Introduction to PCB Silk-screen
PCB silk-screen, also known as legend or nomenclature, is a layer of text and symbols printed on the surface of a printed circuit board (PCB) for identification and orientation purposes. It provides essential information about the components, connectors, and other features on the board, making it easier for designers, assemblers, and technicians to work with the PCB. The silk-screen layer is typically applied using a screen-printing process and is usually white, although other colors may be used for specific applications or aesthetic reasons.
The Importance of PCB Silk-screen
PCB silk-screen serves several important functions:
-
Component identification: Silk-screen labels help identify components, such as resistors, capacitors, and integrated circuits, making it easier for assemblers and technicians to locate and work with specific parts.
-
Orientation guidance: Silk-screen markings can indicate the proper orientation of components, connectors, and the board itself, reducing the risk of assembly errors.
-
Testing and debugging: Clear labeling of test points, jumpers, and other features simplifies the testing and debugging process.
-
Branding and aesthetics: Silk-screen can be used to display company logos, product names, or other branding elements, enhancing the overall appearance of the PCB.
The PCB Silk-screen Process
Preparing the Silk-screen Artwork
The first step in the PCB silk-screen process is creating the artwork. This is typically done using PCB design software, such as Altium Designer, Eagle, or KiCad. The silk-screen layer is designed alongside the other layers of the PCB, such as the copper traces and solder mask. When preparing the silk-screen artwork, consider the following:
-
Text size and font: Choose a font that is legible at small sizes and ensure that the text is large enough to be easily read. A minimum text height of 0.8mm is recommended.
-
Spacing: Maintain sufficient spacing between text and components to avoid obscuring important features or making the PCB appear cluttered.
-
Alignment: Align text and symbols consistently and logically to improve readability and overall aesthetics.
Screen Printing the Silk-screen
Once the artwork is prepared, the silk-screen layer is applied to the PCB using a screen-printing process. This involves the following steps:
-
Screen preparation: A fine mesh screen is coated with a light-sensitive emulsion and exposed to UV light through a film positive of the silk-screen artwork. The unexposed areas of the emulsion are then washed away, leaving a stencil of the desired pattern on the screen.
-
Ink application: The screen is placed over the PCB, and a squeegee is used to force ink through the open areas of the stencil onto the board’s surface.
-
Curing: The printed ink is then cured, typically using UV light or heat, to ensure a durable and long-lasting finish.
Silk-screen Inks and Curing Methods
Several types of inks can be used for PCB silk-screening, each with its own curing requirements:
-
UV-curable inks: These inks are cured by exposure to ultraviolet light, which causes a rapid polymerization reaction. UV-curable inks offer fast curing times and excellent durability.
-
Thermal-curable inks: These inks are cured by exposure to heat, typically in a conveyor oven. Thermal-curable inks provide good durability and are suitable for a wide range of substrates.
-
Air-dry inks: These inks cure through solvent evaporation at room temperature. While they offer the simplest curing process, air-dry inks may not provide the same level of durability as UV or thermal-curable inks.
The choice of ink and curing method depends on factors such as the specific requirements of the PCB, the production volume, and the available equipment.
PCB Silk-screen Design Guidelines
To ensure optimal readability and aesthetics, follow these guidelines when designing your PCB silk-screen:
Text Size and Font
- Use a minimum text height of 0.8mm for standard PCBs and 0.5mm for smaller, high-density boards.
- Choose a clean, simple font such as Arial, Helvetica, or Verdana for improved legibility.
- Avoid using serif fonts or overly decorative styles that may be difficult to read at small sizes.
Spacing and Clearance
- Maintain a minimum clearance of 0.25mm between silk-screen elements and copper features, such as pads and traces, to prevent short circuits and improve manufacturability.
- Keep a minimum spacing of 0.25mm between adjacent silk-screen elements to avoid crowding and improve readability.
- Ensure that silk-screen text and symbols do not overlap with component footprints or other critical board features.
Alignment and Orientation
- Align text and symbols consistently and logically, using grid lines or other reference points to ensure a neat and organized appearance.
- Orient text to be easily readable when the PCB is installed in its final position, considering factors such as connector locations and mounting orientation.
- Use standard orientations for common components, such as pin 1 indicators for ICs and polarity markings for diodes and capacitors.
Symbols and Graphics
- Use standard symbols and graphics, such as polarity indicators and test point markers, to improve clarity and consistency.
- Keep symbols simple and clear, avoiding overly complex or detailed graphics that may be difficult to reproduce accurately.
- Consider using custom graphics, such as company logos or product branding elements, to enhance the overall appearance and professionalism of the PCB.
