What are PCB Pins?
PCB pins, also known as printed circuit board pins or header pins, are small, conductive components used to establish electrical connections between different parts of a PCB or to connect a PCB to external devices. These pins are essential for creating reliable and secure connections in electronic circuits.
PCB pins come in various shapes, sizes, and materials, depending on their specific application. They are typically made of metal, such as brass or phosphor bronze, and are plated with gold, tin, or nickel to improve conductivity and prevent corrosion.
Types of PCB Pins
There are several types of PCB pins available, each designed for specific purposes and applications. Some of the most common types include:
-
Through-hole pins: These pins are inserted into drilled holes on a PCB and soldered in place. They provide a strong mechanical connection and are suitable for high-power applications.
-
Surface-mount pins: Also known as SMT pins, these are designed to be soldered directly onto the surface of a PCB. They are smaller than through-hole pins and are commonly used in high-density circuits.
-
Press-fit pins: These pins are designed to be pressed into plated through-holes on a PCB, creating a secure connection without the need for soldering. They are often used in automotive and industrial applications.
-
Wire-wrap pins: These pins have a square post that allows wires to be wrapped around them, creating a temporary or permanent connection. They are commonly used for prototyping and testing.
How to Use PCB Pins
Using PCB pins involves several steps, including selecting the appropriate pin type, preparing the PCB, and soldering or pressing the pins in place.
Selecting the Right PCB Pin
When choosing PCB pins for your project, consider the following factors:
- Current and voltage requirements
- Mechanical strength and durability
- PCB layout and space constraints
- Environmental factors (e.g., temperature, humidity)
Once you have determined your requirements, select the appropriate pin type and size that best suits your application.
Preparing the PCB
Before installing PCB pins, ensure that your PCB is properly designed and manufactured. This includes:
- Creating the appropriate footprints for the selected pin type
- Ensuring that the drill holes or pad sizes are correct
- Applying solder mask and silkscreen as needed
Installing PCB Pins
The installation process for PCB pins varies depending on the pin type and the specific application. However, the general steps involve:
-
Positioning the pins: Place the pins in their designated locations on the PCB, ensuring that they are aligned correctly.
-
Soldering or pressing: For through-hole and surface-mount pins, apply solder to the pins and PCB Pads to create a secure connection. For press-fit pins, use a press-fit tool to apply even pressure and insert the pins into the plated through-holes.
-
Inspecting the connections: After installation, visually inspect the connections to ensure that the pins are properly seated and that there are no shorts or open circuits.
Advantages of Using PCB Pins
PCB pins offer several advantages over other connection methods, such as wire soldering or using connectors. These advantages include:
-
Improved reliability: PCB pins provide a secure and stable connection, reducing the risk of loose or broken connections that can lead to circuit failures.
-
Increased efficiency: Using PCB pins streamlines the assembly process, as they can be quickly and easily installed using automated equipment.
-
Space savings: PCB pins, especially surface-mount types, occupy less space on a PCB compared to other connection methods, allowing for more compact designs.
-
Enhanced signal integrity: PCB pins can help maintain signal integrity by reducing the risk of electromagnetic interference (EMI) and providing a low-resistance path for electrical signals.
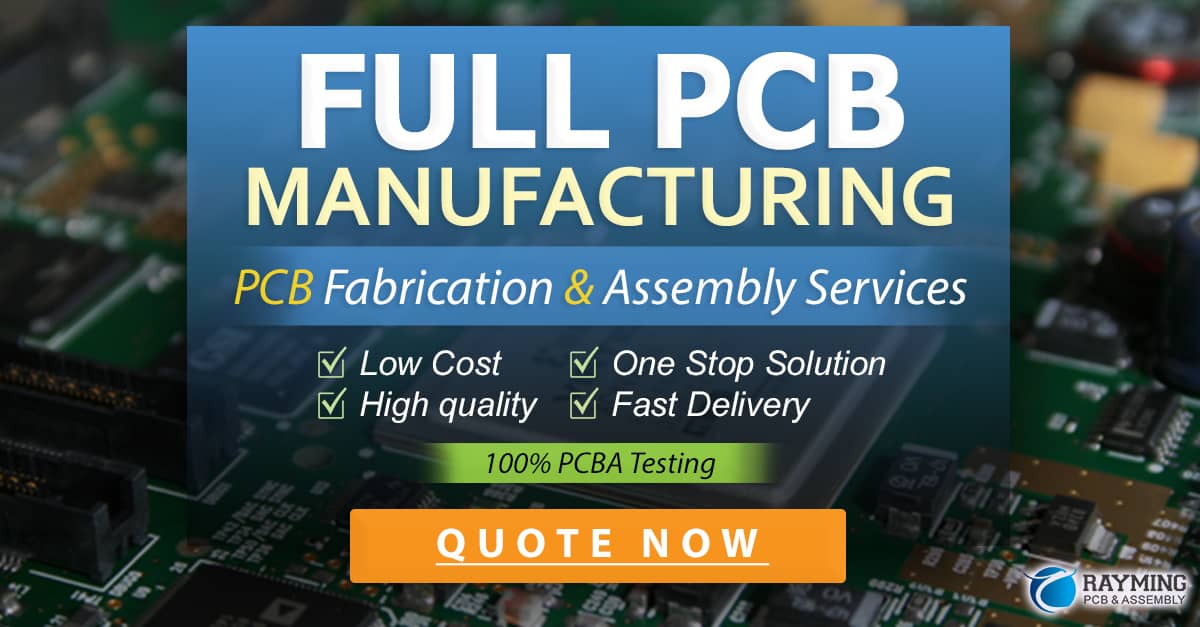
Common Applications of PCB Pins
PCB pins are used in a wide range of electronic applications, from consumer devices to industrial equipment. Some common applications include:
-
Microcontrollers and processors: PCB pins are used to connect microcontrollers, processors, and other integrated circuits to a PCB.
