Required Equipment and Supplies for PCB Milling
To mill PCBs, you’ll need access to the following equipment:
- A CNC milling machine or router capable of working with FR-1, FR-2, or FR-4 copper clad boards
- Carbide milling bits in various sizes (see table below)
- A computer with PCB design software and CAM software for generating toolpaths
- Drill bits for holes
- Copper clad PCB blanks
- Isopropyl alcohol and cleaning supplies
Recommended Milling Bit Sizes
Trace/Pad Size | Milling Bit Diameter |
---|---|
0.2-0.5mm | 0.1mm |
0.5-1.0mm | 0.25mm |
1.0-2.0mm | 0.5mm |
>2.0mm | 0.8-1.0mm |
It’s a good idea to have milling bits in a few different sizes so you can choose the most appropriate one for the job. Smaller diameter bits can mill finer traces but take longer. Larger bits remove copper faster but have a higher minimum trace width.
Preparing PCB Designs for Milling
Before you can mill a PCB, you need to design it using EDA (electronic design automation) software. Some popular options include KiCad, Eagle, and Altium. The specific steps will vary depending on your software, but the general process is:
- Create a schematic of your circuit
- Lay out the PCB based on the schematic, placing and routing all components and traces
- Export the PCB design as a standard Gerber or SVG file
Next, you need to use CAM (Computer-Aided Manufacturing) software to generate the toolpaths that will control the mill’s movement to match your PCB design. This typically involves:
- Importing the PCB design file into the CAM software
- Selecting the areas to be milled (traces and pads)
- Choosing appropriate milling bits and cut depths
- Generating GCode that can be read by the milling machine
Some all-in-one software like FlatCAM can handle both PCB design and CAM. Otherwise you may need separate programs for each step.
Step-by-Step PCB Milling Process
Once your design is ready and the toolpaths are generated, it’s time to set up the milling machine and make your PCB. Here’s a simplified overview of the process:
- Fasten your copper clad board to the mill’s bed using tape or fixturing
- Zero the milling bit to the PCB surface to establish a reference point
- Load the generated GCode into the mill’s control software
- Run the milling job, watching closely to make sure there are no issues
- Use compressed air or a brush to clear away chips as the mill is running
- Once complete, remove the PCB and inspect it for any problems
- Clean the copper surface with isopropyl alcohol to remove grease and oxidation
- Drill any required holes using a drill press or the mill itself if it has that capability
If everything looks good, you now have a functional PCB that’s ready for soldering components and testing. It may take a few attempts to dial in all the settings and get a perfect result, but stick with it!
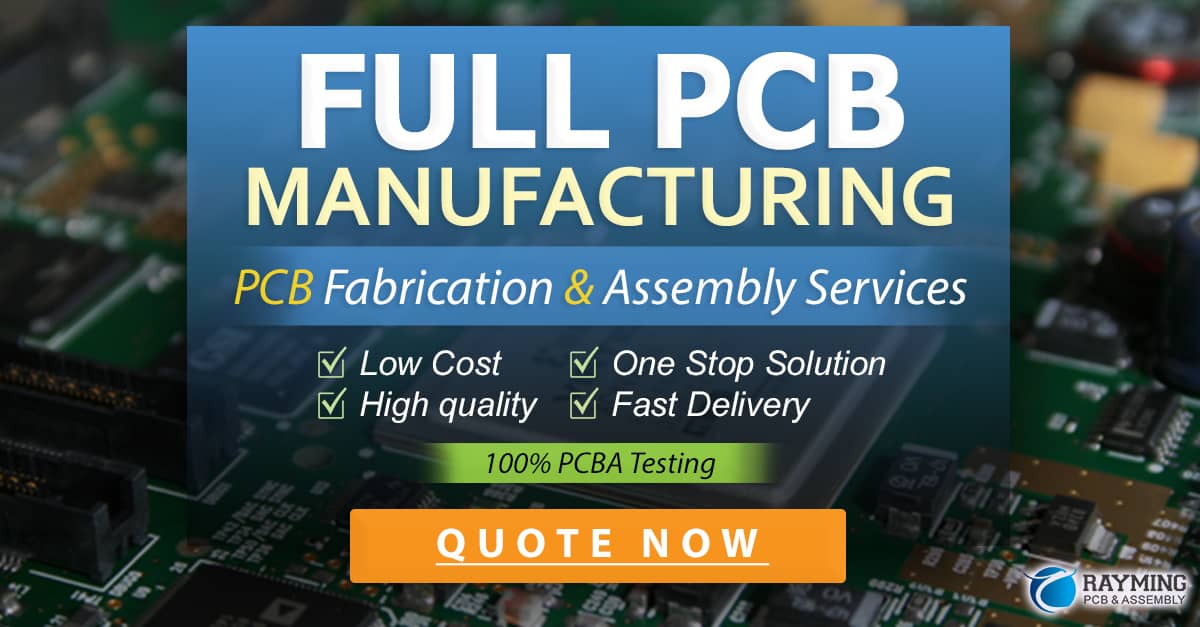
Tips and Tricks for PCB Milling Success
- Mirror your PCB design before milling since you’ll be cutting from the bottom side of the board.
