What is a PCB Via?
A Printed Circuit Board (PCB) via is a small hole drilled through a PCB to allow electrical connections between different layers of the board. Vias are essential components in multi-layer PCB designs, enabling the creation of compact and complex circuits. They provide a means for signals and power to be routed vertically through the board, connecting traces on different layers.
Types of PCB Vias
There are several types of PCB vias, each with its own characteristics and applications:
Through-hole Vias
Through-hole vias are the most common type, extending through all layers of the PCB. They are typically used for mounting through-hole components or providing structural support.
Blind Vias
Blind vias start on an outer layer and terminate on an inner layer, without extending through the entire board thickness. They are used to save space and improve signal integrity.
Buried Vias
Buried vias are located entirely within the inner layers of a PCB, not visible from the outer surfaces. They are used to create complex routing paths and reduce electromagnetic interference (EMI).
Microvias
Microvias are small, laser-drilled vias with diameters less than 150 microns. They are used in high-density interconnect (HDI) PCB designs to achieve fine-pitch connections and minimize board size.
Factors Affecting PCB Via Size
Several factors influence the choice of PCB via size:
PCB Thickness
The thickness of the PCB is a primary factor in determining via size. Thicker boards require larger via diameters to maintain reliable connections and prevent manufacturing issues.
Copper Weight
The copper weight, or thickness of the copper layers, also affects via size. Heavier copper weights require larger via diameters to ensure proper plating and avoid excessive resistance.
Manufacturing Capabilities
The manufacturing capabilities of the PCB fabricator play a role in via size selection. Advanced facilities can produce smaller vias with tighter tolerances, while others may have limitations.
Signal Integrity
Signal integrity considerations, such as impedance matching and minimizing reflections, can influence via size. Smaller vias may be preferred for high-speed signals to reduce capacitance and improve signal quality.
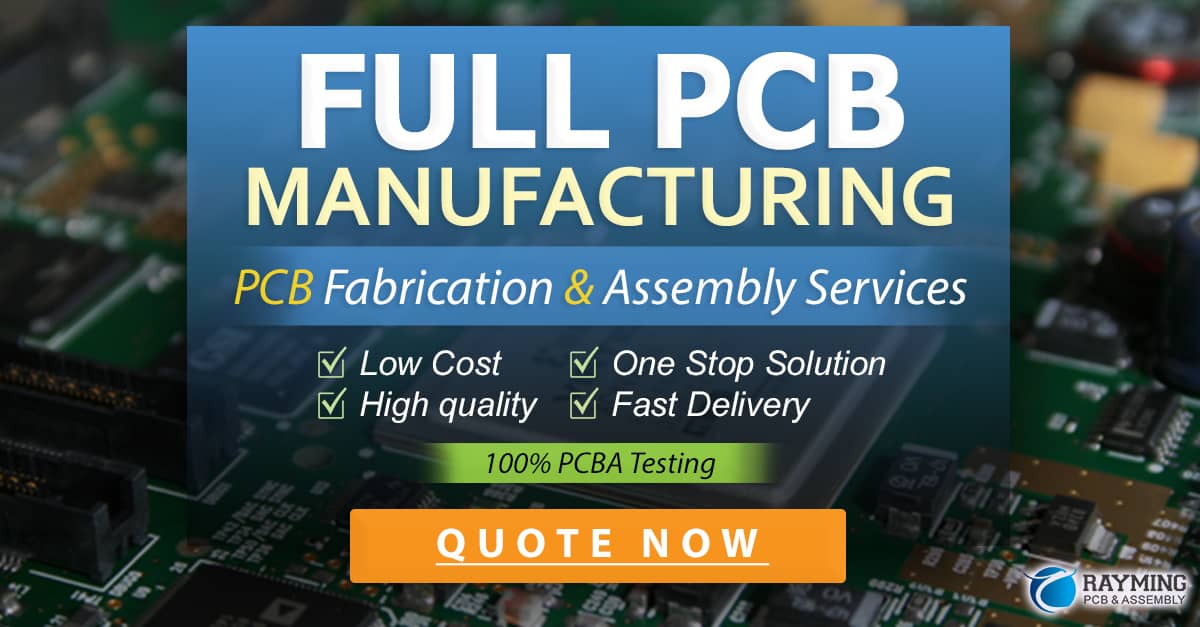
Standard PCB Via Sizes
The following table presents some standard PCB via sizes and their typical applications:
Via Diameter (mm) | Drill Size (mm) | Application |
---|---|---|
0.2 | 0.1 | High-density designs, microvias |
0.3 | 0.15 | Fine-pitch components, dense routing |
0.4 | 0.2 | General-purpose, moderate density |
0.6 | 0.3 | Through-hole components, power distribution |
0.8 | 0.4 | High-current applications, connectors |
1.0 | 0.5 | Structural support, large components |
Calculating PCB Via Size
To calculate the appropriate PCB via size, consider the following guidelines:
-
Determine the minimum via diameter based on the PCB thickness and aspect ratio (ratio of via depth to diameter). A common aspect ratio is 8:1, meaning the via diameter should be at least 1/8th of the board thickness.
