What are PLCC Packages?
PLCC stands for “Plastic Leaded Chip Carrier”. PLCC packages are a type of surface-mount integrated circuit package used for housing and connecting microchips and other electronic components. They consist of a plastic housing with metal leads or pins extending from the sides that are used to solder the package onto a printed circuit board (PCB).
Key Characteristics of PLCC Packages
PLCC packages have several defining characteristics:
- Plastic housing material
- Leads/pins on all four sides of the package
- Typically square or rectangular in shape
- Surface-mount design for PCB Assembly
- Available in various sizes and pin counts
The table below summarizes the common PLCC package sizes and their dimensions:
PLCC Package Size | Number of Pins | Package Dimensions (mm) |
---|---|---|
PLCC-20 | 20 | 8.89 x 8.89 x 4.57 |
PLCC-28 | 28 | 11.43 x 11.43 x 4.57 |
PLCC-44 | 44 | 16.51 x 16.51 x 4.57 |
PLCC-52 | 52 | 18.54 x 18.54 x 4.45 |
PLCC-68 | 68 | 24.89 x 24.89 x 4.45 |
PLCC-84 | 84 | 30.22 x 30.22 x 4.45 |
The plastic housing of PLCC packages provides protection for the delicate chip and bonding wires inside. The sideleads allow the package to be soldered directly to pads on the surface of a PCB, enabling a more compact assembly compared to through-hole mounting.
Advantages of Using PLCC Packages
Space Efficiency
One of the main benefits of PLCC packages is their space efficiency. The surface-mount design allows PLCCs to be soldered directly onto the PCB without the need for drilled holes. This enables tighter component spacing and more compact PCB layouts compared to through-hole packages.
The relatively high pin density of PLCC packages also contributes to their space efficiency. Smaller PLCC sizes like PLCC-20 and PLCC-28 are commonly used for housing microcontrollers, EEPROMs, and other small-scale ICs. Larger sizes like PLCC-68 and PLCC-84 provide ample connectivity for more complex chips while still maintaining a smaller footprint than comparable through-hole packages.
Mechanical Stability
The leads on all four sides of a PLCC package provide a strong mechanical connection to the PCB. When properly soldered, PLCCs offer good stability and resistance to mechanical stress and vibration. The plastic housing also helps protect the internal chip from physical damage.
However, due to their surface-mount nature, PLCC packages are more susceptible to thermal expansion mismatches between the package and PCB. Proper PCB design techniques, such as using thermal relief pads and minimizing component crowding, can help mitigate thermal stress issues.
Ease of Assembly
PLCC packages are well-suited for automated PCB assembly processes. The surface-mount design allows PLCCs to be easily picked and placed by machine. The leads are typically spaced with a 1.27 mm pitch, which provides sufficient room for solder joints while still enabling a compact layout.
However, hand soldering PLCCs can be more challenging than through-hole packages due to their small lead pitch and the need for precise alignment. Specialized soldering techniques, such as drag soldering or hot air reflow, are often used for manual assembly of PLCC packages.
PLCC Socket and Adapter Options
PLCC Sockets
PLCC sockets provide a way to mount PLCC packages onto a PCB without directly soldering the leads. The socket is soldered to the PCB and the PLCC package is inserted into the socket, allowing it to be easily removed or replaced as needed. DIP (Dual Inline Package) to PLCC adapter sockets are also available for prototyping and assembling PLCC packages in breadboard-style setups.
PLCC to DIP Adapters
For applications where a PLCC package needs to interface with through-hole components or be used in a breadboard, PLCC to DIP adapters are available. These adapters have a PLCC socket on one side and DIP pins on the other, allowing a PLCC package to be used in a through-hole environment.
PLCC to PGA Adapters
PGA (Pin Grid Array) to PLCC adapters provide a way to use PLCC packages in applications that require a PGA socket. These adapters have a PLCC socket on one side and a PGA pin layout on the other, allowing a PLCC package to interface with a PGA socket.
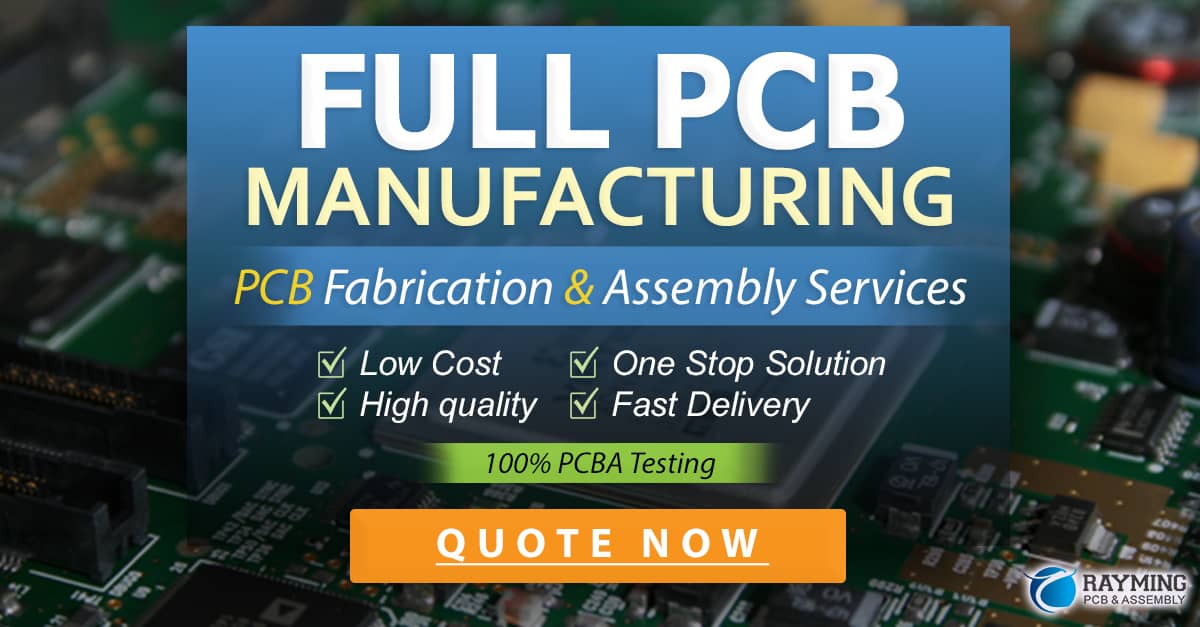
Common Applications of PLCC Packages
Microcontrollers and Microprocessors
Many microcontrollers and microprocessors are available in PLCC packages. The compact size and good pin density of PLCCs make them well-suited for these applications. Common examples include:
- 8-bit microcontrollers like the Microchip PIC16F series and Atmel AVR series
- 16-bit and 32-bit microcontrollers like the Microchip dsPIC series and some ARM Cortex-M devices
- Microprocessors like the Intel 8051 and Zilog Z80
Memory Devices
Various types of memory ICs are packaged in PLCCs, including:
- EEPROMs (Electrically Erasable Programmable Read-Only Memory)
- Flash memory
- Static RAM (SRAM)
- Mask ROM (Read-Only Memory)
The space efficiency and durability of PLCC packages make them a good choice for memory devices that need to be compact and reliable.
