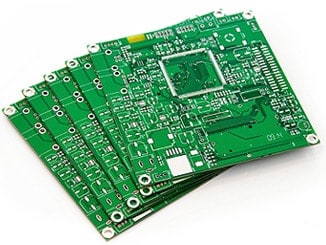
Optimizing Low Volume SMT Designs
Careful design considerations can streamline prototyping assembly and avoid unnecessary costs:
Minimize Unique Parts
The more unique components required, the more complex and costly procurement and assembly become. Reduce variety through standardization.
Design with Common Components
Selecting readily available parts from major suppliers makes procurement faster and cheaper. Check availability.
Use Standard Packages
Common packaging like SOIC, QFP, SOT-23 etc. makes assembly more straightforward than exotic packages.
Provide Detailed BOM
Supply complete bill of materials detailing part numbers, quantities, reference designators, specifications, and supplier information.
Include Assembly Drawings
Clear drawings indicating component placement locations and orientation assists assembly.
Design Test Points
Include test points linking traces and components to simplify validating assemble boards.
Avoid Dense Packing
Avoid designing boards that pack components together too densely for the capabilities of the assembler.
Allow Sufficient Clearances
Ensure adequate spacing between components and traces based on assembler feedback.
Validate Before Ordering
Have assembler review designs, BOM, etc. and make recommendations before finalizing orders.
Assembled Prototype Testing Best Practices
Testing finished prototypes is crucial before progressing to production. Here are key testing best practices:
Visual Inspection
Thoroughly inspect assembled boards to check for issues like missing or misaligned components, poor solder joints, debris, etc. Use magnification where helpful.
Basic Functionality
Confirm basic operation of primary components like ICs, regulators, connectors, LEDs, etc. Methodically validate each section.
Simulation Testing
Expose prototypes to simulated environmental conditions like temperature, vibration, humidity, electrical noise, etc. based on product specifications.
Long Duration Testing
Run prototypes continuously for multiple days/weeks under realistic loads to catch intermittent issues.
Validation Testing
Compare prototype performance metrics to expected targets derived from models, calculations, simulations, etc.
Destructive Testing
Intentionally apply stresses beyond normal conditions to check failure modes and physical robustness.
Iterate
Use testing insights to refine designs, assembly processes, QA procedures, and other aspects for subsequent versions.
Global Prototype Assembly Manufacturers
Many contract manufacturers worldwide offer SMT assembly services focused on low volume and prototypes. Here are some well known options:
United States
- Jabil – One of the largest global contract manufacturers with dedicated prototyping services.
- Plexus – End-to-end product realization including low volume engineering and manufacturing.
Europe
- Asteelflash – Headquartered in France, with prototype assembly in Europe.
- Scanfil – Finish manufacturer supporting new product introduction and ramp to volume.
China
- AllCircuits – Chinese prototype assembly service catering to startups and makers.
- Seeed Studio – Manufacturing services for rapid prototyping through open parts library.
- JLPCB – Low cost PCBs, custom cables, stencils, assembly and other services.
Southeast Asia
- Inventec – Taiwanese EMS firm supporting prototypes and pre-production ramps.
- Venture – Singapore based manufacturing services including prototyping.
Company | Location | Min. Order | Lead Time |
---|---|---|---|
Jabil | USA | 10 units | 2 weeks |
Plexus | USA | 50 units | 4 weeks |
Asteelflash | France | 10 units | 2 weeks |
Scanfil | Finland | 10 units | 3 weeks |
AllCircuits | China | 5 units | 1 week |
Seeed Studio | China | 1 unit | 2 weeks |
JLPCB | China | 5 units | 1 week |
Inventec | Taiwan | 10 units | 2 weeks |
Venture | Singapore | 10 units | 4 weeks |
Frequently Asked Questions
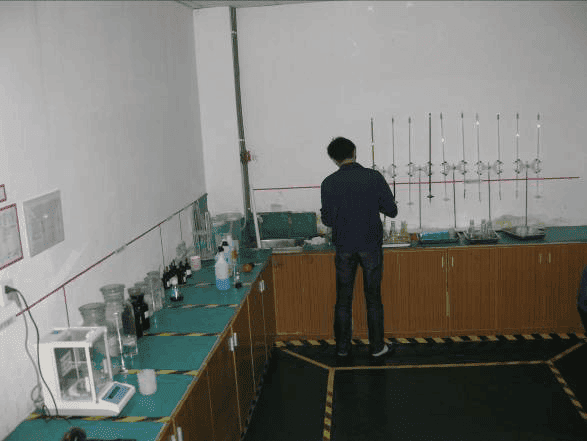
What documentation is required for prototype assembly?
Typical documents needed are bill of materials, PCB gerber files, assembly drawings, mechanical drawings, component datasheets, and any special instructions.
How are parts procured for prototype builds?
You can provide parts yourself or the assembler can procure based on the BOM. Pre-requesting quotes for long lead parts helps avoid delays.
What are the most common SMT assembly defects?
Typical defects include missing components, tombstoning, skewed parts, insufficient solder, excess solder, shorts, opens, and backward or out of place components.
Should every unit be functionally tested after assembly?
While testing each unit would be ideal, the cost may not make sense for very small batches. Statistically sampling 10-25% could be a viable compromise.
Can prototypes be easily revised?
With careful design, subsequent versions can reuse most of the same components and PCB layout. Only update aspects needing improvement to avoid unnecessary costs.
0 Comments