Why is PCB Testing Important?
PCB testing is vital for several reasons:
- Ensuring product quality and reliability
- Detecting and preventing potential failures
- Reducing manufacturing costs by identifying issues early in the process
- Meeting industry standards and customer requirements
- Improving overall customer satisfaction
The 8 Essential PCB Testing Methods
1. Visual Inspection
Visual inspection is the first and most basic PCB testing method. It involves examining the PCB for any visible defects, such as:
- Incorrect component placement
- Solder bridges or shorts
- Damaged or missing components
- Contamination or foreign objects
This method can be performed manually by trained operators or using automated optical inspection (AOI) systems.
2. Automated Optical Inspection (AOI)
AOI is an advanced form of visual inspection that uses high-resolution cameras and image processing software to detect surface-level defects on PCBs. The benefits of AOI include:
- High-speed inspection
- Consistent and accurate results
- Ability to detect minute defects
- Reduced human error
AOI systems compare the captured images of the PCB against a reference image to identify any discrepancies.
3. X-Ray Inspection
X-ray inspection is a non-destructive testing method that uses X-rays to examine the internal structure of PCBs. This method is particularly useful for detecting:
- Solder joint defects (e.g., voids, insufficient solder)
- Component placement issues
- Counterfeit components
- Faulty or missing connections
X-ray inspection can be performed using 2D or 3D X-ray systems, depending on the level of detail required.
4. In-Circuit Testing (ICT)
In-circuit testing is a powerful method that verifies the functionality of individual components on a PCB. ICT involves using a bed-of-nails fixture to make electrical contact with specific points on the PCB and apply test signals. This method can detect:
- Component failures
- Short circuits
- Open circuits
- Incorrect component values
ICT is highly effective in identifying manufacturing defects and ensuring that the PCB meets its design specifications.
5. Flying Probe Testing
Flying probe testing is an alternative to ICT that uses movable probes to make electrical contact with the PCB. The main advantages of flying probe testing include:
- Flexibility in testing different PCB designs
- No need for custom test fixtures
- Ability to test both sides of the PCB
However, flying probe testing is generally slower than ICT and may not be suitable for high-volume production.
6. Functional Testing
Functional testing involves verifying the overall functionality of the PCB by simulating its intended operating conditions. This method tests the PCB’s:
- Input/output signals
- Communication interfaces
- Power supply
- Thermal performance
Functional testing ensures that the PCB performs as expected and meets the required specifications.
7. Boundary Scan Testing
Boundary scan testing, also known as JTAG (Joint Test Action Group) testing, is a method that uses a built-in test infrastructure to test the interconnections between components on a PCB. This method involves:
- Adding boundary scan cells to each component
- Connecting the cells to form a serial scan chain
- Applying test patterns to the scan chain to detect faults
Boundary scan testing is particularly useful for testing complex PCBs with high component density and limited physical access.
8. Burn-In Testing
Burn-in testing is a method that subjects the PCB to elevated temperatures and operating conditions for an extended period to identify potential early-life failures. This method helps to:
- Eliminate infant mortality failures
- Improve long-term reliability
- Reduce warranty claims and field returns
Burn-in testing is typically performed in an environmental chamber that controls temperature, humidity, and other stress factors.
