Introduction to PCB Assembly for LED Applications
PCB (Printed Circuit Board) assembly is a crucial process in the manufacturing of LED (Light Emitting Diode) products. LED PCB Assembly involves the placement and soldering of electronic components, including LEDs, onto a printed circuit board. The assembled PCB forms the backbone of the LED product, providing electrical connectivity and mechanical support for the components.
LED applications have gained immense popularity due to their energy efficiency, long lifespan, and versatility. From lighting solutions to display systems and automotive applications, LEDs have revolutionized various industries. To ensure the optimal performance and reliability of LED products, it is essential to partner with a professional LED PCB assembly supplier.
The Importance of Choosing a Professional LED PCB Assembly Supplier
When it comes to LED PCB assembly, choosing a professional and experienced supplier is of utmost importance. A professional LED PCB assembly supplier possesses the expertise, state-of-the-art equipment, and stringent quality control measures necessary to deliver high-quality assemblies consistently. Here are some key reasons why selecting a professional supplier is crucial:
-
Quality Assurance: Professional LED PCB assembly suppliers adhere to strict quality standards and employ rigorous testing procedures to ensure the assembled PCBs meet the required specifications. They invest in advanced inspection systems, such as automated optical inspection (AOI) and X-ray inspection, to detect and rectify any defects or anomalies in the assembly process.
-
Technical Expertise: LED PCB assembly requires specialized knowledge and skills. Professional suppliers have a team of experienced engineers and technicians who possess in-depth understanding of LED technology, PCB design, and assembly techniques. They can provide valuable insights and recommendations to optimize the design and manufacturing process, resulting in improved product performance and reliability.
-
Advanced Equipment and Facilities: Professional LED PCB assembly suppliers invest in state-of-the-art equipment and maintain clean, controlled manufacturing environments. They utilize high-precision pick-and-place machines, reflow ovens, and soldering systems to ensure accurate component placement and reliable solder joints. Additionally, they have dedicated ESD (Electrostatic Discharge) protection measures in place to prevent damage to sensitive electronic components.
-
Scalability and Flexibility: LED PCB assembly requirements can vary widely depending on the application and production volume. Professional suppliers have the capability to handle both small-scale prototyping and large-scale production runs efficiently. They can adapt to changes in design or demand, offering flexibility to meet evolving customer needs.
-
Supply Chain Management: Professional LED PCB assembly suppliers have established relationships with reliable component manufacturers and distributors. They can source high-quality components, manage inventory, and ensure timely delivery of materials. This streamlined supply chain management minimizes lead times and reduces the risk of component shortages or delays.
-
Cost-Effectiveness: While cost is an important consideration, focusing solely on the lowest price can compromise quality and reliability. Professional LED PCB assembly suppliers strike a balance between cost-effectiveness and maintaining high standards. They employ efficient processes, utilize economies of scale, and implement cost-saving measures without sacrificing quality.
The LED PCB Assembly Process
The LED PCB assembly process involves several critical steps that ensure the proper functionality and reliability of the final product. Let’s take a closer look at each stage of the assembly process:
-
PCB Design and Fabrication:
The LED PCB assembly process begins with the design and fabrication of the printed circuit board. The PCB design takes into account factors such as component placement, signal integrity, thermal management, and manufacturability. Once the design is finalized, the PCB is fabricated using high-quality materials and advanced manufacturing techniques. -
Solder Paste Printing:
Solder paste, a mixture of tiny solder particles and flux, is precisely applied onto the PCB’s surface using a stencil or screen printing process. The solder paste is deposited on the designated pads where the electronic components will be placed. -
Component Placement:
Using automated pick-and-place machines, the electronic components, including LEDs, resistors, capacitors, and integrated circuits, are accurately placed onto the PCB. These machines use vision systems and precise positioning mechanisms to ensure the correct placement of each component. -
Reflow Soldering:
After component placement, the PCB undergoes a reflow soldering process. The assembly is heated in a controlled manner, typically using a reflow oven. The solder paste melts and forms a strong electrical and mechanical bond between the components and the PCB pads. -
Inspection and Testing:
Once the soldering process is complete, the assembled PCB undergoes thorough inspection and testing. Automated optical inspection (AOI) systems are used to detect any missing components, misalignments, or soldering defects. Additionally, functional testing is performed to verify the proper operation of the LED PCB assembly. -
Cleaning and Conformal Coating:
If required, the assembled PCB may undergo cleaning to remove any residual flux or contaminants. Conformal coating, a protective layer applied to the PCB surface, can be used to enhance the assembly’s resistance to moisture, dust, and other environmental factors. -
Final Assembly and Packaging:
The LED PCB assembly is then integrated into the final product or enclosure. Any necessary wiring, connectors, or additional components are attached. Finally, the product is packaged and prepared for shipment to the customer.
