Introduction to PCB Relays
A PCB relay, short for printed circuit board relay, is a compact electromagnetic switching device widely used in various electronic applications for power management and signal routing. These relays are designed to be directly mounted onto printed circuit boards (PCBs), providing a space-saving and efficient solution for switching electrical circuits.
PCB relays consist of an electromagnet, armature, spring, and contacts, all integrated into a compact package. When a current is passed through the electromagnet coil, it generates a magnetic field that attracts the armature, causing the contacts to switch from their normally open (NO) or normally closed (NC) position to the opposite state. This allows the relay to control the flow of electricity in a circuit, acting as a switch.
Advantages of PCB Relays
PCB relays offer several advantages over traditional relays and other switching devices:
-
Compact size: PCB relays are designed to be mounted directly onto PCBs, taking up minimal space compared to traditional relays. This makes them ideal for applications where space is limited, such as in portable devices or high-density electronic systems.
-
Easy integration: As PCB relays are designed for direct PCB mounting, they can be easily integrated into electronic circuits during the PCB Assembly process. This streamlines the manufacturing process and reduces the need for additional wiring or connectors.
-
High reliability: PCB relays are constructed using high-quality materials and are designed to withstand the stresses of frequent switching cycles. They offer reliable performance and long operational life, making them suitable for critical applications.
-
Electrical isolation: PCB relays provide electrical isolation between the control circuit and the switched circuit, which is essential for safety and noise reduction. This isolation helps protect sensitive electronic components from damage caused by voltage spikes or surges.
-
Versatility: PCB relays are available in a wide range of configurations, including different contact arrangements (SPST, SPDT, DPDT), coil voltages, and current ratings. This versatility allows designers to select the most suitable relay for their specific application requirements.
Types of PCB Relays
PCB relays can be classified into several types based on their construction, operating principle, and performance characteristics:
1. Electromechanical PCB Relays
Electromechanical PCB relays are the most common type and operate using an electromagnet to mechanically switch the contacts. They offer high reliability, electrical isolation, and the ability to switch both AC and DC loads. However, they have a relatively slower switching speed compared to solid-state relays and may be subject to contact wear over time.
2. Solid-State PCB Relays
Solid-state PCB relays use semiconductor devices, such as thyristors or transistors, to perform the switching function. They offer faster switching speeds, silent operation, and longer operational life compared to electromechanical relays. However, they have lower electrical isolation and are more sensitive to voltage transients and temperature fluctuations.
3. Reed PCB Relays
Reed PCB relays use a pair of ferromagnetic reed contacts sealed in a glass envelope. They are activated by an external magnetic field, typically generated by a coil wound around the glass envelope. Reed relays offer high reliability, fast switching speeds, and low contact resistance, making them suitable for low-power and high-frequency applications. However, they have lower current carrying capacity compared to electromechanical relays.
4. Latching PCB Relays
Latching PCB relays, also known as bistable relays, maintain their switched state even after the coil power is removed. They use a permanent magnet to hold the contacts in position, requiring only a short pulse of current to switch between states. Latching relays are useful in applications where power consumption is a concern or where the relay state needs to be maintained during power outages.
