What is a Printing Wiring Board (PWB)?
A Printing Wiring Board, or PWB, is a thin board made of insulating materials, such as fiberglass or plastic, with conductive pathways printed or etched onto its surface. These pathways, known as traces or tracks, are designed to connect various electronic components, such as resistors, capacitors, and integrated circuits (ICs), to create a functional electronic circuit.
PWBs come in various sizes, shapes, and complexity levels, depending on the specific application and the number of layers required. They can range from simple single-layer boards to complex multi-layer boards with intricate designs and high component density.
History of Printing Wiring Boards
The concept of PWBs dates back to the early 20th century when the first patent for a printed circuit was filed by Albert Hanson in 1903. However, it wasn’t until the 1940s that PWBs gained widespread adoption, primarily driven by the needs of the military and aerospace industries.
During World War II, the U.S. military required reliable and compact electronic systems for their equipment, such as radios and radar systems. PWBs offered a solution by providing a more compact and reliable alternative to traditional point-to-point wiring. The first mass-produced PWBs were used in proximity fuses for anti-aircraft shells, which played a crucial role in the war effort.
In the post-war era, the demand for consumer electronics grew rapidly, and PWBs became an essential component in the manufacturing process. The introduction of through-hole technology in the 1950s and surface-mount technology (SMT) in the 1980s further revolutionized the industry, enabling the production of smaller, more complex, and cost-effective electronic devices.
Manufacturing Process of PWBs
The manufacturing process of PWBs involves several stages, each requiring precise control and attention to detail. The main steps in the PWB manufacturing process are as follows:
- Design and Layout
- Substrate Preparation
- Copper Cladding
- Photoresist Application
- Exposure and Development
- Etching
- Drill and Plating
- Solder Mask and Silkscreen
- Surface Finish
- Quality Control and Testing
1. Design and Layout
The PWB manufacturing process begins with the design and layout of the Circuit Board. Engineers use specialized software, such as Electronic Design Automation (EDA) tools, to create a digital representation of the board, including the placement of components, routing of traces, and the creation of solder pads.
The design process takes into account various factors, such as signal integrity, power distribution, thermal management, and manufacturability. Once the design is finalized, the digital files are sent to the PWB manufacturer for production.
2. Substrate Preparation
The substrate, or base material, of a PWB is typically made of fiberglass-reinforced epoxy resin, known as FR-4. Other materials, such as polyimide or ceramic, may be used for specialized applications that require higher temperature resistance or better electrical properties.
The substrate is cut to the desired size and shape using precise machinery, such as CNC routers or Laser Cutters. The surface of the substrate is then cleaned and prepared for the subsequent steps in the manufacturing process.
3. Copper Cladding
A thin layer of copper foil is laminated onto the surface of the substrate using heat and pressure. The copper foil serves as the conductive layer for the traces and pads on the PWB. The thickness of the copper foil can vary depending on the specific requirements of the board, with typical thicknesses ranging from 0.5 oz to 2 oz per square foot.
For multi-layer PWBs, additional layers of substrate and copper foil are laminated together, with insulating materials placed between the layers to prevent short circuits.
4. Photoresist Application
A photoresist, a light-sensitive polymer, is applied to the surface of the copper-clad substrate. The photoresist can be applied using various methods, such as spin coating, roller coating, or dry film lamination. The purpose of the photoresist is to create a protective layer that will define the desired pattern of traces and pads on the PWB.
5. Exposure and Development
The photoresist-coated substrate is then exposed to ultraviolet (UV) light through a photomask, which contains the negative image of the desired circuit pattern. The UV light causes the exposed areas of the photoresist to polymerize and become resistant to the subsequent developing solution.
After exposure, the board is immersed in a developing solution that removes the unexposed areas of the photoresist, revealing the copper layer beneath. This process creates a positive image of the circuit pattern on the copper surface.
6. Etching
The exposed copper areas are then etched away using a chemical solution, typically ferric chloride or ammonium persulfate. The etching process removes the unwanted copper, leaving behind only the desired traces and pads protected by the polymerized photoresist.
After etching, the remaining photoresist is stripped away using a solvent, revealing the final copper circuit pattern on the substrate.
7. Drill and Plating
Holes are drilled through the PWB at specific locations to accommodate through-hole components or to create vias that connect different layers in multi-layer boards. The drilling process is performed using high-speed, computer-controlled drill machines that ensure precise hole placement and size.
After drilling, the holes are plated with copper to create electrical connections between layers and to provide a surface for soldering components. The copper plating process involves several steps, including electroless copper deposition and electrolytic copper plating.
8. Solder Mask and Silkscreen
A solder mask, typically a green or blue polymer, is applied to the surface of the PWB, covering the copper traces and pads. The solder mask serves two primary purposes: it protects the copper from oxidation and prevents solder bridges from forming between adjacent pads during the soldering process.