-
Consider the copper weight and adjust the via size accordingly. Heavier copper weights may require larger via diameters to ensure reliable plating.
-
Verify the manufacturing capabilities of the PCB fabricator to ensure they can produce the desired via size with acceptable tolerances.
-
Evaluate signal integrity requirements and adjust the via size if needed to optimize impedance matching and minimize reflections.
PCB Via Plating
Proper plating of PCB vias is crucial for ensuring reliable electrical connections and preventing manufacturing defects. The two primary methods of via plating are:
Electroless Copper Plating
Electroless copper plating involves depositing a thin layer of copper onto the via walls using a chemical process. This method provides good coverage and adhesion, but the resulting copper thickness is limited.
Electrolytic Copper Plating
Electrolytic copper plating uses an electric current to deposit a thicker layer of copper onto the via walls. This method allows for greater copper thickness and improved conductivity but may result in uneven plating if not carefully controlled.
PCB Via Filling
In some cases, PCB vias may need to be filled with a conductive or non-conductive material to improve reliability, prevent Solder Wicking, or create a smooth surface for component placement. The two main types of via filling are:
Conductive Via Filling
Conductive via filling involves filling the via with a conductive material, such as copper or silver epoxy. This method provides a solid electrical connection and helps dissipate heat.
Non-conductive Via Filling
Non-conductive via filling uses a dielectric material, such as epoxy or resin, to fill the via. This method is used to prevent solder wicking, improve the planarity of the PCB surface, and provide mechanical support.
PCB Via Stacking
Via stacking is a technique used in multi-layer PCB designs to create vertical connections between multiple vias on different layers. By aligning vias on adjacent layers, designers can create longer, continuous paths for signals or power distribution. Via stacking helps reduce board size, improve routing efficiency, and minimize the number of layers required.
PCB Via Shielding
Via shielding is a method used to reduce EMI and crosstalk in high-speed PCB designs. It involves surrounding vias with a conductive barrier, such as a grounded copper ring or a plated through-hole, to contain electromagnetic fields and prevent interference between adjacent vias. Via shielding is particularly important in applications with sensitive analog circuits or high-frequency digital signals.
PCB Via Design Considerations
When designing PCB vias, consider the following best practices:
-
Minimize the number of vias to reduce manufacturing costs and improve reliability. Use efficient routing techniques and consider alternative layer stackups to minimize via count.
-
Place vias strategically to minimize signal path length and reduce impedance discontinuities. Avoid placing vias in critical signal paths or near sensitive components.
-
Maintain appropriate clearances between vias and other components, traces, and board edges to prevent manufacturing issues and ensure reliable operation.
-
Use consistent via sizes and patterns throughout the design to simplify manufacturing and improve yields. Avoid using multiple via sizes unless necessary for specific applications.
-
Consider the thermal management aspects of via placement, particularly for high-power components. Use thermal vias to dissipate heat and prevent localized hot spots on the PCB.
Frequently Asked Questions (FAQ)
1. What is the minimum via size I can use in my PCB design?
The minimum via size depends on several factors, including PCB thickness, copper weight, and manufacturing capabilities. As a general rule, the via diameter should be at least 1/8th of the board thickness to maintain an 8:1 aspect ratio. However, consult with your PCB fabricator to determine their specific capabilities and limitations.
2. Can I use different via sizes in the same PCB design?
Yes, you can use different via sizes in the same PCB design to accommodate various requirements, such as component mounting, power distribution, or signal integrity. However, it’s generally recommended to minimize the number of different via sizes to simplify manufacturing and improve yields.
3. What is the difference between a blind via and a buried via?
A blind via starts on an outer layer and terminates on an inner layer, without extending through the entire board thickness. In contrast, a buried via is located entirely within the inner layers of a PCB, not visible from the outer surfaces. Blind vias are used to save space and improve signal integrity, while buried vias are used to create complex routing paths and reduce EMI.
4. How do I determine the appropriate via size for my PCB design?
To determine the appropriate via size, consider factors such as PCB thickness, copper weight, manufacturing capabilities, and signal integrity requirements. Calculate the minimum via diameter based on the board thickness and aspect ratio, and adjust the size as needed to accommodate other factors. Consult with your PCB fabricator to ensure your design is manufacturable and meets their specific guidelines.
5. What is via stacking, and when should I use it?
Via stacking is a technique used in multi-layer PCB designs to create vertical connections between multiple vias on different layers. By aligning vias on adjacent layers, designers can create longer, continuous paths for signals or power distribution. Via stacking helps reduce board size, improve routing efficiency, and minimize the number of layers required. Use via stacking when you need to create complex routing paths or optimize board space in dense designs.
Conclusion
PCB via size is a critical aspect of PCB design, affecting manufacturability, reliability, and performance. Understanding the types of vias, factors influencing via size, and design best practices is essential for creating successful PCB layouts. By selecting appropriate via sizes, considering manufacturing capabilities, and optimizing via placement, designers can ensure their PCBs meet functional and quality requirements while minimizing costs and time-to-market.
0 Comments