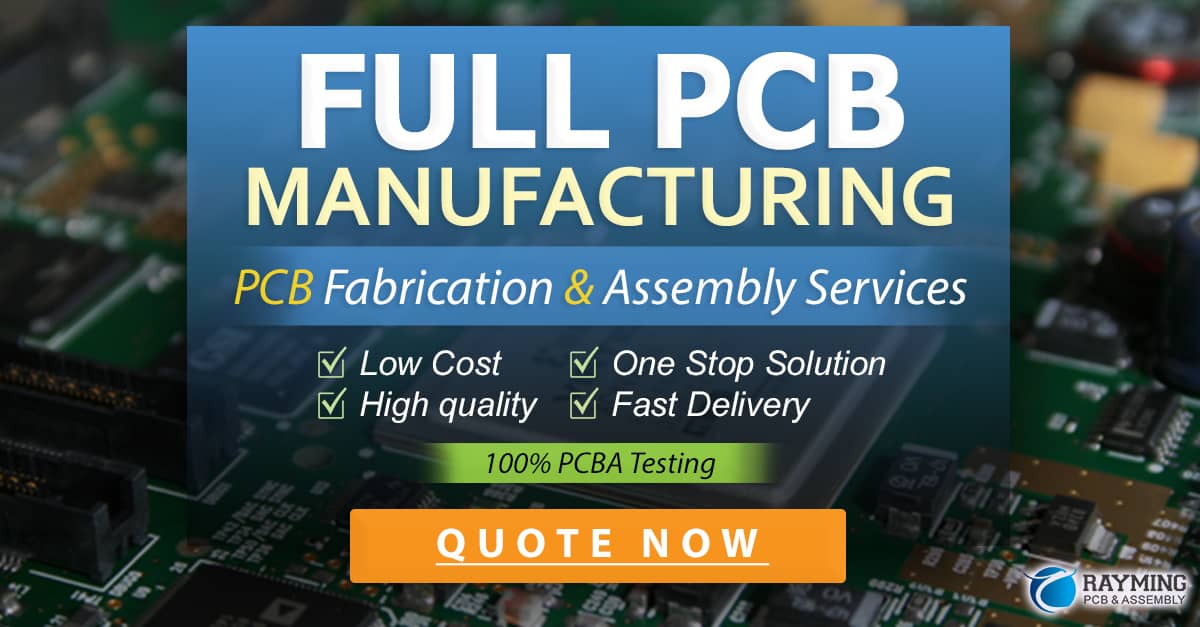
PCB Relay Specifications
When selecting a PCB relay for a specific application, several key specifications should be considered:
1. Contact Arrangement
PCB relays are available in different contact arrangements, depending on the number of poles (single or double) and the number of throw positions (single or double). Common contact arrangements include:
- SPST (Single Pole, Single Throw)
- SPDT (Single Pole, Double Throw)
- DPST (Double Pole, Single Throw)
- DPDT (Double Pole, Double Throw)
The choice of contact arrangement depends on the switching requirements of the application.
2. Coil Voltage and Current
The coil voltage and current determine the power required to activate the relay. PCB relays are available with coil voltages ranging from a few volts to several hundred volts, and coil currents ranging from a few milliamps to several amps. It is essential to select a relay with a coil voltage and current compatible with the control circuit.
3. Contact Rating
The contact rating specifies the maximum voltage and current that the relay contacts can safely switch. It is crucial to select a relay with a contact rating suitable for the load being switched. Exceeding the contact rating can lead to premature contact wear, reduced relay life, or even contact welding.
4. Switching Speed
The switching speed refers to the time required for the relay contacts to change state after the coil is energized or de-energized. It is usually specified in terms of operate time (the time taken for the contacts to close) and release time (the time taken for the contacts to open). Switching speed is an important consideration in applications that require fast response times, such as in high-speed switching or pulse-width modulation (PWM) control.
5. Insulation Resistance and Dielectric Strength
Insulation resistance and dielectric strength are measures of the relay’s ability to withstand voltage stress and maintain electrical isolation between the coil and contacts. A high insulation resistance and dielectric strength are essential for safety and reliability, particularly in applications with high voltages or sensitive electronic components.
6. Operating Temperature Range
The operating temperature range specifies the ambient temperature limits within which the relay can function reliably. It is important to select a relay with an operating temperature range suitable for the intended application environment.
PCB Relay Selection Guide
Selecting the right PCB relay for a specific application involves considering several factors:
-
Load requirements: Determine the voltage, current, and power requirements of the load being switched. Select a relay with a contact rating that exceeds the maximum load specifications.
-
Control circuit compatibility: Ensure that the relay’s coil voltage and current are compatible with the control circuit. Consider the available power supply and the driving capability of the control device (e.g., microcontroller, transistor).
-
Switching speed: If the application requires fast switching or precise timing control, select a relay with a suitable switching speed. Solid-state relays generally offer faster switching speeds compared to electromechanical relays.