Throughout the LED PCB assembly process, strict quality control measures are implemented to ensure consistency and reliability. Professional LED PCB assembly suppliers adhere to industry standards and employ best practices to deliver high-quality assemblies that meet customer requirements.
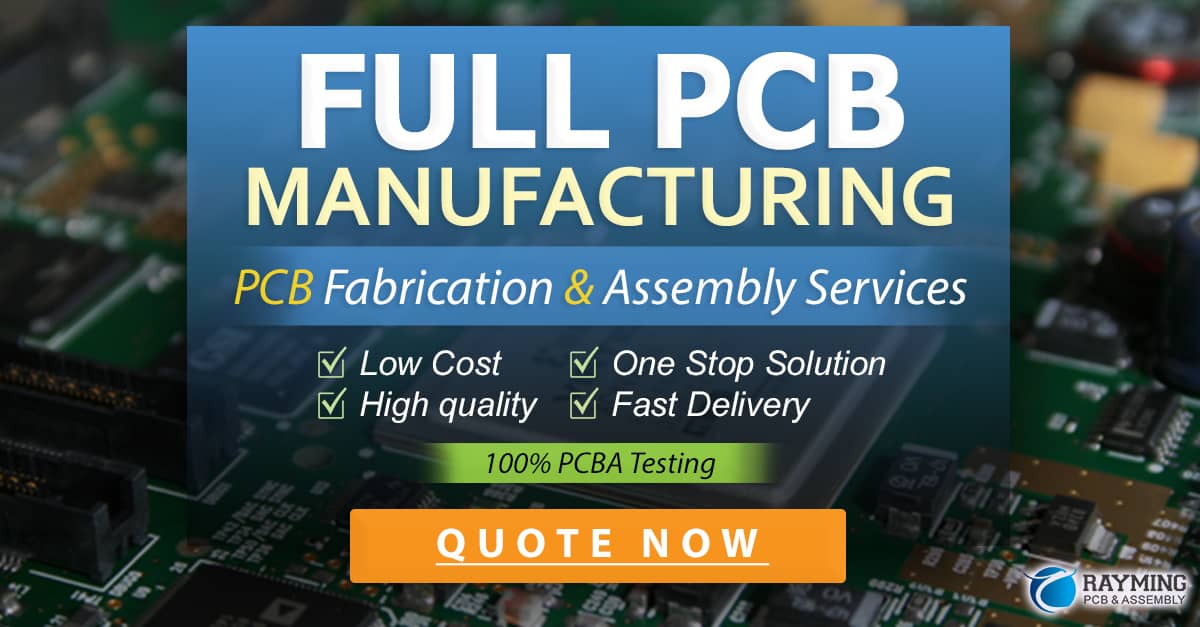
Choosing the Right LED PCB Assembly Supplier
When selecting an LED PCB assembly supplier, it is essential to consider several key factors to ensure a successful partnership. Here are some important criteria to evaluate:
-
Technical Capabilities:
Assess the supplier’s technical expertise and experience in LED PCB assembly. Look for a supplier with a proven track record of successfully completing projects similar to yours. Consider their knowledge of LED technology, PCB design, and assembly techniques. -
Quality Management System:
Ensure that the supplier has a robust quality management system in place. ISO certifications, such as ISO 9001, demonstrate the supplier’s commitment to quality and adherence to international standards. Inquire about their quality control processes, inspection methods, and testing procedures. -
Manufacturing Facilities and Equipment:
Evaluate the supplier’s manufacturing facilities and equipment. Look for state-of-the-art production lines, automated pick-and-place machines, reflow ovens, and inspection systems. Well-maintained and modern facilities indicate the supplier’s investment in technology and their ability to deliver consistent quality. -
Scalability and Flexibility:
Consider the supplier’s capacity to handle your production requirements, both in terms of volume and complexity. Assess their ability to scale production as your needs grow and their flexibility to accommodate changes in design or demand. -
Supply Chain Management:
Investigate the supplier’s supply chain management capabilities. Ensure they have reliable relationships with component manufacturers and distributors to ensure a stable supply of high-quality components. Inquire about their inventory management practices and their ability to meet delivery deadlines. -
Customer Support and Communication:
Evaluate the supplier’s customer support and communication channels. Look for a supplier that is responsive, proactive, and maintains open lines of communication throughout the project. Consider their ability to provide technical support, address concerns, and collaborate effectively. -
Cost and Value:
While cost is an important consideration, it should not be the sole determining factor. Evaluate the supplier’s pricing in relation to the value they provide. Consider factors such as quality, reliability, technical expertise, and overall service. Strike a balance between cost-effectiveness and ensuring the long-term success of your LED PCB assembly project. -
Reputation and References:
Research the supplier’s reputation in the industry. Look for customer testimonials, case studies, and references from companies with similar requirements. Reach out to their existing clients to gather feedback on their experience working with the supplier.
