Printed Circuit Boards (PCBs) are the backbone of modern electronics, serving as the foundation for virtually every electronic device we use today. They provide a platform for the interconnection of various electronic components, allowing them to function as intended and enabling the creation of complex circuits. The raw materials used in the manufacturing of PCBs are crucial components that determine the performance, reliability, and overall quality of the final product.
In this comprehensive article, we will delve into the diverse range of raw materials employed in the production of PCBs, exploring their properties, functions, and significance. We will also examine the various manufacturing processes involved in transforming these raw materials into the intricate and highly functional PCBs that power our technological world.
Raw Materials in PCBs
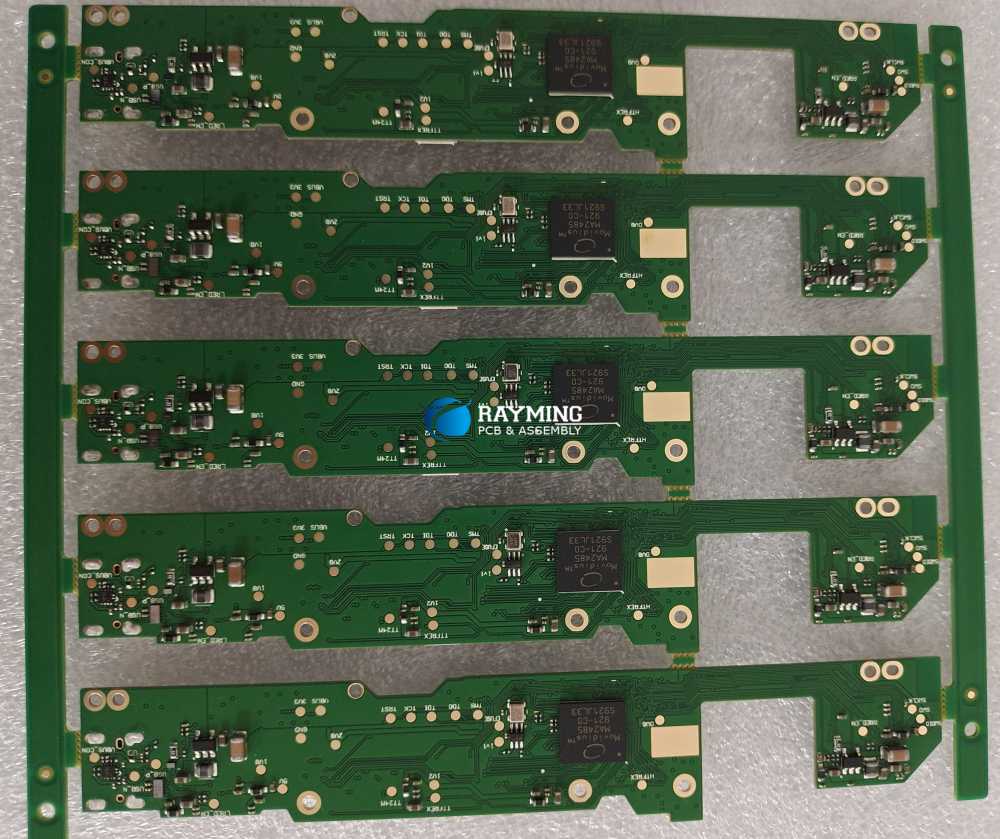
PCBs are intricate structures composed of several layers, each serving a specific purpose and requiring different raw materials. The primary raw materials used in the production of PCBs can be broadly categorized into the following groups:
1. Base Materials
The base material, also known as the substrate, forms the foundation of a PCB. It provides mechanical support and serves as the platform upon which the conductive layers and other components are built. The most commonly used base materials are:
a. Epoxy Resin
Epoxy resin is a thermoset plastic widely used in PCB manufacturing due to its excellent electrical insulation properties, high mechanical strength, and chemical resistance. It serves as the primary material for the base substrate and is combined with reinforcing materials, such as fiberglass, to enhance its durability and dimensional stability.
b. Fiberglass
Fiberglass, a reinforcing material made of fine glass fibers, is often combined with epoxy resin to create a robust and rigid base substrate. The fiberglass provides mechanical strength, thermal stability, and dimensional stability to the PCB, ensuring it can withstand the rigors of assembly and operation.
c. Polyimide
Polyimide is a high-performance polymer known for its exceptional thermal resistance, chemical stability, and mechanical properties. It is used in the production of flexible PCBs, where flexibility and resistance to high temperatures are essential requirements.
2. Conductive Materials
Conductive materials are used to create the conductive layers and traces on the PCB, enabling the flow of electrical signals and power. The most common conductive materials used in PCB manufacturing are:
a. Copper
Copper is the predominant conductive material used in PCB production due to its excellent electrical conductivity, ductility, and resistance to corrosion. Copper foils or thin layers of copper are etched or deposited onto the base substrate to create the conductive patterns and interconnections.
b. Aluminum
Although less common than copper, aluminum is sometimes used as a conductive material in PCBs, particularly in applications where weight reduction is a critical factor, such as in the aerospace industry.
3. Solder Masks and Coverlays
Solder masks and coverlays are protective coatings applied to the PCB surface to insulate and protect the conductive layers from environmental factors and mechanical damage.
a. Solder Mask
The solder mask is a polymer-based coating applied to the PCB surface, covering the conductive traces and leaving only the necessary pad areas exposed for component soldering. It provides insulation, prevents solder bridging, and enhances the overall reliability of the PCB.
b. Coverlays
Coverlays are thin layers of protective material, typically made of polyimide or epoxy resin, applied to the outer surfaces of the PCB. They offer additional mechanical protection, electrical insulation, and resistance to harsh environmental conditions, such as moisture, chemicals, and abrasion.
