Introduction to PCBA Contract Manufacturing
Printed circuit board assembly (PCBA) manufacturing involves assembling electronic components onto printed circuit boards (PCBs) to produce functioning circuit boards. Many companies choose to outsource PCBA production to contract manufacturing partners rather than manufacture in-house.
PCBA contract manufacturing provides numerous benefits, including:
- Access to advanced manufacturing expertise and capabilities
- Flexibility to scale production up and down
- Cost savings from avoiding capital expenditure on equipment
- Faster time-to-market by leveraging existing infrastructure
This comprehensive guide covers key aspects of PCBA contract manufacturing, from selecting the right partner to navigating the production process.
Finding the Right PCBA Contract Manufacturer
Selecting the right contract manufacturing partner is crucial for getting high-quality boards produced on time and on budget. Here are key factors to evaluate:
Technical Capabilities
- Equipment: Look for SMT lines with the latest mounters, printers, AOIs, testers, etc. This ensures the ability to assemble advanced PCBs.
- Materials: Partner should have experience with various solder types, substrates, components including 01005 passives, 0.4mm pitch ICs, etc.
- Process expertise: Look for expertise in complex assembly processes like chip-on-board, flip chip, embedded components, etc.
Quality Systems
- Certifications: ISO 9001, IATF 16949, AS9100 certifications indicate robust quality systems.
- Process controls: Stringent process controls like automated optical inspection (AOI), in-circuit test (ICT), functional test (FCT), etc. ensure quality.
- Traceability: End-to-end component traceability systems prevent counterfeit components.
Supply Chain Capability
- Procurement: Ability to procure long lead time and shortage components through global networks.
- Inventory: Just-in-time inventory systems prevent material stock-outs during production.
- Logistics: Smooth customs clearance capability speeds up export/import of materials.
Program Management
- Customer focus: Dedicated program managers provide white-glove service.
- Communication: Regular project updates through the production cycle.
- Continuous improvement: Willingness to improve processes based on feedback.
Company Heritage & Finance
- Years in business: Look for long, proven track records of contract manufacturing.
- Financial health: Review financial statements to ensure company stability.
The PCBA Manufacturing Process
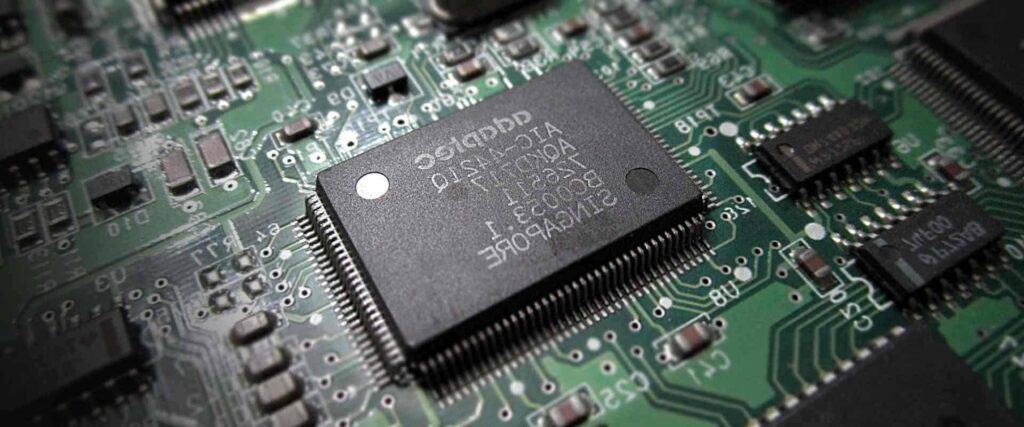
PCBA production involves complex processes requiring close coordination between engineering, procurement, assembly, and test teams. Here are key phases:
Engineering Support
The contract manufacturer’s engineers support design-for-manufacturing (DFM) analysis and design reviews early in the design cycle to optimize manufacturing success. They provide feedback on:
- Component selection
- Placement for manufacturability
- Test point insertion
They also create assembly drawings, bill of materials, fabrication and assembly documentation required for production.
