1. Cold Solder Joints
Cold solder joints occur when the solder fails to melt completely or when there is insufficient heat transfer between the solder and the components. This results in a dull, grainy appearance and a weak mechanical and electrical connection.
To avoid cold solder joints:
– Ensure the soldering iron is at the correct temperature (typically between 300°C and 400°C).
– Clean the soldering iron tip regularly to maintain proper heat transfer.
– Apply the soldering iron to both the component lead and the PCB pad simultaneously.
– Use the appropriate amount of solder and allow it to flow freely.
2. Bridging
Bridging, also known as solder bridges, happens when excess solder accidentally connects adjacent pins or pads, creating a short circuit. This can cause the circuit to malfunction or even damage the components.
To prevent bridging:
– Use a fine-tipped soldering iron for precise control.
– Apply the right amount of solder, avoiding excessive amounts.
– Maintain a steady hand while soldering to prevent solder from spreading to unintended areas.
– Inspect the PCB after soldering to identify and remove any bridges.
3. Insufficient Solder
Insufficient solder occurs when there is not enough solder to create a proper connection between the component lead and the PCB pad. This can lead to weak joints and intermittent electrical connections.
To ensure sufficient solder:
– Use the appropriate solder wire diameter for the job.
– Apply enough solder to create a concave fillet between the component lead and the PCB pad.
– Reheat the joint and add more solder if necessary.
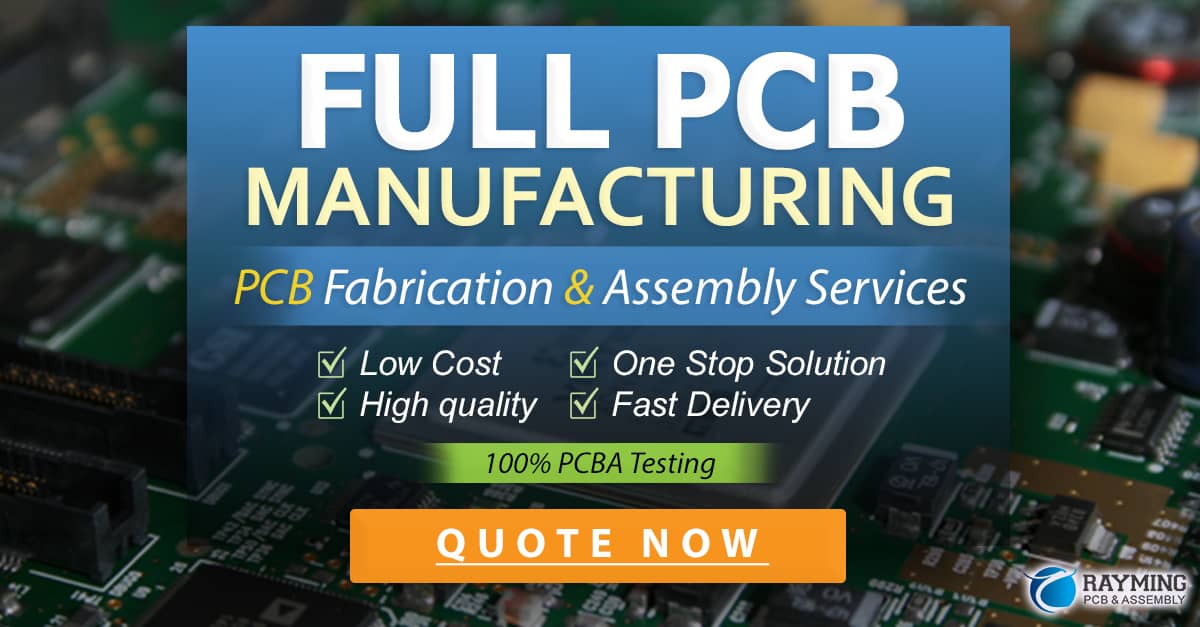
4. Excessive Solder
Excessive solder, also known as solder blobs or peaks, happens when too much solder is applied to the joint. This can cause short circuits, bridging, and difficulty in inspecting the joint quality.