4. Surface Finishes
Surface finishes are applied to the exposed conductive areas of the PCB, such as pads and through-holes, to enhance solderability, protect against oxidation, and improve the overall reliability of the board.
a. Hot Air Solder Leveling (HASL)
HASL is a surface finish technique that involves applying a thin layer of solder (typically a tin-lead alloy) to the exposed conductive areas of the PCB. This process enhances solderability and protects the copper from oxidation.
b. Electroless Nickel Immersion Gold (ENIG)
ENIG is a surface finish that involves the deposition of a thin layer of nickel followed by a thin layer of gold on the exposed conductive areas. This finish provides excellent solderability, corrosion resistance, and wire bondability, making it suitable for high-density interconnect (HDI) PCBs and surface mount technology (SMT) applications.
c. Immersion Silver (ImAg)
Immersion silver is a surface finish that involves the deposition of a thin layer of silver on the exposed conductive areas. It offers good solderability and provides an alternative to lead-based finishes, making it an environmentally friendly option.
5. Reinforcement Materials
In addition to the primary raw materials, PCBs may incorporate reinforcement materials to enhance their mechanical properties and durability.
a. Aramid Fibers
Aramid fibers, such as Kevlar, are often used as reinforcement materials in PCBs, particularly in high-reliability applications. They provide excellent mechanical strength, dimensional stability, and resistance to high temperatures.
b. Carbon Fibers
Carbon fibers are lightweight yet extremely strong reinforcement materials that can be incorporated into PCBs to improve their mechanical properties, thermal conductivity, and electromagnetic shielding capabilities.
6. Miscellaneous Materials
Several other materials are used in PCB manufacturing for various purposes, such as adhesives, etchants, and cleaning agents.
a. Adhesives
Adhesives are used to bond different layers of the PCB together, ensuring proper adhesion and reliability. Common adhesives used in PCB manufacturing include epoxy-based adhesives and acrylic-based adhesives.
b. Etchants
Etchants are chemical solutions used to selectively remove unwanted portions of the conductive layer (typically copper) from the PCB surface during the etching process. Common etchants include ammonium persulfate and ferric chloride solutions.
c. Cleaning Agents
Cleaning agents are used to remove various contaminants, such as residues, flux, and oxides, from the PCB surface during the manufacturing process. Examples include solvents, acids, and alkaline cleaning solutions.
Manufacturing Processes
The raw materials mentioned above are transformed into functional PCBs through a series of manufacturing processes. These processes involve various techniques, including lamination, imaging, etching, plating, and surface finishing, among others. Each step plays a crucial role in shaping the final product and ensuring its quality and performance.
Data Visualization
To better understand the raw materials used in PCBs, let’s visualize some of the key components using tables:
Table 1: Base Materials
Material | Properties | Applications |
---|---|---|
Epoxy Resin | Excellent electrical insulation, high mechanical strength, chemical resistance | Rigid PCBs, base substrate |
Fiberglass | Mechanical strength, thermal stability, dimensional stability | Reinforcement for epoxy resin base substrate |
Polyimide | High thermal resistance, chemical stability, mechanical properties | Flexible PCBs |
Table 2: Conductive Materials
Material | Properties | Applications |
---|---|---|
Copper | Excellent electrical conductivity, ductility, corrosion resistance | Conductive layers, traces, and pads |
Aluminum | Lightweight, good electrical conductivity | Weight-sensitive applications (e.g., aerospace) |
Table 3: Surface Finishes
Finish | Properties | Applications |
---|---|---|
HASL (Hot Air Solder Leveling) | Enhances solderability, protects against oxidation | General PCB applications |
ENIG (Electroless Nickel Immersion Gold) | Excellent solderability, corrosion resistance, wire bondability | HDI PCBs, SMT applications |
ImAg (Immersion Silver) | Good solderability, environmentally friendly | Lead-free applications |
Frequently Asked Questions (FAQ)
- What is the most commonly used base material in PCB manufacturing? The most commonly used base material in PCB manufacturing is epoxy resin combined with fiberglass reinforcement. This combination provides excellent electrical insulation, mechanical strength, and dimensional stability, making it suitable for a wide range of PCB applications.
- Why is copper the preferred conductive material for PCBs? Copper is the preferred conductive material for PCBs due to its excellent electrical conductivity, ductility, and resistance to corrosion. It is relatively inexpensive and easy to process, making it a cost-effective choice for PCB manufacturing.
- What is the purpose of solder masks in PCB manufacturing? Solder masks are polymer-based coatings applied to the PCB surface to insulate and protect the conductive layers from environmental factors and mechanical damage. They prevent solder bridging during the assembly process and enhance the overall reliability of the PCB.
- What are the advantages of using ENIG surface finish? The Electroless Nickel Immersion Gold (ENIG) surface finish offers several advantages, including excellent solderability, corrosion resistance, and wire bondability. It is particularly suitable for high-density interconnect (HDI) PCBs and surface mount technology (SMT) applications, where reliability and performance are critical.
- Why are reinforcement materials used in PCBs? Reinforcement materials, such as aramid fibers (e.g., Kevlar) and carbon fibers, are used in PCBs to enhance their mechanical properties, dimensional stability, and durability. These materials provide additional strength and resistance to high temperatures, making PCBs suitable for demanding applications and harsh environments.
0 Comments