Supply Chain Management
The procurement team sources components and materials needed for production based on the bill of materials (BOM). They manage long lead time, hard-to-find, and obsolete parts. Strategic inventory management ensures no material shortages to avoid production delays.
SMT Assembly
Surface mount technology (SMT) assembly involves:
- Solder Paste Printing: Solder paste is printed on PCB pads where components will be mounted.
- Component Placement: Surface mount components are accurately placed onto the pads using automated pick-and-place machines.
- Reflow Soldering: The PCB passes through ovens melting the solder paste and attaching components.
Automated optical inspection (AOI) validates component placement and solder joint integrity.
Through Hole Assembly
Some components like connectors and power devices are inserted into plated through-holes in the board. This may involve:
- Wave soldering
- Manual insertion and soldering
- Selective soldering
AOI validates through-hole assembly quality.
Box Build Assembly
Additional metalwork, cabling, electromechanical components are assembled and integrated as needed into the final product.
Testing
Each board goes through electrical testing:
- In-circuit test (ICT) validates electrical connectivity between components
- Functional test validates overall board operation against specifications
Boards that fail are repaired, reworked, or scrapped.
Compliance Testing and Certifications
Additional specialized testing like burn-in, environmental stress testing, emissions/immunity testing may be conducted for compliance with standards like CE, FCC, UL, etc. as needed.
Final Finishing
Boards undergo final washing, coating, marking, packing, and other finishing steps. They are then shipped to the customer per the requested method.
Key Considerations for Optimizing PCBA Manufacturing
Proactively managing certain aspects of your PCB assembly process leads to better outcomes:
Design for Manufacturing (DFM)
Analyzing PCB design earlier for manufacturability prevents assembly issues. DFM helps optimize:
- Component selection
- Placement for ease of assembly
- Test points for inspection and debug
- Board stackup for thermal dissipation
This table summarizes key DFM guidelines to share with your design team:
DFM Aspect | Guidelines |
---|---|
Component Selection | Prefer standard parts from authorized distributors<br>Avoid obsolete, end-of-life, single-sourced parts |
Placement | 01005 passives should not be placed adjacent to BGAs<br> Group passives and connectors near edges for easy access |
Thermals | Ensure adequate thermal pads for heat dissipation from large ICs |
Test Points | Include testpoints for easy probing during test and debug |
Copper Thickness | Use adequate copper thickness for required current ratings |
Silkscreen | Place reference designators and polarity markings for easier assembly |
Manufacturing Data Management
Proactively share assembly drawings, bill of materials, assembly notes,Fab drawings,NC drill files, IPC netlists, etc. Missing or inaccurate data causes delays.
Component Procurement
- Share long lead time component details upfront for timely procurement
- Approve component substitution recommendations quickly to avoid delays
- Provide guideline on prioritizing cost vs lead time during shortages
Quality Expectations
- Clarify quality criteria like acceptable defect levels
- Align inspection scope and methodology
- Define repair/rework guidelines
- Establish failure analysis and corrective action process
Production Monitoring
- Get regular status updates from your program manager
- Visit the production floor during initial builds
- Review manufacturing defects data frequently
- Provide feedback to help continual improvement
Proactively managing these aspects will prevent issues and lead to a smoother PCBA production experience.
