Introduction to Polyimide PCB
Polyimide PCB (printed circuit board) is a type of high-performance circuit board that uses polyimide as the base material instead of the more common FR-4 (flame retardant-4). Polyimide is a synthetic polymer known for its exceptional thermal stability, mechanical strength, and chemical resistance. These properties make polyimide PCBs an ideal choice for applications that demand reliability under extreme conditions.
What is Polyimide?
Polyimide is a polymer of imide monomers. It is a high-performance plastic that maintains its properties over a wide temperature range and has excellent chemical resistance. Polyimide films, such as DuPont’s Kapton, are used in various applications, including insulation for wires and cables, flexible electronics, and aerospace components.
Advantages of Polyimide PCB
Polyimide PCBs offer several advantages over traditional FR-4 PCBs:
- High thermal stability: Polyimide can withstand temperatures up to 400°C, making it suitable for high-temperature applications.
- Excellent mechanical strength: Polyimide has a high tensile strength and low coefficient of thermal expansion, which reduces the risk of warping and cracking.
- Chemical resistance: Polyimide is resistant to most chemicals, including acids, bases, and solvents.
- Low dielectric constant: Polyimide has a lower dielectric constant than FR-4, which reduces signal loss and improves high-frequency performance.
- Flexibility: Some types of polyimide PCBs are flexible, allowing for unique form factors and applications.
Types of Polyimide PCB
There are several types of polyimide PCBs, each with its own unique properties and applications.
Standard Polyimide PCB
Standard polyimide PCBs use a rigid polyimide base material, typically with a thickness of 0.005″ to 0.010″. They are manufactured using a process similar to that of FR-4 PCBs, with the polyimide material replacing the fiberglass substrate. Standard polyimide PCBs are suitable for applications that require high thermal stability and chemical resistance but do not need flexibility.
Flexible Polyimide PCB
Flexible polyimide PCBs, also known as Flex PCBs, use a thin, flexible polyimide film as the base material. The copper traces are attached to the polyimide film using an adhesive layer. Flex PCBs can be bent and folded, making them ideal for applications with limited space or that require dynamic flexing.
Types of Flexible Polyimide PCB
- Single-sided flex PCB: Copper traces are on one side of the polyimide film.
- Double-sided flex PCB: Copper traces are on both sides of the polyimide film, with through-hole connections.
- Multi-layer flex PCB: Multiple layers of polyimide film and copper traces are laminated together.
- Rigid-flex PCB: A combination of rigid and flexible sections, allowing for complex 3D shapes.
High-Frequency Polyimide PCB
High-frequency polyimide PCBs are designed for applications that operate at frequencies above 1 GHz. They use a low-loss polyimide material with a low dielectric constant and dissipation factor. High-frequency polyimide PCBs often incorporate advanced features, such as buried capacitance layers and edge-coupled differential pairs, to optimize signal integrity.
High-Density Interconnect (HDI) Polyimide PCB
HDI polyimide PCBs use microvias and fine-pitch traces to achieve higher component density and smaller form factors. They are manufactured using a build-up process, where layers of polyimide and copper are added sequentially. HDI polyimide PCBs are suitable for applications that require miniaturization, such as wearable electronics and implantable medical devices.
Applications of Polyimide PCB
Polyimide PCBs are used in a wide range of industries and applications, thanks to their unique properties and performance advantages.
Aerospace and Defense
Polyimide PCBs are extensively used in aerospace and defense applications due to their ability to withstand extreme temperatures, vibrations, and radiation. Some specific applications include:
- Satellite electronics: Polyimide PCBs can withstand the harsh conditions of space, including high radiation levels and extreme temperature fluctuations.
- Avionics: The high thermal stability and reliability of polyimide PCBs make them suitable for critical avionics systems, such as flight control and communication equipment.
- Missile guidance systems: Polyimide PCBs can withstand the high acceleration and vibration levels experienced during missile launches.
Automotive Electronics
The automotive industry is increasingly adopting polyimide PCBs for high-temperature and safety-critical applications, such as:
- Engine control units (ECUs): Polyimide PCBs can operate reliably in the high-temperature environment of an engine compartment.
- Electric vehicle battery management systems: The thermal stability and chemical resistance of polyimide PCBs make them suitable for monitoring and controlling lithium-ion battery packs.
- Automotive sensors: Polyimide PCBs are used in various automotive sensors, such as temperature, pressure, and exhaust gas sensors.
Medical Devices
Polyimide PCBs are used in medical devices that require biocompatibility, flexibility, and reliability, such as:
- Implantable devices: Flexible polyimide PCBs can be used in implantable devices, such as pacemakers and neurostimulators, thanks to their biocompatibility and ability to conform to body contours.
- Medical imaging equipment: High-frequency polyimide PCBs are used in medical imaging systems, such as MRI and ultrasound machines, to ensure high signal integrity and image quality.
- Wearable medical devices: Flexible polyimide PCBs are used in wearable medical devices, such as ECG monitors and insulin pumps, for their comfort and durability.
Industrial Electronics
Polyimide PCBs are used in industrial electronics that operate in harsh environments, such as:
- Oil and gas equipment: Polyimide PCBs can withstand the high temperatures and corrosive chemicals encountered in oil and gas exploration and processing.
- Power electronics: The high thermal stability of polyimide PCBs makes them suitable for power electronic applications, such as motor drives and inverters.
- Industrial sensors: Polyimide PCBs are used in industrial sensors that monitor temperature, pressure, and other parameters in harsh environments.