By carefully evaluating these criteria and conducting thorough due diligence, you can select a professional LED PCB assembly supplier that aligns with your specific needs and goals. Building a strong partnership with a reliable supplier is crucial for the success of your LED products.
Benefits of Professional LED PCB Assembly
Partnering with a professional LED PCB assembly supplier offers numerous benefits that contribute to the success and competitiveness of your LED products. Here are some key advantages:
-
Enhanced Product Quality:
Professional LED PCB assembly suppliers adhere to strict quality standards and employ rigorous testing procedures. They utilize advanced inspection systems, such as automated optical inspection (AOI) and X-ray inspection, to detect and rectify any defects or anomalies in the assembly process. This ensures that the assembled PCBs meet the highest quality standards, resulting in enhanced product performance and reliability. -
Faster Time-to-Market:
By leveraging the expertise and efficiency of a professional LED PCB assembly supplier, you can significantly reduce your product development and production timelines. Suppliers have streamlined processes, automated equipment, and experienced personnel that enable them to complete assembly projects quickly and accurately. This faster time-to-market allows you to respond to market demands and gain a competitive edge. -
Cost Savings:
Professional LED PCB assembly suppliers have economies of scale and efficient manufacturing processes that can result in cost savings for your business. They can optimize material usage, minimize waste, and leverage their purchasing power to secure components at competitive prices. Additionally, their expertise in design for manufacturability (DFM) can help identify cost-saving opportunities without compromising quality. -
Access to Advanced Technology:
Professional LED PCB assembly suppliers invest in state-of-the-art equipment and stay updated with the latest advancements in LED technology. By partnering with them, you gain access to cutting-edge manufacturing capabilities, such as high-precision pick-and-place machines, reflow ovens, and advanced inspection systems. This ensures that your LED products are assembled using the most advanced techniques and technologies available. -
Scalability and Flexibility:
Professional LED PCB assembly suppliers have the capacity and flexibility to accommodate varying production volumes and design requirements. Whether you need small-scale prototyping or large-scale production runs, they can adapt to your needs efficiently. They can also handle changes in design or demand, providing the flexibility necessary to respond to market dynamics and customer preferences. -
Technical Expertise and Support:
Professional LED PCB assembly suppliers have a team of experienced engineers and technicians who possess in-depth knowledge of LED technology, PCB design, and assembly processes. They can provide valuable technical guidance and support throughout the entire project lifecycle. From design optimization to troubleshooting and performance enhancements, their expertise can help you overcome challenges and achieve optimal results. -
Risk Mitigation:
Partnering with a professional LED PCB assembly supplier helps mitigate various risks associated with the manufacturing process. They have established quality control measures, reliable supply chain networks, and contingency plans in place to minimize the impact of potential issues. Their expertise in handling complex assembly projects and their ability to deliver consistent quality reduce the chances of costly errors or delays. -
Focus on Core Competencies:
By outsourcing LED PCB assembly to a professional supplier, you can focus on your core competencies, such as product design, marketing, and customer support. This allows you to allocate your resources effectively and concentrate on areas that drive business growth and innovation. Leaving the assembly process to experts enables you to streamline your operations and improve overall efficiency.
By leveraging the benefits of professional LED PCB assembly, you can enhance the quality, reliability, and competitiveness of your LED products. Partnering with a reputable and experienced supplier ensures that your products meet the highest standards and exceed customer expectations.