- If using a double-sided board, add alignment holes so you can accurately mill both sides.
- Perform an “air cut” of the toolpaths before milling to check for errors.
- Use the smallest milling bit possible for better precision, but not so small that milling takes an excessive amount of time.
- Aim for 0.2-0.3mm cut depth per pass to avoid breaking bits. Enable multiple passes in your CAM software.
- Calculate feed and plunge rates based on your specific machine and milling bits.
- Consider using a sacrificial bed of MDF or plywood underneath the PCB to allow some margin of error and prevent damaging your machine bed.
- Learn how to manually touchoff and zero the Z-axis for consistent cutting depth.
- Don’t neglect regular machine maintenance like lubricating and checking for loose belts and bearings.
Frequently Asked Questions about PCB Milling
What kind of accuracy and feature sizes are achievable with PCB milling?
Most entry-level desktop CNC machines are capable of around 0.1-0.3mm trace and space with proper calibration and setup. More advanced machines may be able to achieve finer results down to 50 micron trace/space, but this requires very precise tooling and machine control.
Can I mill PCBs with a standard wood router or 3D printer?
Many hobbyist routers and 3D printers can be converted into PCB mills with some modifications. You’ll likely need to upgrade the spindle to a high speed brushless motor, improve the linear motion components, and fine-tune the electronics to minimize runout and vibration. It requires some tinkering but is doable on a budget.
How much does it cost to get started with PCB milling?
All-in-one desktop CNC machines marketed for PCB milling start around $500-1000. Converting a 3D printer or building a machine from scratch could cost $200-500 in parts. Plus budget $50-100 for milling bits, drill bits, and PCB blanks. While not the cheapest hobby, it’s very accessible for individuals, schools, and small businesses.
What materials can be used for making PCBs?
The most common material is FR-4 glass-reinforced epoxy laminate. It’s affordable, rigid, and has good thermal and electrical properties for most applications. Cheaper options like FR-1 phenolic paper and FR-2 phenolic cotton paper are less durable but easier to mill. You can also mill Flexible PCBs from polyimide film or directly from copper sheet.
What are the advantages of milling vs. chemical etching?
Compared to traditional chemical etching, PCB milling has several benefits:
– No need for acids, solvents, photoresists, or other hazardous chemicals
– Faster turnaround time since there’s no need to produce a phototool
– Easier to make revisions and iterate designs
– Better for rapid prototyping and low volume production
– More environmentally friendly with less waste generated
However, etching still has some advantages like higher precision, lower cost for volume production, and the ability to produce plated through-holes, so it’s not obsolete.
How do I get started designing my own PCBs?
- Learn to use schematic capture and PCB layout software. KiCad and Eagle are popular beginner-friendly options. Many offer detailed tutorials.
- Study PCB design best practices like component placement, routing techniques, manufacturability guidelines, etc.
- Start with simple designs and practice the whole workflow from schematic to physical board.
- Leverage online resources like reference designs, component libraries, forums, and articles. The electronics community is very helpful!
With patience and experience, PCB design is a skill that can be learned by anyone. Having your own mill helps shorten the feedback loop and accelerate your progress.
I hope this guide has given you a solid foundation to start exploring the world of in-house PCB Fabrication through milling. As you can see, it’s a powerful capability that can open up many possibilities for your electronics projects and endeavors. Give it a try and see what you can create!
0 Comments