Introduction to PCB Price Composition
Printed Circuit Boards (PCBs) are essential components in nearly all electronic devices, from smartphones and computers to medical equipment and automotive systems. The cost of PCBs can significantly impact the overall price of these devices, making it crucial for manufacturers and designers to understand the factors that influence PCB pricing. In this article, we will explore the various elements that contribute to the composition of PCB prices, helping you make informed decisions when designing and sourcing PCBs for your projects.
Factors Affecting PCB Price Composition
1. PCB Size and Complexity
One of the primary factors influencing PCB price is the size and complexity of the board. Larger PCBs require more materials and take longer to manufacture, resulting in higher costs. Additionally, complex designs with intricate traces, small vias, and tight tolerances demand more advanced manufacturing processes, further increasing the price.
PCB Size | Relative Cost |
---|---|
Small (< 50 cm²) | Low |
Medium (50-200 cm²) | Moderate |
Large (> 200 cm²) | High |
2. Number of Layers
PCBs can have multiple layers, ranging from single-sided to multi-layer boards with 8, 12, or even more layers. As the number of layers increases, so does the cost of the PCB. Each additional layer requires more materials, processing time, and complexity in the manufacturing process.
Number of Layers | Relative Cost |
---|---|
Single-sided | Low |
Double-sided | Moderate |
4-layer | High |
6-layer | Very High |
8+ layers | Extremely High |
3. Material Selection
The choice of materials used in PCB Fabrication also plays a significant role in determining the price. The most common base material for PCBs is FR-4, a glass-reinforced epoxy laminate. However, specialized applications may require more expensive materials, such as high-frequency laminates (e.g., Rogers RO4000 series) or flexible substrates (e.g., polyimide).
Material | Relative Cost |
---|---|
FR-4 | Low |
High-Tg FR-4 | Moderate |
Polyimide | High |
Rogers RO4000 | Very High |
4. Surface Finish
The surface finish of a PCB is crucial for ensuring proper solderability and protecting the exposed copper traces from oxidation. Common surface finishes include Hot Air Solder Leveling (HASL), Immersion Silver (IAg), Immersion Tin (ISn), and Electroless Nickel Immersion Gold (ENIG). Each surface finish has its own advantages and cost implications.
Surface Finish | Relative Cost |
---|---|
HASL | Low |
IAg | Moderate |
ISn | Moderate |
ENIG | High |
5. Quantity and Lead Time
The quantity of PCBs ordered and the required lead time also influence the price. Larger order quantities often result in lower per-unit costs due to economies of scale. Additionally, shorter lead times may incur expedite fees or rush charges, increasing the overall cost of the PCBs.
Quantity | Relative Cost Per Unit |
---|---|
1-10 | Very High |
11-100 | High |
101-1000 | Moderate |
1000+ | Low |
6. Design Features and Requirements
Specific design features and requirements can also impact PCB pricing. These include:
- Controlled Impedance: Designing PCBs with controlled impedance for high-speed applications requires more precise manufacturing processes, increasing costs.
- Blind and Buried Vias: Incorporating blind and buried vias in a PCB design adds complexity and requires additional processing steps, resulting in higher prices.
- Trace Width and Spacing: Smaller trace widths and tighter spacing demand more advanced manufacturing capabilities, driving up costs.
- Hole Size and Aspect Ratio: Smaller hole sizes and higher aspect ratios (the ratio of hole depth to diameter) increase drilling complexity and cost.
7. Testing and Certification
Depending on the application and industry, PCBs may need to undergo various testing and certification processes to ensure quality, reliability, and compliance with standards. These additional steps can contribute to the overall cost of the PCBs.
Some common testing and certification requirements include:
- Electrical Testing: Continuity, insulation resistance, and high-potential (HiPot) testing to verify electrical integrity.
- Microsectioning: Cross-sectional analysis to inspect internal layer alignment, copper plating thickness, and lamination quality.
- Environmental Testing: Thermal cycling, moisture resistance, and vibration testing to assess the PCB’s durability under various conditions.
- Compliance Certification: Ensuring PCBs meet industry standards such as UL, IPC, RoHS, and REACH.
Strategies for Optimizing PCB Price Composition
Understanding the factors that influence PCB price composition enables designers and manufacturers to make informed decisions and optimize costs. Some strategies for achieving cost-effective PCB designs include:
-
Design for Manufacturability (DFM): Adhering to DFM guidelines helps avoid unnecessary complexity, reduces manufacturing challenges, and ultimately lowers costs.
-
Standardization: Using standardized materials, components, and processes whenever possible can lead to cost savings through economies of scale and reduced inventory requirements.
-
Panel Utilization: Optimizing panel utilization by arranging multiple PCB designs on a single panel can minimize material waste and reduce overall manufacturing costs.