Quality Assurance in LED PCB Assembly
Quality assurance is a critical aspect of LED PCB assembly, as it directly impacts the performance, reliability, and safety of the final product. Professional LED PCB assembly suppliers employ stringent quality control measures throughout the entire manufacturing process to ensure that the assembled PCBs meet the required specifications and standards. Here are some key quality assurance practices in LED PCB assembly:
-
Incoming Material Inspection (IMI):
Before the assembly process begins, all incoming materials, including PCBs, components, and solder paste, undergo thorough inspection. The supplier verifies the quality, authenticity, and conformity of the materials to the specified requirements. This initial inspection helps prevent defective or counterfeit components from entering the assembly process. -
Process Control and Monitoring:
Throughout the LED PCB assembly process, various parameters and conditions are closely monitored and controlled. This includes solder paste printing, component placement, reflow soldering, and cleaning. Automated systems, sensors, and statistical process control (SPC) techniques are used to ensure that each step of the assembly process is performed within the specified tolerances and guidelines. -
Automated Optical Inspection (AOI):
AOI systems are widely used in LED PCB assembly for detecting surface-level defects and anomalies. These systems utilize high-resolution cameras and advanced image processing algorithms to inspect the assembled PCBs for missing components, misalignments, solder bridges, and other visual defects. AOI helps identify and rectify issues early in the assembly process, reducing the chances of defective products reaching the next stages. -
X-Ray Inspection:
For complex LED PCB assemblies with hidden or obscured solder joints, X-ray inspection is employed. X-ray systems provide a non-destructive means to examine the integrity of solder joints, detect voids, and identify any internal defects. This inspection method is particularly useful for BGAs (Ball Grid Arrays) and other high-density component packages. -
Functional Testing:
After the assembly process, the LED PCBs undergo functional testing to verify their electrical and operational performance. This may include power-on testing, LED functionality checks, and other application-specific tests. Functional testing ensures that the assembled PCBs meet the desired specifications and operate as intended. -
Environmental Testing:
Depending on the end-use application and customer requirements, LED PCBs may undergo environmental testing to assess their durability and reliability under various conditions. This can include temperature cycling, humidity testing, vibration testing, and other stress tests. Environmental testing helps identify potential weaknesses or failure modes and ensures the PCBs can withstand the intended operating conditions. -
Traceability and Documentation:
Professional LED PCB assembly suppliers maintain detailed traceability and documentation throughout the manufacturing process. Each PCB is assigned a unique identifier, and records are kept for material lot numbers, process parameters, inspection results, and test data. This traceability allows for quick identification and resolution of any issues that may arise, as well as facilitates root cause analysis and continuous improvement efforts. -
Continuous Improvement:
Quality assurance in LED PCB assembly is an ongoing process. Professional suppliers continuously monitor and analyze quality metrics, customer feedback, and process data to identify areas for improvement. They implement corrective and preventive actions (CAPA) to address any identified issues and strive for continuous improvement in their processes, equipment, and personnel training.
By implementing robust quality assurance practices, professional LED PCB assembly suppliers ensure that the assembled PCBs meet the highest standards of quality, reliability, and performance. These practices instill confidence in customers and help establish long-term partnerships built on trust and mutual success.
Industry Standards and Certifications in LED PCB Assembly
Adhering to industry standards and certifications is crucial for professional LED PCB assembly suppliers to demonstrate their commitment to quality, reliability, and best practices. These standards and certifications provide a framework for consistent and efficient manufacturing processes, ensuring that the assembled PCBs meet the required specifications and customer expectations. Here are some key industry standards and certifications relevant to LED PCB assembly:
-
ISO 9001 – Quality Management System:
ISO 9001 is an internationally recognized standard for quality management systems. It provides a framework for organizations to establish, document, and continuously improve their processes to meet customer and regulatory requirements. LED PCB assembly suppliers certified to ISO 9001 demonstrate their commitment to quality, customer satisfaction, and continuous improvement. -
IPC Standards:
IPC (Association Connecting Electronics Industries) is a global trade association that develops and publishes standards for the electronics industry, including PCB assembly. Some relevant IPC standards for LED PCB assembly include: - IPC-A-610: Acceptability of Electronic Assemblies
- IPC-J-STD-001: Requirements for Soldered Electrical and Electronic Assemblies
-
IPC-7711/7721: Rework, Modification, and Repair of Electronic Assemblies
Compliance with IPC standards ensures that the LED PCB assembly processes adhere to industry-recognized guidelines for quality, workmanship, and reliability. -
UL (Underwriters Laboratories) Certification:
UL is a global safety certification company that sets standards for product safety and performance. LED PCB assemblies used in lighting applications may require UL certification to ensure they meet specific safety requirements. UL certification demonstrates that the assembled PCBs have been tested and comply with the relevant safety standards, such as UL 8750 for LED equipment. -
RoHS (Restriction of Hazardous Substances) Compliance:
The RoHS directive restricts the use of certain hazardous substances in electrical and electronic equipment. LED PCB assembly suppliers must ensure that the materials and components used in the assembly process comply with RoHS requirements. This involves selecting RoHS-compliant components, managing material declarations, and implementing appropriate manufacturing processes to prevent contamination. -
ESD (Electrostatic Discharge) Control:
LED components and PCBs are sensitive to electrostatic discharge, which can cause damage or performance issues. Professional LED PCB assembly suppliers implement ESD control measures in accordance with standards such as ANSI/ESD S20.20. This includes using ESD-safe workstations, grounding equipment, and personnel training to minimize the
0 Comments