-
Environmental factors: Consider the operating environment of the relay, including temperature, humidity, vibration, and shock. Select a relay with an operating temperature range and environmental ratings appropriate for the application.
-
PCB layout and space constraints: Evaluate the available space on the PCB and the layout requirements for the relay. Consider the relay’s package size, pin configuration, and required clearances.
-
Reliability and lifetime: Assess the reliability requirements of the application and select a relay with a suitable expected lifetime. Consider factors such as the number of switching cycles, contact material, and contact rating.
-
Cost and availability: Compare the cost and availability of different relay options that meet the application requirements. Consider factors such as lead time, minimum order quantity, and supplier reliability.
PCB Relay Applications
PCB relays find applications in a wide range of industries and electronic systems, including:
-
Automotive electronics: PCB relays are used in various automotive applications, such as power window control, lighting control, and engine management systems. They provide reliable switching and power management in harsh automotive environments.
-
Industrial automation and control: PCB relays are employed in industrial control panels, programmable logic controllers (PLCs), and process control systems. They are used for switching loads, such as motors, solenoids, and indicators, and for isolating control signals from power circuits.
-
Instrumentation and test equipment: PCB relays are used in test and measurement equipment, such as data acquisition systems, signal generators, and switching matrices. They provide signal routing, isolation, and conditioning capabilities.
-
Medical devices: PCB relays are found in medical equipment, such as patient monitoring systems, diagnostic devices, and therapy equipment. They ensure reliable and safe switching of electrical signals and power in sensitive medical applications.
-
Telecommunications: PCB relays are used in telecommunications equipment, such as routers, switches, and multiplexers. They provide signal routing, isolation, and protection in high-speed communication networks.
-
Consumer electronics: PCB relays are employed in various consumer electronic devices, such as home appliances, audio/video equipment, and gaming consoles. They enable power management, signal switching, and protection features.
-
Renewable energy systems: PCB relays are used in solar inverters, wind turbine controllers, and energy storage systems. They provide reliable switching and isolation of high-voltage and high-current circuits in renewable energy applications.
PCB Relay Mounting and Soldering
Proper mounting and soldering techniques are essential for ensuring the reliable operation and longevity of PCB relays. Here are some guidelines for mounting and soldering PCB relays:
-
PCB layout: Design the PCB layout to accommodate the relay’s package size and pin configuration. Ensure adequate clearance around the relay for heat dissipation and to avoid interference with other components.
-
Relay orientation: Orient the relay on the PCB according to the manufacturer’s recommendations. Ensure that the relay is properly aligned with the PCB pads and that the pin numbers match the PCB layout.
-
Soldering process: Use a temperature-controlled soldering iron with a suitable tip size for soldering the relay pins. Apply the appropriate amount of solder to create a strong and reliable solder joint. Avoid applying excessive heat or solder, as this can damage the relay or cause short circuits.
-
Cleaning: After soldering, clean the PCB to remove any flux residue or contaminants that may affect the relay’s performance. Use appropriate cleaning agents and methods recommended by the relay manufacturer.
-
Inspection: Visually inspect the soldered joints to ensure proper solder coverage, absence of bridging or short circuits, and correct alignment of the relay on the PCB. Use magnification tools if necessary to verify the soldering quality.
-
Mechanical stress: Avoid subjecting the mounted relay to excessive mechanical stress, such as bending or twisting the PCB, as this can damage the relay or cause solder joint failures.
PCB Relay Testing and Troubleshooting
After mounting and soldering the PCB relay, it is important to test its functionality and troubleshoot any issues that may arise. Here are some steps for testing and troubleshooting PCB relays:
-
Continuity test: Use a multimeter to check the continuity between the relay pins and the corresponding PCB pads. Ensure that there is a good electrical connection and no open circuits.
-
Coil resistance test: Measure the resistance of the relay coil using a multimeter. Compare the measured value with the specified coil resistance in the relay datasheet. A significant deviation from the specified value may indicate a damaged coil or incorrect relay selection.