Interface and I/O Devices
PLCC packages are commonly used for interface and I/O devices such as:
- USB interface ICs
- Ethernet controllers
- LCD drivers
- UART and RS-232 interface chips
- Analog-to-digital converters (ADCs) and digital-to-analog converters (DACs)
The good pin density and small footprint of PLCCs allow these devices to be integrated into space-constrained designs.
Designing with PLCC Packages
When designing a PCB that uses PLCC packages, there are several factors to consider:
PCB Layout Considerations
- Ensure proper pad size and spacing for the specific PLCC package being used. Consult the device datasheet for recommended footprint dimensions.
- Provide adequate clearance around the PLCC package for soldering and inspection.
- Use thermal relief pads or spokes to minimize thermal stress on the solder joints.
- Follow good PCB layout practices to minimize noise and crosstalk, such as proper grounding and power plane usage.
Soldering Considerations
- Use solder paste and stencils for automated assembly of PLCC packages.
- For hand soldering, use a fine-tipped soldering iron and apply heat evenly to the leads and pads.
- Inspect solder joints for proper wetting and fillets. Use a magnifying lens to check for shorts or incomplete joints.
- Clean flux residue from the PCB after soldering to prevent corrosion or contamination.
Thermal Management
- Consider the power dissipation and thermal characteristics of the PLCC device being used.
- Provide adequate copper pours or heatsinks for high-power devices to dissipate heat.
- Use thermal vias or Thermal Pads under the PLCC package to transfer heat to inner layers or the opposite side of the PCB.
PLCC Package Handling and Storage
Proper handling and storage of PLCC packages is important to prevent damage and ensure reliable operation:
- Use ESD (electrostatic discharge) safe handling procedures when working with PLCC packages. This includes wearing grounded wrist straps and using ESD-safe workstations and storage containers.
- Avoid touching the leads of the PLCC package directly. Handle the package by the edges or use vacuum pens designed for surface-mount components.
- Store unused PLCC packages in moisture-resistant packaging, such as moisture barrier bags with desiccant packs. Moisture can cause damage to the package during reflow soldering.
- Follow the manufacturer’s recommended storage conditions, including temperature and humidity ranges, to prevent deterioration of the package and its internal components.
Frequently Asked Questions (FAQ)
Q: Can PLCC packages be replaced if they are soldered onto a PCB?
A: Yes, PLCC packages can be replaced using hot air rework or desoldering tools. However, the process requires care and precision to avoid damaging the PCB or surrounding components. It is often easier to use a PLCC socket for applications that require frequent chip swapping.
Q: Are PLCC packages obsolete?
A: While PLCC packages are not as widely used as they once were, they are still available and used in many applications. Some newer package types, such as QFP (Quad Flat Pack) and BGA (Ball Grid Array), have become more popular for high-density and high-speed designs. However, PLCCs remain a viable choice for many applications due to their simplicity, durability, and relatively low cost.
Q: Can PLCC packages be used in high-speed designs?
A: PLCC packages can be used in high-speed designs, but care must be taken to minimize parasitic inductance and capacitance in the PCB layout. The lead length and spacing of PLCCs can limit their performance at very high frequencies compared to more advanced package types like BGA. Proper PCB layout techniques, such as minimizing trace lengths and using ground planes, can help optimize high-speed performance with PLCC packages.
Q: Are there any special requirements for soldering PLCC packages?
A: Soldering PLCC packages requires a steady hand and precise temperature control. A fine-tipped soldering iron or hot air rework station is recommended for hand soldering. Solder paste and a reflow oven are typically used for automated assembly. It is important to use the correct temperature profile and to not overheat the package, as this can cause damage to the plastic housing or internal components.
Q: Can PLCC packages be used with surface-mount or through-hole components?
A: PLCC packages are designed for surface-mount assembly, but they can be used with through-hole components using PLCC to DIP adapters. These adapters allow a PLCC package to be plugged into a standard DIP socket or soldered into through-holes on a PCB. However, using adapters may increase the overall height and footprint of the assembly compared to using a pure surface-mount design.
0 Comments