Silkscreen, a white or yellow ink, is then applied to the surface of the solder mask to create labels, logos, and component designators. The silkscreen helps in the assembly process and provides a visual reference for the placement of components on the board.
9. Surface Finish
A surface finish is applied to the exposed copper pads to protect them from oxidation and to enhance the solderability of the board. Common surface finishes include Hot Air Solder Leveling (HASL), Organic Solderability Preservative (OSP), Electroless Nickel Immersion Gold (ENIG), and Immersion Silver.
The choice of surface finish depends on the specific requirements of the application, such as the type of components being used, the expected shelf life of the board, and the environmental conditions the board will be exposed to.
10. Quality Control and Testing
Throughout the manufacturing process, various quality control measures are implemented to ensure the consistency and reliability of the PWBs. These measures include:
- Visual inspection: Automated optical inspection (AOI) systems and manual visual inspection are used to identify defects, such as missing components, solder bridges, or incorrect component placement.
- Electrical testing: Flying probe tests and boundary scan tests are performed to verify the electrical continuity and functionality of the board.
- Environmental testing: PWBs may be subjected to temperature cycling, humidity testing, or vibration testing to ensure their robustness and reliability under various operating conditions.
Once the PWBs have passed all quality control checks, they are packaged and shipped to the customer for final assembly and integration into the end product.
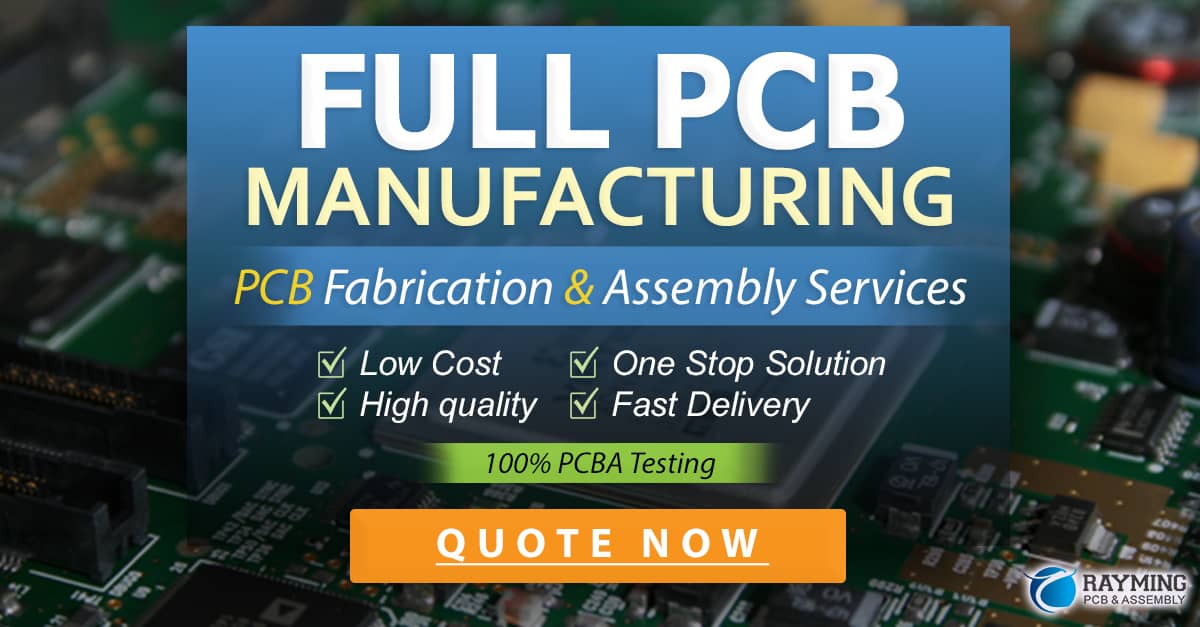
Applications of PWBs
PWBs find applications in a wide range of industries and products, from consumer electronics to aerospace and defense systems. Some common applications include:
- Consumer Electronics
- Smartphones and tablets
- Laptops and desktop computers
- Televisions and home entertainment systems
-
Wearable devices and smart appliances
-
Automotive Electronics
- Engine control units (ECUs)
- Infotainment systems
- Advanced driver assistance systems (ADAS)
-
Electric vehicle power electronics
-
Industrial Automation and Control
- Programmable logic controllers (PLCs)
- Human-machine interfaces (HMIs)
- Sensors and actuators
-
Power electronics and motor drives
-
Medical Devices
- Diagnostic imaging equipment
- Patient monitoring systems
- Implantable devices and wearable health monitors
-
Laboratory instruments and analyzers
-
Aerospace and Defense
- Avionics systems
- Radar and communication equipment
- Satellite and spacecraft electronics
-
Military-grade computers and devices
-
Telecommunications
- Network switches and routers
- Wireless base stations and infrastructure
- Fiber optic transmission equipment
- Satellite communication systems
The versatility and reliability of PWBs have made them indispensable in the modern world, enabling the development of increasingly complex and sophisticated electronic systems.