-
Connectors and headers: PCB pins are essential components in various types of connectors and headers, such as USB, HDMI, and GPIO headers.
-
Power supply and distribution: PCB pins are used in power supply circuits to distribute power to different parts of a PCB.
-
Sensors and modules: Many sensors and modules, such as temperature sensors, accelerometers, and wireless communication modules, use PCB pins to interface with a main PCB.
Best Practices for Using PCB Pins
To ensure optimal performance and reliability when using PCB pins, follow these best practices:
-
Follow manufacturer guidelines: Always refer to the manufacturer’s datasheets and application notes for specific guidelines on installing and using PCB pins.
-
Use appropriate soldering techniques: When soldering PCB pins, use the correct temperature, duration, and amount of solder to create a strong and reliable connection.
-
Maintain proper pin alignment: Ensure that PCB pins are properly aligned with the corresponding holes or pads on the PCB to prevent misalignment and connection issues.
-
Consider environmental factors: Select PCB pins that are suitable for the intended operating environment, taking into account factors such as temperature, humidity, and vibration.
-
Perform regular inspections: Periodically inspect PCB pin connections for signs of wear, corrosion, or damage, and replace or repair as necessary.
Troubleshooting Common PCB Pin Issues
Despite best practices, issues can still arise when using PCB pins. Some common problems and their solutions include:
-
Cold Solder joints: These occur when the solder fails to melt completely, resulting in a weak and unreliable connection. To fix this, reheat the joint and apply fresh solder.
-
Misaligned pins: If pins are not properly aligned with the PCB holes or pads, they may not make a secure connection. Carefully reposition the pin and resolder if necessary.
-
Damaged pins: Pins can become bent, broken, or corroded over time. Replace damaged pins with new ones to ensure proper functionality.
-
Shorts or open circuits: These can occur due to excessive solder, damaged pins, or incorrect pin placement. Carefully inspect the connections and remove any excess solder or debris.
Frequently Asked Questions (FAQ)
-
What is the difference between through-hole and surface-mount PCB pins?
Through-hole pins are inserted into drilled holes on a PCB and soldered in place, while surface-mount pins are soldered directly onto the surface of the PCB. Surface-mount pins are smaller and more suitable for high-density circuits. -
Can I mix different types of PCB pins on the same board?
Yes, you can mix different types of PCB pins on the same board, provided that the PCB is designed to accommodate them and that the pins are compatible with each other. -
How do I choose the right PCB pin size for my application?
When selecting PCB pin size, consider factors such as the current and voltage requirements, mechanical strength, and PCB layout. Refer to the manufacturer’s datasheets for specific recommendations. -
What is the purpose of plating on PCB pins?
Plating on PCB pins, such as gold, tin, or nickel, helps improve conductivity and prevent corrosion, ensuring a reliable and long-lasting connection. -
Can I reuse PCB pins after desoldering them from a board?
While it is possible to reuse PCB pins after desoldering, it is generally not recommended, as the desoldering process can damage the pins or affect their performance. It is best to use new pins for each application.
Conclusion
PCB pins are essential components in electronic circuits, providing reliable and secure connections between different parts of a PCB or external devices. By understanding the different types of PCB pins, their installation processes, and best practices for use, you can ensure optimal performance and reliability in your electronic projects.
When selecting and using PCB pins, always consider factors such as current and voltage requirements, mechanical strength, and environmental conditions. Following manufacturer guidelines and performing regular inspections can help prevent common issues and ensure the longevity of your PCB pin connections.
As electronic devices continue to become more complex and compact, the role of PCB pins in enabling efficient and reliable connections will only grow in importance. By staying up-to-date with the latest developments in PCB pin technology and best practices, you can create innovative and robust electronic designs that meet the demands of today’s rapidly evolving industry.
Pin Type | Characteristics | Common Applications |
---|---|---|
Through-hole | Inserted into drilled holes and soldered, strong mechanical bond | High-power applications, connectors, headers |
Surface-mount | Soldered directly onto PCB surface, smaller size | High-density circuits, microcontrollers, sensors |
Press-fit | Pressed into plated through-holes, no soldering required | Automotive, industrial applications |
Wire-wrap | Square post for wire wrapping, temporary or permanent connection | Prototyping, testing |
0 Comments