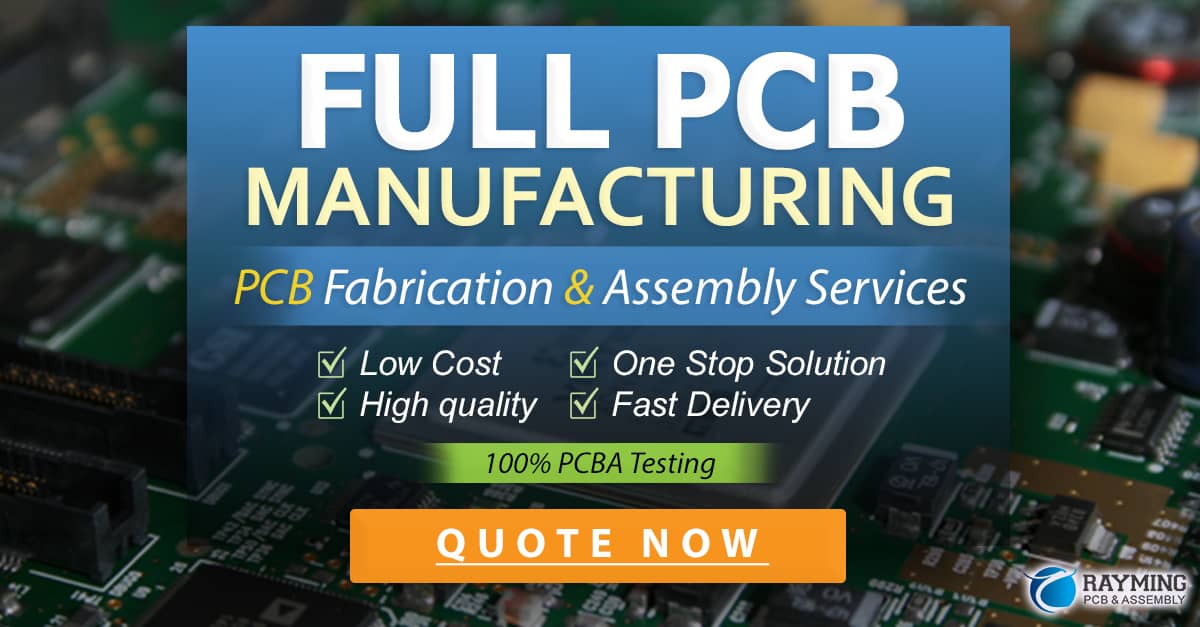
Common PCB Silk-screen Challenges and Solutions
Despite the benefits of PCB silk-screening, several challenges can arise during the process. Here are some common issues and their solutions:
Incomplete or Inconsistent Ink Coverage
Incomplete or inconsistent ink coverage can result from issues such as incorrect screen mesh size, improper ink viscosity, or poor squeegee technique. To address this:
- Ensure that the screen mesh size is appropriate for the ink and the desired level of detail.
- Adjust the ink viscosity to achieve optimal flow and coverage.
- Use a consistent squeegee pressure and angle to ensure even ink distribution.
Poor Ink Adhesion
Poor ink adhesion can cause the silk-screen to peel or flake off the PCB surface over time. To improve adhesion:
- Ensure that the PCB surface is clean and free of contaminants before printing.
- Use an ink that is compatible with the PCB substrate material.
- Follow the recommended curing process for the selected ink, ensuring adequate exposure to UV light or heat.
Misalignment or Registration Errors
Misalignment or registration errors can occur when the silk-screen layer is not correctly positioned relative to the other PCB Layers. To minimize these errors:
- Use accurate and well-maintained screen printing equipment.
- Ensure that the film positives used to create the screen stencil are correctly aligned and free of distortions.
- Implement a robust quality control process to identify and correct misalignment issues early in the production process.
By understanding these common challenges and implementing appropriate solutions, you can ensure high-quality and reliable PCB silk-screening results.
Frequently Asked Questions (FAQ)
-
Q: What is the minimum text size for PCB silk-screen?
A: The minimum recommended text height for standard PCBs is 0.8mm, while smaller, high-density boards may use text as small as 0.5mm. -
Q: Can PCB silk-screen be applied in colors other than white?
A: Yes, while white is the most common color for PCB silk-screen, other colors such as yellow, red, or black can be used for specific applications or to enhance contrast and readability. -
Q: How does the choice of ink affect the durability of PCB silk-screen?
A: The durability of PCB silk-screen depends on the type of ink used. UV-curable and thermal-curable inks generally provide better durability than air-dry inks, as they form a stronger bond with the PCB surface during the curing process. -
Q: Can PCB silk-screen be used for component assembly instructions?
A: Yes, PCB silk-screen can include assembly instructions, such as component orientation indicators, pin numbering, and polarity markings, to guide the assembly process and reduce the risk of errors. -
Q: Is it possible to remove or modify PCB silk-screen after it has been applied?
A: While it is possible to remove PCB silk-screen using abrasive methods or solvents, it is generally not recommended, as it can damage the PCB surface or other components. If modifications are necessary, it is best to make changes to the silk-screen artwork and reprint the layer.
Conclusion
PCB silk-screen is an essential element of printed Circuit Board Design and assembly, providing critical information and guidance for designers, assemblers, and technicians. By understanding the silk-screen process, design guidelines, and common challenges, you can create high-quality and informative PCBs that are both functional and aesthetically pleasing. As PCB technology continues to evolve, the role of silk-screen in ensuring clear communication and error-free assembly will remain crucial to the success of electronic projects.
Aspect | Recommendation |
---|---|
Text Size | Minimum 0.8mm for standard PCBs, 0.5mm for high-density boards |
Font | Clean, simple fonts like Arial, Helvetica, or Verdana |
Spacing | Minimum 0.25mm between silk-screen elements and copper features |
Alignment | Consistent and logical, using grid lines or reference points |
Symbols | Use standard symbols and keep graphics simple and clear |
Ink | Choose UV-curable, thermal-curable, or air-dry inks |
Curing | Follow recommended curing process for selected ink |
Quality Control | Implement robust processes to identify and correct issues |
By following these recommendations and staying informed about the latest developments in PCB silk-screening technology, you can create printed circuit boards that are informative, reliable, and professional in appearance.
0 Comments