-
Contact resistance test: Measure the resistance across the relay contacts in both the open and closed states. The resistance should be low (typically a few milliohms) when the contacts are closed and high (several megohms) when the contacts are open. High contact resistance may indicate contact contamination or wear.
-
Functional test: Apply the appropriate control signal to the relay coil and verify that the contacts switch as expected. Use a multimeter or oscilloscope to monitor the contact status and switching times. Ensure that the relay operates within the specified parameters.
-
Isolation test: Measure the insulation resistance and dielectric strength between the relay coil and contacts, as well as between adjacent contacts. Use a high-voltage insulation tester or megohmmeter to verify that the relay meets the specified isolation requirements.
-
Troubleshooting: If the relay fails to operate as expected, check for common issues such as incorrect coil voltage or polarity, damaged components, solder joint failures, or PCB layout problems. Refer to the relay datasheet and application notes for specific Troubleshooting Guidelines.
PCB Relay Maintenance and Replacement
To ensure the long-term reliability and performance of PCB relays, regular maintenance and timely replacement may be necessary. Here are some guidelines for maintaining and replacing PCB relays:
-
Periodic inspection: Regularly inspect the PCB relays for signs of physical damage, corrosion, or contamination. Check for loose or damaged solder joints, cracked or discolored relay housings, and bent or misaligned pins.
-
Cleaning: If the relay contacts become contaminated or oxidized, clean them using a suitable contact cleaner or relay burnishing tool. Follow the manufacturer’s recommendations for cleaning methods and materials.
-
Environmental control: Ensure that the PCB relays are operated within their specified environmental conditions, such as temperature, humidity, and vibration limits. Use appropriate enclosures, heatsinks, or conformal coatings to protect the relays from harsh environments.
-
Replacement criteria: Replace the PCB relay if it shows signs of excessive wear, contact damage, or performance degradation. Consider factors such as the number of switching cycles, contact resistance, and coil current consumption when determining the replacement interval.
-
Handling precautions: When replacing a PCB relay, handle the new relay with care to avoid damage during installation. Use proper ESD (electrostatic discharge) precautions and follow the manufacturer’s mounting and Soldering Guidelines.
-
Compatibility: Ensure that the replacement relay is compatible with the original relay in terms of package size, pin configuration, electrical ratings, and performance characteristics. Verify that the new relay meets the application requirements and any applicable safety or regulatory standards.
FAQ
-
What is the difference between a PCB relay and a traditional relay?
A PCB relay is designed to be mounted directly onto a printed circuit board (PCB), whereas a traditional relay is a standalone component that requires additional wiring and mounting hardware. PCB relays are generally more compact and easier to integrate into electronic systems compared to traditional relays. -
Can PCB relays switch both AC and DC loads?
Yes, PCB relays can switch both AC and DC loads, depending on their specifications. However, it is important to select a relay with a contact rating suitable for the type and magnitude of the load being switched. AC loads may require relays with higher voltage and current ratings compared to DC loads. -
What is the difference between a normally open (NO) and normally closed (NC) relay contact?
A normally open (NO) relay contact is open when the relay coil is not energized and closes when the coil is energized. In contrast, a normally closed (NC) relay contact is closed when the relay coil is not energized and opens when the coil is energized. The choice between NO and NC contacts depends on the specific switching requirements of the application. -
How do I select the appropriate coil voltage for a PCB relay?
The coil voltage of a PCB relay should be selected based on the available control circuit voltage and the relay’s specified coil voltage range. Ensure that the control circuit can provide sufficient voltage and current to energize the relay coil. It is also important to consider the power consumption of the relay coil and any voltage drop in the control circuit wiring. -
What is the expected lifetime of a PCB relay?
The expected lifetime of a PCB relay depends on various factors, such as the relay type, contact rating, switching frequency, and operating environment. Most PCB relays are rated for a specific number of switching cycles, typically ranging from several hundred thousand to several million cycles. However, the actual lifetime may vary based on the application conditions and the relay’s maintenance and replacement practices.
0 Comments