To avoid excessive solder:
– Use the correct amount of solder for the joint size.
– Remove excess solder using a solder wick or desoldering pump.
– Maintain the soldering iron at the appropriate temperature to control solder flow.
5. Lifted Pads
Lifted pads occur when the copper pad on the PCB separates from the board during soldering. This can happen due to excessive heat, improper soldering technique, or poor PCB design.
To prevent lifted pads:
– Use a temperature-controlled soldering iron to avoid overheating the pads.
– Apply gentle pressure when soldering to prevent stress on the pads.
– Ensure proper PCB design with adequate pad size and copper weight.
6. Tombstoning
Tombstoning, also known as drawbridging, is a defect that occurs in surface-mount devices (SMDs) when one end of the component lifts off the PCB pad during soldering. This is often caused by uneven heating or an imbalance in the Solder volume on the pads.
To avoid tombstoning:
– Ensure even heating of both component pads during soldering.
– Use solder paste with the appropriate viscosity and particle size.
– Design the PCB with balanced pad sizes and shapes for each component.
7. Solder Balls
Solder balls are small, spherical particles of solder that can form during the soldering process. They can cause short circuits and affect the reliability of the PCB.
To minimize solder balls:
– Use solder wire with a no-clean flux core to reduce residue.
– Maintain proper soldering iron temperature and tip cleanliness.
– Avoid excessive solder and flux on the PCB.
– Clean the PCB thoroughly after soldering to remove any solder balls.
8. Flux Residue
Flux is a chemical agent used to improve solder flow and prevent oxidation during soldering. However, if not cleaned properly, flux residue can lead to corrosion and affect the long-term reliability of the PCB.
To manage flux residue:
– Use no-clean flux whenever possible to minimize residue.
– Clean the PCB with isopropyl alcohol or a dedicated flux cleaner after soldering.
– Follow the manufacturer’s guidelines for flux selection and cleaning methods.
9. Dry Joints
Dry joints occur when the solder fails to form a proper metallurgical bond with the component lead or PCB pad. This can happen due to insufficient heat, contamination, or improper flux activation.
To prevent dry joints:
– Ensure the soldering iron is at the correct temperature for the solder type.
– Clean the component leads and PCB pads before soldering.
– Use fresh solder and flux to ensure proper bonding.
– Apply the soldering iron to both the component lead and PCB pad simultaneously.
10. Whiskers
Solder whiskers are thin, hair-like protrusions that can grow from solder joints over time. They can cause short circuits and reliability issues in the PCB.
To mitigate solder whiskers:
– Use lead-free solder alloys that are less prone to whisker formation.
– Apply conformal coatings to the PCB to prevent whisker growth.
– Maintain proper storage conditions for the PCB to minimize whisker formation.
11. Thermal Damage
Thermal damage can occur when the PCB or components are exposed to excessive heat during soldering. This can lead to delamination, warping, or component failure.
To avoid thermal damage:
– Use a temperature-controlled soldering iron with the appropriate tip size.
– Follow the manufacturer’s recommended soldering temperature and duration for each component.
– Avoid prolonged exposure of the PCB and components to high temperatures.
12. Cold Solder Joints on Ground Planes
Cold solder joints can also occur on ground planes, which are large copper areas on the PCB used for grounding purposes. These joints can be difficult to detect and cause intermittent connections.
To prevent cold solder joints on ground planes:
– Use a larger soldering iron tip or a higher wattage iron to provide sufficient heat.
– Increase the soldering time to allow proper heat transfer to the ground plane.
– Ensure the ground plane is clean and free from oxidation before soldering.
13. Solder mask damage
Solder mask is a protective layer applied to the PCB to prevent solder bridging and protect the copper traces. Damage to the solder mask can expose the underlying copper and lead to short circuits.
To avoid solder mask damage:
– Use a soldering iron with a fine tip to avoid contact with the solder mask.
– Maintain the appropriate soldering iron temperature to prevent overheating the solder mask.
– Handle the PCB carefully to avoid scratching or abrading the solder mask.
