Introduction
Printed Circuit Board (PCB) design is a complex process that involves various factors, one of which is the thickness of the traces. PCB Trace Thickness plays a crucial role in determining the overall performance, reliability, and manufacturability of the circuit board. In this article, we will delve into the intricacies of PCB trace thickness, discussing its importance, calculation methods, and best practices.
What is PCB Trace Thickness?
PCB trace thickness refers to the height of the copper traces on a printed circuit board. It is measured in ounces per square foot (oz/ft²) or microns (µm). The thickness of the copper traces directly affects the current-carrying capacity, signal integrity, and mechanical stability of the PCB.
Common PCB Trace Thicknesses
Thickness (oz/ft²) | Thickness (µm) | Application |
---|---|---|
0.5 | 17.5 | Low-power, high-density designs |
1 | 35 | General-purpose PCBs |
2 | 70 | High-current, power electronics |
3 | 105 | Extreme high-current, automotive electronics |
Factors Affecting PCB Trace Thickness
Several factors influence the choice of PCB trace thickness, including:
Current-Carrying Capacity
The current-carrying capacity of a trace is directly proportional to its cross-sectional area. Thicker traces can handle higher currents without overheating or suffering from voltage drop. The IPC-2221 standard provides guidelines for calculating the minimum trace width based on the current requirements.
Signal Integrity
Trace thickness affects the impedance and propagation delay of signals on the PCB. Thinner traces have higher resistance and may cause signal degradation, especially at high frequencies. Controlled impedance designs require careful consideration of trace thickness to maintain signal integrity.
Manufacturing Constraints
PCB Manufacturers have limitations on the minimum and maximum trace thicknesses they can produce reliably. Very thin traces (less than 0.5 oz/ft²) may be difficult to etch and prone to defects, while very thick traces (more than 3 oz/ft²) may lead to issues with plating uniformity and adhesion.
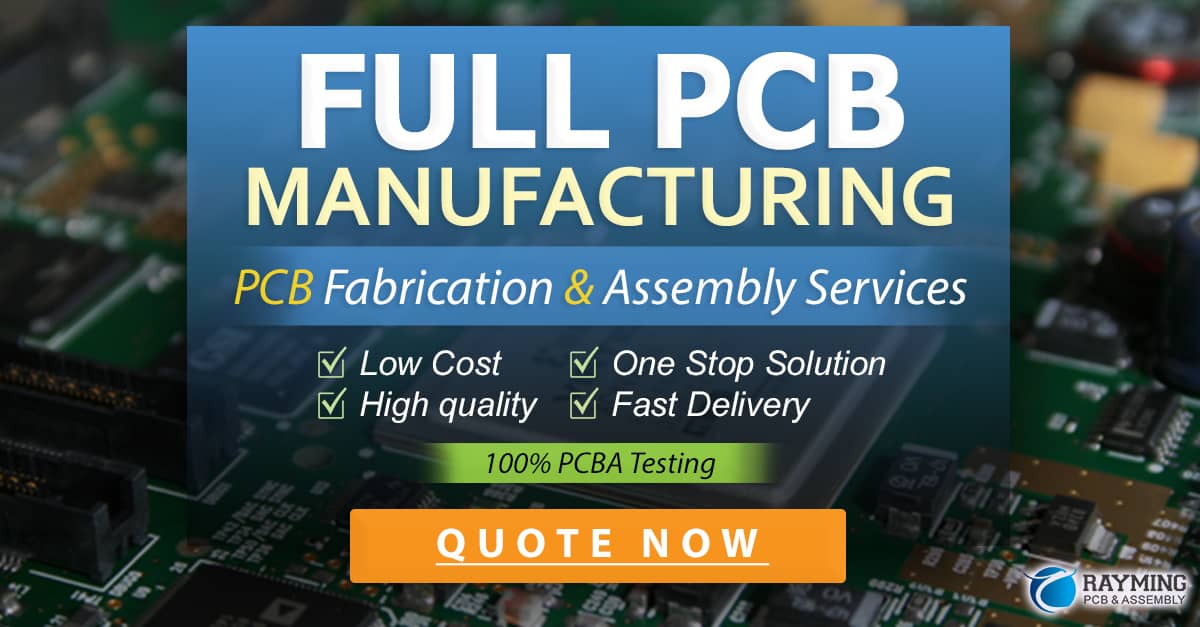
Calculating PCB Trace Thickness
To determine the appropriate trace thickness for a given design, several factors must be considered, including:
Current Requirements
The IPC-2221 standard provides a formula for calculating the minimum trace width based on the current requirements:
W = (I / (k * ΔT^b))^(1/c)
Where:
– W = Trace width (mils)
– I = Current (amps)
– ΔT = Temperature rise above ambient (°C)
– k, b, c = Constants based on the copper thickness
Voltage Drop
Voltage drop along a trace can be calculated using Ohm’s law:
V = I * R
Where:
– V = Voltage drop (volts)
– I = Current (amps)
– R = Trace resistance (ohms)
The trace resistance is determined by its length, width, and thickness. Thicker traces have lower resistance and, consequently, lower voltage drop.
High-Speed Signals
For high-speed signals, the trace impedance must be controlled to minimize reflections and ensure signal integrity. The characteristic impedance of a trace is determined by its width, thickness, and the dielectric properties of the PCB substrate. Specialized tools and calculators are available to determine the optimal trace dimensions for a given impedance target.
Best Practices for PCB Trace Thickness
To ensure optimal performance and manufacturability, consider the following best practices:
- Use appropriate trace thicknesses for the current requirements and signal integrity needs of your design.
- Follow the IPC-2221 guidelines for minimum trace widths based on current-carrying capacity.
- Consider the manufacturing capabilities and limitations of your PCB fabricator when selecting trace thicknesses.
- Use controlled impedance design techniques for high-speed signals, carefully selecting trace dimensions to meet impedance targets.
- Perform thorough design reviews and simulations to validate trace thickness choices before manufacturing.
FAQ
1. What is the most common PCB trace thickness?
The most common PCB trace thickness is 1 oz/ft² (35 µm), which is suitable for a wide range of general-purpose applications.
2. Can I use different trace thicknesses on the same PCB?
Yes, it is possible to use different trace thicknesses on the same PCB. This is often done to optimize current-carrying capacity and signal integrity for different parts of the circuit.
3. How does trace thickness affect the cost of PCB manufacturing?
Thicker traces require more copper and may increase the cost of PCB manufacturing. However, the cost difference is usually minimal, especially for small to medium-sized production runs.
4. What are the challenges associated with very thin PCB traces?
Very thin PCB traces (less than 0.5 oz/ft² or 17.5 µm) can be challenging to manufacture reliably. They are more prone to defects, such as open circuits or shorts, and may have higher resistance, leading to signal integrity issues.
5. How can I ensure that my PCB design has the appropriate trace thicknesses?
To ensure that your PCB design has the appropriate trace thicknesses, follow the IPC-2221 guidelines for current-carrying capacity, consider signal integrity requirements, and consult with your PCB manufacturer regarding their capabilities and limitations. Perform thorough design reviews and simulations to validate your trace thickness choices before committing to manufacturing.
Conclusion
PCB trace thickness is a critical aspect of Circuit Board Design that directly impacts the performance, reliability, and manufacturability of the final product. By understanding the factors affecting trace thickness, using appropriate calculation methods, and following best practices, designers can create PCBs that meet their specific requirements while ensuring optimal functionality and cost-effectiveness.
0 Comments