PCB Testing Equipment and Tools
To perform effective PCB testing, manufacturers rely on various equipment and tools, such as:
- Multimeters
- Oscilloscopes
- Logic analyzers
- Thermal imaging cameras
- Automated test equipment (ATE)
- Test fixtures and jigs
Equipment/Tool | Purpose |
---|---|
Multimeter | Measures voltage, current, and resistance |
Oscilloscope | Displays and analyzes waveforms and signals |
Logic Analyzer | Captures and analyzes digital signals |
Thermal Imaging Camera | Identifies hot spots and thermal issues on PCBs |
Automated Test Equipment (ATE) | Performs automated testing and measurement |
Test Fixtures and Jigs | Provides mechanical support and electrical interface for testing |
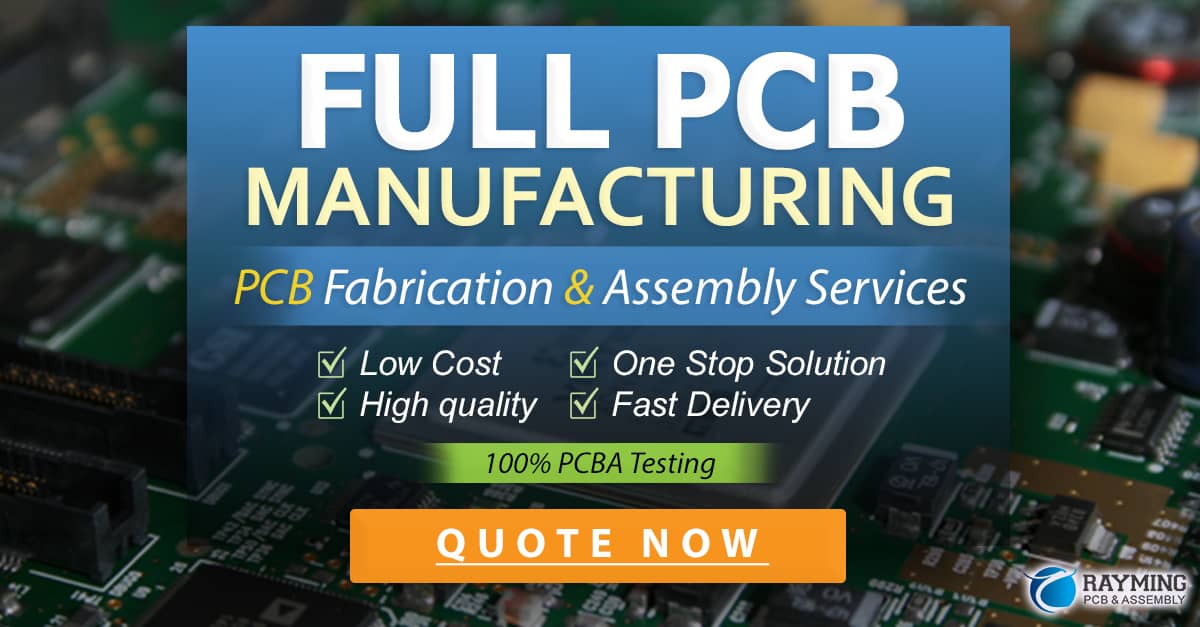
Implementing a Comprehensive PCB Testing Strategy
To ensure the highest quality and reliability of PCBs, it is essential to implement a comprehensive testing strategy that incorporates multiple methods. A typical PCB testing process may include:
- Visual inspection or AOI to detect surface-level defects
- X-ray inspection to examine internal structures
- In-circuit testing or flying probe testing to verify component functionality
- Boundary scan testing to test interconnections
- Functional testing to validate overall performance
- Burn-in testing to identify early-life failures
By employing a combination of these testing methods, manufacturers can identify and resolve issues at various stages of the production process, reducing the risk of defective products reaching the end-user.
Frequently Asked Questions (FAQ)
-
Q: What is the difference between in-circuit testing and flying probe testing?
A: In-circuit testing uses a bed-of-nails fixture to make electrical contact with specific points on the PCB, while flying probe testing uses movable probes. ICT is faster but requires custom test fixtures, while flying probe testing is more flexible but slower. -
Q: Can visual inspection alone guarantee the quality of a PCB?
A: While visual inspection is an important first step, it cannot detect all potential issues, such as internal defects or functional problems. A comprehensive testing strategy that includes multiple methods is necessary to ensure the highest quality. -
Q: How does boundary scan testing work?
A: Boundary scan testing uses a built-in test infrastructure, where boundary scan cells are added to each component on the PCB. These cells are connected to form a serial scan chain, and test patterns are applied to the chain to detect faults in the interconnections between components. -
Q: What is the purpose of burn-in testing?
A: Burn-in testing subjects the PCB to elevated temperatures and operating conditions for an extended period to identify potential early-life failures. This helps to eliminate infant mortality failures, improve long-term reliability, and reduce warranty claims and field returns. -
Q: How do I choose the right PCB testing methods for my product?
A: The choice of PCB testing methods depends on various factors, such as product complexity, reliability requirements, production volume, and cost considerations. Consulting with experienced PCB testing professionals can help you develop a tailored testing strategy that meets your specific needs.
Conclusion
PCB testing is a critical aspect of the electronics manufacturing process, ensuring the quality, reliability, and functionality of the final product. By understanding and implementing the eight essential PCB testing methods discussed in this article, manufacturers can identify and prevent potential issues, reduce costs, and improve customer satisfaction. A comprehensive testing strategy that combines visual inspection, AOI, X-ray inspection, in-circuit testing, flying probe testing, functional testing, boundary scan testing, and burn-in testing is key to producing high-quality, reliable PCBs that meet industry standards and customer expectations.
0 Comments