-
Volume Pricing: Consolidating orders and purchasing larger quantities of PCBs can result in significant cost savings due to volume discounts offered by manufacturers.
-
Early Collaboration: Engaging with PCB Manufacturers early in the design process allows for expert input on design optimization, material selection, and cost reduction strategies.
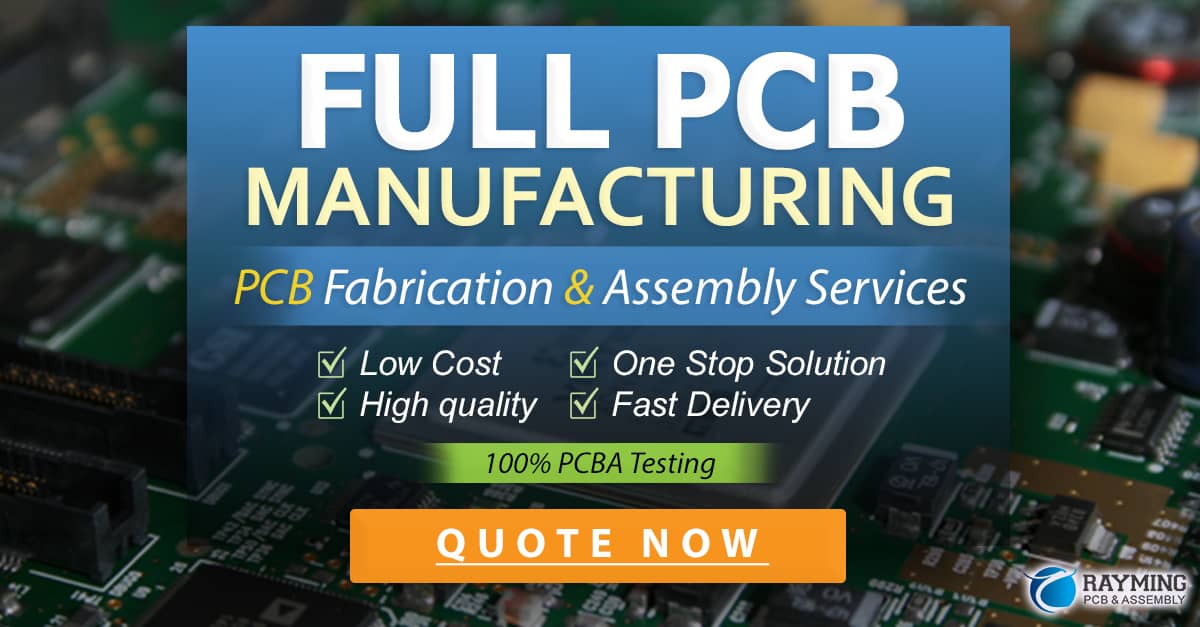
FAQ
1. What is the most significant factor affecting PCB price?
The most significant factor affecting PCB price is typically the size and complexity of the board. Larger and more complex PCBs require more materials, processing time, and advanced manufacturing capabilities, resulting in higher costs.
2. How can I reduce the cost of my PCB design?
To reduce the cost of your PCB design, consider the following strategies:
- Minimize board size and complexity
- Use standard materials and components
- Follow Design for Manufacturability (DFM) guidelines
- Optimize panel utilization
- Order larger quantities to take advantage of volume pricing
3. Is it always better to choose the lowest-cost PCB manufacturer?
While cost is an important consideration, it is not always advisable to choose the lowest-cost PCB manufacturer. Quality, reliability, and customer support are equally important factors to consider. Striking a balance between cost and quality is essential to ensure the long-term success of your project.
4. How can I ensure my PCBs meet the necessary testing and certification requirements?
To ensure your PCBs meet the necessary testing and certification requirements, follow these steps:
- Clearly communicate your requirements to your PCB manufacturer
- Choose a reputable manufacturer with experience in your industry and application
- Request documentation and certificates of compliance from your manufacturer
- Consider third-party testing and certification services for added assurance
5. What is the impact of lead time on PCB pricing?
Shorter lead times often result in higher PCB prices due to the need for expedited processing and rush charges. If your project allows for longer lead times, you may be able to secure lower prices. It is essential to balance your project timeline and budget when considering lead time options.
Conclusion
PCB price composition is a complex topic influenced by numerous factors, including board size and complexity, number of layers, material selection, surface finish, quantity, lead time, design features, and testing and certification requirements. By understanding these factors and implementing cost optimization strategies, designers and manufacturers can make informed decisions to balance cost, quality, and performance in their PCB projects. Effective communication, collaboration, and a focus on Design for Manufacturability (DFM) principles are key to achieving success in PCB design and manufacturing.
0 Comments