Future Trends in PWB Technology
As electronic devices continue to advance and become more complex, PWB technology must evolve to keep pace with the demands of the industry. Some of the key trends shaping the future of PWBs include:
- Miniaturization and High-Density Interconnect (HDI)
- Smaller component sizes and tighter packaging requirements drive the need for higher-density PWBs with finer trace widths and smaller via sizes.
-
HDI technology, which involves the use of micro-vias and buried/blind vias, enables the creation of highly compact and complex PWBs.
-
Advanced Materials
- The development of new substrate materials, such as high-frequency laminates and low-loss dielectrics, enables PWBs to support higher signal speeds and frequencies.
-
The use of flexible and stretchable substrates, such as polyimide or thermoplastic polyurethane (TPU), allows for the creation of flexible and conformable PWBs for wearable devices and other applications.
-
Embedded Components
- The integration of passive components, such as resistors and capacitors, directly into the PWB substrate helps to reduce the overall size and improve the performance of electronic systems.
-
Active components, such as ICs and sensors, can also be embedded into the PWB, enabling the creation of highly integrated and multifunctional boards.
-
3D Printing and Additive Manufacturing
- The use of 3D printing technologies, such as inkjet printing and aerosol jet printing, allows for the rapid prototyping and low-volume production of PWBs.
-
Additive manufacturing techniques enable the creation of complex, three-dimensional PWB structures and the integration of novel materials and functionalities.
-
Environmental Sustainability
- The push for eco-friendly and sustainable electronics is driving the development of PWBs made from renewable and biodegradable materials, such as paper-based substrates and bioplastics.
- The use of lead-free solders and the reduction of hazardous substances in PWB manufacturing processes help to minimize the environmental impact of electronic waste.
As these trends continue to shape the PWB industry, we can expect to see increasingly innovative and advanced circuit board solutions that enable the development of smarter, more efficient, and more sustainable electronic devices.
Frequently Asked Questions (FAQ)
- What is the difference between a PWB and a PCB?
-
PWB (Printing Wiring Board) and PCB (Printed Circuit Board) are essentially the same things. Both terms refer to a board that provides electrical connections between electronic components. PWB is an older term that was more commonly used in the past, while PCB is the more modern and widely used term today.
-
What are the different types of PWBs?
-
There are several types of PWBs, including:
- Single-layer PWBs: These boards have conductive traces on only one side of the substrate.
- Double-layer PWBs: These boards have conductive traces on both sides of the substrate.
- Multi-layer PWBs: These boards consist of three or more layers of conductive traces, separated by insulating layers.
- Flexible PWBs: These boards are made from flexible materials, such as polyimide, and can bend or conform to various shapes.
- Rigid-flex PWBs: These boards combine rigid and flexible sections, allowing for the creation of complex, three-dimensional structures.
-
What materials are used to make PWBs?
-
The most common base material for PWBs is FR-4, a fiberglass-reinforced epoxy resin. Other materials include polyimide, which is used for high-temperature and flexible applications, and ceramic, which is used for high-frequency and high-power applications. The conductive traces on PWBs are typically made of copper, while the solder mask and silkscreen are made from polymer-based inks.
-
How are components mounted on PWBs?
-
There are two primary methods for mounting components on PWBs:
- Through-hole mounting: Components with long leads are inserted through holes drilled in the PWB and soldered to pads on the opposite side.
- Surface-mount technology (SMT): Components with small, flat contacts are placed directly onto pads on the surface of the PWB and soldered in place.
-
What is the role of solder mask on a PWB?
- The solder mask is a protective layer applied to the surface of a PWB, covering the copper traces and pads. It serves two main purposes:
- Protection: The solder mask protects the copper from oxidation and mechanical damage.
- Solder control: The solder mask prevents solder from bridging between adjacent pads during the soldering process, which could cause short circuits.
The solder mask is typically green or blue in color and is applied using a screen-printing or photoimaging process. Openings in the solder mask expose the pads where components will be soldered.
In conclusion, Printing Wiring Boards (PWBs) are essential components in modern electronics, providing a reliable and efficient means of interconnecting electronic components. The manufacturing process of PWBs involves several precise steps, from design and layout to etching, drilling, and plating. PWBs find applications in a wide range of industries, from consumer electronics to aerospace and defense, and are constantly evolving to meet the demands of increasingly complex and sophisticated electronic systems. As new technologies and materials emerge, we can expect to see even more advanced and innovative PWB solutions in the future.
0 Comments