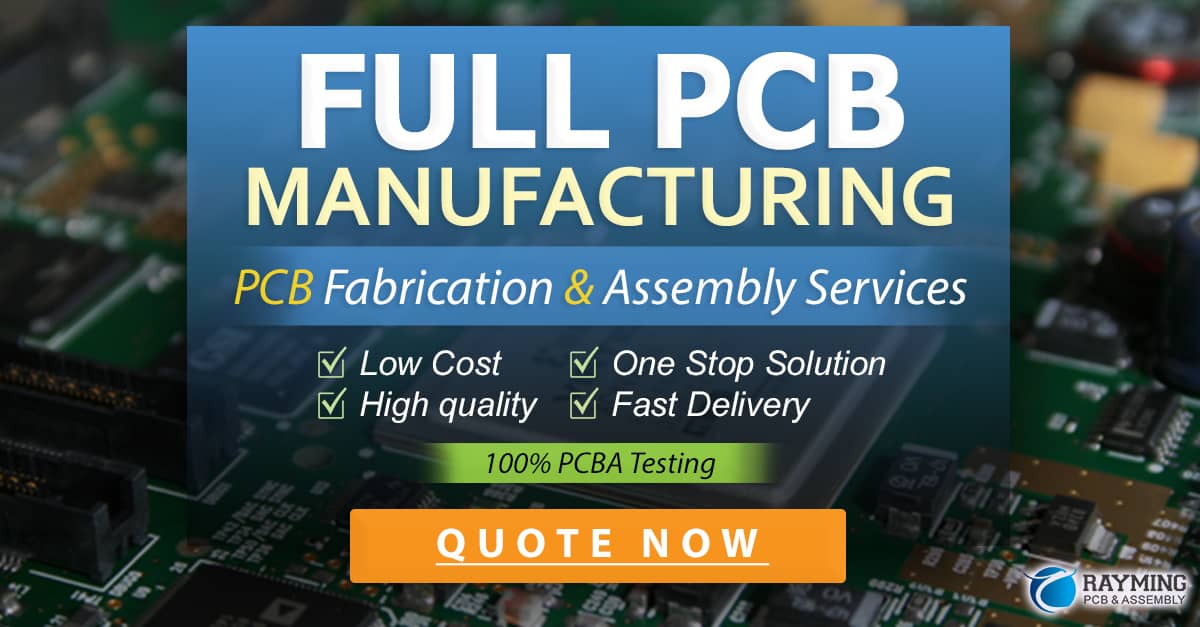
Benefits of Using Polyimide PCB
Using polyimide PCBs offers several benefits over traditional FR-4 PCBs:
- Increased reliability: The high thermal stability, mechanical strength, and chemical resistance of polyimide PCBs result in increased reliability and longer product lifetimes.
- Improved performance: The low dielectric constant and dissipation factor of polyimide materials enable better high-frequency performance and signal integrity.
- Space savings: Flexible and HDI polyimide PCBs allow for smaller form factors and higher component density, saving space in electronic devices.
- Cost reduction: Although polyimide PCBs may have a higher initial cost, their increased reliability and longer product lifetimes can result in lower total cost of ownership.
- Design flexibility: Flexible polyimide PCBs allow for unique form factors and 3D packaging, enabling innovative product designs.
Comparison of Polyimide PCB with Other PCB Materials
Here is a comparison table of polyimide PCB with other common PCB materials:
Property | Polyimide | FR-4 | Ceramics | Metal Core |
---|---|---|---|---|
Max Operating Temp (°C) | 400 | 130 | 1000 | 180 |
Dielectric Constant | 3.5 | 4.5 | 9.0 | N/A |
Dissipation Factor | 0.002 | 0.02 | 0.001 | N/A |
Thermal Conductivity (W/mK) | 0.2 | 0.3 | 20 | 2.2 |
Flexibility | Yes | No | No | No |
Cost | High | Low | High | Moderate |
As shown in the table, polyimide PCBs offer the highest operating temperature and flexibility among the compared materials. They also have a low dielectric constant and dissipation factor, which is beneficial for high-frequency applications. However, polyimide PCBs have a higher cost compared to FR-4, which is the most common PCB material.
FAQ
1. What is the maximum operating temperature of polyimide PCBs?
Polyimide PCBs can withstand temperatures up to 400°C, making them suitable for high-temperature applications.
2. Are polyimide PCBs flexible?
Some types of polyimide PCBs, such as flexible and rigid-flex PCBs, are designed to be flexible. This allows for unique form factors and applications that require dynamic flexing.
3. How do polyimide PCBs compare to FR-4 PCBs in terms of cost?
Polyimide PCBs generally have a higher initial cost compared to FR-4 PCBs. However, their increased reliability and longer product lifetimes can result in lower total cost of ownership in the long run.
4. Can polyimide PCBs be used in medical implants?
Yes, flexible polyimide PCBs can be used in implantable medical devices thanks to their biocompatibility and ability to conform to body contours.
5. What are the benefits of using high-frequency polyimide PCBs?
High-frequency polyimide PCBs offer better signal integrity and lower signal loss compared to FR-4 PCBs. They are designed for applications that operate at frequencies above 1 GHz and incorporate advanced features to optimize high-frequency performance.
Conclusion
Polyimide PCBs are a high-performance alternative to traditional FR-4 PCBs, offering exceptional thermal stability, mechanical strength, and chemical resistance. They are available in various types, including standard, flexible, high-frequency, and HDI, each with its own unique properties and applications.
Polyimide PCBs are widely used in industries such as aerospace, defense, automotive, medical, and industrial electronics, where reliability under extreme conditions is critical. Although they may have a higher initial cost compared to FR-4 PCBs, their increased reliability and longer product lifetimes can result in lower total cost of ownership.
As technology advances and the demand for high-performance electronics grows, polyimide PCBs will continue to play a crucial role in enabling innovative product designs and pushing the boundaries of what is possible in electronIC Packaging.
0 Comments