14. Flux Splattering
Flux splattering occurs when the flux vaporizes rapidly during soldering, causing small droplets to scatter across the PCB. This can lead to contamination and affect the appearance of the PCB.
To minimize flux splattering:
– Use a low-spattering flux or a flux with a higher activation temperature.
– Maintain the appropriate soldering iron temperature to control flux vaporization.
– Keep the soldering iron tip clean to prevent flux buildup and splattering.
15. Insufficient Wetting
Insufficient wetting happens when the molten solder fails to spread evenly across the component lead and PCB pad. This can result in weak joints and poor electrical connections.
To improve wetting:
– Ensure the surfaces to be soldered are clean and free from oxidation.
– Use fresh solder and flux to promote proper wetting.
– Maintain the appropriate soldering iron temperature for the solder type.
– Apply the soldering iron to both the component lead and PCB pad simultaneously.
FAQ
1. What is the ideal soldering iron temperature for PCB Soldering?
The ideal soldering iron temperature depends on the type of solder being used. For lead-based solder, a temperature range of 300°C to 350°C is recommended. For lead-free solder, a higher temperature range of 350°C to 400°C is typically used. Always refer to the solder manufacturer’s guidelines for specific temperature recommendations.
2. How often should I clean my soldering iron tip?
It is essential to clean your soldering iron tip regularly to maintain its performance and longevity. Ideally, you should clean the tip before each use, during prolonged soldering sessions, and after you have finished soldering. Use a damp sponge or a brass wire tip cleaner to remove oxidation and solder residue from the tip.
3. Can I use lead-free solder for all PCB soldering applications?
Yes, lead-free solder can be used for most PCB soldering applications. However, keep in mind that lead-free solder typically requires higher soldering temperatures and may have different wetting characteristics compared to lead-based solder. It is important to choose a lead-free solder alloy that is compatible with your specific PCB materials and components.
4. How can I improve my soldering skills?
To improve your soldering skills, consider the following tips:
– Practice regularly on scrap PCBs or practice kits.
– Watch tutorial videos and read instructional materials to learn proper techniques.
– Invest in a good quality soldering iron and maintain it properly.
– Use the appropriate solder wire diameter and flux for the job.
– Inspect your solder joints closely and learn to identify common defects.
– Seek guidance from experienced soldering professionals or take a soldering course.
5. What should I do if I encounter a soldering problem on my PCB?
If you encounter a soldering problem on your PCB, follow these steps:
1. Identify the type of soldering defect (e.g., cold joint, bridging, insufficient solder).
2. Assess the extent of the problem and its potential impact on the circuit.
3. Determine the appropriate repair method based on the defect type and PCB design.
4. Clean the affected area and remove any excess solder or debris.
5. Reapply solder using the correct technique and materials.
6. Inspect the repaired joint to ensure proper electrical and mechanical connection.
If the problem persists or you are unsure about the repair process, consider seeking assistance from a professional PCB Rework service.
Soldering Problem | Causes | Prevention |
---|---|---|
Cold Solder Joints | – Insufficient heat – Poor heat transfer – Contaminated surfaces |
– Maintain correct soldering iron temperature – Clean soldering iron tip regularly – Apply solder to both component lead and PCB pad |
Bridging | – Excess solder – Unsteady hand – Incorrect soldering iron tip size |
– Use fine-tipped soldering iron – Apply appropriate amount of solder – Maintain steady hand while soldering |
Insufficient Solder | – Incorrect solder wire diameter – Insufficient solder application |
– Use appropriate solder wire diameter – Apply enough solder to create concave fillet |
Excessive Solder | – Too much solder applied – Incorrect soldering iron temperature |
– Use correct amount of solder for joint size – Remove excess solder with solder wick or desoldering pump |
Lifted Pads | – Excessive heat – Improper soldering technique – Poor PCB design |
– Use temperature-controlled soldering iron – Apply gentle pressure when soldering – Ensure proper PCB design |
By understanding these common PCB Soldering Problems, their causes, and preventive measures, you can improve your soldering quality and avoid costly rework. Remember to always follow best practices, use the appropriate tools and materials, and continuously refine your skills through practice and learning.
0 Comments