What is a PCB Stencil?
A PCB stencil is a thin sheet of metal, typically stainless steel, with laser-cut openings that correspond to the solder pad locations on a PCB. The stencil is used to apply solder paste onto the PCB surface during the assembly process, ensuring that the correct amount of solder paste is deposited on each pad.
Types of PCB Stencils
There are two main types of PCB stencils:
-
Framed Stencils: These stencils are mounted on a frame, providing stability and durability. Framed stencils are ideal for high-volume production and automated assembly processes.
-
Frameless Stencils: Also known as prototype stencils, these are unmounted and more flexible. Frameless stencils are suitable for low-volume production, prototyping, and manual assembly processes.
The Importance of PCB Stencils in PCB Assembly
PCB stencils are essential for several reasons:
-
Precision: Stencils ensure that the correct amount of solder paste is applied to each pad, minimizing the risk of defects such as bridging or insufficient solder joints.
-
Consistency: Using a stencil guarantees consistent solder paste application across multiple PCBs, leading to higher quality and reliability.
-
Efficiency: Stencils enable faster and more efficient assembly processes, particularly in high-volume production environments.
PCB Stencil Manufacturing Process
The PCB stencil manufacturing process involves several key steps:
-
Design: The stencil design is created based on the PCB layout, taking into account factors such as pad sizes, pitch, and component placement.
-
Material Selection: Stainless steel is the most common material used for PCB stencils due to its durability and stability. The thickness of the stencil is determined based on the PCB design and solder paste requirements.
-
Laser Cutting: High-precision laser cutting machines are used to create the openings in the stencil. The laser cutting process ensures accurate and clean cuts, minimizing the risk of defects.
-
Inspection: The manufactured stencil undergoes a thorough inspection to ensure that all openings are correctly sized and positioned. This step is crucial for maintaining the quality and reliability of the stencil.
-
Packaging: The finished stencil is packaged and shipped to the customer, ready for use in the PCB assembly process.
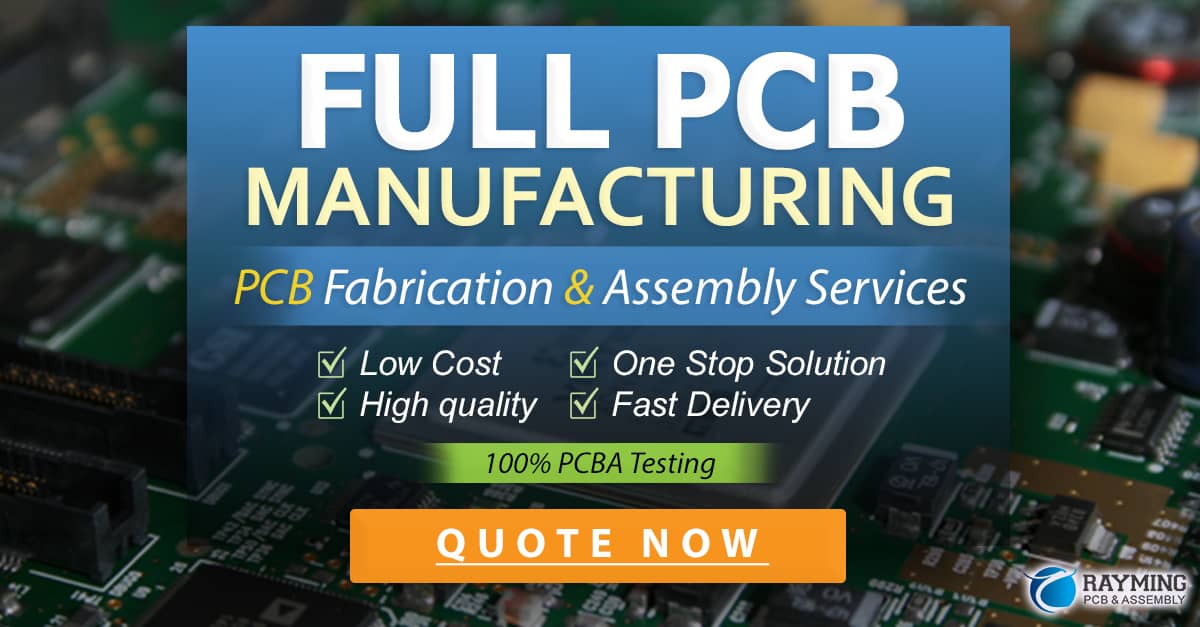
Factors to Consider When Choosing a PCB Stencil Manufacturer
When selecting a PCB stencil manufacturer, several key factors should be considered:
-
Experience: Choose a manufacturer with a proven track record in producing high-quality PCB stencils. Experienced manufacturers have the knowledge and expertise to handle complex designs and ensure optimal results.
-
Technology: Ensure that the manufacturer uses state-of-the-art laser cutting machines and has invested in the latest technology to guarantee precise and reliable stencils.
-
Quality Control: Look for a manufacturer with stringent quality control processes in place. This includes thorough inspections and testing to ensure that each stencil meets the required specifications.
-
Turnaround Time: Consider the manufacturer’s lead times and ability to deliver stencils within your required timeframe. Fast turnaround times are particularly important for time-sensitive projects and prototype development.
-
Customer Support: Choose a manufacturer that offers excellent customer support and is responsive to your inquiries and concerns. Good communication and support can make a significant difference in the overall experience and success of your project.
Top PCB Stencil Manufacturers
Here are some of the leading PCB stencil manufacturers in the industry:
Manufacturer | Location | Specialization |
---|---|---|
PCBWay | China | Prototype and low-volume stencils |
OSHStencils | USA | Rapid prototyping and low-volume stencils |
Sunshine PCB | China | High-volume and framed stencils |
PCBCart | China | Full-service PCB and stencil manufacturing |
EasyEDA | China | Online PCB design and stencil ordering |
These manufacturers offer a range of services and specialize in different aspects of PCB stencil production, catering to various needs and requirements.
Frequently Asked Questions (FAQ)
-
What is the typical thickness of a PCB stencil?
PCB stencil thickness typically ranges from 0.1mm to 0.2mm (4 to 8 mils). The ideal thickness depends on factors such as the solder paste type, PCB design, and component size. -
How long does it take to manufacture a PCB stencil?
The manufacturing time for a PCB stencil varies depending on the complexity of the design and the manufacturer’s workload. Typically, prototype stencils can be produced within 1-3 days, while high-volume production stencils may take 5-7 days. -
Can PCB stencils be reused?
Yes, PCB stencils can be reused multiple times, provided they are properly cleaned and maintained. Regular cleaning helps to remove solder paste residue and prevents clogging of the openings. -
What is the difference between laser-cut and electroformed stencils?
Laser-cut stencils are created using high-precision laser cutting machines, resulting in clean and accurate openings. Electroformed stencils, on the other hand, are produced using an electroplating process, which allows for finer pitch and smaller openings. Laser-cut stencils are more common and cost-effective for most PCB designs. -
How do I choose the right PCB stencil manufacturer for my project?
When selecting a PCB stencil manufacturer, consider factors such as experience, technology, quality control, turnaround time, and customer support. Research and compare different manufacturers to find one that aligns with your specific needs and requirements.
Conclusion
PCB stencils are a critical component in the PCB assembly process, ensuring precise and consistent solder paste application. When choosing a PCB stencil manufacturer, it is essential to consider factors such as experience, technology, quality control, turnaround time, and customer support. By partnering with a reliable and reputable manufacturer, you can ensure that your PCB stencils meet the highest quality standards and contribute to the success of your PCB assembly projects.
0 Comments