Frequently Asked Questions
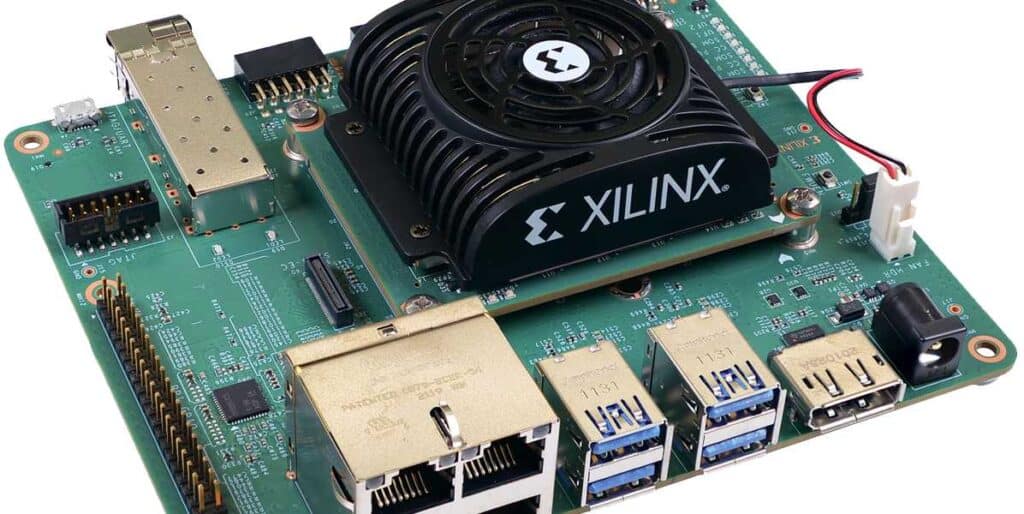
How long does contract manufacturing typically take from prototype to production?
The timeline varies based on factors like design complexity, component lead times, and production schedule. However, a typical timeline is:
- Prototype build: 2-3 weeks
- Pilot build testing: 1-2 weeks
- Design revisions: 1-2 weeks
- Engineering support for DFM: 1-2 weeks
- Production tooling: 2-4 weeks
- First article builds: 2 weeks
- Full production ramp: 1-2 weeks
So around 12-18 weeks can be expected from prototype to full production for a moderately complex assembly. Regular communication is key to expedite the process.
What are the typical volumes required to make contract manufacturing cost effective?
As an estimate, contract manufacturing starts becoming cost beneficial compared to in-house assembly at around 500-1000 boards. However, other factors like layer count, component complexity, test requirements also impact the economics. The contract manufacturer can provide detailed cost trade-offs. Lower volumes may work if leveraging existing assembly lines.
How are NRE and tooling costs handled in PCBA contract manufacturing?
Upfront non-recurring engineering (NRE) fees and tooling refer to production line configuration and programming. This includes costs for stencils, programming pick-and-place machines, debugging fixtures, testing programs, etc. The contract manufacturer normally amortizes these NRE/tooling costs over expected production volume to keep piece-part pricing competitive. These costs can be negotiated especially for higher volumes.
How is quality insured when outsourcing manufacturing?
Reputable contract manufacturers invest heavily in quality systems like ISO certifications, detailed process controls, automated inspection, and end-to-end traceability. However, customers should still define quality expectations upfront through standards like IPC Class 2 vs 3 acceptance, qualification protocols, quality reporting requirements, corrective action processes, etc. Onsite audits and production monitoring also help align quality needs.
What protections exist for my intellectual property when outsourcing?
Reputable contract manufacturers follow stringent data security protocols to protect customer IP and data. It is recommended to execute a non-disclosure agreement (NDA) covering technical documentation, software, production data, etc. explicitly outlining ownership, data handling policies, and liability. Regular security audits of your partner provide additional assurance on IP protection mechanisms.
Conclusion
PCBA contract manufacturing provides significant benefits like expert capabilities, quality systems, supply chain leverage, and cost savings, allowing you to focus on core product development and marketing. However, the key is finding the right partner and proactively managing aspects like design reviews, procurement, quality, and monitoring to get the most value. This guide summarizes best practices to have a successful outsourced assembly experience. Carefully selecting and closely collaborating with your contract manufacturer sets you up for manufacturing excellence and faster time-to-market.
0 Comments